Nitrogen+Syngas 391 Sep-Oct 2024
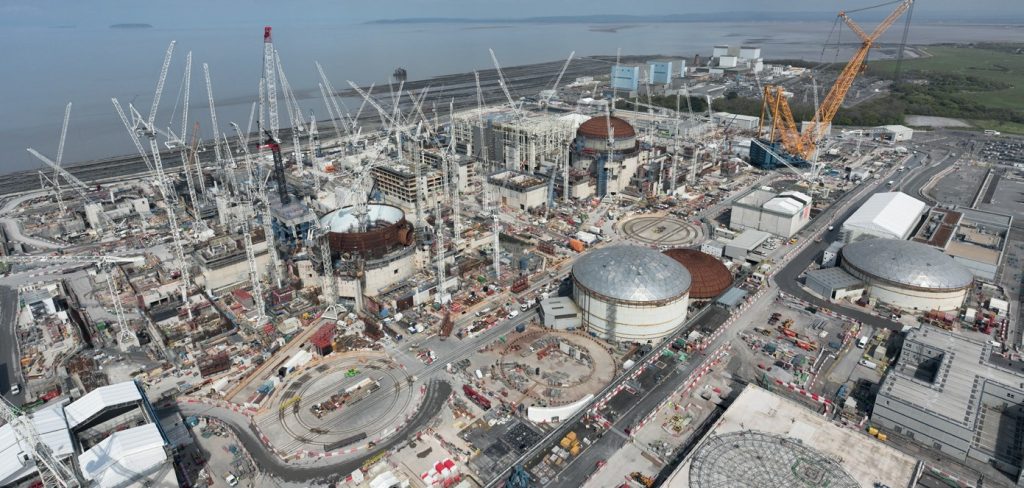
30 September 2024
Nuclear powered ammonia
AMMONIA
Nuclear powered ammonia
With green ammonia from renewable energy facing cost hurdles to adoption, thoughts have turned to using nuclear energy as a carbon free alternative.
Many low carbon projects for producing ammonia have focused on two essential alternatives; conventional ammonia production using fossil fuels, particularly natural gas, followed by carbon capture and storage/utilisation (‘blue’ ammonia), or use of hydrogen generated via water electrolysis using renewable energy – wind, solar or hydroelectric (‘green’ ammonia). However, an alternative zero carbon source of power is already widely available and adopted worldwide; nuclear energy. While it ‘burns’ uranium fuel (although this can be reprocessed where such technology is available), and hence is not strictly renewable, other nuclear fuels are available, and while it generates radioactive waste which must be safely stored and disposed of, it is nevertheless a zero carbon energy source.
The scalability of blue ammonia remains an open question at present, as outside of enhanced oil recovery, carbon dioxide has not been permanently sequestered on the kind of scale that would be needed to convert much of the world’s ammonia production, while green ammonia, although costs of electrolysis are falling, remains expensive compared to conventional ‘grey’ ammonia production. The use of nuclear power to generate hydrogen for ammonia production – sometimes called ‘pink’ or ‘yellow’ ammonia – is consequently receiving serious consideration.
Increasing nuclear use
Nuclear power continues to see an increase in use. According to the World Nuclear Association, global nuclear electricity generation rose to 2,600 TWh in 2023, up from 2,540 TWh in 2022, providing 9% of the world’s electricity—second only to hydropower among clean energy sources. WNA argues that this meant that nuclear reactors currently help avoid 2.1 billion t/a of carbon dioxide emissions from equivalent coal generation, and at COP28, twenty-five countries signed a declaration to triple nuclear capacity by 2050. There are currently 64 reactors under construction in 15 countries, two thirds of these in Asia, and almost half in China alone. Eastern Europe and Russia are also seeing major expansions.
In the European Union, while nuclear energy use has been reduced due to concerns over waste disposal, and in Germany has virtually ended due to environmental concerns, there remain major proponents of nuclear power, particularly France, which uses nuclear power to generate over 60% of all of its electricity. French pressure helped include nuclear energy use as part of EU renewable energy usage targets in a deal agreed at the end of 2023. Nuclear power plants in Europe can now produce and market hydrogen that may be used by industry as a replacement for fossil fuels, and contribute to the region’s goals of sharply reducing fossil fuel use while boosting supplies of clean fuels. Nuclear power has seen something of a re-evaluation in Europe since Russia cut supplies of natural gas to the continent, sending natural gas prices spiking to unheard of levels, and outside of France it remains a major source of energy in several other countries, including Sweden, Spain, Switzerland, Finland, Belgium and Bulgaria.
Indeed, it can be argued that the Borealis project to instal 30 MW of electrolysers at its Ottmarsheim production site in France running off electricity from the French electricity grid will in effect be producing a proportion of nuclear ammonia. The demonstration project is aiming to deliver 24,000 t/a of low carbon ammonia by 2025-26 and it can be argued that 60% of this is effectively nuclear based ammonia capacity. However, nuclear power plants mainly generate base load electricity, more useful to power companies than solar or wind power as it does not have slack periods, while integrating nuclear heat as well as power generation into ammonia production is more efficient, and so it is likely that for large scale ammonia production, dedicated nuclear plants might be required.
Benefits for hydrogen
Nuclear power can operate at very high capacity, for long periods without upset, making it ideally suited to large scale provision with a dedicated end use such as chemical production, as it eliminates supply uncertainties and interruptions which are problematic for fossil fuel based ammonia plants given the several days required for start-up and shutdown. It also means that production is not subject to the volatility of fossil fuel prices, again particularly natural gas prices, making operating costs far more predictable. Finally, eliminating gas or solid fuel reforming as a source simplifies the process, with the hydrogen feed needing far less treatment before it is used in ammonia production.
Methods of hydrogen generation
As Figure 1 shows, there are several ways that nuclear energy can be used to produce hydrogen for ammonia production. Firstly, it can be used for simple ‘cold’ electrolysis of water in the same way that renewable power is used, as per the Borealis project mentioned above. However, the heat generated by nuclear reactors means that this can also be incorporated into the process, as low- or high-temperature steam electrolysis. This increases the efficiency of the electrolysis from around 25% using cold electrolysis (ca 33% for the reactor x 75% for the cell) to up to 45% for high temperature steam electrolysis. It is even possible to use nuclear heat to thermochemically break down water into its component molecules, by using sulphur and/or iodine intermediates, raising efficiency to around 50%. In additional to all of these, it is possible to use nuclear heat to heat the reformer of a conventional ammonia plant. Steam reforming requires temperatures of over 700°C, easily generated by a nuclear reactor, and allowing around one third of gas consumption (i.e. all reformer heating gas) to be eliminated, along with flue gas CO2 emissions.
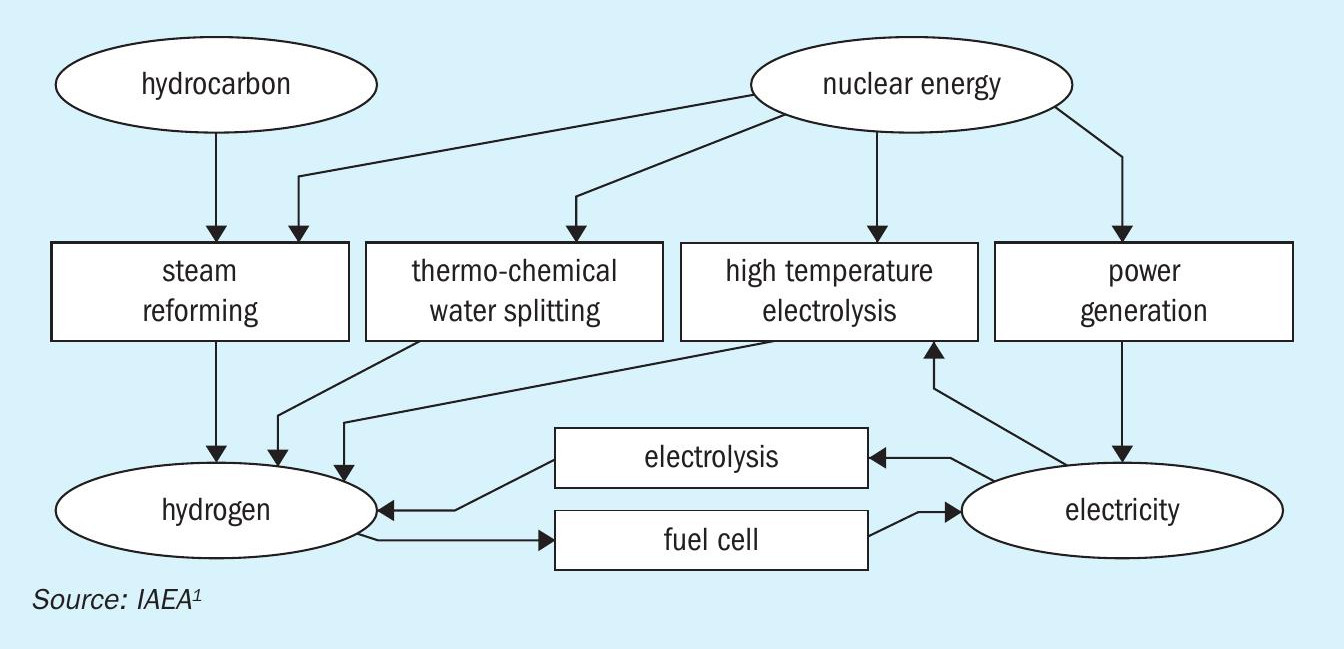
There have been studies of all of these routes recently, in both the US and Russia. Perhaps predictably, however, there remain some technical issues which need to be overcome. High-temperature (550750C) steam electrolysis in solid oxide electrolysis cells requires about one-third less energy than low-temperature electrolysis, but commercialisation has remained elusive due to the poor durability of components in a hot hydrogen environment. High temperature hydrogen attack, also known as ‘metal dusting’, remains a serious problem for steels, and even the ceramics used in the research projects suffered considerable degradation.
Thermochemical processes
Several direct thermochemical processes are being developed for producing hydrogen from water. For economic production, high temperatures are required to ensure rapid throughput and high conversion efficiencies. An intermediate heat carrier is usually used for safety reasons, generally a helium or molten fluoride salt loop. In each of the leading thermochemical processes the high-temperature (800-1000 °C), low-pressure endothermic (heat absorbing) decomposition of sulphuric acid produces oxygen and sulphur dioxide:

Subsequent reactions can involve iodine, such as the General Atomics process, which combines the iodine with the sulphur dioxide in the exothermic Bunsen reaction:

The HI then dissociates to hydrogen and iodine at about 350-450°C, endothermically:
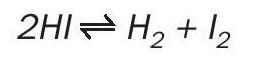
This can deliver hydrogen at high pressure. Overall this is effectively reduction of water to hydrogen and oxygen; all of the reagents other than water are recycled, and there are no effluents, hence it may be called the sulphur-iodine cycle, with zero-carbon hydrogen and oxygen byproducts. Japan and South Korea are both conducting research to use this to generate low cost hydrogen by the end of the decade using high temperature reactors.
Indonesia
Although most of the work on nuclear hydrogen and ammonia has been at a research level, there is a major project in development in Indonesia, where four Danish companies -Copenhagen Atomics, Aalborg CSP, Alfa Laval and Topsoe – have signed a memorandum of understanding with Indonesian ammonia producer PT Pupuk Kalimantan Timur, together with Pertamina New & Renewable Energy to investigate building a facility in the city of Bontang on the eastern coast of the island of Borneo, in the province of East Kalimantan.
The facility – tentatively scheduled to open in 2028 – would produce 1 million t/a of low carbon ammonia, at an estimated investment cost of $4 billion. The facility would be based around 25 of Copenhagen Atomics’ small modular nuclear reactors, each with a capacity of 40 MW, based on thorium technology. Aalborg CSP will design and supply thermal energy storage systems, molten salt based steam boilers providing the energy balancing required to integrate the energy production from the SMR modules with electricity production and waste heat from power turbines with production of ultra clean water. Alfa Laval will deliver heat exchangers to optimise the energy balance of the plant, and desalination to produce ultra-pure water for the electrolysis process. Topsoe would supply its own electrolysis cell technology, based on solid oxide electrolyser cells (SOEC) which are claimed be up to 30% more efficient than competing technologies in generating hydrogen, and would also design the 1 million t/a ammonia plant. All of the offtake would go to local partner Pupuk Kalimantan Timur (Kaltim). Pupuk Kaltim operates a total of 2.74 million t/a of ammonia capacity from its existing five ammonia plants licensed by KBR and Topsoe, making it the largest fertilizer company in southeast Asia. The ammonia is mostly used for downstream urea and ammonium nitrate production. In 2021, Indonesia exported about 0.90 million tonnes of ammonia according to the World Bank. Pupuk Kaltim contributes about one third of Indonesia’s ammonia exports, shipping to east Asia and Australia. The company has 100,000 tonnes of ammonia storage capacity, as well as six jetties able to accommodate ships up to 55,000 dwt.
Thorium
The enabling technology is Copenhagen Atomics’ modular thorium molten salt reactors, which the company says exceptional energy efficiency, capable of extracting 100 times more energy from each ton of mined materials compared to traditional reactors. Whereas a conventional reactor of the same scale would require 10 t/a of enriched uranium, the Bontang plant would only need 850 kilograms of thorium per year. Indonesia is believed to have considerable thorium reserves, around 250,000 tonnes.
Costs
The investment cost is high, several times that of a conventional gas-based ammonia plant. However, once operational, operating costs are relatively much lower, and the companies involved believe that, over the plant’s projected 25 year lifetime, it would actually be a relatively competitive green ammonia supplier. The projected price of ammonia is around $500/t2 , still high compared to ‘grey’ ammonia, but far lower than the estimated $700-1,400/t that wind or solar generated ammonia might cost. A Brazilian study using conventional nuclear generation came to a figure of $790/t for ammonia production for a 100,000 t/a ammonia plant3 , while a study by the Maersk McKinney Moller Center for Zero Carbon Shipping came in at $514/t for the levelised cost of ammonia, admittedly for a larger scale, 10 million t/a ammonia facility4 .
At present the project is in a six month feasibility study period, during which regulatory approvals will be sought for reactor construction on the designated site owned by off-taker Pupuk Kaltim. Funding remains an open question. It is anticipated that Pupuk Kaltim and the Indonesian government will contribute around 50% of the money, with international investors providing the rest. The investment cost is certainly lower than for another green ammonia project in Indonesia, being developed by Pertamina with Tokyo Electric Power and some other Japanese companies, which would use geothermal energy in North Sulawesi to produce up to 1 million t/a of ammonia, and require up to $8-10 billion.
Terrestrial Energy
The other main rival technology to Copenhagen Atomics comes from Canadian-based Terrestrial Energy. Terrestrial Energy is also pioneering a thorium-based nuclear reactor technology which uses molten salt as both a fuel and as a coolant; the Integral Molten Salt Reactor (IMSR). With integrated components, the IMSR can supply heat directly to industrial facilities or use it to generate up to 195 MW of electrical power. Terrestrial Energy says that the use of molten salt as both fuel and coolant also enables passive, or inherent, safety features to be built into the reactor design. It is based on technology developed at the USA’s Oak Ridge National Laboratory, and integrates the primary reactor components, including the graphite moderator, into a sealed and replaceable reactor core unit with an operating lifetime of seven years. Looking towards ammonia production, Terrestrial Energy has entered into a partnership with KBR to integrate the processes for hydrogen and ammonia production, and is currently seeking permits for its technology in North America. It hopes to have its first reactors operational by 2030.
UAE
While the UAE is currently developing blue ammonia capacity using carbon capture technology, it is also looking towards nuclear power to help decarbonise and has indicated that it is interested in using nuclear energy to make ammonia. The Emirates Nuclear Energy Corporation (ENEC) recently successfully started-up a fourth reactor at its Barakah Nuclear Energy Plant which uses pressurised water to generate up to 1.4 GW of electricity. Once fully operational, Barakh will be providing 25% of UAE electricity demand. In advance of COP 28 in Dubai, ENEC also launched a programme called ADVANCE to evaluate technologies in the advanced, small modular reactor and microreactor categories, which can generate both electricity as well as process heat for industrial processes. It hopes to harness these to help decarbonise heavy and energy intensive industries, such as steel, aluminium, oil, gas, cement and chemical/ fertilizer production in order to achieve the UAE’s target of net zero carbon emissions by 2050. Last year, the UAE launched a national hydrogen strategy which forecast the production of 1.4 million t/a of low carbon hydrogen by 2031 and 15 million t/a by 2050. The country is aiming to generate 15 million tonnes by 2050. The plants will be developed in centres dubbed ‘hydrogen oases’. Two hubs have already been identified: one in Ruwais and the other in Kizad, Abu Dhabi, with a third possibly to be established in the port emirate of Fujairah. The UAE has also established partnerships with Germany, Japan and South Korea to export its future production.
References