Sulphur 397 Nov-Dec 2021
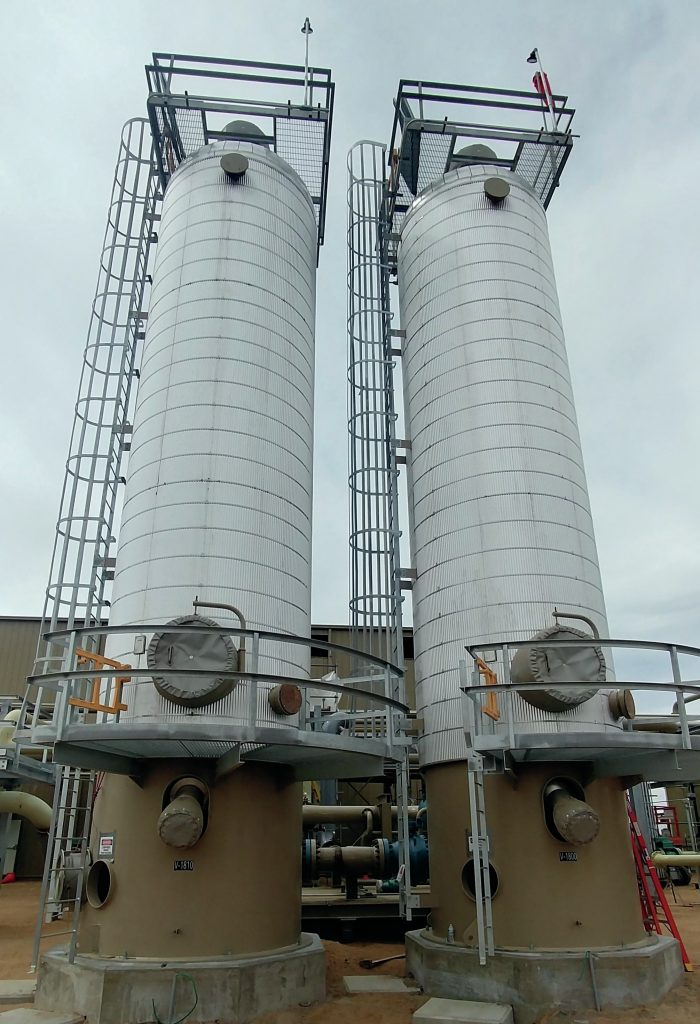
30 November 2021
A new low-cost H2S scavenger
SMALL-SCALE H2S REMOVAL
A new low-cost H2S scavenger
New low-cost metal oxide solid scavengers for hydrogen sulphide (H2S) removal from wet and dry natural gas have been developed and deployed at commercial scale. The desulphurisation process uses a proprietary sorbent chemistry to achieve a high sulphur capacity and removal efficiency. G. Alptekin, F. Kugler and M. Schaefer of SulfaTrap LLC describe the new technology and its performance.
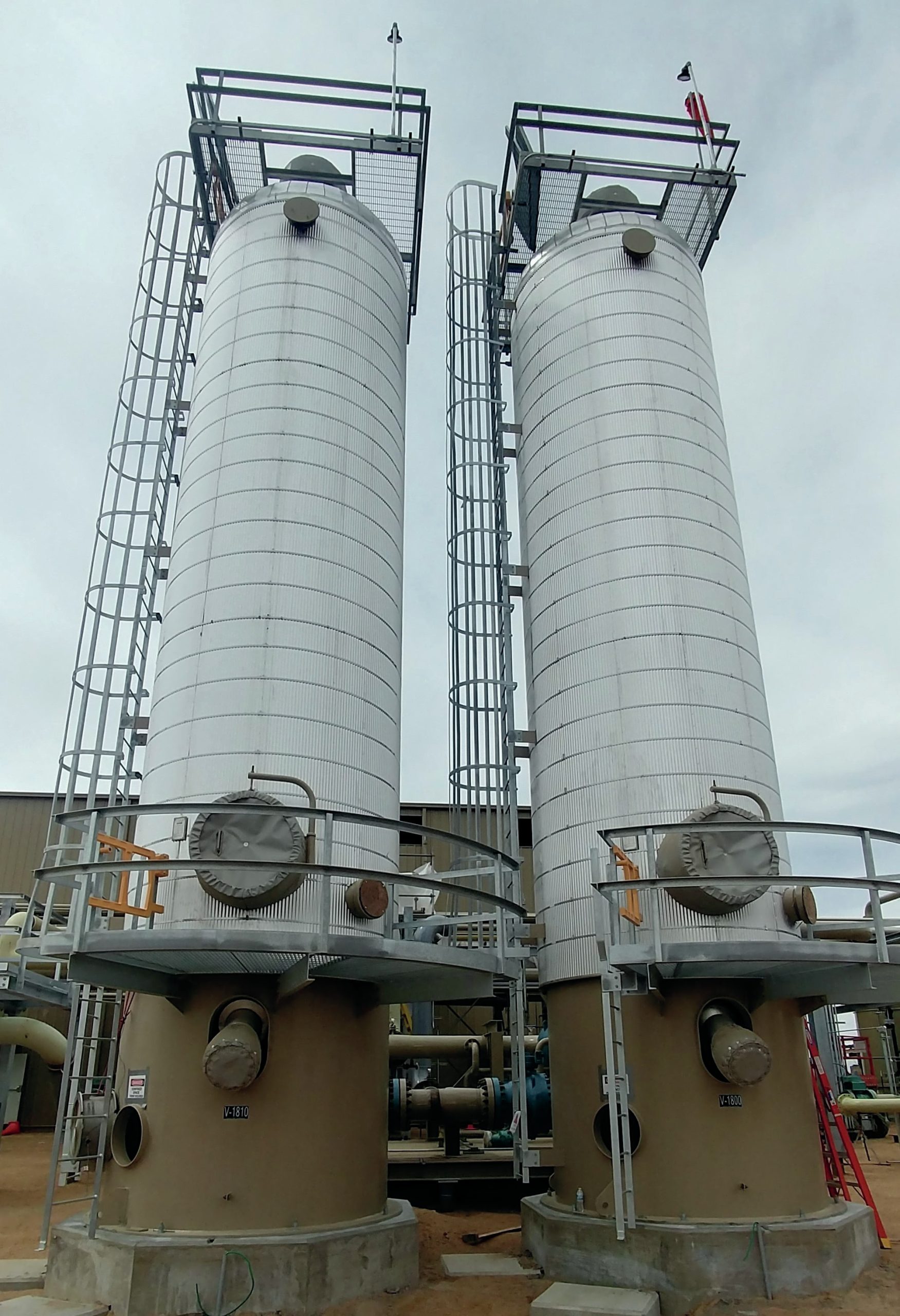
In large gas processing plants, H2S is typically removed from the natural gas by amine solvent scrubbing. While amine wash works effectively to bring the sulphur concentration to levels acceptable for pipeline utilisation, the remaining sulphur concentration is typically too high for using the gas in chemical synthesis applications (e.g., steam methane reforming). Also, the high capital cost associated with amine scrubbing systems make their operation more suitable for large scale applications. As a rule of thumb, amine systems are cost effective for applications requiring higher than 10 t/d sulphur (Fig. 1). The solid-state sorbents are commonly used for polishing and small-scale H2S removal (typical sulphur removal need is less than 1 t/d). Liquid scavengers (e.g., triazine) operate cost effectively in the intermediate range (1-10 t/d).
New technology
SulfaTrap LLC recently introduced the SulfaTrap™ -R7 series sorbents for high performance H2S removal. The very high sulphur uptake achieved by these sorbents and their relatively low cost enable their use in an expendable manner (the media is replaced periodically as it is saturated with the sulphur compounds). The SulfaTrap™ -R7 sorbents consist of transition metal oxides that can remove the H2S via a chemical reaction. SulfaTrap™ -R7Q is an iron-based absorbent that is effective for treating “wet” gas streams containing at least 2,000 ppmv H2O. The SulfaTrap™ -R7J is a copper-based absorbent that can treat dry (or wet) gases containing as low as 0-2,000 ppmv H2O. The reaction between the metal oxide and H2 S forms a stable metal sulphide as described by the sulphidation reaction below:

The reaction produces one mole of water for every mole of H2 S removed which results in net water production. For process feed streams saturated with water, a condensate management strategy must be in place to prevent accumulation of liquid water in the sorbent beds. This may consist of dew point control via process heating and insulation or automatic draining of liquid water from the bottom of the sorbent vessel. The adsorption reaction is exothermic, which results in a modest adiabatic temperature rise depending on the inlet concentration of H2 S. The magnitude of the adiabatic temperature rise depends on the reactivity of the metal oxide. The expected heat of adsorption is between 30-100 kJ/ mol H2 S, which corresponds to a 20-30°C adiabatic temperature rise for every 1 vol-% H2 S removed from the gas.
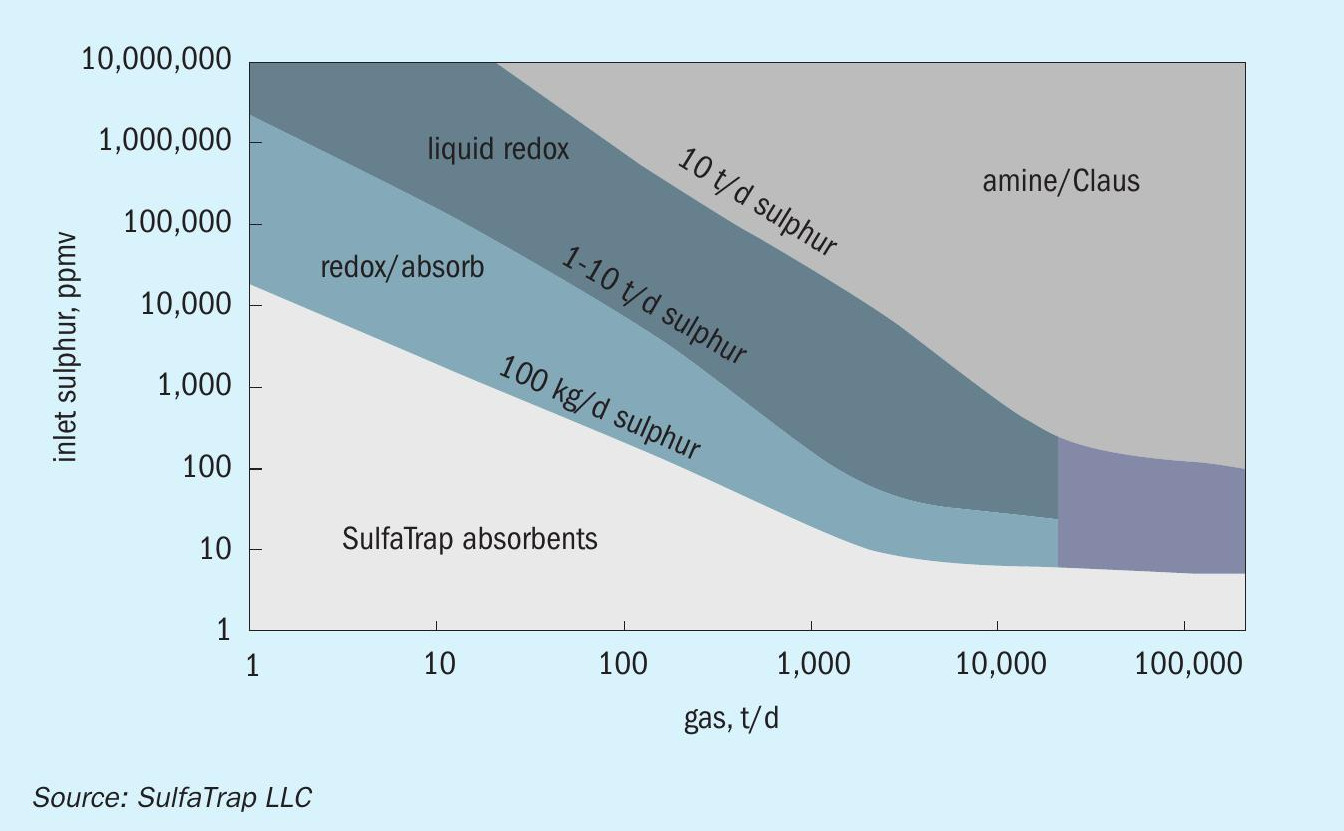
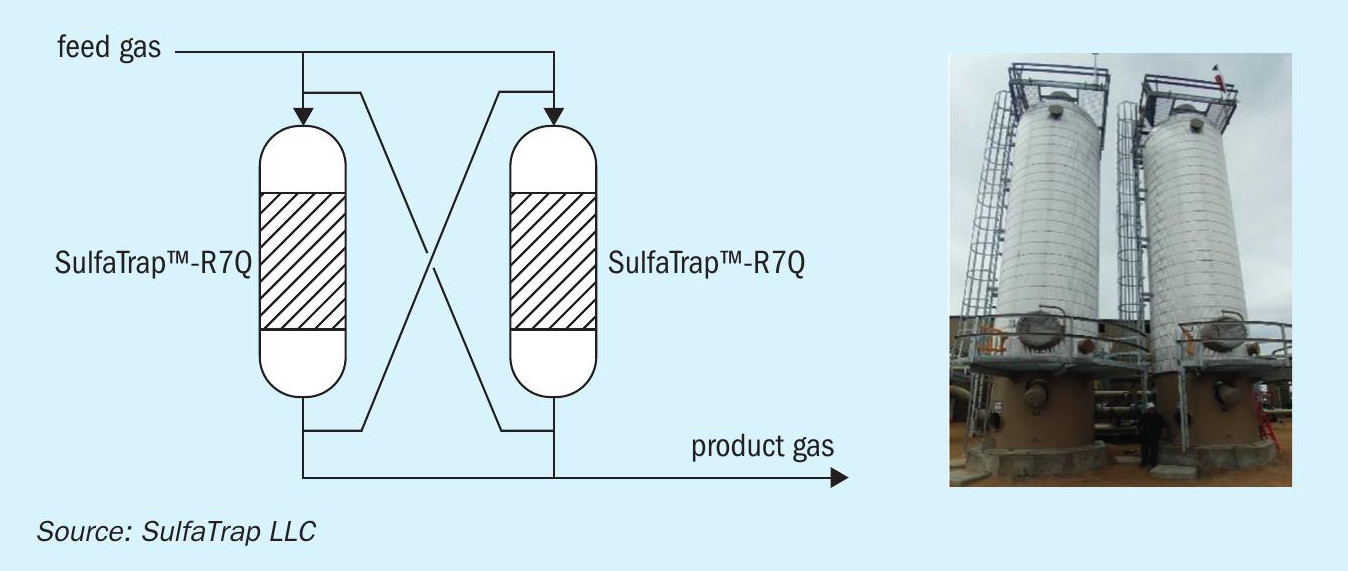
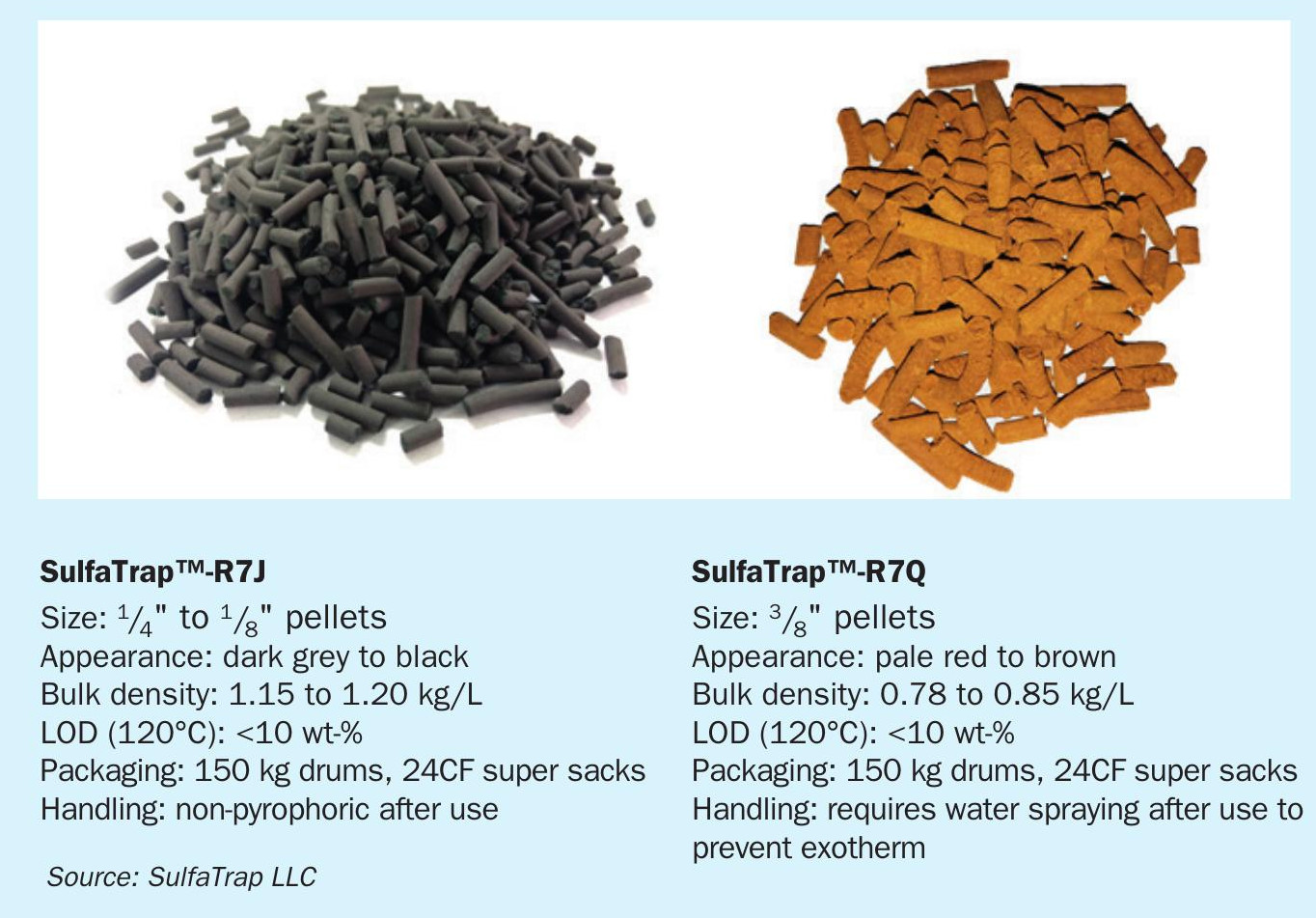
For best utilisation of the sorbent (i.e., to achieve the highest sulphur uptake), it is recommended that the sorbent is housed in two beds operating in lead-lag configuration, where the bed in the lead position removes the bulk of the sulphur, and the bed in the lag position serves as a polisher to reduce the outlet sulphur concentration to ultra-low levels (Fig. 2 left). Once the lead bed is saturated with sulphur, this vessel will be isolated for sorbent replacement while the lag bed provides all sulphur removal during this time. After the lead vessel is refilled with the fresh sorbent, it is placed back online in the lag position for another period of operation. This scheme allows continuous operation while maximising the sorbent utilisation. Typical changeout frequency of the sorbent is adjusted based on the site requirement (typical bed life can range from 3 to 12 months). An example of a lead-lag system treating 230 MMSCFD compressed natural gas (CNG) designed and fabricated by SulfaTrap LLC is shown in Fig. 2 (right). This system consists of two 45-m3 vessels rated for 1,100 psig.
The SulfaTrap™ -R7 family sorbents maintain their mechanical integrity and physical structure after use. Both types of media can be easily removed from the vessels at the end of their useful life, either by using vacuum evacuation (directly transferring the material to a vacuum truck) or by gravity drain. As in common practice, SulfaTrap LLC recommends purging the “spent” sorbent bed with nitrogen at low pressure (after the bed is taken offline and isolated), and prior to the removal of media from the bed. The SulfaTrap™-R7Q sorbent, due to the formation of an iron sulphide phase (FeS),requires treatment with water to eliminate any potential exotherm due to exposure to air. The water quench can be applied inside the vessel housing or to the media taken outside (due to the relatively mild exotherm water can be sprayed onto the media after it is removed from the bed). On the other hand, the “spent” SulfaTrap™ -R7J material is not pyrophoric after use and exposure to air does not cause any heating at all.Neither material requires activation prior to use, and both consist of inexpensive metal oxides and ceramic binders; hence can be used cost effectively in a once-through, expendable manner. A comparison of the sorbent properties is shown in Fig. 3.
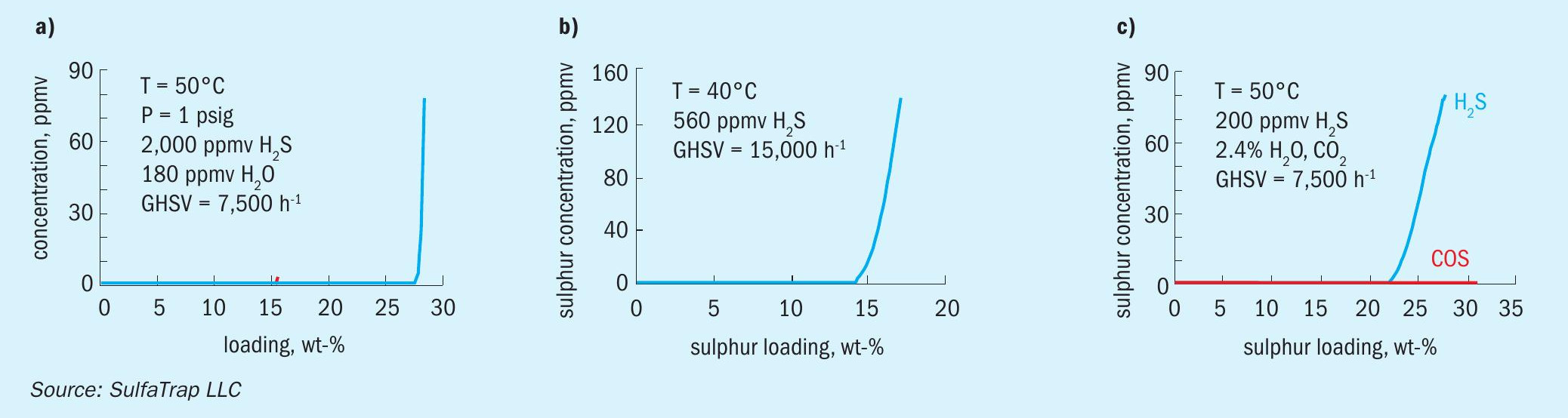
The SulfaTrap™ -R7J dry gas sorbent can achieve a minimum of 27 wt-% S loading at breakthrough (27 kg sulphur removed per 100 kg of sorbent). A representative breakthrough profile is shown in Fig. 4(a) for a natural gas stream containing 2,000 ppm H2 S with only 180 ppm H2 O. The gas hourly space velocity (GHSV) for the test was 7,500 h-1 corresponding to a gas-solid contact time of 0.48 sec. The sharp breakthrough profile even at such short gas-solid contact times suggests rapid sulphur uptake kinetics, resulting in excellent sorbent utilisation and high sulphur capacity in compact vessels.
SulfaTrap™ -R7J sorbent can also effectively treat light hydrocarbon streams. Fig. 4(b) shows the H2 S breakthrough profile while treating a liquefied petroleum gas (LPG) stream. While in this example, the LPG is treated in the gas phase, the sorbent is equally effective when treating the LPG in liquid form. The sorbent achieves 18 wt-% S uptake at saturation.
In treating the wet gases SulfaTrap™ -R7Q sorbent achieves up to 35 wt-% S uptake (35 kg of sulphur removed per 100 kg sorbent) at full saturation. A breakthrough profile for a CO2 stream containing 200 ppmv H2 S and 2.4 vol-% H2 O is shown in Fig. 4(c). This material exhibits a relatively shallow breakthrough profile, but the sulphidation kinetics is much faster (gas-solid contact time is 0.48 sec) than other iron-based commercial sorbents. Notably, the SulfaTrap™ -R7Q sorbent does not promote the formation of carbonyl sulphide (COS) in the presence of high concentrations of CO2 .
Both SulfaTrap™ -R7J and SulfaTrap™ -R7Q have been deployed at commercial scale with proven results treating a wide range of natural gas and LPG feedstocks in numerous sites (gas treatment plants, biogas/landfill gas treatment systems, synthesis gas desulphurisation) in the US, Canada, Europe and the Middle East.
Summary and conclusions
New metal oxide-based sorbents have been developed for removing the H2 S from hydrocarbon gas streams. The sorbent can achieve a high sulphur capacity and removal efficiency. The results from proof-of-concept experiments and field applications show that high sulphur uptake is achievable for treatment of both wet and dry gas streams with favourable economics using relatively low-cost capital systems.