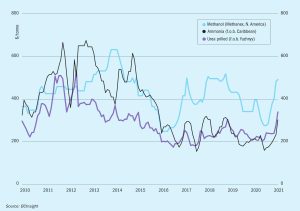
Market Outlook
The ammonia industry faced a difficult February, due to extremely cold weather conditions in the northern hemisphere. In the US, production outages resulting from winter storm Uri affected up to 7 million t/a of capacity.
The ammonia industry faced a difficult February, due to extremely cold weather conditions in the northern hemisphere. In the US, production outages resulting from winter storm Uri affected up to 7 million t/a of capacity.
Market Insight courtesy of Argus Media
Shutdowns in technical ammonia capacity due to the pandemic have contributed to make 2020 a turbulent year for ammonia markets, but plant shutdowns, strong fertilizer demand and a shortage of new merchant ammonia capacity are contributing to finally removing the burden of overcapacity.
Several safety risks threaten urea high pressure equipment such as high pressures, high temperatures, various kind of corrosion phenomena, crystallisation risks, and the release of large volumes of toxic ammonia in case of a leak. A significant number of serious incidents with high pressure urea equipment still occur in the industry and, in 50% of cases, a failing leak detection system was one of the main causes. UreaKnowHow’s Risk Register for a 316L urea grade reactor identifies 50+ safety risks of which 75% can be prevented by operating a proper leak detection system. In this article, UreaKnowHow answers some key questions about the importance of an effective active leak detection system.
Ammonia synthesis catalysts have long lives and catalyst replacement is an infrequent activity. Many people will go through their careers in the ammonia industry without ever having to replace a synthesis catalyst and the infrequent nature of catalyst replacement means that many plants may not have direct experience of this activity. Ammonia synthesis catalyst can present a range of hazards throughout the replacement process, from transport through loading, reduction, start-up, shutdown and discharge, but the good practice illustrated in this article, and collaboration between catalyst suppliers and end users can ensure safe and successful catalyst changeouts.
As industry trends add pressure to optimise processes, new digital technologies for roundthe-clock, data-driven decision-making can help plants boost production efficiency without time-consuming manual analysis or large-scale investment. Here, Dr S. Werner of Navigance explores their potential and shares the difference they are already making.
The ammonia industry seems to have quite a buzz about it at the moment. As can be glimpsed in our Nitrogen Industry News section this issue, the number of proposed green ammonia production sites continues to grow, as does interest in ammonia as a hydrogen or energy carrier, while the shipping sector continues to seriously consider ammonia as a green fuel candidate for the longer term. The latter prospect could see current ammonia demand double by 2050, although as our article on sustainable nitrogen production on page 22 notes, whether enough renewable power will exist by then to generate that must be seriously doubted.
Because of the ongoing pandemic, this year’s CRU Nitrogen + Syngas conference was held as a ‘virtual’ event, in early March 2021.
Georgy Eliseev , Principal Analyst at Fertecon for IHS Markit, looks at the medium to long term outlook for both ‘green’ and ‘blue’ ammonia production.
Bodo Albrecht, BASF writes: Among the many sad news of 2020 is the passing of Alan Heywood, a leading authority in the advancement of nitric acid catalysts and recovery systems. At the time I first met Alan in 1997, he already had 6 patents to his name ranging from improved aircraft gas turbine igniters and “ZGS” grain stabilized precious metal composite materials to PGPs “cartridge” catalyst, arguably the first true catalyst system ever produced.