Emissions
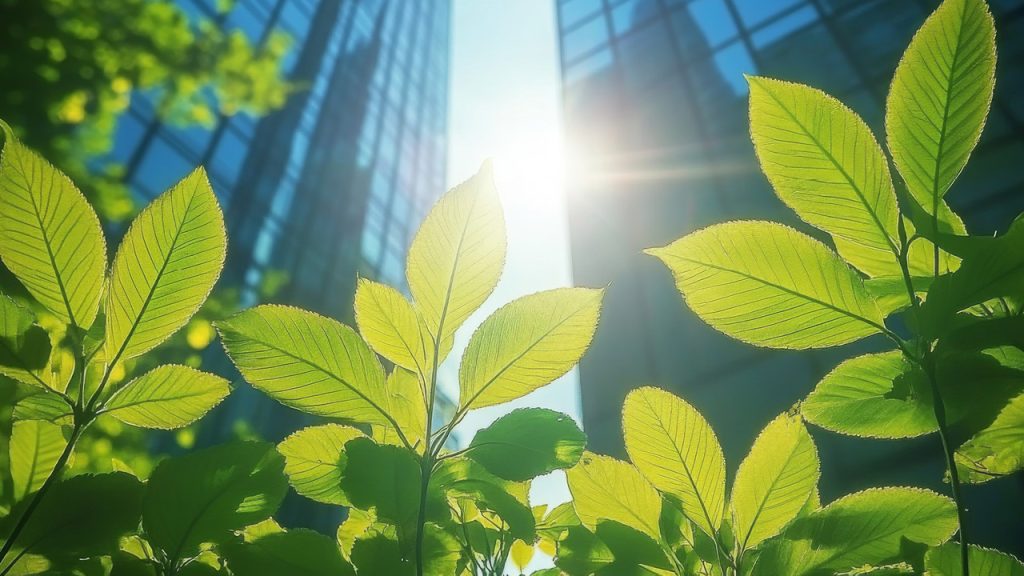
12 March 2025
Press Release: Metso launches sustainable copper sulfide concentrates leaching process with high copper recovery
Metso Corporation’s press release: 12 March 2025, at 09:00 a.m. EET
Metso is excited to launch its efficient Cu POX leaching process to address the needs of the copper extraction industry. As ore compositions change due to depletion of deposits and increasing environmental and efficiency demands, this cutting-edge solution not only maximizes copper recovery but also reduces environmental impact.
The Metso Cu POX process is a proven hydrometallurgical method for the treatment of copper sulfide concentrates at lower capacities. The heart of this process is Metso’s proprietary OKTOP® Autoclave unit, where copper concentrate is oxidized under high pressure and temperature. This results in a copper-bearing pregnant leach solution (PLS) to be further treated in solvent extraction and electrowinning processes, where copper is recovered as high-purity LME Grade A cathodes.
“Copper sulfide minerals require specialized leaching conditions to achieve high recovery rates. Metso’s Cu POX leaching utilizes high-temperature oxidation to convert sulfide sulfur into sulfate and sulfuric acid, ensuring efficient copper dissolution. This technology offers a high-performance solution with high, up to 99%, copper recovery rates, ensuring maximum extraction of valuable metals from the ore. The process also minimizes environmental impact by reducing emissions and optimizing the use of resources through, for example, closed loop process steps reducing the use of water,” says Petteri Pesonen, Technology Manager, Copper Hydrometallurgy at Metso.
The flexible and scalable Cu POX process accommodates various capacities and raw material compositions. The pre-designed process and equipment package enables fast ramp-up to production and integrates seamlessly with solvent extraction and electrowinning (SX – EW) infrastructure. The Cu POX plant can also be implemented to improve existing heap leaching – SX – EW operations to complete depleting heap leaching PLS production. In all cases, Metso can provide end-to-end expertise from batch tests, modelling and pilot tests to engineering, equipment deliveries and plant commissioning, and training. In addition, Metso provides services, spare parts and digital solutions to optimize continuous process and plant performance.
Full offering for copper
Most of the copper ores mined today are either oxides or sulfide ores. Both ore types require specific processes to extract the valuable minerals. With the broadest portfolio in the market and a large installed base and global lifecycle service capability, Metso’s offering for the copper industry covers both ore types from comminution to production of copper cathodes and anodes.