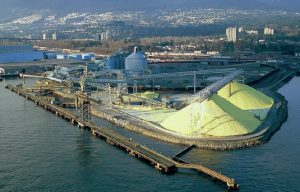
Canadian sulphur
After many years of slow decline, Canadian sulphur exports have begun to rise slightly, but dwindling US markets are seeing a move towards more sulphur forming to expand export opportunities.
After many years of slow decline, Canadian sulphur exports have begun to rise slightly, but dwindling US markets are seeing a move towards more sulphur forming to expand export opportunities.
A look back at some of the major events of 2020 for the sulphur and sulphuric acid industries, as well as a look forward as to how 2021 might look.
Demand for oil in developed countries was already falling before the coronavirus outbreak, and consumption growth is slowing in the developing world. Peak oil demand may arrive in the next decade. Coupled with more reinjection of sour gas rather than sulphur extraction, could we be seeing falling elemental sulphur production in a decade or so?
Although 2019 had been a volatile year for acid markets, with shutdowns disrupting supply, the coronavirus outbreak wrought even more havoc in 2020, across both supply and demand.
Sulphur reports on this year’s Sour Oil and Gas Advanced Technology (SOGAT) conference, which was run as a virtual event at the end of September 2020.
New approaches and novel processing schemes employing oxygen enrichment in sulphur recovery units have been developed and commercialised. In this feature Siirtec Nigi, Linde, Blasch, Fluor and RATE report on their latest developments.
Several highly corrosion resistant materials are available today for use in handling process fluids encountered in the production of concentrated sulphuric acid. These alloys, properly selected for the operating conditions, provide the benefits of long operating life under harsh operating conditions extending the period of uninterrupted production cycles and lowering the incidence of catastrophic equipment failure. In this article, M. J. Cooke of Weir Minerals discusses materials of construction for pumps, valves and piping used in the production of sulphuric acid.
A. Bhargav and A. Krishnan of Helium Consulting Pvt. Ltd discuss how it is possible to reduce SOx emissions within the existing system setup of an oil refinery or gas plant through detailed analysis, expedited corrective actions and the use of automated algorithms in real-time, by using a digital IIoT solution to monitor, control and optimise.
K. Hanlon Kinsberg and J. Lewis of Comprimo review the main approaches for mercaptan removal in gas processing plants, based on past project experience and generally accepted industry practice.
Undegassed molten sulphur can contain several hundred ppmw H2 S. If the headspace in the storage tank is stagnant, the H2 S can accumulate in the vapour space above undegassed liquid sulphur to dangerous levels. Sweeping and blanketing systems are commonly applied to manage the explosion risk in the headspace of molten sulphur storage tanks. D. J. Sachde , C. M. Beitler , K. E. McIntush , and K. S. Fisher of Trimeric Corporation review these approaches, outlining the benefits and limitations, design considerations, and industry experience/guidance for each approach. Calculation methods for natural draft flow of sweep air are also presented.