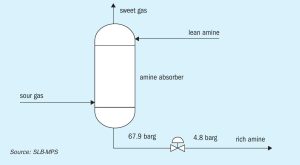
Energy optimisation in amine sweetening units
Aparna Saiju and Nishevitha U G of SLB-MPS explore the concept of energy optimisation using power recovery turbine (PRT) technology in amine sweetening units, focusing on its potential benefits, implementation strategies, and environmental implications.