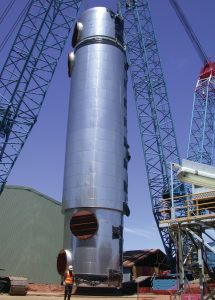
Extending the life of sulphuric acid plants
Chemetics describes a variety of ways to extend the life of sulphuric acid plants. Debottlenecking, emissions reduction and/or energy recovery projects require a systematic, phased approach to maximise the potential of economic and operational benefits to the owner.