Nitrogen+Syngas 363 Jan-Feb 2020
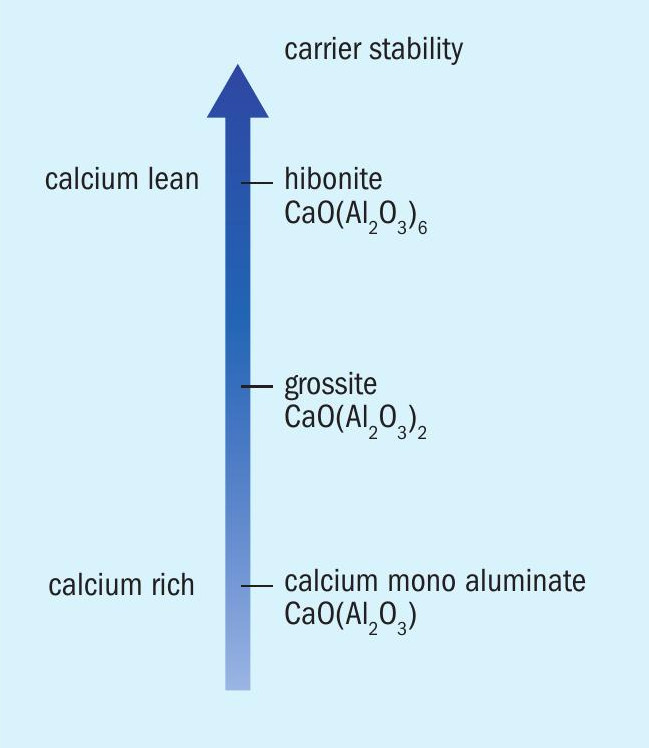
31 January 2020
Novel carrier improves performance
STEAM REFORMING CATALYSTS
Novel carrier improves performance
The increased severity of operating conditions in modern steam methane reformers requires catalysts with high catalyst activity and good mechanical stability to avoid premature replacements or unplanned shutdowns. F. Morales Cano, M. Stenseng and M. Feddersen of Haldor Topsoe describe a new catalyst formulation with a very homogenous and stable carrier material delivering the high activity and high mechanical strength required for long time operation.
Even mature areas like steam reforming catalysts have room for improvements. By investing in R&D and performing fundamental studies of the different carrier systems and their properties during fabrication and industrial use, Topsoe has developed a new and more robust carrier system. This system forms the basis for a new range of Topsoe steam reforming catalysts – the TITAN ™ series.
What defines a good steam reforming catalyst?
In order to have a well-functioning steam reforming catalyst, the following objectives should be met:
- high and stable activity which ensures conversion very close to equilibrium at the outlet of the tubes;
- ability to avoid carbon formation in the upper part of the tubes;
- good resistance to the small amounts of sulphur which enters with the feed streams;
- a catalyst shape which results in a low pressure drop across the reformer;
- high mechanical strength to withstand the thermal cycles taking place throughout its lifetime.
All of the above points are very much dependent on the design and formulation of the carrier material, as this is the main platform for making the finished active catalyst and fulfilling the above objectives.
Hibonite-rich carrier system
The new series of TITAN ™ catalysts comprises a hibonite (CaAl 12 O 19 )-rich carrier with excellent mechanical and thermal stability under the harsh operation conditions in reformers. The manufacturing process involves solid-state synthesis methods in the presence of titanium (Ti) promoters, which enhance the hibonite formation and minimise the formation of calcium (Ca)-rich aluminate phases such as grossite (CaAl 4 O 7 ) and calcium mono-aluminate (CaAl 2 O 4 ). As revealed from Topsoe’s detailed fundamental studies, Ca-rich aluminate phases may have a negative impact on the catalyst performance and therefore a carrier with a high fraction of hibonite phase is most desirable, as depicted in Fig. 1.
The addition of Ti promoters decreases the free energy of formation of hibonite during the synthesis process, leading to higher hibonite content in the new carrier system. The hibonite phase features hexagonal plate-like grains arranged in a three-dimensional structure providing a highly porous structure whilst ensuring excellent mechanical strength and stability (see Fig. 2).
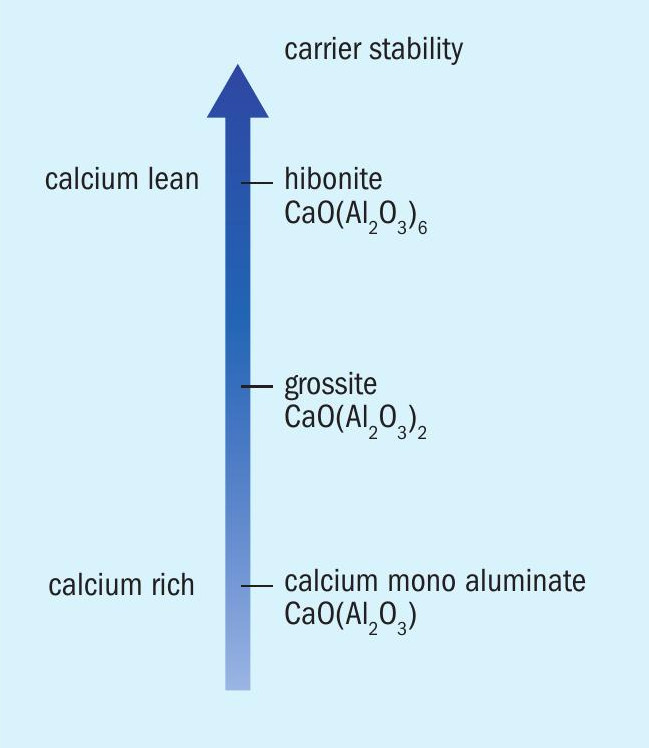
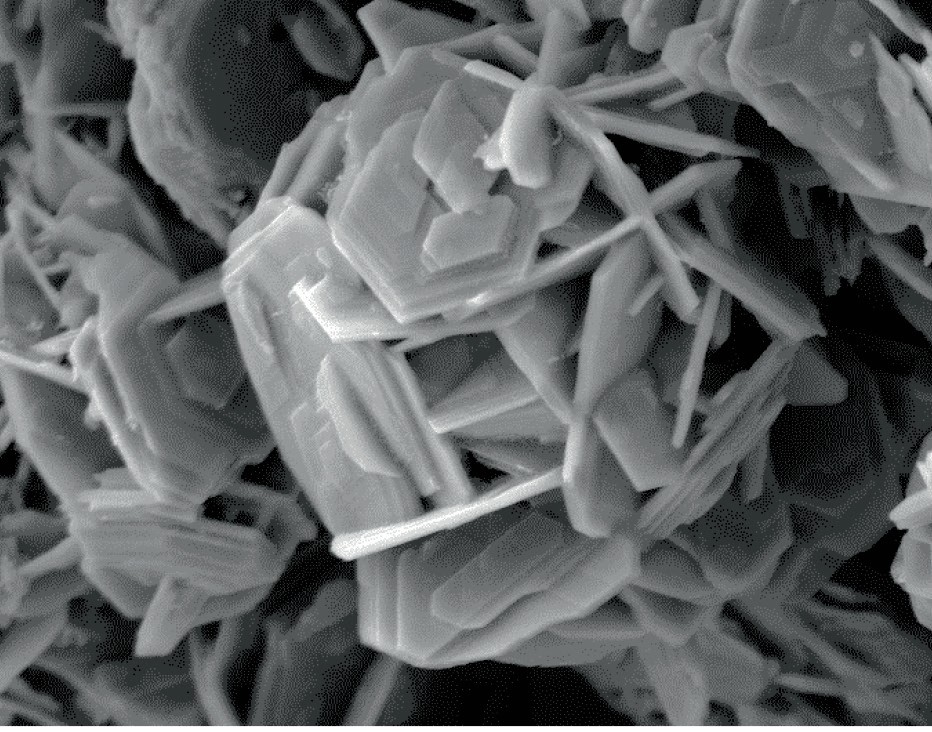
Nickel is loaded onto the carrier by means of novel impregnation methods that enable the deposition of small and well dispersed nickel nanoparticles over the hibonite platelets, as seen in Fig. 3. The result is an innovative catalyst with very high and stable reforming activity throughout the catalyst lifetime and with an improved end-of-run activity.
During reforming operation, any reforming catalyst will unavoidably age and lose some active surface area due to sintering of the active nickel nanoparticles on the catalyst surface and consequently, it will lose some catalytic activity. The sintering phenomena occur gradually over time, and the degree of sintering depends on the operating conditions as well as the composition and microstructure of the catalyst. An advantage of the new TITAN ™ catalyst series is the unique hibonite-rich microstructure with outstanding thermal stability, resulting in a low and contained sintering of the Ni particles during the catalyst lifetime; in other words, the catalytic activity will remain more stable towards end-of-run, relative to other conventional industrial catalysts.
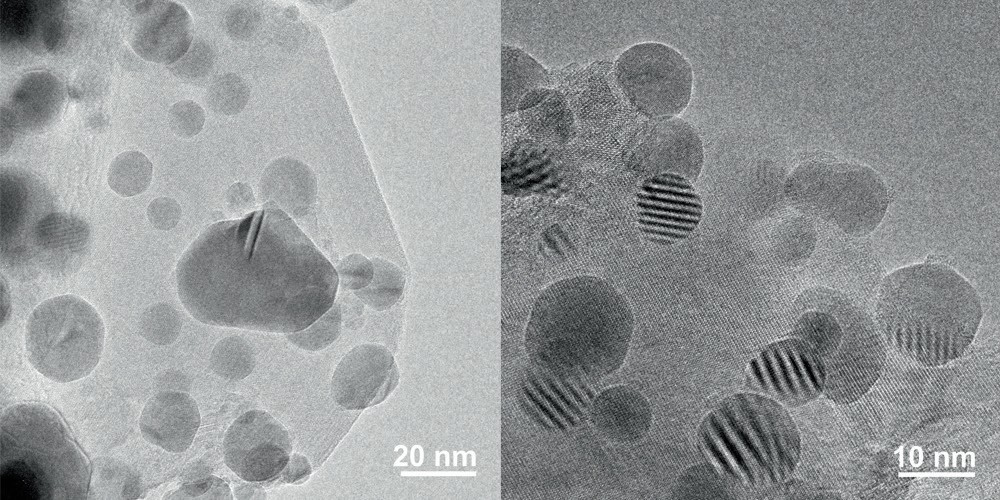

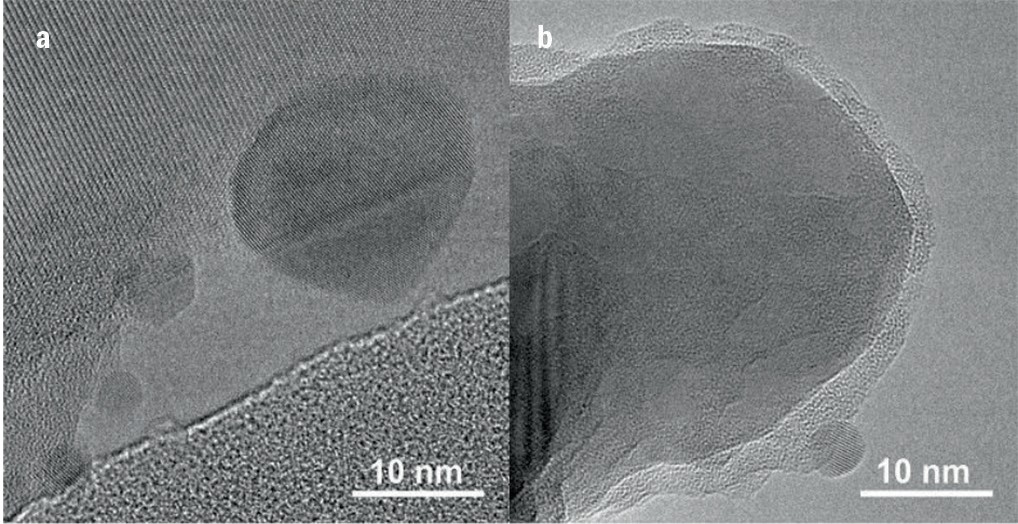
Fundamental studies
The hibonite-rich composition of the new carrier system provides a remarkable boost of the catalytic performance of the new TITAN ™ series, which becomes evident after long operation times in the reformer. In order to simulate several years of operation in a reformer, Topsoe has carried out aging treatments of different catalysts in the lab under controlled atmospheres by applying high temperature and high steam pressure conditions. The purpose is to induce sintering of the nickel particles as it occurs during aging in industry. The synthesis and evaluation of catalysts containing variable hibonite contents, as determined by X-ray powder diffraction (XRPD), has led to new insights on the optimal calcium aluminate composition for reforming applications.
As seen in Fig. 4, the carrier composition has indeed a strong influence on the activity per mass of catalyst. As the hibonite content increases in the aged catalysts, the reforming activity follows the same trend; the highest methane reforming activity was achieved with the most Ca-lean aluminate carrier containing over 80 wt-% hibonite.
The results from fundamental studies reveal that the superior activity of the hibonite-rich catalyst is attributed to:
- the ability of the hibonite structure to stabilise small Ni particles;
- the higher number of nickel active sites on the hibonite carrier due to absence of free CaO species potentially binding to the nickel surface.
Topsoe has observed the latter phenomenon for grossite-rich catalysts using combined in-situ transmission electron microscopy (TEM) and electron energy loss spectroscopy (EELS) studies. The results reveal that the new TITAN ™ catalyst contains smaller nickel particles, relative to the more calcium-rich (grossite) catalysts, thus providing a larger active nickel surface area for the reforming reactions.
In-situ TEM studies show that grossiterich catalysts are more difficult to reduce due to the presence of CaO species forming an overlayer on the nickel particles that blocks some of the active nickel sites. Fig. 5 displays an example of an aged TITAN ™ catalyst (a) and an aged grossite-rich catalyst (b), inspected by in-situ TEM under reductive atmosphere. The nickel particles on the TITAN ™ catalyst reduced easily to metallic nickel after short reduction times and exhibited a very clean nickel surface. On the other hand, the nickel particles supported on the grossite-rich carrier did not fully reduce under the same conditions even after longer reduction times, since a NiO overlayer was still present around the nickel particles. This is evident in Fig. 6b by the oxygen signal around the particle. Fig. 6 shows elemental chemical maps produced by scanning transmission electron microscopy (STEM-EELS). The reason for the hampered nickel reduction is ascribed to the presence of CaO species on the nickel surface, as indicated by the EELS calcium chemical map from Fig. 6c. The EELS maps acquired on the same sample area from Fig. 5b confirm the presence of a CaO layer encapsulating the nickel particle. The results are therefore consistent with the much lower reforming activity of the grossite-rich catalyst.
Benchmarking of industrial catalysts
The reforming activity of the RC-67 TITAN ™ catalyst was benchmarked against two other industrial catalysts well established in the market. The catalyst samples were firstly aged in the lab and subsequently tested for methane reforming activity as well as measured for sulphur capacity. As seen in Fig. 7, the activity of the RC-67 TITAN ™ catalyst is much higher than the other two industrial catalysts, which exhibit relative activities below 30%. The sulphur capacities obtained for the two conventional catalysts were also significantly lower than for the TITAN ™ catalyst.
The phase quantification in the three aged catalysts reveals that the hibonite content is also substantially higher in RC-67 TITAN ™ . It is therefore demonstrated that a high fraction of hibonite in the catalyst is crucial for ensuring superior high reforming activity and stability.
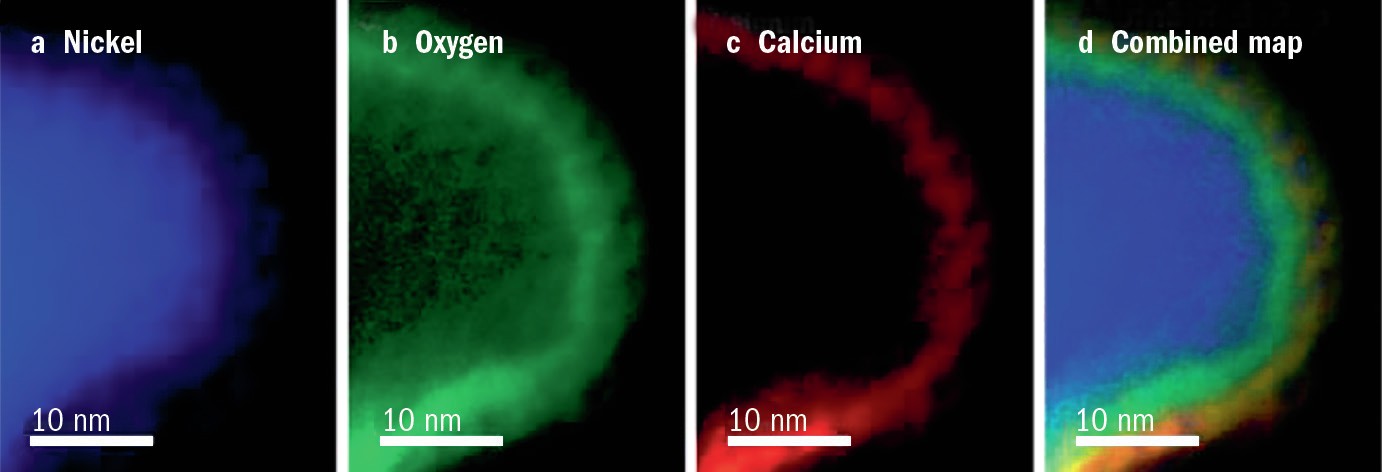
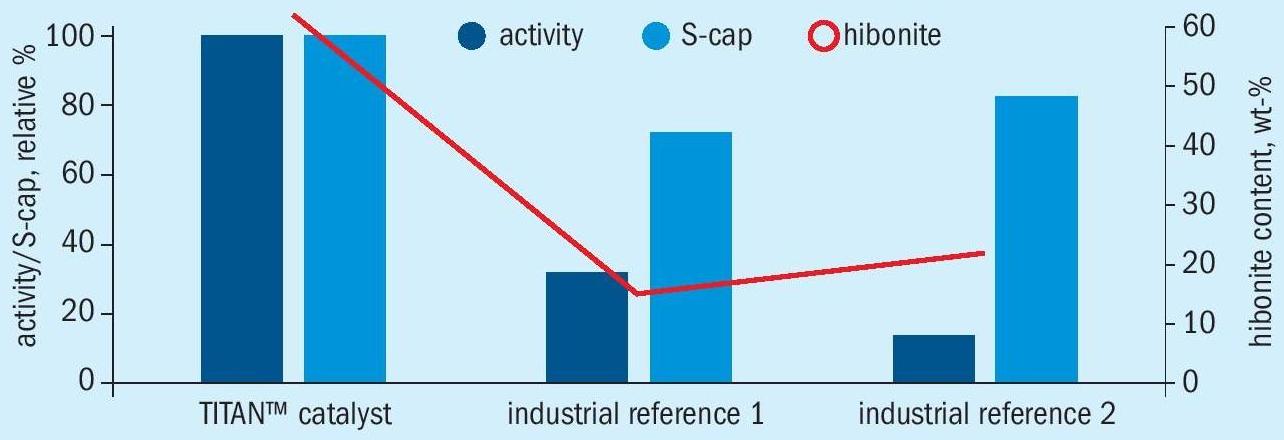
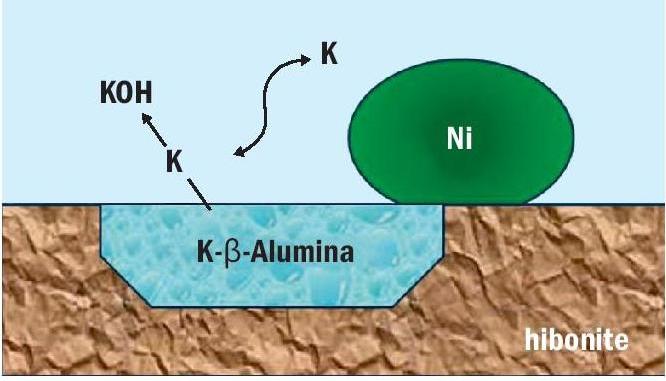
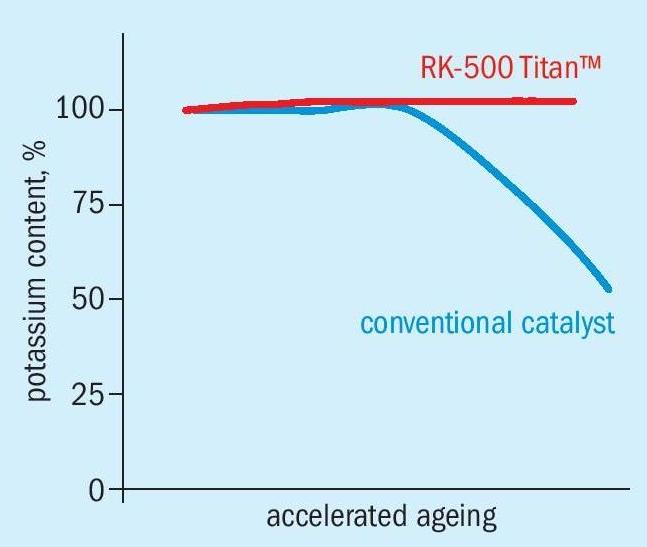
Alkali-promoted TITAN ™ catalyst to reduce carbon formation
Potassium-promoted catalysts have long been used to reduce carbon formation in top-fired reformers and/or when operating with heavy natural gas as feedstock in the plant. While the previous generations of alkali-promoted reforming catalysts have been successfully applied for many decades, the use of these catalysts may, due to low potassium stability, result in alkali fouling downstream. This was mitigated by the introduction of the RK-400 catalyst series. Building on this know-how, the TITAN ™ series includes a new generation alkali-promoted calcium aluminate-supported catalyst, promising more reliable and efficient protection against carbon formation and higher catalytic activity than older conventional catalysts. The new catalyst is based on a hibonite-rich carrier where potassium is bound into the carrier as a K-beta-alumina phase, forming an integral part of the carrier structure. The K-beta-alumina phase is designed to be a potassium reservoir that ensures slow, gradual and stable release of potassium to the nickel particles. Fig. 8 illustrates how the potassium partially adsorbs on the nickel step sites, thus preventing nucleation of graphene islands and formation of pyrolytic carbon.
This design of the new TITAN ™ alkali-promoted catalyst also minimises the leaching of potassium during operation, which is known to be a problem for downstream exchangers when operating with some non-Topsoe catalysts. Fig. 9 illustrates the superiority of the RK-500 TITAN ™ with respect to potassium stability compared to conventional catalysts.
Industrial experience
A well-performing tubular reforming catalyst has a huge impact on the overall economics of the industrial unit. This impact is due to various improvements in process parameters that are monitored during daily operation. The following two examples illustrate improvements that have materialised after the installation of TITAN ™ catalysts.
Example 1: 1,620 t/d ammonia plant
The first example is an ammonia plant with a top-fired reformer operating with a competitor catalyst. The plant was operating very far from equilibrium, resulting in much higher methane leakage than necessary. After installing TITAN ™ catalysts in their reformer, a large performance improvement was observed. The methane slip was lower and the approach to reforming equilibrium was reduced by 15°C compared to the previous catalyst after approximately six months of operation. The decreased methane leakage results in a better utilisation of the natural gas feedstock and a lower inert level in the ammonia synthesis loop, resulting in lower opex.
Example 2: 825 t/d ammonia plant
The second example is an ammonia plant that used to run competitor catalyst. When the TITAN ™ catalyst was installed, the pressure drop was lower than for the previous catalyst at start-of-run even though the plant load was more than 25% higher. The decreased pressure drop enables the plant to increase its throughput even further.
Due to its excellent properties and high performance, Topsoe’s TITAN ™ tubular reforming catalyst has quickly taken off in the reforming market, obtaining 18 references in 14 months.