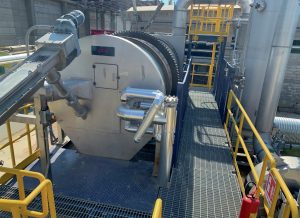
New showcase drum granulator commissioned
Sulphur processing and handling equipment manufacturer IPCO has completed the commissioning of a groundbreaking new drum granulator in Italy that will serve as a global showcase for this patented system. C. Metheral of IPCO, describes the innovative approach and key features of the SG20 sulphur granulation system.