Sulphur 419 Jul-Aug 2025

17 July 2025
Meeting growing demand for solidified sulphur
SULPHUR FORMING
Meeting growing demand for solidified sulphur
Varun Mathur is Market Manager for the Middle East region at industrial processing company IPCO, one of the world’s largest suppliers of sulphur solidification systems. In this article, he highlights the reasons for converting sulphur into a solid form, and compares two of the technologies most commonly used to achieve this.
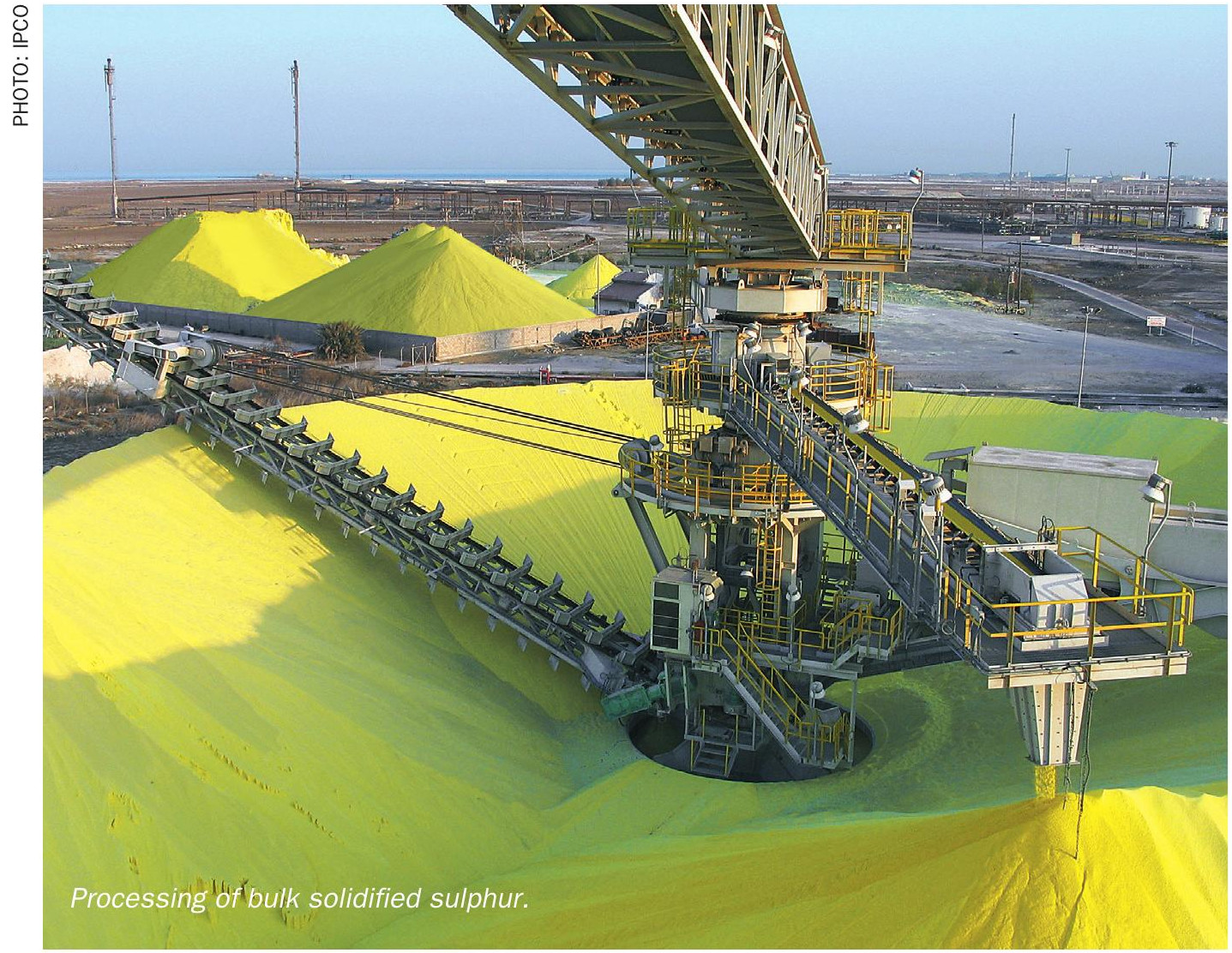
Sulphur is key to the success of products and processes used by a whole range of different industries, from agriculture, rubber and chemicals to food, pharmaceuticals, and personal care products.
In the agricultural sector, where it is often referred to as the fourth major nutrient (after nitrogen, phosphorus, and potassium), its use first boomed when sulphur was removed from fossil fuels and no longer fell onto fields from the atmosphere. Today, the need for sulphur-enriched fertilizers continues to grow.
It is also an element that is produced in ever greater quantities due to stringent environmental regulations requiring reduced levels of sulphur in fuels (hence greater volumes being extracted) and growth in overall output.
Most of the elemental sulphur arriving on the market is recovered through desulphurisation of natural gas and oil using the Claus process. The result is molten sulphur, delivered at a temperature of 145–150°C and a form that presents a range of challenges in terms of storage, handling and transportation:
Temperature control: Molten sulphur remains in a liquid state within a narrow range (125–145°C) and any deviation will result in either solidification or increased viscosity. Maintaining this range requires heating systems and insulation, both of which contribute to capital and energy expenditures.
Fire and explosion hazards: The flash point of molten sulphur ranges from 168– 188°C, while auto-ignition can occur at temperatures between 248–261°C. The flammability of sulphur, especially when combined with its potential to emit hydrogen sulphide (H2S), creates serious fire and explosion risks.
Vapour control: H2S is particularly dangerous due to its broad explosive limits (4.3– 46%) and toxicity. Vapour control systems are essential, especially in storage tanks, to avoid dangerous accumulations.
Corrosion: Molten sulphur is inherently corrosive, necessitating specialised storage tanks made from stainless steel or high-performance alloys.
Electrostatic discharge: Molten sulphur can accumulate electrostatic charge during transfer, requiring rigorous grounding and bonding measures to prevent discharge-related accidents.
Dangers of SO2 : Sulphur fires release sulphur dioxide (SO2), a highly toxic – sometimes lethal – respiratory irritant.
Environmental and regulatory pressures: Handling molten sulphur will require compliance with multiple safety and environmental regulations, including but not limited to:
• IMDG (International Maritime Dangerous Goods)
• IATA (International Air Transport Association) Regulations
• OSHA (Occupational Safety and Health Administration) Standards
• EPA (Environmental Protection Agency) Guidelines
For these reasons and more, handling molten sulphur is generally only commercially viable when it is processed close to the refinery where it was extracted. But sulphur is now a global commodity, often shipped from continent to continent for processing, so usually needs to be converted into a form that is safe and practical to store, transport, and reprocess.
Solidifying sulphur reduces the risks of fire, H2S vapour, and SO2 emissions, eliminates the need for costly heated equipment, and enables it to be stored, traded and transported around the world by road, rail and ship. A premium quality solidified product also enables easy, accurate metering and dosing too, essential for downstream reprocessing.
Solidification isn’t without its own costs and challenges of course. There’s the initial capital investment of the solidification equipment, and the energy consumption of the process. The solidified product can release sulphur dust if incorrectly handled, and this must be mitigated.
And if the end application requires molten sulphur, then the cost of remelting must also be factored in. But overall there’s no real argument: if sulphur is to be stored for any length of time, or transported over any significant distance, it needs to be solidified.
Premium quality forming
It was in order to establish standards for solidified sulphur – and its suitability for transportation (i.e. export) – that, in the late 1970s, SUDIC (Sulphur Development Institute of Canada) set about defining what has now become globally recognised as a ‘premium’ quality product.
In determining this quality, SUDIC looked at friability and fines content, both critical to efficient, clean and environmentally safe production and handing. The other major factor was moisture content; excess moisture not only adds weight, leading to unnecessary transportation and remelting costs, but also results in increased acidity, causing corrosion in conveyors, silos, trucks, rails cars and ship holds. A ‘wetter’ product is also more susceptible to freezing into lumps during cold weather, a significant factor in North America and Russia.
Together, these factors determine not only the quality of the formed sulphur but also the ease with which it can be handled and the potential impact on the environment during storage and transportation (formed sulphur can be handled as many as 15 times between solidification and subsequent reprocessing).
Sulphur solidification processes
There are three main methods of solidifying sulphur: wet prilling, indirect belt cooled pastillation, and drum granulation.
In the wet process, droplets of sulphur are sprayed down through a forming tank where they come into direct contact with a counter-current of cooling water. While dewatering screens are used to reduce the moisture content in the solid product, the resulting levels – typically up to 3% – are well in excess of the 0.5% moisture content defined under SUDIC ‘premium’ quality standards.
Both forms of dry processing deliver a product with a moisture content within the SUDIC standards.
Dry forming – or pastillation – offers a number of other advantages over prilling, notably predictable and constant bulk density and consistency of formed size: prill sizes will typically range from between 1-6 mm, sometimes bigger, whereas pastilles and granule sizes can be controlled by process parameters.
Dry formed sulphur also benefits from low friability and low fines content, leading to low dust emissions in the working environment, less risk to operator health and minimised risk of explosions.
Pastillation and granulation both deliver a SUDIC-quality product and each process has distinct advantages tailored to specific industrial needs. To compare them the following sections will look at two of IPCO’s systems, the Rotoform pastillation process and the SG drum granulator.
Rotoform pastillation
This is the only indirect solidification system on the market and the world’s most widely used sulphur pastillation process with more than 700 installations to date.
The Rotoform consists of a heated, cylindrical stator and a perforated rotating shell that turns concentrically around the stator, depositing sulphur drops across the whole operating width of a continuously running steel belt (Fig. 1). The circumferential speed of the Rotoform is synchronised with the speed of the belt, ensuring that drops are deposited accurately, consistently and without deformation.
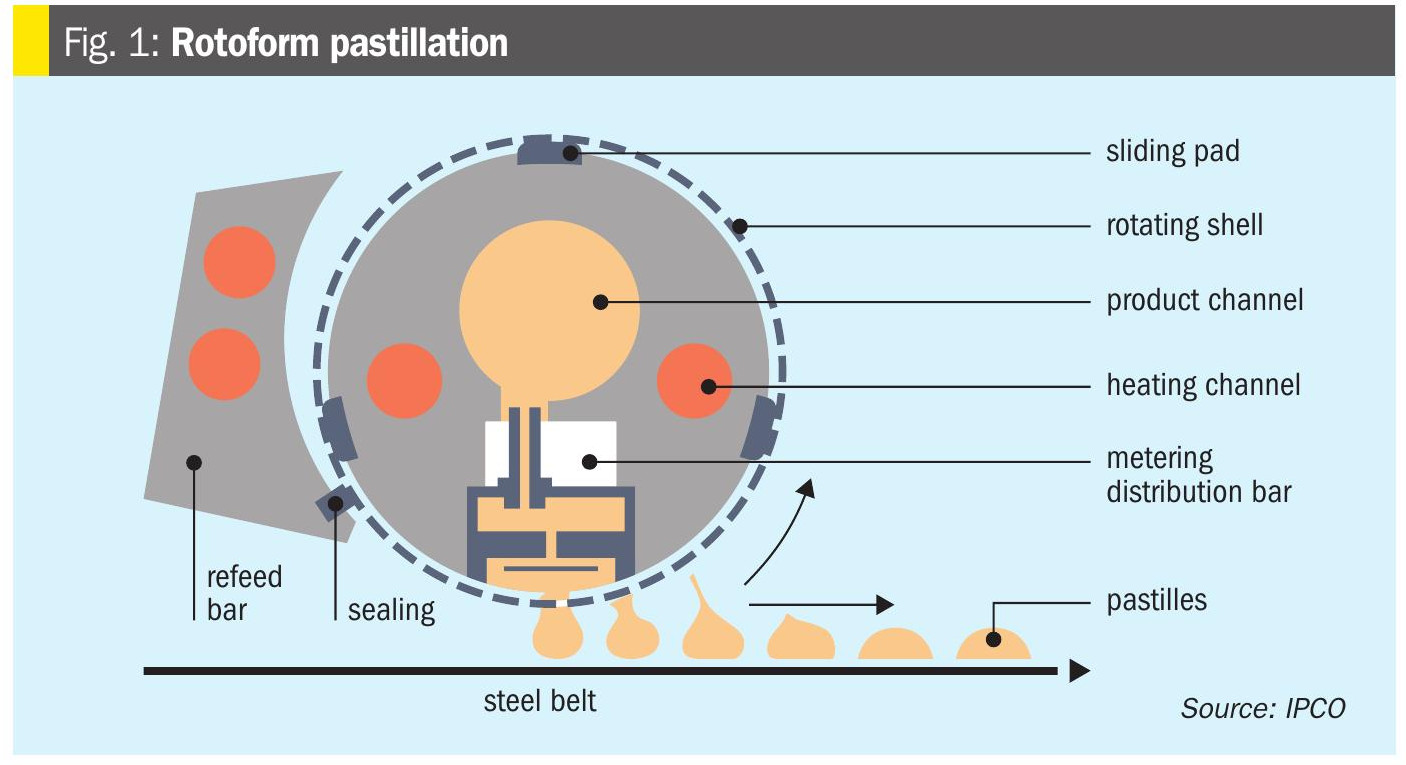
This single step, liquid-to-solid process results in a high-purity, low-dust, and dimensionally consistent product, one classified as ‘premium’ as defined by SUDIC. Uniformity of shape and size makes them free-flowing for easy handling and precise dosing, while a predictable high bulk density is a major advantage in terms of storage and transportation.
In terms of capacity, IPCO’s Rotoform S8 system enables throughputs of up to 5.5 t/h, and the Rotoform HS is a high speed model with a capacity of up to 11.5 t/h. Where greater capacity is required, multiple lines can be operated in parallel.
SG drum granulation
In contrast, drum granulation is a much higher capacity process, producing larger, coarse, round granules by rotating molten sulphur within a tumbling drum (Fig. 2). Particles grow in size as sulphur builds upon seed particles, creating bulkier outputs suitable for large-scale applications.
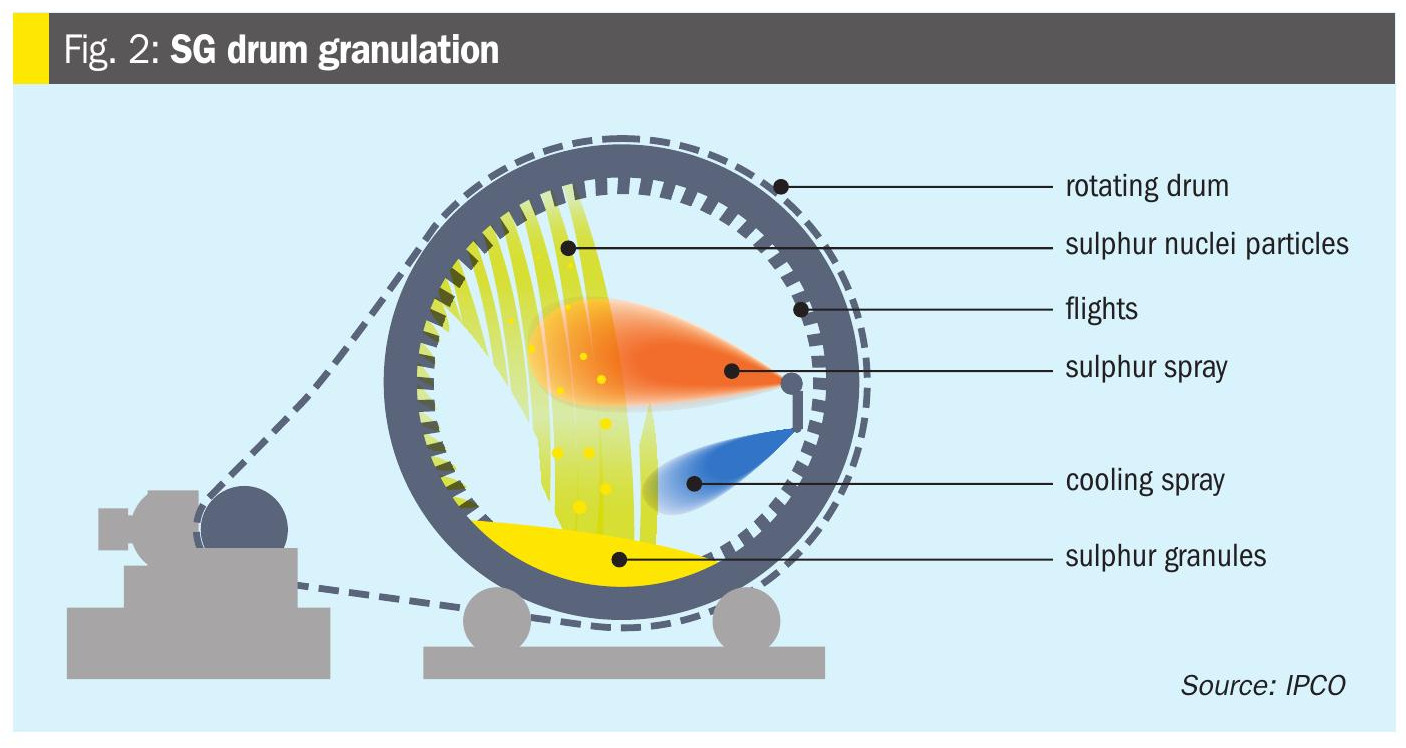
Solid sulphur seeds are generated externally from the drum by freezing sprays of liquid sulphur in a water bath at controlled pressures to form the desired size range. These particles are then conveyed into a rotating drum with appropriately placed flights attached to its inner surface. These flights create curtains of falling sulphur particles inside the drum while moving them towards the discharge end.
The sulphur particles are progressively enlarged to the required size by coating the curtains of particles with liquid sulphur using spray nozzles on a header running the length of the drum.
The temperature inside the drum is moderated by the evaporation of water from spray nozzles located inside the drum. The result is a high-quality, low dust granulated product that meets SUDIC standard product specifications.
Two models are available: the SG20 sulphur granulator, with a solidification capacity of up to 800 t/d, and the SG30, a unit capable of granulating 2,000 t/d, the highest capacity solution available to the sulphur processing industry.
Choosing the most appropriate technology
So which one to choose? Both technologies have their advantages and disadvantages as shown in Table 1:
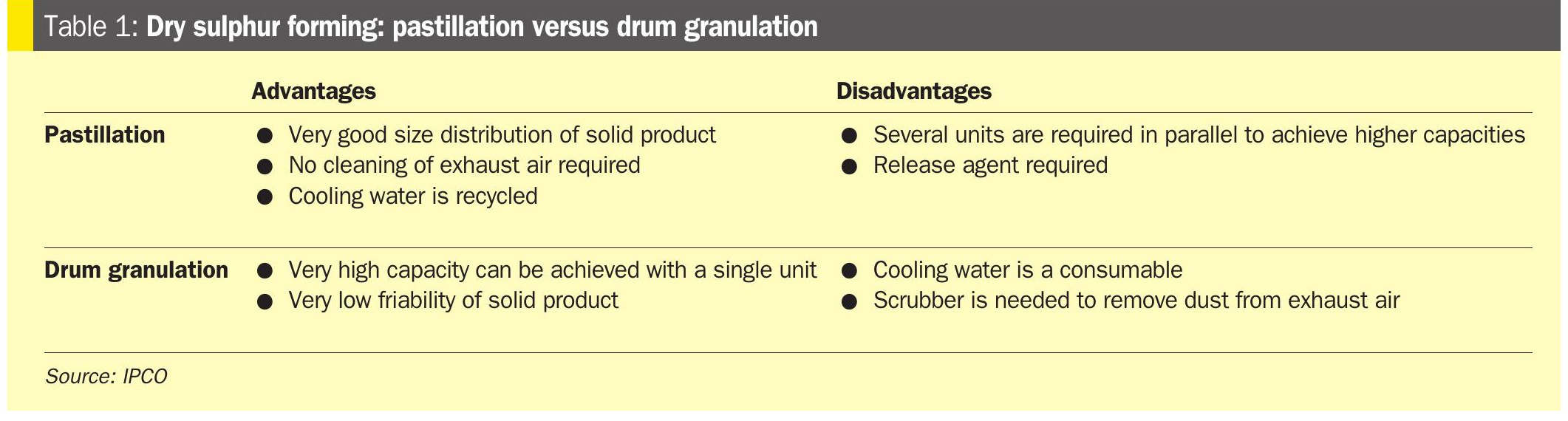
Capacity considerations aside, the answer will very often depend on how and where the solidified product will be used. Pastilles are small, smooth, uniform, and hemispherical in shape, whereas granules are spherical, large, and coarse. These qualities make the former better suited to precision dosing, while the later are ideal for large-scale applications,
In agriculture for instance, one of the largest markets for formed sulphur, the accurate distribution and fast nutrient release of sulphur bentonite pastilles make them best suited to smaller-scale farming, whereas granules are ideal for gradual nutrient release in broad-acre agriculture.
Other typical applications for premium quality pastilles include the rubber industry, ensuring consistency in vulcanisation processes, and chemical manufacturing, where the purity of the end product supports stable and consistent production of sulphuric acid. Pastilles are also ideal for use as preservatives and antioxidants in the food industry, where they are preferred for their low dust and high uniformity, and for pharmaceutical products requiring safe, reliable, and high purity sulphur inputs.
Granules are also widely used for the production of sulphuric acid, typically in bulk, mass-scale operations where cost is a key consideration. Other applications include metallurgy, where sulphur is used in bulk for large-scale ore processing and metal extraction, and in construction, incorporated in sulphur concrete for acid and salt resistance. Sulphur granules are also used on a wide scale in soil pH correction for environmental reasons.
Conclusion
The transformation of sulphur from a difficult-to-manage molten substance into a safe, reliable solid form is a necessity in today’s industrial ecosystem. As global demand for sulphur grows – driven by the needs of agriculture, energy, chemicals, and healthcare – solidification offers a robust solution to these challenges, whether through high-precision pastilles or bulk-ready granules.