Fertilizer International 526 May-Jun 2025
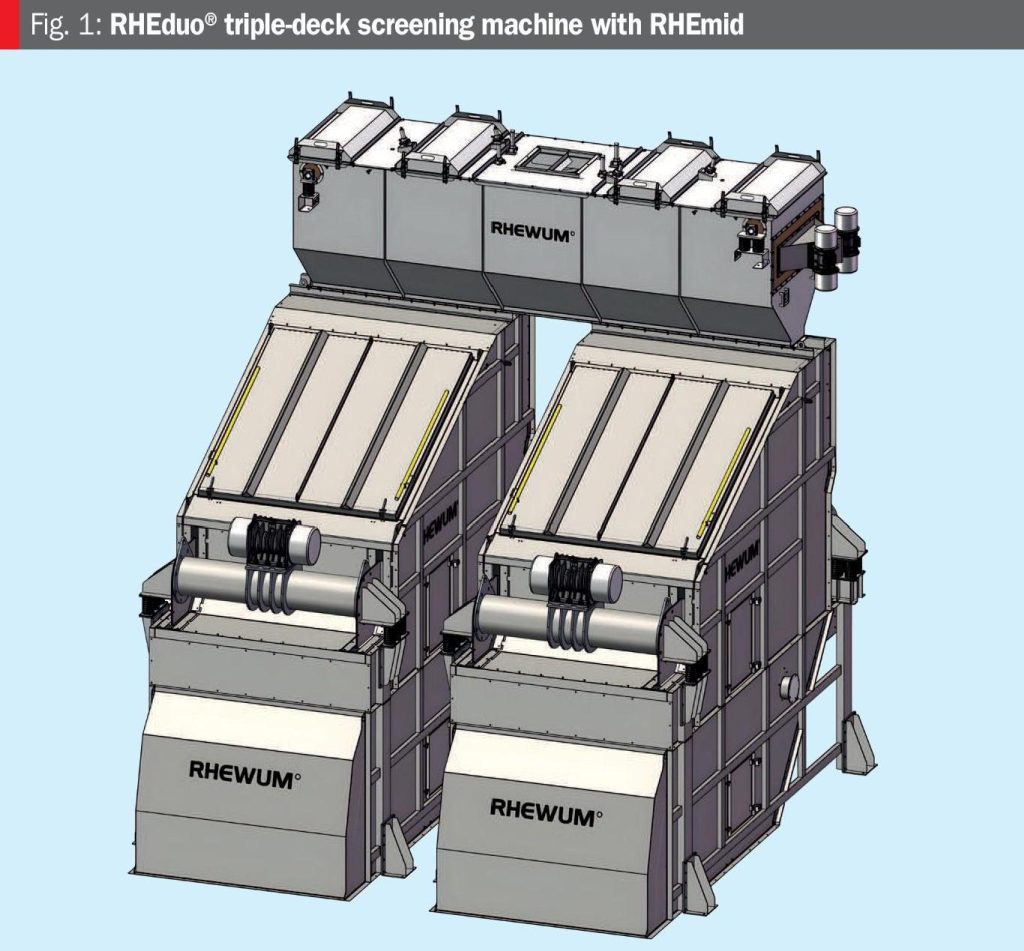
2 May 2025
Tackling bottlenecks in potash production
CRUSHING AND SCREENING
Tackling bottlenecks in potash production
In a volatile potash market shaped by geopolitical risks and supply chain disruptions, operational agility and throughput flexibility are strategic necessities that offer competitive advantages. Unlocking capacity through intelligent de-bottlenecking is a scalable, cost-efficient path forward for potash producers. Tountzer Ramadan and Alexander Krasovsky of RHEWUM provide a compelling case study to illustrate this.
Introduction
The global potash market is currently experiencing a period of significant growth, an expansion which is projected to increase by over 50% in the next decade to reach a total market value of more than $30 billion.
This impressive growth is primarily driven by the crucial role of potash – an essential crop nutrient – in global food security. Looking ahead, the demand for potash is anticipated to rise further due to the intensification of agriculture and the expansion of cash crop cultivation, particularly in countries like China.
However, the global potash market is being reshaped currently, with production from major supply centres, like Canada, Russia, and Belarus, being buffeted by geopolitical events and volatile trade relationships. The ongoing tariff discussions between the US and Canada highlight the complex, unfolding situation facing operators and the potential impacts of trading uncertainties on potash supply chains.
This fast-moving picture also underscores the importance of production efficiency and the ability to adapt to dynamic market conditions. Indeed, in the current operating environment, optimising production becomes paramount, given that bottlenecks in the production process can significantly limit output and hinder the ability to respond to changing market demands.
This article will focus on the vital role of screening technology in potash production. Strategic upgrades to screening equipment to alleviate bottlenecks, improve product quality, and maximise output are highlighted. Potash producers, by addressing these critical ‘pinch points’ in the production process, can unlock their full potential and position themselves for success in the expanding global market.
Potash and screening machines
At the beginning of the production process, screening machines are used for size control of mined potash ore after the primary and/or secondary crushing stages. Depending on plant layout, they can also be used downstream for:
• The removal of large pieces of material after compaction/granulation
• Wet classification
• Dewatering
• Screening of the finished product
• Protective screening before product dispatch.
Encouragingly, the de-bottlenecking of screening-related processes offers a rapid, near-term opportunity to increase potash production by 10–20%. Optimising the potash granulation circuit, immediately prior to the final product stage, is one example of a quick win. This mainly involves upgrades to the compactor/granulator and the screener.
Modern potash industry compactors/ granulators are handling ever larger volumes. The product is compacted, crushed, screened for usable on-size particles, and then fed to the next step. Oversized particles, meanwhile, are re-crushed, dust is returned to the circuit, and the process is repeated. This whole cycle is energy-intensive, as powder is pressed into flakes, crushed again, and reprocessed.
Applying modern and improved screening technology at this stage, additional to efficient potash compaction/granulation, can reduce the recirculation of material and boost output and profit. This type of process optimisation can also be implemented at a potash plant within just six months.
Quick profits in a brownfield environment
Currently, RHEWUM is receiving numerous enquiries from potash producers around the world looking to increase their production capacities. What is driving these requests?
The main reason is that screening machines are the frequent cause of bottlenecks in potash production. Many of the existing machines installed in compaction/ granulation, for example, do not reach manufacturers’ specifications and their anticipated output.
Consequently, choosing a screening machine especially designed for this task can deliver a significant capacity increase at potash plants of 20-30% per line, or 100-150 tonnes per hour, and achieve a much higher throughput capacity at the required product purity.
Two strategies are suggested to address production limitations caused by ineffective screening at potash plants:
- Replacement of undersized screening machines with larger ones of adequate size.
- Providing additional surface area for screening by installing screening machines upstream or downstream to relieve overloaded existing machines.
To illustrate the practical implementation of these strategies, and their measurable benefits, the following case study presents a real-world example of a de-bottlenecking project in a potash production plant producing MOP (muriate of potash) granules.
De-bottlenecking case study – background
A comprehensive feasibility study was conducted to evaluate the technical potential and operational viability of a capacity expansion and de-bottlenecking initiative for a potassium chloride (KCl) production plant generating MOP granules. The aim was to increase the throughput of the compaction and screening line from a total feed capacity of 400 t/h to 696 t/h (design capacity 900 t/h).
The existing installation is characterised by a rigid structural layout that precluded any modifications to the building infrastructure. Moreover, pervasive dust accumulation at the facility exacerbates wear and complicates equipment maintenance. Product specifications require precise particle size separation at 10 mm, 4 mm, and 2 mm, where the 4–2 mm fraction constitutes the final product. Oversized fractions (>10 mm and 4–10 mm) are recirculated via milling stages.
The de-bottlenecking project focused on overcoming process limitations and eliminating inefficiencies — particularly those arising in the screening section, as this was identified as the primary bottleneck. The two major project tasks are described below.
Task 1: primary product screening – size separation
The current setup involves four third-party product screens operating at 100 t/h each, these being tasked with the classification and recovery of the 4–2 mm product fraction. However, the existing screening technology suffers from severe operational drawbacks.
Maintenance procedures, for example, are labour-intensive, involving manual screen cleaning that takes up to 8 hours per month. The mechanical knockers, necessary for screen deblinding, also degrade due to high temperatures and require replacement every three months due to the wear. Additionally, the feed conveyor belt to these units requires frequent replacement (every three weeks) due to wear. Uneven distribution of feed across the screens further hampers screening efficiency.
To address these shortcomings, RHEWUM proposed replacing the four existing screens with two RHEduo® triple-deck screening machines (Figure 1), each capable of handling a feed capacity of 348 t/h (design capacity 450 t/h). Material distribution would be managed via RHEmid feeders to ensure uniform material loading on the screens.
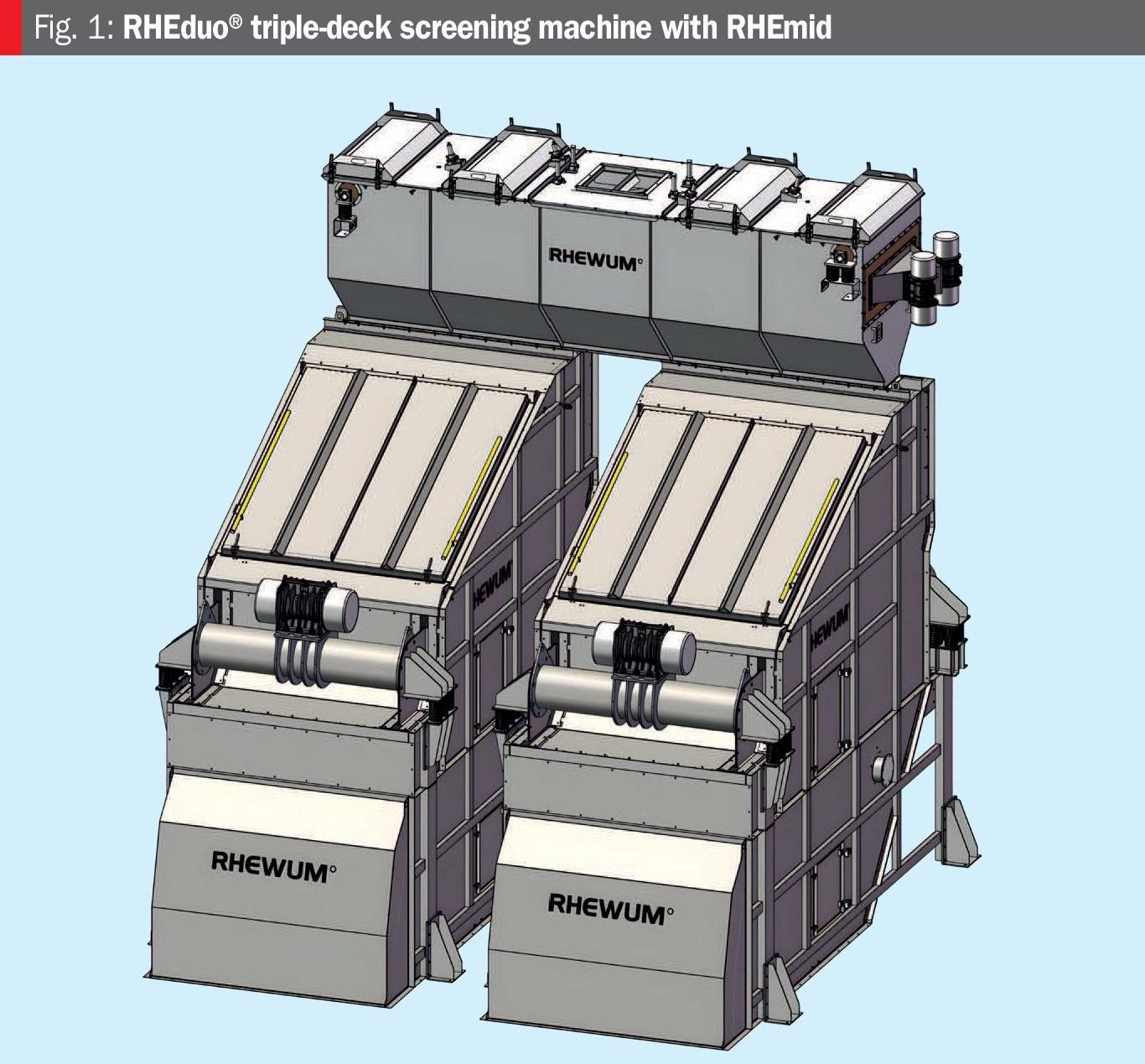
The targeted throughput of both machines is 696 t/h (design capacity 900 t/h), providing a final product output of approximately 138–155 t/h in the 4–2 mm range. The RHEduo® screening machines are equipped with integrated chain-based screen cleaning systems, eliminating the need for high-maintenance bouncing balls and drastically reducing manual cleaning efforts.
Screening trials confirmed the system’s capabilities, demonstrating a product purity of 77.6% and a yield of 90.6% for the critical 4–2 mm fraction. The detailed trial results are shown in Tables 1 and 2.
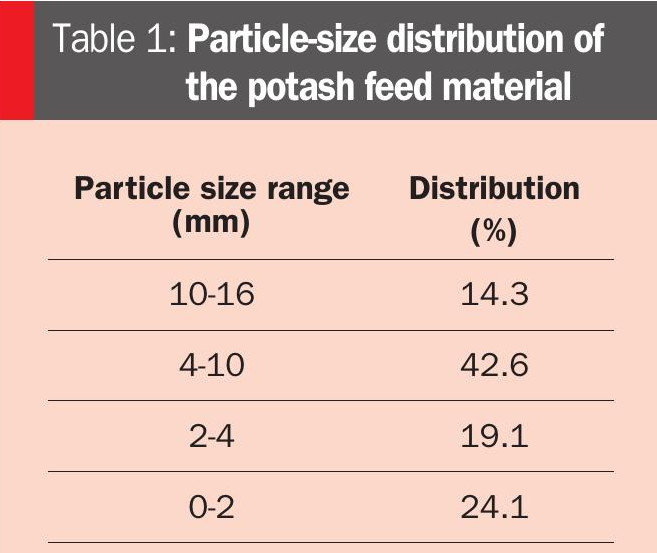
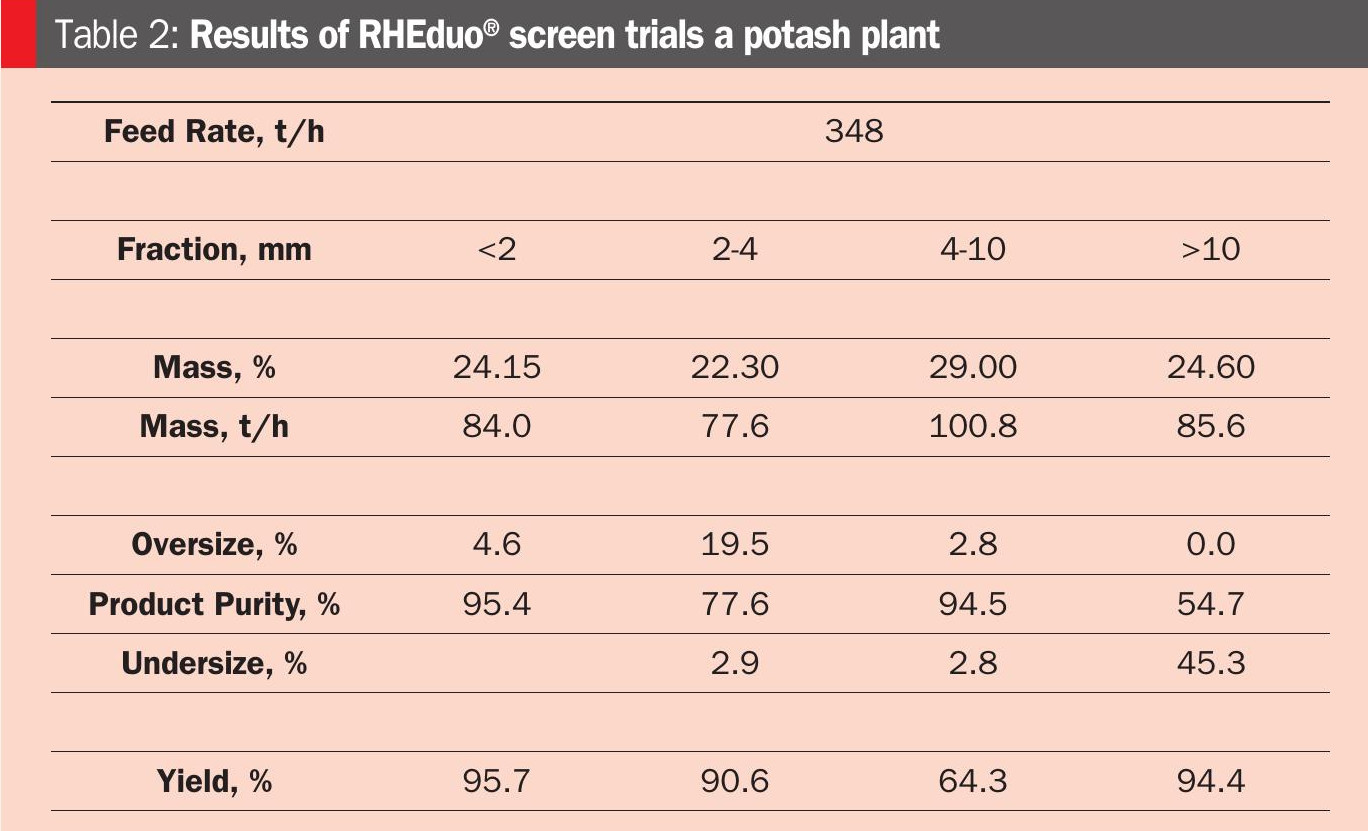
The RHEduo® screening system stands out due to its ability to reliably process a very high throughput on a single machine, thanks to its high-capacity inlet and outlet design. The machine’s steep inclination, by preventing screen flooding, reduces the likelihood of unplanned production downtimes. Furthermore, its static housing permits the use of fixed flange connections, a design feature which eliminates the frequent replacement of compensators.
With drives mounted externally, the system can also withstand product temperatures up to 450°C. Importantly, its low-vibration footprint obviates the need for an anti-vibration frame. The incorporation of an innovative chain cleaning mechanism also ensures consistent deblinding performance, this makes periodic replacement of the bouncing balls typically used in cleaning unnecessary.
Task 2: control screening – dust separation
The final screening step involves a single third-party unit designed to remove dust (<2 mm) from the 4–2 mm product stream. This unit was identified as underperforming and was therefore also slated for replacement. RHEWUM proposed installing a RHEflex® linear vibrating screen (Figure 2). This was optimised for the separation of fine particles from granulated product, with a capacity rating of 146 t/h.
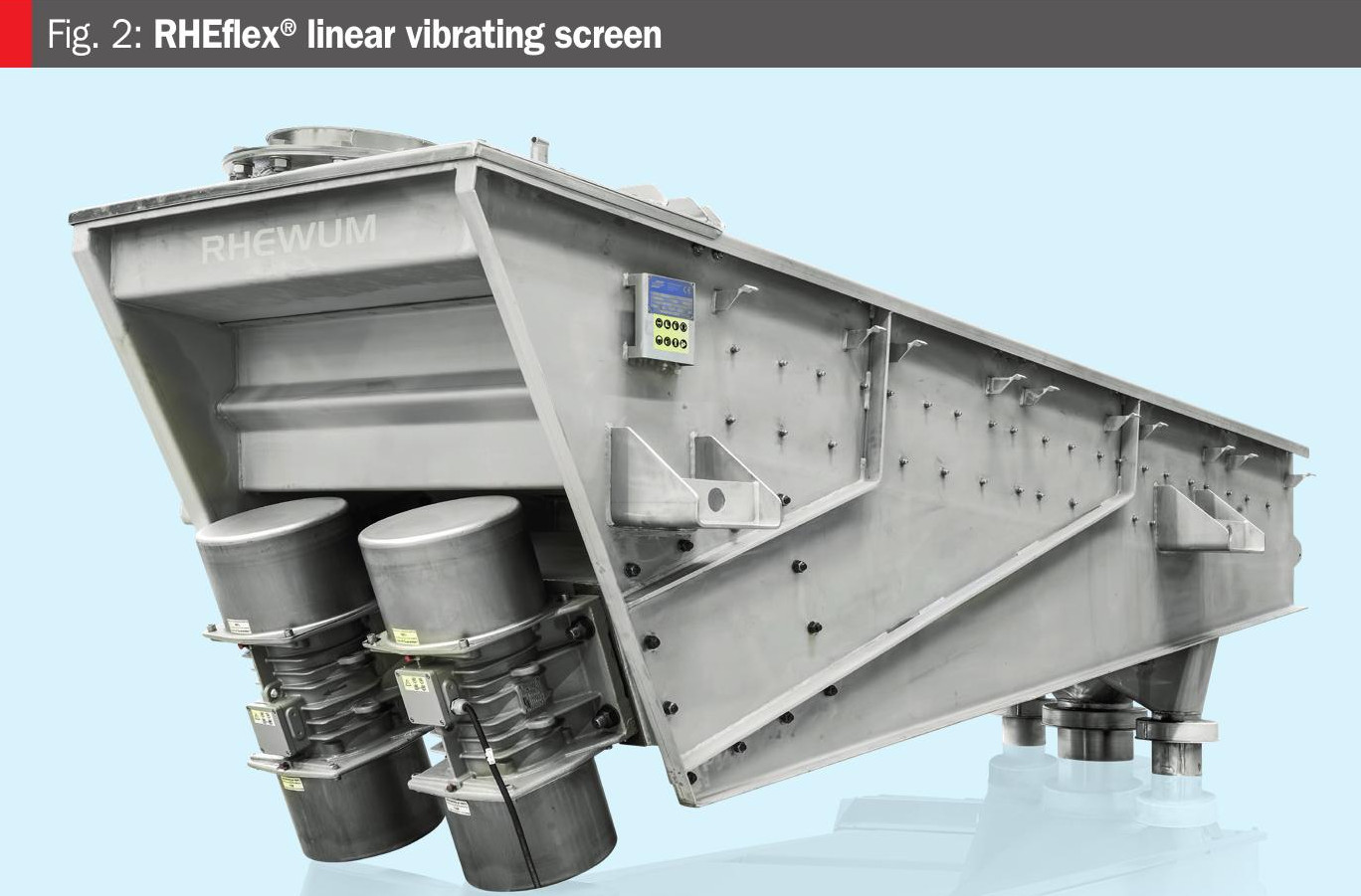
The following test results from trial operation of the RHEflex® unit demonstrated its precision and efficiency in potash screening:
• <2 mm fraction: product purity of 98.6%, yield of 35.31%
• 2–4 mm fraction: product purity of 78.9%, yield of 99.97%
The RHEflex® screening machine features a high-frequency, linear vibration driven by unbalanced motors. This enables accurate particle separation even at tight cut sizes. The machine’s compact, modular design allows its integration within tight plant layouts, while its minimal dynamic load enables installation without structural reinforcement.
In this case study, installation of the RHEflex® significantly enhanced final potash product quality, while addressing the critical dust contamination issue, thereby contributing to both operational reliability and environmental compliance.
Conclusions
This case study illustrates the significant impact targeted upgrades to screening technology can have on potash production efficiency. By replacing outdated, maintenance-intensive equipment with high-capacity, precision-engineered solutions, such as the RHEduo® and RHEflex®, bottlenecks in the compaction and screening stages were effectively eliminated. The result was a measurable increase in throughput of up to 696 t/h (design capacity up to 900 t/h), with consistently high product quality across all critical particle-size fractions.
Equally important is the improvement in operational reliability. The robust design of RHEWUM screening systems – featuring externally mounted drives, static machine housings, and maintenance-free screen cleaning mechanisms – translates into fewer production downtimes, reduced maintenance intervals, and significantly lower lifecycle costs.
From an investment standpoint, the technical and economic benefits are also compelling. Given the current high market value of potassium chloride and prevailing demand from global agriculture, the return on investment (ROI) for the modernisation measures highlighted in this article can typically be realised in less than one year – per potash production line or plant – provided that the improved capacity is fully leveraged.
In a volatile potash market shaped by geopolitical risks and supply chain disruptions, operational agility and throughput flexibility are not just competitive advantages – they are strategic necessities. Ultimately, unlocking capacity through intelligent de-bottlenecking is a scalable, cost-efficient path forward for potash producers seeking to capitalise on favourable market dynamics and secure long-term profitability.
About the authors
Tountzer Ramadan is Sales Director and Alexander Krasovsky is Sales Engineer, Potash, Salt & Building Materials, for RHEWUM in Germany.