Nitrogen+Syngas 369 Jan-Feb 2021
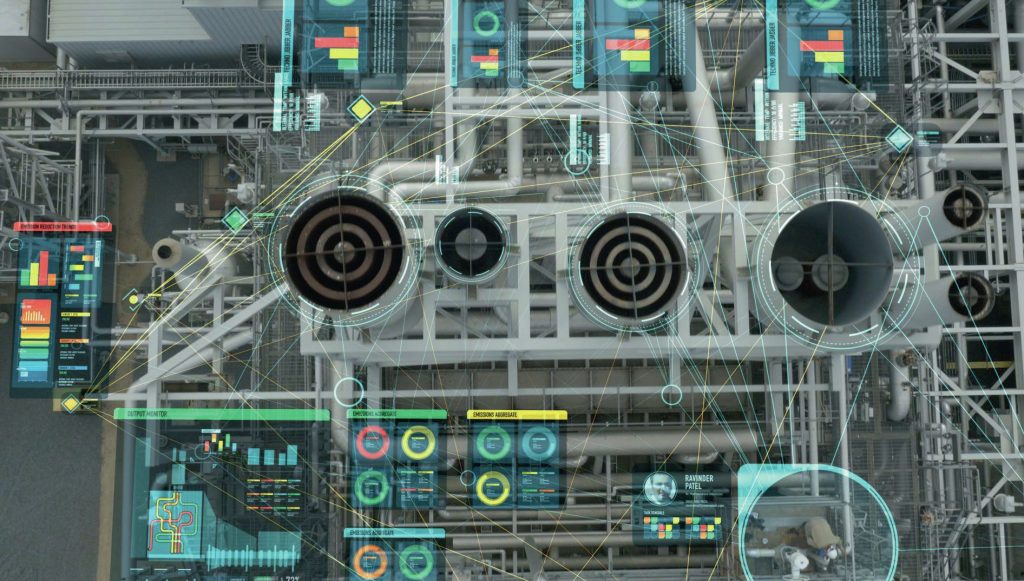
31 January 2021
Digitisation in the fertilizer industry: scope and potential
DIGITISATION
Digitisation in the fertilizer industry: scope and potential
Dr MP Sukumaran Nair, policy analyst and director of the Centre for Green Technology & Management in Cochin, India, discusses the ways that digitisation is improving fertilizer plant operation.
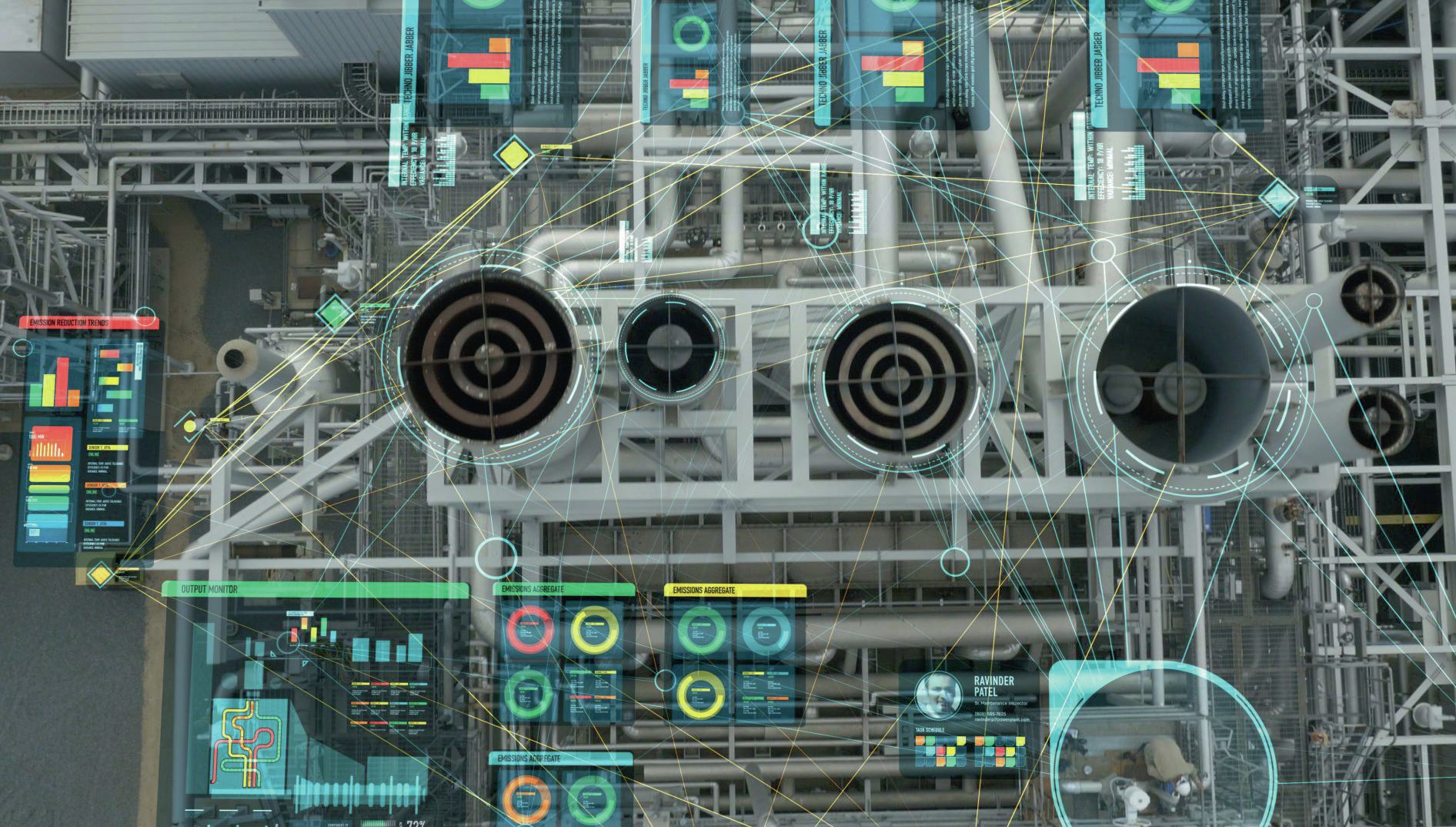
The fertilizer industry is facing several challenges in these Covid-affected times. Several industry majors have seen a weakening in their financial performance due to curtailments in production caused by lockdowns and associated disruptions to logistics and supply chains, and ensuring the health and safety of staff, which are the most daunting among the many challenges being confronted by the industry. On the raw material front, consumer demands are changing, new energy resources are emerging, unconventional oil and gas resources are being developed. The significance of the role played by emerging economies such as China and India are increasing, and a host of other factors had contributed to depressing the market even prior to the onset of the pandemic. The ensuing Covid 19 pandemic has had widespread economic fallout in the industry. Oil demand is falling due to lockdowns and travel bans, and the oil price has plunged well below the level needed to turn a profit. For survival’s sake companies are reducing expenditure, bringing down capital spending and trying to drive down operating costs. One good thing is that emissions have been reduced due to the dip in industrial activity.
Facility management
These days optimisation holds the key to survival. The effective functioning of modern industrial facilities involves a tremendous amount of planning and scheduling with regard to procurement, production, quality control, safety and environmental care, off-sites and utilities, and marketing and logistics, besides ensuring the optimal use of raw materials, energy and manpower. We have been using aspect-specific systems and tools to address optimisation in each of these areas for prudent decision making to improve the bottom-line, but digitisation can help to develop a holistic approach in the decision-making process.
Operational efficiency
Over the years, the industry has witnessed considerable improvement in its operational efficiency. This has been possible because of the timely adoption of innovative and commercially proven retrofit and revamp technologies. Modern managements try to strategically advance reliability, availability, operational efficiency of manufacturing systems and achieve increased production, yields and ensure profitable capacity utilisation. With advanced automation, rigorous and real time plant monitoring resulting in optimisation of all kinds of resources, better management through effective planning and scheduling becomes possible. Going further, highly connected open systems with real time domain and instant data integrated with enterprise resource planning (ERP) systems gives operators command over the increasing complexities in the industry.
Even in the best designed and well operated plants, there exists ample scope for improvement in operating efficiency through the adoption of digitisation and the industrial internet of things (IIoT). However, identifying where to look for further improvement can be a tough task. Technologies continue to develop; operating facilities adopt newer ones as and when they become technically proven and commercially viable and the operating results in the real time plant environment follow them. It is exactly within the gaps between these developments that there lies further scope for optimisation. The operator’s response time to changes in operating parameters is also reduced considerably by digitised plant optimisers. A major technology company has shown through internal studies that 80% of production downtime is preventable, and much of it is due to operator errors. These errors cost that particular industry approximately $20 billion a year. A well-developed preventative maintenance strategy can bring down operating costs, including losses caused by downtime due to unexpected failures, by 25%. An advanced predictive maintenance program with the support of wireless technologies, IIoT and machine learning (ML) and artificial intelligence (AI) enables even greater savings. Under the challenging conditions unfolded by the outbreak of the pandemic, there is likely to be a growth of remote operations supported by modern artificial intelligent platforms.
Current developments in wireless technology, smart sensors, intelligent connectivity, mobile technologies, data storage, analytics and cyber security are increasingly contributing to advances in the operability, productivity, maintenance, safety, and environmental stability in the industry. The internet of things intelligently connects physical devices, driving improved operating efficiencies, business growth and environment friendliness. Industry engages with the IIoT and uses a number of sensors of different designs to capture the operating parameters in real time and use the output for decision making to ensure that the operation of the facility adheres closely to the designer’s intent and enhances stakeholder value. Connected devices sense operating data and communicate the same to the data centre, where it is analysed with the support of big data analytics, artificial intelligence, and cognitive analysis. The output from the analysis is developed into actionable programs to operate the facility in the most optimised manner.
Digitisation and IIoT are engaged to monitor variations in operating parameters, detect leaks in pipelines, oversee the security and integrity of installations and check physical condition and location. Real time monitoring of pumping and compressor stations along cross country pipelines helps to instantly assess inhibitory factors depressing operational efficiencies and expose corrosion and erosion which may lead to failure situations. Such measures, taken in advance, improve productivity and thus reduce costs.
In recent years, the industry has been increasingly encouraged to use wireless sensor networks and supervisory control and data acquisition (SCADA) for monitoring of oil and gas installations. Compared to IIoT, wireless sensor networks (WSN) have limited transmission range, storage capacity and power backup, all of which need more improvements. On the other hand, SCADA systems are costly, difficult to maintain and are not scalable. In its place, digital twins are capable of multiple access of wide-ranging data of several equipment at a time at a lower cost. Thus, IIoT is capable of addressing the bottlenecks and improving productivity by enabling predictive maintenance in place of preventive maintenance, monitoring changes in operating conditions in real time, and reducing downtime due to accidents. The IoT architecture for the above purpose comprises a sensor (smart device), connectivity to the control centre (gateway) and control centre (server), responsible for the application and analysis of data gathered from sensors to generate information and support the decision making process for better asset management.
Digital twins are coming on in a big way in manufacturing industry, offering increased utilisation of capacity, improved product quality and output, forecasting deviations from the designer’s intent with regard to processes and operating parameters, reduced specific consumptions of energy and feedstock, improved bottom lines and better workplace safety, and better achievement of environmental targets. A digital twin is a virtual model of an asset (e.g. compressor) or process (e.g. catalytic cracking), using IoT sensors to monitor and capture data from physical objects, process it in real time in combination with historical data to get a holistic view on the performance of manufacturing equipment and plants. These models are combined with advanced visualisation technologies and data analytics to fast track troubleshooting, forecast imminent failures, and innovate and retrofit new equipment designs in an existing facility. Often, a low turndown ratio arising out of over-design in term s of the size and capacity of equipment is a generic problem associated with design. Data driven models in the virtual environment provide the requisite inputs to improve future designs. Digital twins are used in brownfield projects to guide the revamp and modernisation of existing facilities to capture better operating efficiencies.
Shifting maintenance strategy
The shift from a reactive (‘run to failure’) to a reliability centred maintenance (RCM) model was gradual and successfully avoided costly equipment failures. Today, we have pro-active or predictive maintenance programs that use advanced AI-based analytics to identify the predominant factors and monitor parameters to fix variations leading to failures – abrupt or incipient. Moreover, advanced predictive systems are capable of accurately predicting remaining the life of furnace tubes and the likely failure time of rotating equipment. By this operators are empowered to extend equipment service life, avoid expensive repairs, and minimise unscheduled downtime.
Corrosion management
NACE International puts the annual cost impact of corrosion on the processing industry alone as $50 billion. A 30% savings via the adoption of best practices in corrosion prevention would amount to $15 billion – a very significant sum. Beyond economics, corrosion also adversely affects plant reliability, leads to accidents, damages assets and spoils the environment. Therefore, early detection of corrosion, its progress and the impact of the vulnerabilities of varying process parameters have to be understood through advanced monitoring techniques. In fact, we may have to prioritise inspections and strengthen predictive capabilities with regards to corrosion by improving upon data evaluation and better decision making using accurate and real time data.
Data security
In the digital world, data security is a prime consideration and responsibility. While current operating data is relevant for day to day business, historical data is useful for policy formulation and prediction of price and market trends. Maintaining the confidentiality and integrity of data via controlling its access are important from a security point of view. Digitisation and encryption helps to protect an organisation’s electronic information systems from the attack of hackers and unauthorised access.
Turnaround management
Turnarounds inevitably contribute to significant downtime in operating plants. A lot of planning and scheduling is done before shutting down a productive plant for the purposes of inspection of vessel internals, catalyst change, equipment replacement, cleaning of fouled equipment or hooking up retrofit systems in order to ensure reliability of plant assets and ward off unexpected failures. Most often, turnarounds incur time and cost overruns due to faulty projections based on inadequate and primitive information about the condition of equipment, delivery schedule of critical supplies, and assessment of the amount of work and manpower required. Today, with the use of artificial intelligence and real time modelling of maintenance and turnarounds, debottlenecking and troubleshooting becomes easier and targets can be achieved within the required schedule.
The development of an app-based software approach is yet another means to enhance facility safety. Operating personnel exposure to hazardous areas in the plant can be limited via wirelessly monitoring process plant data through sensors. Online monitoring of the loss of heat transfer efficiency of heat exchangers, energy and steam loss through faulty traps, and predicting the end of run of reactor catalysts are all well established through app-based software. Abnormal situation monitoring is yet another area where smart wireless devices and sensors enable cloud computing of equipment data in various formats. Overheating, over-pressurisation and excessive vibration limits are set to identify normal and abnormal operations. In AI based predictive solutions, deviations from the designer’s intent or a set fault threshold initiates a warning to alert the operating staff.
Thus, the industrial internet of things allows delivery of a large volume of data at greater speeds and at lower costs. A recent Gartner survey suggests that nearly half of all organisations implementing IoT technologies were currently using or were planning to use digital twins. According to a recent research report, the market value of digital twins is estimated to grow from $3.8 billion in 2019 to $35.8 billion by 2025. Industry majors have been harnessing the power of digital transformation for over two decades to optimise operations and drive enterprise-wide performance. Indeed, a wedding of operational technology (OT) and information and communication technology (ICT) can result in a potential saving on the order of 25% on avoidable costs. Sharing this 15% and 10% respectively between the facility owner and the service provider seems like a fair apportionment.