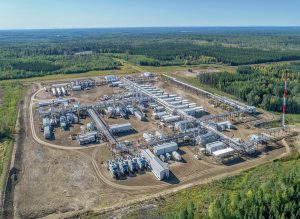
Treating highly sour gas
Sour gas processing presents a number of unique challenges, especially at high levels of hydrogen sulphide and carbon dioxide content.
Sour gas processing presents a number of unique challenges, especially at high levels of hydrogen sulphide and carbon dioxide content.
Euro Support’s new generation, titania-based low temperature tail gas catalyst shows a marked robustness to the start-up procedure compared to its common alumina-based counterparts. Dr B. Hereijgers of Euro Support discusses the promising lab results.
Automatic identification and optimum online monitoring using sonic velocity measurements can now be used to determine the concentration of both sulphuric acid and oleum.C. Kahrmann and T. Knape of SensoTech report on a new user-friendly method of measurement providing a significant step towards automated process control.
All acid towers eventually require replacement. In this article, K. Sirikan, A. Mahecha-Botero et al of NORAM Engineering and Constructors Ltd discuss two recently executed acid tower replacement projects. The first project involved the replacement of a brick-lined tower by an alloy acid tower for a sulphur burning plant in North America. The second project involved the replacement of a brick-lined acid tower with a NORAM designed brick-lined tower for a smelter off gas acid plant in South America. The impacts of various design considerations on acid tower replacement projects are compared, including in-situ replacement versus a new location; brick-lined versus alloy shell, and selection criteria for mist eliminators.
Prayon’s Hadrien Leruth and Marc Sonveaux highlight the latest phosphate production developments at the company – and share their experience of how innovative ideas are validated, industrialised and turned into commercially-viable technologies.
Newly-developed froth flotation equipment and reagents are improving selectivity and the grade and recovery of phosphate concentrates.
NOx emissions from chemical processes such as steam methane reforming contribute to air pollution. The chemical industry is required to take steps to lower such emissions. Technology, developed for related industries, can be designed and optimised to reduce NOx emissions from steam methane reformers. Emission control experts can use a combination of modelling and experience to guide plant operators in recommending and designing optimum, sometimes tailor-made solutions. In this article different options are discussed including low NOx burners, selective catalytic reduction, selective non-catalytic reduction and high emissivity ceramic coatings.
Dr MP Sukumaran Nair, policy analyst and director of the Centre for Green Technology & Management in Cochin, India, discusses the ways that digitisation is improving fertilizer plant operation.
In a carbon-constrained world, carbon capture and utilisation or storage (CCUS) installed on a methanol plant is a necessary and feasible solution. The new, patented AdWinMethanol CC® technology, jointly developed by thyssenkrupp Industrial Solutions AG and GasConTec GmbH, integrates carbon capture into large-scale, natural gas-fuelled methanol production to yield a drastically reduced carbon footprint. U. Koss and W. Balthasar of GasConTec and J. Wagner of thyssenkrupp Industrial Solutions discuss how it removes CO 2 emissions in an efficient, cost effective, and environmentally friendly manner, taking advantage of the design features of AdWinMethanol ® .
Process and simulation models can be valuable tools when troubleshooting to solve operational issues in sulphur recovery units. Two examples are provided. In the first case study it is shown how a tuned model was useful in troubleshooting an SRU that was experiencing lower than expected recovery efficiency and apparent channelling in the first catalytic converter. In the second case study an SRU simulation tool is used to investigate sulphidic corrosion in a waste heat boiler.