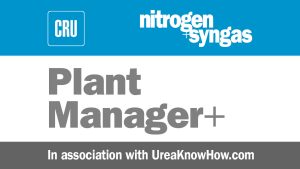
Problem No. 69: Impact of ammonia catalyst fines on urea plant
Rohit Khurana and Umesh Jainker of KBR presented a technical paper on this topic during the 2013 Asian Nitrogen + Syngas Conference. It can be found in the UreaKnowHow.com E-Library with the title: ”Replacing ammonia plant catalyst with maximum efficiency and lowest cost”. The paper addresses the importance of de-dusting catalyst beds before commissioning and the serious impacts on the plant if not performed thoroughly. Many ammonia plants have faced problems related to the plugging of exchangers, pipe choking, pressure drop increase of the downstream catalyst beds and separators or foaming in the CO 2 removal section which could be caused by the presence of catalyst dust. Most of these problems have led to either decrease in the efficiency of the plant or operation at lower throughputs. The paper presents the critical steps and procedures for proper dedusting of the catalyst beds before commissioning. In addition, the foaming problem in the CO 2 removal section associated with catalyst dust is discussed signifying the importance of cleaning the CO 2 removal system and solution. The role of filters in the CO 2 removal section was also emphasised.