Nitrogen+Syngas 380 Nov-Dec 2022
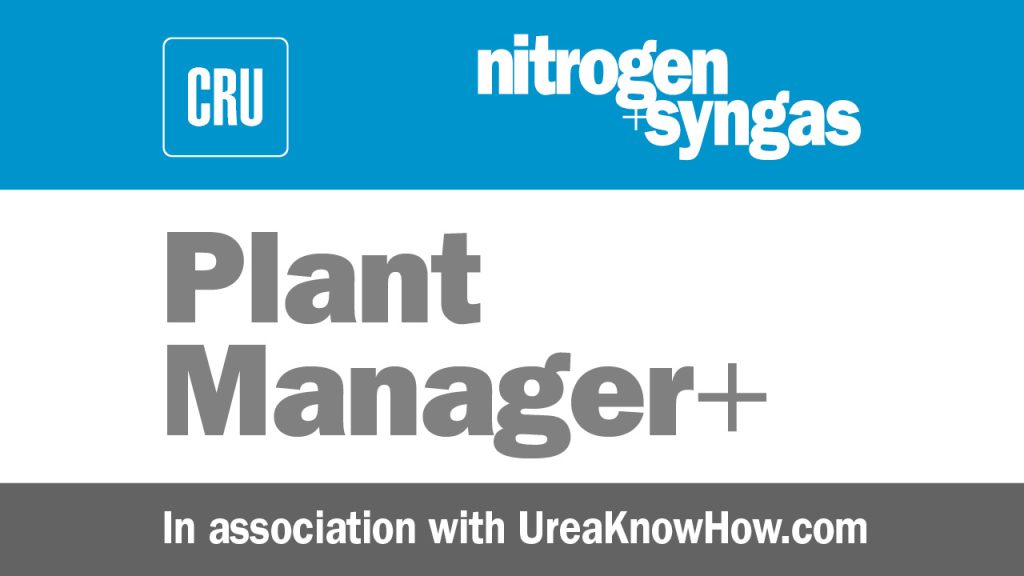
30 November 2022
Handling leaks in urea plants: part 4
Leaks in the high-pressure synthesis section of a urea plant may lead to catastrophic consequences. UreaKnowHow.com started to collect incidents in an incident database and in 2017 AmmoniaKnowHow.com and UreaKnowHow.com introduced FIORDA, the Fertilizer Industry Operational Risk Database, a global open source risk register for ammonia and urea plants.
Part 1 of this short series of articles on how to handle leaks in urea plants explained why leaks in the high-pressure synthesis section of a urea plant are so critical, part 2 looked at the causes and consequences of leaks, part 3 discussed different measures to prevent carbamate leaks and this final part discusses mitigation measures.
Mitigation measures
Once a carbamate leak occurs most of the time one the only option is to shut down the plant. Ammonium carbamate will dissociate into ammonia and carbon dioxide and thus a carbamate leak forms a health threat due to the presence of ammonia. Key is to act quick and keep the ammonia cloud small.
Install a proper ammonia leak detection system
Installing a proper ammonia leak detection system at critical locations is a good way to detect leaks at an early stage and be able to act quickly. Professionals from the Ammonia Safety & Training Institute (www.ammonia-safety.com) confirm early detection and quick action of an ammonia leak is vital to avoid catastrophes. Critical locations are the high-pressure synthesis section especially at locations which are difficult to reach like for example the top floors. The carbon steel ammonia feed lines and the ammonia and carbamate high press ure pumps are also critical with respect to potential ammonia leaks.
Shut down the plant
In case of a leak, the best option after the leak has been confirmed and located is to shut down the plant. In real situations this is not always an easy choice to make, but when faced with a critical leak as described in part 2, the recommendation is to shut down the plant.
Flush with steam and/or condensate
In case of a small leak, consider flushing away the solids and diluting/absorbing the ammonia from the leak by means of a continuous flush with steam and/or condensate. The leak and integrity of the leaking equipment should be monitored continuously by means of a camera as even flashing ammonium carbamate can corrode carbon steel bolts and nuts as shown in part 1 of this series.
When a flush is applied it is important to be careful that water with ammonia and ammonium carbamate does not drip on high pressure vessels located under the leak. This mixture can cause stress corrosion cracks in the carbon steel pressure bearing wall of these vessels. This risk increases when one uses fine grain carbon steel materials 1 .
Do not allow solids to reduce/stop the leak
Do not allow solids to form even if these reduce/stop the leak. One does not know what happens under these solids and ammonium carbamate can still corrode carbon steel parts and even stainless steel parts due to active corrosion as a result of lack of oxygen (see Fig. 1).
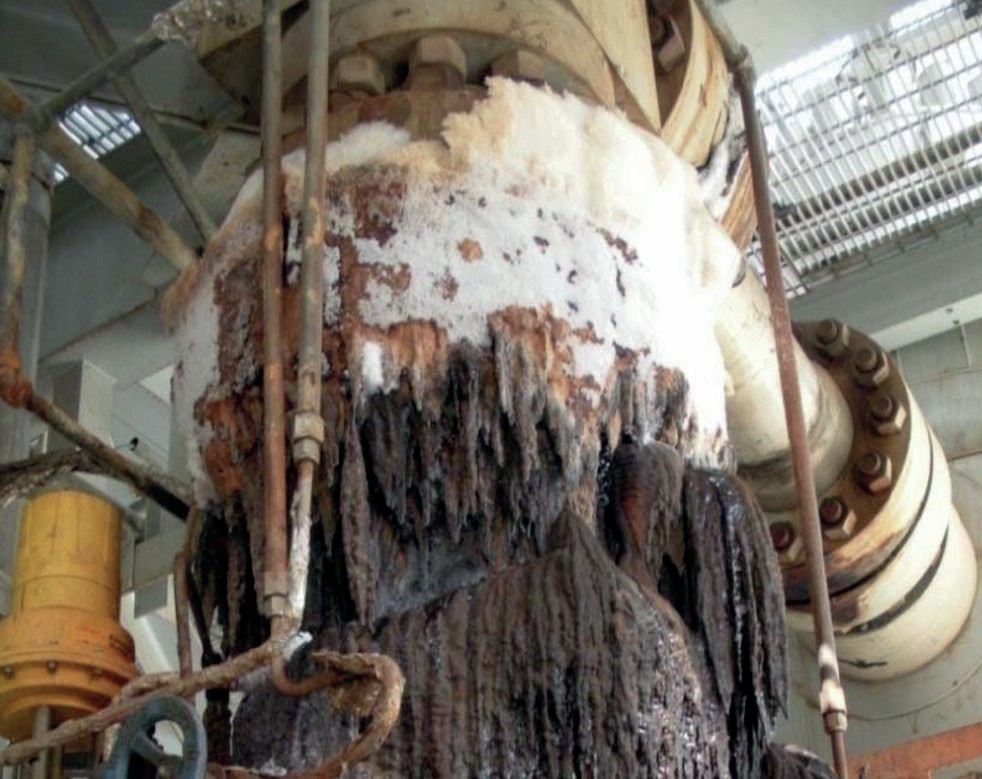
Do not install a clamp on ammonium carbamate and ammonia lines. Installing a clamp on a ammonium carbamate line is not allowed for the following reasons:
- One does not know what happens to the materials underneath these solids and ammonium carbamate corrosion will weaken the carbon steel parts and even stainless steel will corrode as a result of lack of oxygen;
- During the installation of the clamp additional, forces will be applied and these extra forces could lead to a rupture due to corrosion that may have occurred due to the leak.
- Installing a clamp on ammonia lines can be very risky and has led to catastrophic events2 .
Clamps when installed should always be considered a temporary solution. Develop a procedure to check its integrity during installation.
References