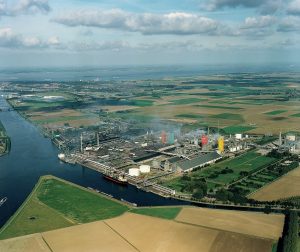
The future of Europe’s nitrogen industry
High feedstock prices and regulatory burdens continue to put pressure on European nitrogen producers to innovate.
High feedstock prices and regulatory burdens continue to put pressure on European nitrogen producers to innovate.
New innovations, services and latest technologies to improve the operation and reliability of steam methane reformers from AMETEK Land, Kontrolltechnik, BD Energy Systems, Koch Engineered Solutions, and Quest integrity.
Haldor Topsoe has appointed Elena Scaltritti as the company’s new chief commercial officer. She will take up her new position no later than July 1st, 2022. She has previously been executive vice president at Korea’s SONGWON Industrial Group, where she was responsible for the group’s commercial activities.
The COP-26 summit in Glasgow last year signed into force new rules on carbon emissions trading which may gradually start to see carbon pricing spread worldwide, with knock-on effects on emissions intensive industries like ammonia and methanol.
A complete listing of all articles and news items that appeared in Nitrogen+Syngas magazine during 2021.
The production of syngas from hydrocarbon feedstock uses a number of catalytic steps to increase efficiency and maximise conversion while minimising energy consumption. In this article we report on the latest developments in water gas shift catalysis from Johnson Matthey, Clariant and Topsoe, and shift converter design from Casale.
A proper leak detection system for loose liners of high-pressure urea equipment is the number one safeguard for any urea plant, as has been proven by detailed safety studies and incidents investigations. However, leak detection systems easily choke especially when urea is present in the leaking solution. When no urea is present, the ammonium carbamate will dissociate above 60°C when flashing to atmospheric pressure in the leak detection system. But, when urea is present, it can solidify and at higher temperatures polymerise into biuret and triuret, which have even higher crystallisation temperatures. An early and reliable leak detection system is therefore very important. UreaKnowHow.com has developed such a system: the state-of-the-art AMMO LASER Leak Detection System.
As a quick glance through the Index of last year’s articles and news items in this issue of the magazine will amply demonstrate, 2021 was a year full of project announcements for low carbon ammonia and methanol projects of all hues; blue, green, turquoise and many other shades besides. Market analysts CRU said in December that they calculated that there have been a total of 124 million t/a of low carbon ammonia projects announced, 80 million t/a of which came in 2021 alone, equivalent to 55% of current ammonia capacity. These range from tentative pilot plants that are fully costed and often with government grants already secured to blue sky visions of vast electrolysis hubs in the deserts of Arabia with timescales towards the end of the decade – it’s often the case that the longer the proposed timescale, the less likely a project is to happen.
The International Fertilizer Association (IFA) has signed a memorandum of understanding with the United Nations Food and Agriculture Organisation (FAO) over collaboration to support the FAO’s vision of transformative change and innovation in agriculture. Svein Tore Holsether, IFA Chair, signed the agreement at a live virtual signing in December together with FAO deputy director general Beth Bechdol. The agreement outlines collaboration to further shared goals and objectives with regard to the promotion of sustainable food and agriculture. Both parties will work together to raise awareness about the International Code of Conduct for the Sustainable Use and Management of Fertilizers (Fertilizer Code), promote education and knowledge transfer and continue their successful collaboration on fertilizer statistics.
The ammonia market has entered 2022 looking very different to last year, with early January Pivdenny prices $875/t higher on a mid-point basis than they were at the start of 2021, and the likelihood of further gains ahead.