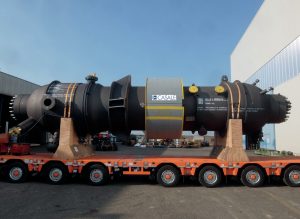
Urea plant efficiency and reliability
Improvements to equipment and materials are driving greater operational performance and higher efficiencies at urea plants. Recent advances are reviewed.
Improvements to equipment and materials are driving greater operational performance and higher efficiencies at urea plants. Recent advances are reviewed.
Efficient size preparation and ore transport are key prerequisites for successful potash and phosphate production. We highlight the range of equipment options.
As sulphur recovery units operate at progressively higher temperatures, creep stress in the furnace refractory lining can lead to deformation or even failure of the bricks and require the shutdown of the SRU. UK-based DSF Refractories have developed a product which minimises creep stress damage at high temperatures, for a longer-lived furnace lining.
Johnson Matthey’s latest methanol synthesis catalyst, KATALCO™ 51-102, was introduced in 2018 to offer improved catalyst stability and therefore higher end-of-life activity and extended lifetimes than conventional methanol synthesis catalysts. Since launch, KATALCO 51-102 has been successfully installed in two methanol plants and a third is planned for later in the year. In this article Johnson Matthey provides an update on the proven performance of KATALCO 51-102 during lab and pilot scale testing as well as in customer plants. The application of catalysts made using the KATALCO 51-102 technology for methanol synthesis via new ‘green’ routes, such as using captured and purified CO2 in conjunction with ‘green’ hydrogen, is also discussed.
The crushing and grinding of mined phosphate rock and potash ore is a vital preparatory step for subsequent beneficiation and chemical processing. Although often overlooked, the efficiency of downstream P & K fertilizer production is heavily reliant on successful particle size reduction upstream.
To comply with stricter stack emission obligations, industries are required to recover more heat from flue gas and to clean it before it can be discharged into the atmosphere. J. Kitzhofer of APEX Group discusses the challenges and limitations of the majority of current heat recovery systems and reports on a new family of acid resistant tubular and plate-type heat exchangers developed by APEX Group that overcomes these problems. The new heat exchangers are resistant to dew point corrosion. The heat transfer elements are constructed from an acid resistant polymer composite with high thermal conductivity, allowing the design of new trouble-free heat recovery systems and the upgrade of existing systems to meet heat recovery and stack emission targets.
Metal dusting corrosion damage on steam reformers is no longer a major issue in modern methane steam reformer units. Nevertheless, failures related to metal dusting corrosion attack still take place in some specific designs and configurations that are more prone to experience this damage. Poor maintenance or deterioration of insulation components on transition areas might expose metallic surfaces to metal dusting attack. In this article, Dr P. Cardín and P. Imízcoz of Schmidt+Clemens Group describe different case studies, where the end users benefited from the experience of a collaboration to address potential risks and improve plant reliability against metal dusting corrosion damage.
M. Østberg and M. Rautenbach of Haldor Topsoe describe ReShift ™ technology, a new high temperature CO 2 reforming process, where preheated CO 2 is added directly downstream of a main reformer and then equilibrated in an adiabatic reactor. This new technology makes use of the high temperature of the reformer effluent to circumvent carbon formation, while at the same time maintaining an overall minimum steam to hydrocarbon carbon ratio, depending on process specific conditions. An increase in the amount of CO 2 added to the process will result in an increased fraction of CO in the produced synthesis gas. Synthesis gas with H 2 /CO ratios in the range 0.5-3 can be produced. These CO-rich gases are typically utilised in the production of functional chemicals and synthetic fuels.
Temperature monitoring and measurement of the Claus thermal reactor in sulphur recovery units is one of the most challenging applications in the oil and gas industry. Recently, market interest in unpurged thermocouples has increased with the introduction of new unpurged thermocouple designs utilising alternative thermowell materials such as monocrystalline sapphire.
New state-of-the-art equipment has been installed in the thermal stage of one of Europe’s largest Claus SRU units. Substoichiometric firing and a furnace designed with CFD calculations and a modern compact boiler system design based on detailed heat engineering and FEM calculations were key to the success of the retrofit. P. Foith of CS Combustion Solutions reports on the retrofit and how the novel combination of a CS low pressure swirl burner, additional mixing using a VectorWall™ and a new waste heat boiler design achieved the desired results.