Nitrogen+Syngas 366 Jul-Aug 2020
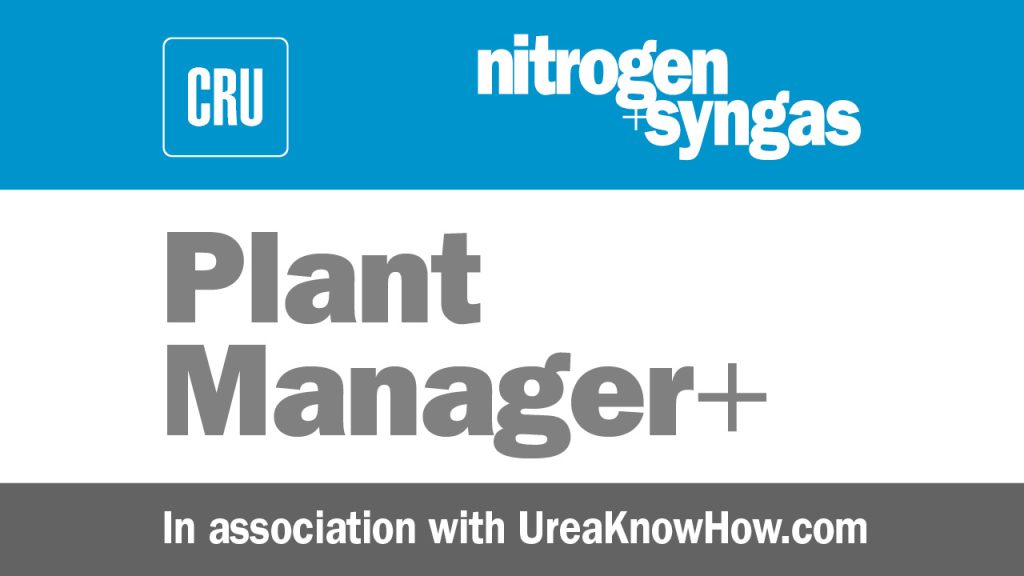
31 July 2020
Incident No. 1: Leak in nozzle in urea reactor bottom
High pressure urea equipment often has lined nozzles. A lined nozzle is a full strength carbon steel nozzle that is protected against carbamate corrosion by a 5 or 6 mm thick stainless steel liner plate, which is welded to the carbon steel nozzle on either end. This design is however very vulnerable to fatigue cracking due to the difference in thermal expansion between the austenite liner and the carbon steel nozzle. History shows that such a design will lead to cracking in the long term. The following case study reports on a serious incident in a urea plant where a leak in a urea reactor nozzle caused a plant shutdown but could have resulted in rupture of the high pressure vessel.
Event description
Operators noted an excessive leak in the bottom forged head of the urea reactor in a CO2 stripping technology 700 t/d urea plant from 1971. The leak detection holes did not indicate any leak. A crack of 50.8 mm was found adjacent to a 203.2 mm nozzle. Extensive thickness gauging was carried out on the head from outside and revealed corrosion on an area about 800 mm in diameter. Thickness loss was intensive in the vicinity of the split where the measured thickness was only a few millimetres. The bottom dished liner section (1,000 mm in diameter) on the lower head was found to be buckled and a corroded groove was noted in the weld between this liner section and the collar around the inner lining sleeve of the 203.2 mm bottom nozzle. This groove was located on the opposite side to the zone of maximum thickness loss and the open split in the lower head. The bottom dished liner section was cut and removed. A thick layer of corrosion products was found covering the carbon steel head. This layer was washed out and the terrifying topography of corroded surfaces was exposed. The removed dished liner section was found corroded on the backside at many locations. Leak detection holes in the lower head as well as in the attached nozzles were found plugged with corrosion products. A corroded hole 30 mm X 70 mm was noted in the lining sleeve inside the 203.2 mm bottom nozzle.
Immediate response action
The plant was shut down when the leakage was identified. The reactor bottom was repaired.
Causes
The locations of the corroded groove in collar weld, the opening in the lining sleeve and the area of most corrosion action and the open split in the carbon steel head all assumed that the whole problem started by a local damage, most probably cracking on the lap weld joint between the bottom liner section and the sealing collar around the lining sleeve inside the 203.2 mm bottom nozzle. This was followed by a seepage of the corrosive solution to the lower carbon steel head. Leak detection holes in the area were blocked with corrosion products and detection of the occurred leak was thus prohibited. Corrosion action continued for a prolonged time with a pronounced rate on the area around the developed crack in liner weld until the head was split open in that area.
Primary consequence:
- Near miss of rupture of high pressure vessel.
Secondary consequence:
- Unplanned shutdown for a significant number of days costing >US$1 million.
Urea reactor design
The urea reactor is designed to operate at 160 kg/cm2 and 200°C and was operating at 140 kg/cm2 and 183°C. The reactor has a diameter of 1.68 m and length of 37.5 m. The bottom forging is 50 mm thick. The bottom cup has four nozzles, three of them fitted vertically to the bottom and the fourth one fitted horizontally on the side of the lower cup. The whole shell of the reactor and nozzles are lined with 5 mm 316L stainless steel material. The reactor liner is made up of nine stainless steel segments or compartments, backed with two 10 mm weepholes for each compartment. The weepholes are drilled through the carbon steel shell. The top and bottom cups are also protected with weepholes.
Risk level:
There was a high risk of a major incident.
Prevention safeguards:
- Perform corrosion inspections during turnarounds;
- Apply a solid stainless steel/duplex design of nozzle to avoid thermal cracking risks;
- Assure a proper leak detection system (active vacuum based system with an accurate and reliable ammonia detector).
Mitigation safeguards:
In case of a leak, confirm and locate the leak, shut down the plant and drain the synthesis section as soon as possible.
Additional causes to consider:
- Fatigue cracking at nozzle (bad design);
- No proper leak detection system;
- Nozzle design of HP urea equipment.
UreaKnowHow.com prefers a solid stainless steel/duplex nozzle design for high pressure urea equipment.
This case study report is one of many serious incident reports on UreaKnowHow.com’s Fertilizer Industry Operational Risks Database, FIORDA, which has been created for collecting and sharing process safety and reliability information among participating companies in the fertilizer industry.