Fertilizer International 526 May-Jun 2025
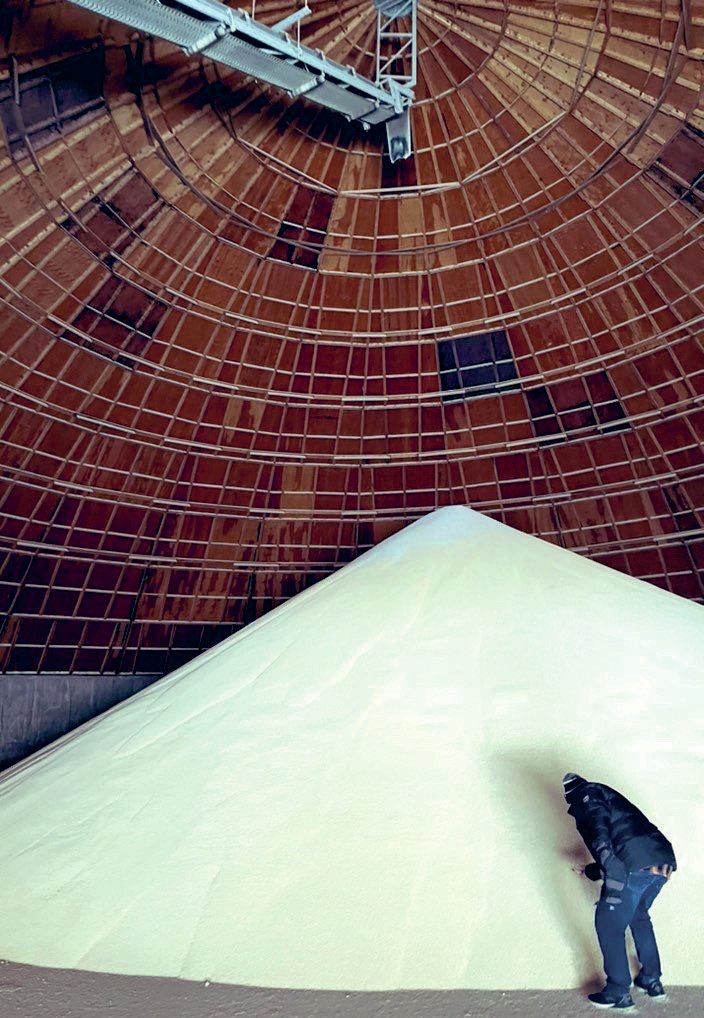
2 May 2025
Sulphur fertilizers – the processes, the products
Sulphur fertilizers – the processes, the products
While sulphur is regarded by many as the fourth crop nutrient, soils globally are becoming increasingly sulphur deficient. Fortunately, there are proven and successful process technologies available for incorporating sulphur – in elemental or sulphate form – into urea, the world’s most widely applied commodity fertilizer. Mark Brouwer of UreaKnowHow.com reviews the main production options and highlights key reference installations.
Sulphur is present in all crops and plays an important metabolic role. It is essential for the formation of proteins, amino acids, vitamins and enzymes, being vital for photosynthesis, energy metabolism and carbohydrate production. Sulphur also contributes to the flavour and aroma of crops such as onions and can therefore influence the quality of farm produce (Fertilizer International 497, p24).
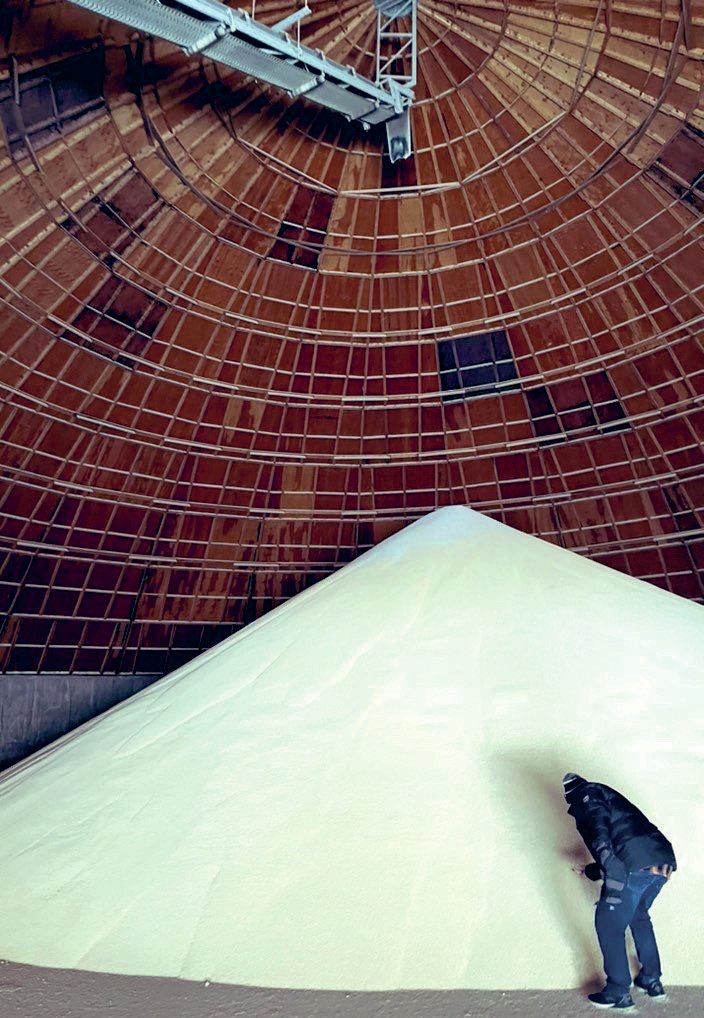
- Light and sandy soils with low organic matter
- Sulphur leaching during high winter rainfall
- Low sulphate mobility during dry spring conditions
- Slower mineralisation at low temperatures
- Low input of organic matter and mineral sulphur
- Low atmospheric deposition of sulphur to soils.
Crops can typically remove between 15 to 30 kilograms of sulphur per hectare from soil. Root vegetables, onions and brassica, especially oilseed rape (canola), have a particularly high demand for sulphur. Pasture and other widely grown crops such as coffee, corn, cotton, rice, soybean, sugarcane and wheat also require moderately high sulphur applications. For these crop types, sulphur requirements can match or even exceed demand for phosphorus (Fertilizer International 497, p24).
Increasingly widespread sulphur deficiency is having an impact on crop yields and quality in many regions. The reasons behind growing global soil deficiency include:
- Declining industrial and vehicle SO2 emissions and, consequently, less deposition of atmospheric sulphur to soil
- Greater sulphur removal due to expansions in the land area devoted to crops and higher crop yields
- The increasing prevalence of high-analysis fertilizers with little or no sulphur content.
Sulphur demand
Globally, it is possible to estimate crop nutrient demand for sulphur by multiplying different crop growing areas by their specific sulphur requirements. Regional sulphur deficits can then be calculated by comparing this demand with actual sulphur fertilizer applications.
Only around half of the global sulphur requirement from crops is being met by fertilizer applications currently, based on CRU estimates. (Fertilizer International 520, p20). All global regions are calculated to be operating with a sulphur nutrient deficit, this being most pronounced in India, Africa and the CIS region. Despite high levels of sulphur nutrient application in East Asia and South Asia, sulphur nutrient deficits in these two regions are calculated at 46 percent and 62 percent, respectively (Figure 1).
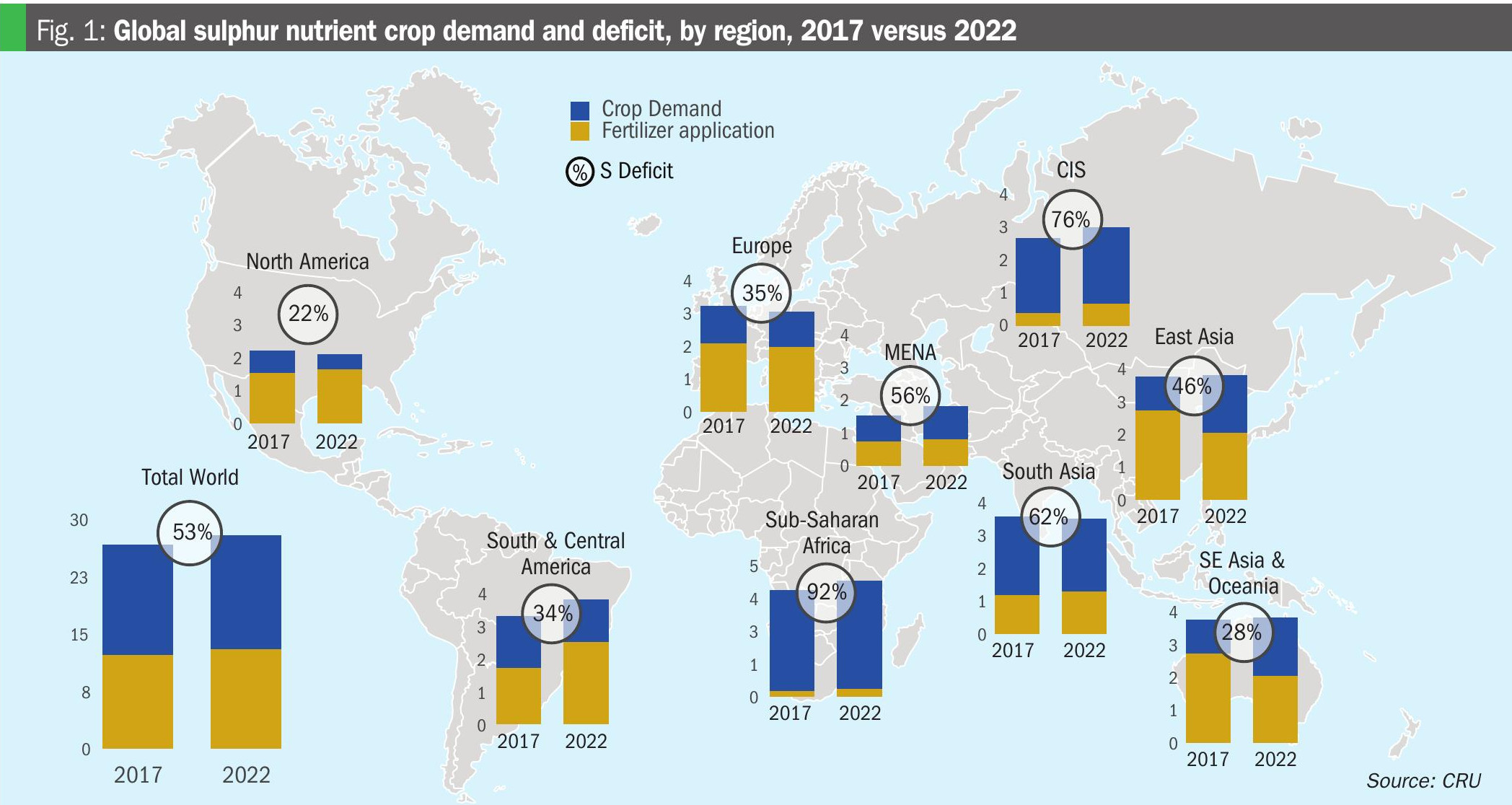
Sulphur and nitrogen – inseparable nutrients
Importantly, sulphur does not act alone as a plant nutrient, as it works in tandem with nitrogen to enable the formation of amino acids during protein synthesis. Sulphur is also part of the plant enzyme required for nitrogen uptake. Sulphur and nitrogen are inseparable nutrients because of this, according to major fertilizer producer Yara International:
“Many agronomists now consider sulphur to be the second most important nutrient after nitrogen. Certainly, sulphur is an essential nutrient, closely linked with nitrogen in biological processes with both elements forming an inseparable team.
“Previously, crop requirements were generally met from atmospheric deposition, so sulphur was confined to a secondary role. However, today it is back in its rightful place as an essential component of optimum nitrogen management.”
The link between nitrogen and sulphur metabolism in plants has been known for many years. As a general rule, every kilogram of S enables 5-10 kilograms of N to be used fully in crop growth and ultimately maximise crop yields.
As the world’s most popular commodity fertilizer, enriching urea (U) with sulphur, by adding elemental sulphur (ES) or ammonium sulphate (AS) – to create U+ES and UAS products, respectively – can be an effective approach that addresses both soil sulphur deficiencies and improves nitrogen use efficiency (NUE)
Sulphate is readily available for uptake by plants but can be prone to leaching, especially under high rainfall conditions. While elemental sulphur remains in soils longer than sulphate, its plant availability depends upon its oxidation to sulphate – with this being controlled by soil conditions and other factors. Generally, elemental sulphur particles below 20 microns in size are better dispersed in soils and more prone to microbial oxidation.
Enriching urea with sulphur or sulphate
This article reviews and summarises the different commercial finishing technologies used to create U+ES and UAS fertilizers. Recent industrial references are also included as examples.
In practice, there are four main finishing options:
- Prilling
- Fluid bed granulation
- Drum granulation
- IPCO Rotoform pastillation.
Each of these finishing technologies, while having their own distinct pros and cons, have been successfully used by fertilizer producers to manufacture urea products enriched with sulphur in elemental or sulphate form.
Prilling
Around 75% of urea plants globally use prilling as their finishing technology. Urea melt (99.6 wt%) is fed to a rotating prilling bucket (or shower heads with numerous small holes) located at the top of a prilling tower (see photo). This creates droplets of urea melt that solidify as they fall from the top of the tower – essentially an empty vertical cylinder of great height – and are cooled by a large volume of air flowing upwards in counter current.
Prilling tower capacities can range between 100 t/d and 4,000 t/d. The urea prills obtained typically have a diameter of 1.7-2.1 mm with a crushing strength of around 1 kg/cm2 . These prills, due to their relatively low strength, are generally not suitable for bulk blending processes or long-distance transport – and are usually bagged for local consumption instead.
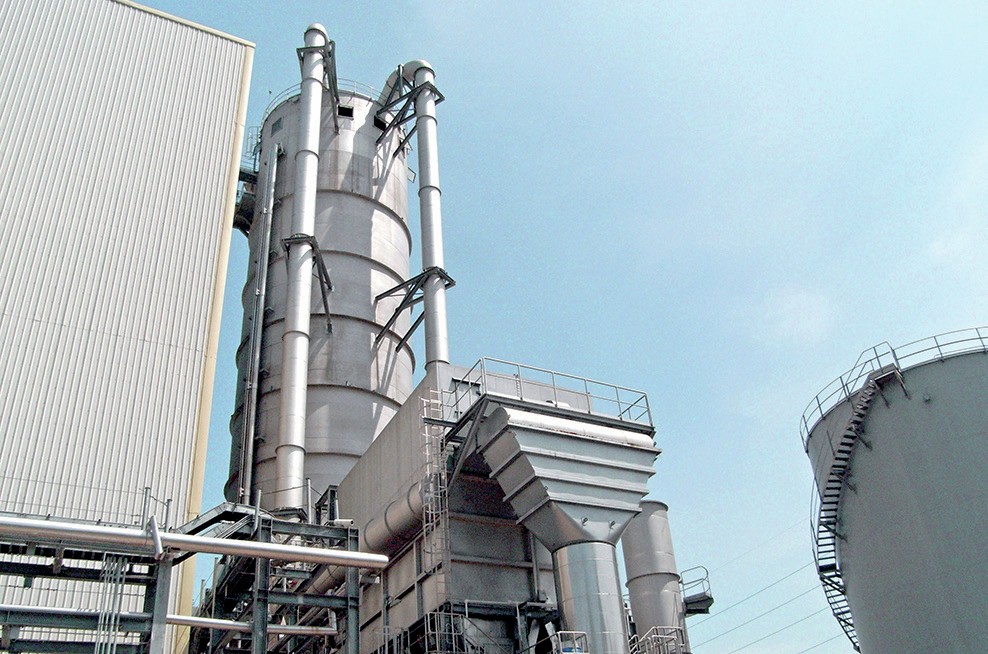
The main advantages of the prilling process are its simplicity and its flexibility when it comes to incorporating additional crop nutrients. Kreber, for example, offers prilling tower technology for both U+ES and UAS. Valuably, adding ES or AS to prills improves handling properties by increasing crushing strength and their diameter.
Fluid bed granulation
Most of remaining 25% of urea plants operate a fluid bed granulation unit for fertilizer finishing. Capacities range from 500 t/d to 4,000 t/d. The concentration of urea melt varies between 96-98.5 wt% depending on the fluid bed granulation technology (Uhde, Stamicarbon, Toyo, Casale etc.). Fluid bed granulation is generally a more complicated process than prilling and, consequently, sprayer design and spraying conditions can have a real influence on overall urea plant performance.
Similar to prilling, large air flows are used to remove heat during solidification. Urea granules (average size typically 3 mm) are larger than prills and have a higher crushing strength (3 kg/cm2 ). Fluid bed granulation is typically used in export-oriented urea plants as the robust granules obtained are suitable for both bulk transport and bulk blending.
Drum granulation
Globally, some ten urea plants currently use drum granulators in their finishing sections. Capacities vary between 100-500 t/d, although Ballestra’s new bi-fluid drum granulator (BFDG) – see Figure 2 – can handle higher capacities due to its superior cooling performance (Fertilizer International 513, p33). Typically, 96 wt% urea melt is used as feed and, again, large air flows are required during solidification to remove heat.
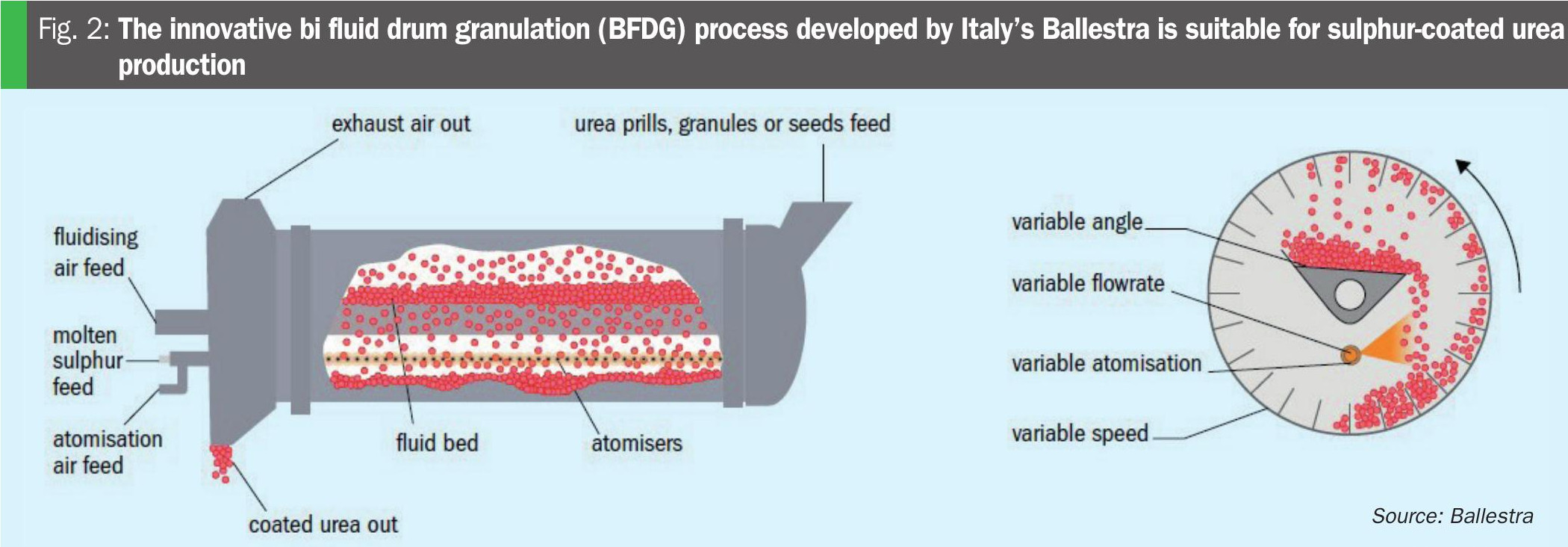
Drum granulation is a more flexible process, compared to fluid bed granulation, and thanks to a simpler sprayer design can be used to create multi-nutrient fertilizers as well as applying a coating. The granules obtained have similar properties to those from fluid bed granulation. Additionally, drum granulation can also be used to ‘fatten’ prills and convert these into granules, although the resulting crushing strength is lower than that of conventional granules.
IPCO Rotoform pastillation
Ten or more IPCO Rotoform urea finishing units are operating currently, with many more units installed for sulphur pastillation. Each line has a 125 t/d capacity and uses a 99.6 wt% urea melt. Heat is removed during solidification by cooling water. The process helps to avoid atmospheric emissions as hardly any air flow is required.
Rotoform equipment generates very uniform pastilles and allows the size of these to be varied from 1-5 mm. The crushing strength of pastilles is intermediate between that of prills and granules. IPCO recently introduced the Rotoform XG high capacity pastillation system for fertilizer finishing (see photo).
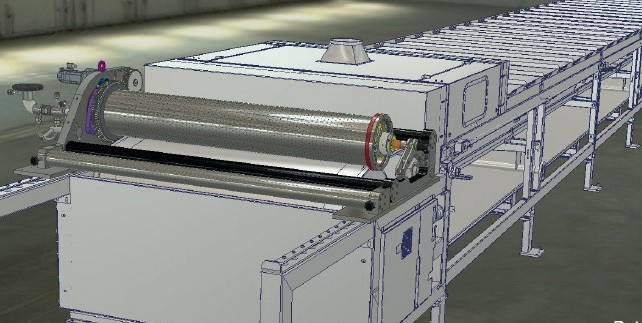
IPCO can also supply upstream solutions including blending and grinding units (Figure 3) that, by combining liquid and solid raw materials, enable the production of specialty urea products (Fertilizer International 497, p24) such as:
- Urea + elemental sulphur
- Urea + ammonium sulphate
- Urea + potassium
- Urea blended with micronutrients.
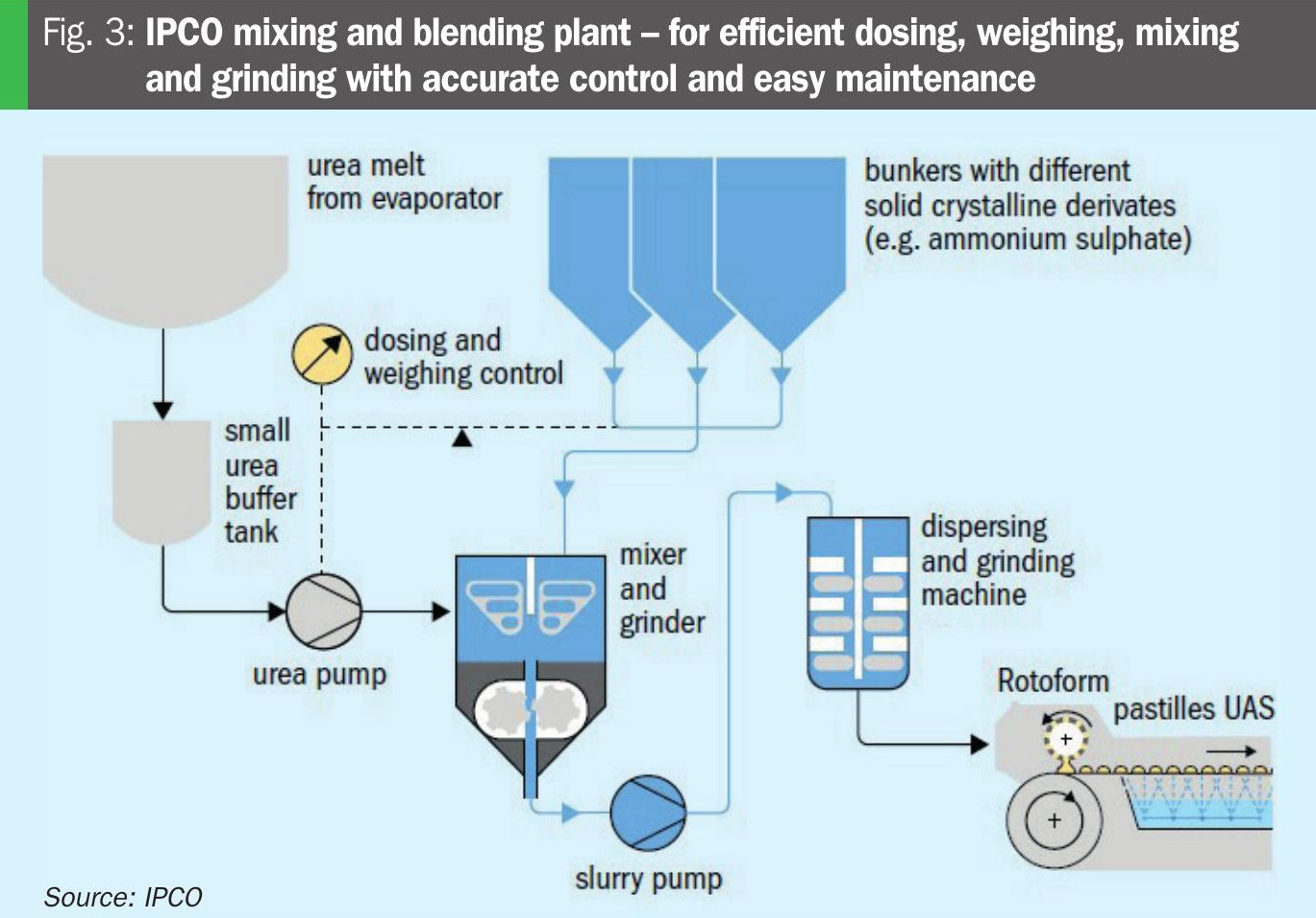
Urea plus elemental sulphur (U+ES) production
Successful production of U+ES has a number of requirements:
- The ability to cope with the different melting melt points of urea (133°C) and elemental sulphur (115°C).
- Then properly mix the urea melt and sulphur melt using an emulsifier. This is necessary as they are immiscible, like oil and water.
- Finally, the elemental sulphur needs to be finely dispersed and incorporated within prills, granules and pastilles as micron-size particles. This is necessary to provide a large available surface area that will subsequently allow soil bacteria to quickly convert elemental sulphur into plant-available sulphate.
Three companies, Yara International, Shell Sulphur Solutions and Sulvaris, have developed technologies that combine elemental sulphur with urea (including a patented emulsifier) and – except for Yara – license these to third-party fertilizer producers.
Shell Sulphur Solutions successfully commercialised its patented Thiogro technology in the early 2000s. This was initially developed for dispersing sulphur within granulated ammonium phosphates. Sulphur-enhanced phosphate lines have subsequently been licensed and installed at phosphate fertilizer plants in Asia, North America and Australia. This includes a major collaboration with SinoChem in China (Sulphur 381, p24). Shell also landed a major licensing deal with OCP Group in 2016. This allows the Moroccan phosphate giant to produce its own range of highly concentrated sulphur-enhanced fertilizers using Thiogro technology at its Jorf Lasfar site.
Shell subsequently introduced Urea-ES – a product with a nitrogen content of 37-43% and containing a 7-20% dispersion of micronised sulphur in a urea matrix – to the market in 2015. This was followed in 2017 by the introduction of high sulphur urea product Special-S (11-0-0-75ES).
Shell has successfully collaborated with both thyssenkrupp (Uhde Fertilizer Technologies) and IPCO, leading providers of fluid bed granulation and Rotoform pastillation, respectively. These partnerships mean Urea-ES and Special-Stechnologies are now widely available to producers wishing to expand their portfolios to include sulphur-enhanced fertilizers (Fertilizer International 492, p44).
In the US, Thiogro technology was installed at Two Rivers Terminal’s production site in Moses Lake, Washington state, in 2018. The company produces highly concentrated Special-S pastilles (11-0-0-75ES) for the Pacific Northwest and California markets using IPCO Rotoform equipment.
H Sulphur Corp, one of Asia’s leading sulphur suppliers and sulphur-bentonite producers, commissioned the first ever Special-S production plant in South Korea in 2019 using Thiogro technology under license from Shell. The company has successfully sold and shipped Special-S to customers in Canada, Australia and Brazil under its own Super S brand name (Fertilizer International 492, p44).
Canada’s Northern Nutrients has been producing Special-S (10-0-0-75, Artic-S) and Urea-ES (38-0-0-18+stabiliser) products under license from Shell using two IPCO Rotoform units since 2022 (see main photo). In comparison to AS, the highly concentrated Special-S formula delivers transportation, storage and application cost savings by efficiently moving almost double the per tonne nutrient content through the supply chain.
In the Middle East, RNZ International has been producing the sulphur-enhanced Purti NS Plus fertilizer (10-0-0+75S) at its Kizad production plant in Abu Dhabi since 2022 using Thiogro technology under license (Fertilizer International 520, p26).
Calgary-headquartered Sulvaris has commercialised a proprietary micronised sulphur technology (MST® ) that reduces elemental sulphur to an average size of less than 10 microns. MST® has successfully been incorporated into a range of fertilizers, including AS, monoammonium phosphate (MAP), potash, triple superphosphate (TSP) and urea ammonium nitrate (UAN).
In collaboration with Nutrien, the world’s largest fertilizer producer and retailer, Sulvaris has developed a product that combines with MST® with MAP. This is marketed by Nutrien under the brand name Smart Nutrition™ MAP+MST® (Fertilizer International 513, p33).
Sulvaris has also created a patented urea + MST® product. This is manufactured by incorporating micronised elemental sulphur directly into the urea melt during granulation. The resulting Urea + MST® granules have a 5-12 percent elemental sulphur content. The Canadian company is also collaborating with Netherlands-based prilling experts Kreber on incorporating MST® into urea prills.
Urea ammonium sulphate (UAS) production
Successful UAS production is a particular challenge because the two components have a eutectic point at around 9-12% AS, depending on the water content. Increasing AS content beyond this significantly increase the melting point and therefore creates a suspension at higher AS levels.
Despite this potential drawback, Casale, IPCO, Stamicarbon, Toyo/Agrofert and Yara International have all successfully developed production processes for UAS. Again, all these companies – except for Yara – license their UAS technologies to third-party fertilizer producers.
In Germany, Toyo and Agrofert (formerly SKW) have jointly developed a UAS production route using Toyo’s ‘spouted bed’ fluid bed granulator. The process uses a solid AS feedstock prepared with a mixer-grinder. The 500 t/d unit has been in operation since 1998 and produces a 33-0-0-12 fertilizer, corresponding to around 50% AS by weight.
Yara has been producing UAS at its Sluiskil plant in the Netherland since 1998. The company added another 2,000 t/d capacity UAS fluid bed granulation line at the site in 2020.
Sluiskil operates as an integrated urea/ UAS unit that generates AS within the urea melt plant. Sulphuric acid is added to the urea solution downstream of the high-pressure CO2 stripper using a pipe reactor. The heat of reaction between ammonia and sulphuric acid reduces energy consumption by helping to evaporate water. Sluiskil produces a 40-0-0-5.6 UAS product, this corresponding to an AS content of around 23%.
In Poland, Grupa Azoty Pulawy has been producing UAS from two IPCO Rotoform pastillation units (125 t/d capacity each) since 2013. These consume a solid AS feedstock prepared with a mixer-grinder which also features a slurry pump. The site produces a 36-0-0-8 fertilizer with 35% AS content.
Stamicarbon designed its first commercial UAS plant for EuroChem’s Novomoskovk Azot production site. This was formally opened in December 2018 as Russia’s first urea-UAS plant with a capacity of 400 t/d for urea and 600 t/d for UAS (Fertilizer International 490, p31). Stamicarbon’s UAS process is designed for 0-50% AS content, with up to 32% being realised. This process (Figure 4) also uses a solid AS feedstock prepared with a mixer-grinder.
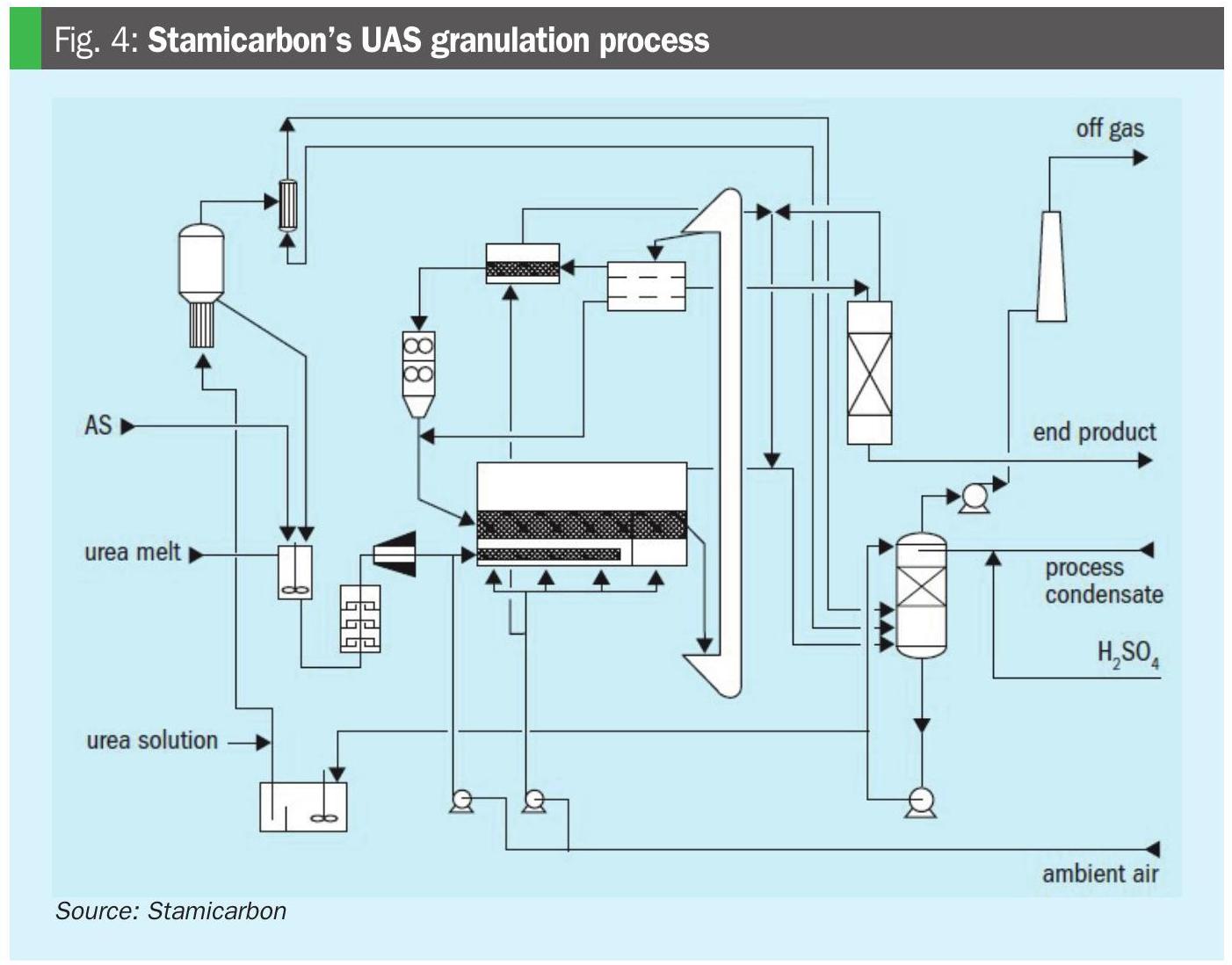
Most recently, China’s Xinjiang Xinji Energy Recycling was expected to start up a 1,900 t/d capacity Casale UAS fluid bed granulation unit in December 2024. The plant, which consumes a solid AS feedstock, is fully flexible with the ability to produce either standard urea or UAS with an AS content of up to 25%.
Casale uses a ‘double granulator’ design to avoid reaching the eutectic point in UAS production. This enables the continuous production of UAS at any composition between 0-25% AS under optimum granulation conditions, by allowing melts of different compositions to be fed to separate sections of the granulator. This flexibility also provides the plant operator with the ability to continue production even if the supply of AS becomes unavailable or is reduced.
Conclusions
- While sulphur is regarded by many as the fourth crop nutrient, soils globally are becoming increasingly sulphur deficient.
- Fortunately, there are several proven and successful process technologies available for incorporating sulphur – in elemental or sulphate form – into urea, the world’s most widely applied commodity fertilizer.
- Beneficially, the addition of sulphur also increases the nitrogen use efficiency (NUE) of urea.
- The production of urea plus elemental sulphur (U+ES) fertilizers requires an emulsifier to properly disperse sulphur particles within granules, prills and pastilles.
- The elemental sulphur is also micronised so it can be quickly converted into plant-available sulphate by soil bacteria.
- Successful urea ammonium sulphate (UAS) production is a particular challenge because the two components – urea and ammonium sulphate (AS) – have a eutectic point at around 9-12% AS.
- Despite this potential drawback, the nitrogen industry’s main technology licensors and leading fertilizer producer Yara International have all successfully developed production processes for UAS.
Author’s note
This article is based on the paper presented at the International Fertiliser Society (IFS) Conference, Cambridge, UK, 12th December 2024, and subsequently published by the Society. Additional reporting by Simon Inglethorpe.
Reference
Brouwer, M., 2024. Proven process technologies for urea fertilisers enriched with elemental sulphur or ammonium sulphate. International Fertiliser Society Proceedings, 890. ISBN 9780-85310-527-5.