Nitrogen+Syngas 395 May-Jun 2025
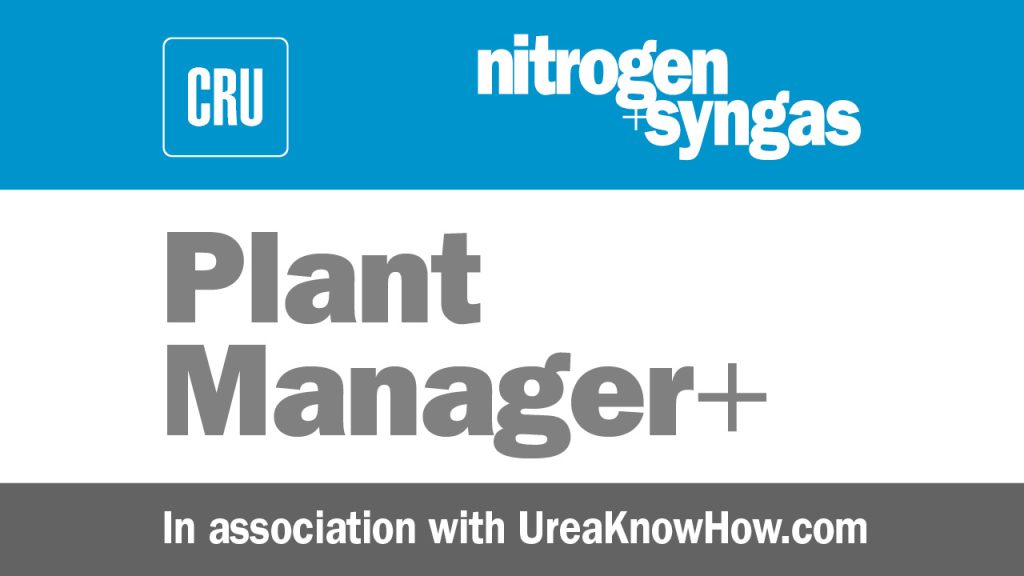
2 May 2025
Problem No. 74: Is green urea really green?
Ali Ançaza from Igsas in Turkey kicks off this round table discussion: Our synthesis section was blocked during a 12-hour shutdown. The synthesis section was then drained and emptied. While recycling the urea solution in the urea solution tank via the evaporation section, we noticed that the colour of the solution was green as you can see in the pictures below. I wonder what could be the reason for this? Has anyone experienced such an event?
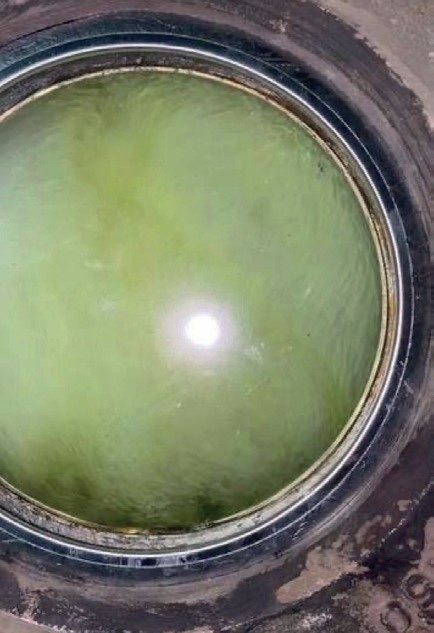
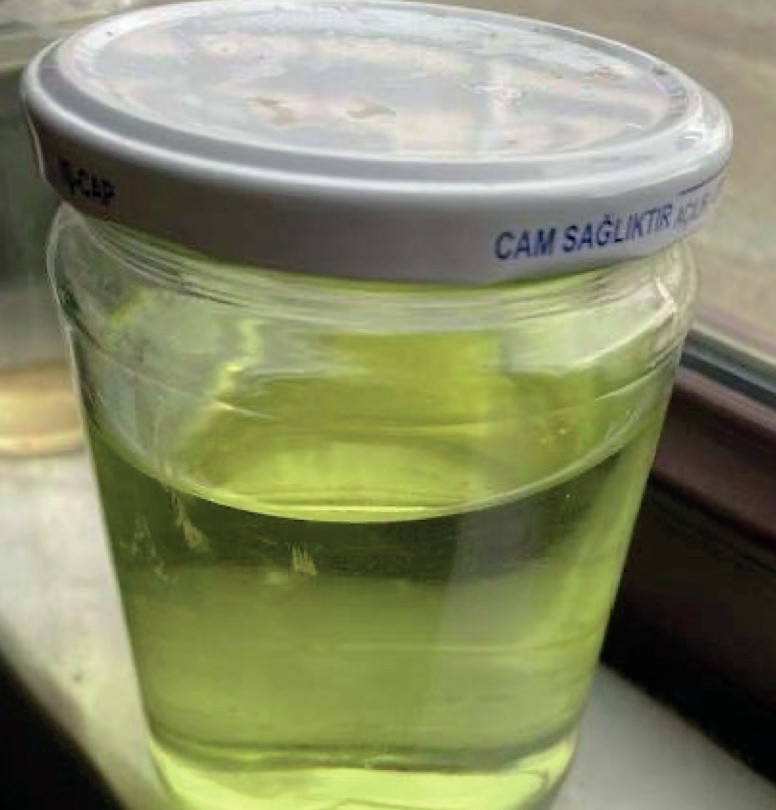
Mark Brouwer of UreaKnowHow.comin the Netherlands replies and asks a question: As you know, normally the urea melt and product can become reddish after blocking in. Did you analyse for metals (Ni, Cr, Fe, Cu, …)?
Ali replies: We did the analyses and obtained the following results. The first sample result: Cu: 0 ppm; Fe: 0 ppm; Ni: 0.9 ppm; Cr: 9.6 ppm, Na: 0.7 ppm; Mo: 0.9 ppm, N: 2.75%. 2nd sample result (after 15 minutes): Cu: 0 ppm, Fe: 0 ppm, Ni: 1.7 ppm, Cr: 17.8 ppm, Na: 1.3 ppm, Mo: 0.74 ppm, N: 4.08%. 3nd sample result (after 30 minutes): Cu: 0 ppm, Fe: 0 ppm, Ni: 3.1 ppm, Cr: 28 ppm, Na: 2.3 ppm, Mo: 1.24 ppm.
Mark responds: What are the normal Ni levels? In case you see a rising trend of nickel (days) you are experiencing active corrosion. The next step is take more samples upstream and see where the delta-Ni over an equipment item or section is rising. Then shut down and inspect that equipment/section.
Rama Raghava Kumar Kotti, freelance operations consultant and expert of UreaKnowHow.com joins the discussion: To further investigate this incident, I’d like to clarify a few points:
- Sampling procedure: Were the samples taken sequentially during the draining process of the synthesis section, or were they collected after the draining was complete and the tank level stabilised?
- Off-spec urea recycling: Are you recycling any off-spec urea into the system? If so, what are the known contaminants in this off-spec urea?
- Urea storage tank cleaning: When was the last time the urea storage tank was cleaned? Prolonged periods without cleaning can lead to the accumulation of impurities.
- Other tank draining: During the 12-hour shutdown, were any other tanks, such as the ammonia receiver or carbonate solution tank, drained alongside the synthesis section?
- CO2 removal section: Could potential carbon components or byproducts from the CO2 removal section in the ammonia plant be contributing to the green coloration?
- Equipment inspection: If you have already inspected the relevant equipment, could you please share the findings?
Ali replies: We had a stop for about one month. During this stop, all synthesis lines were technically checked by Stamicarbon. The urea solution tank was completely emptied and cleaned. We put the system back into operation. Stripper, rectifying column (first picture below) and melt urea pump (second picture below) samples were taken from the first solution coming from the synthesis. We observed a visible green solution. We took samples and analysed them. Chromium nickel values were high. After about two hours, the colour of the solution started to return to normal. Analysis values also started to return to normal. The system is still working. Ni values continue to be around 0.5 to 0.6 ppm.
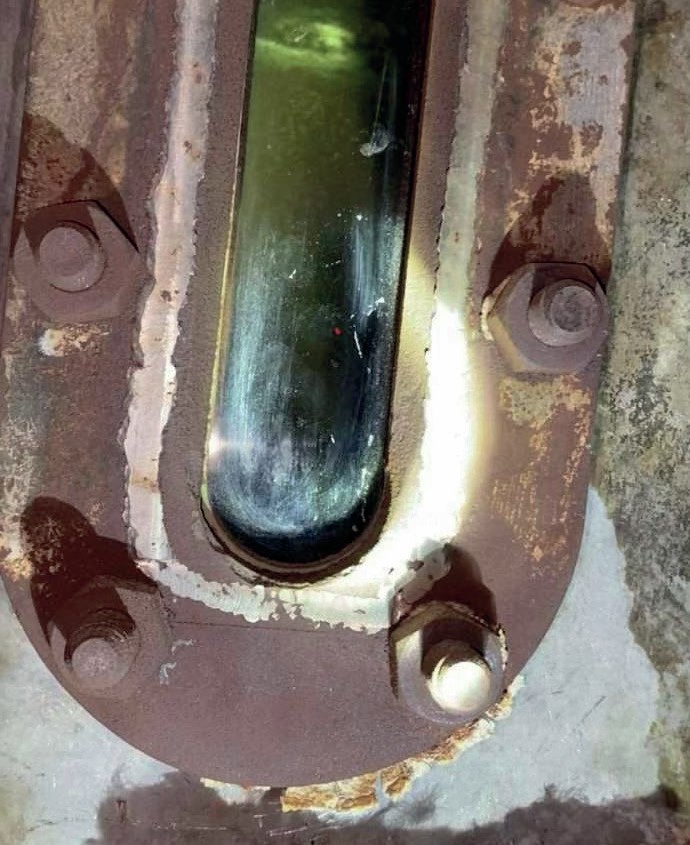
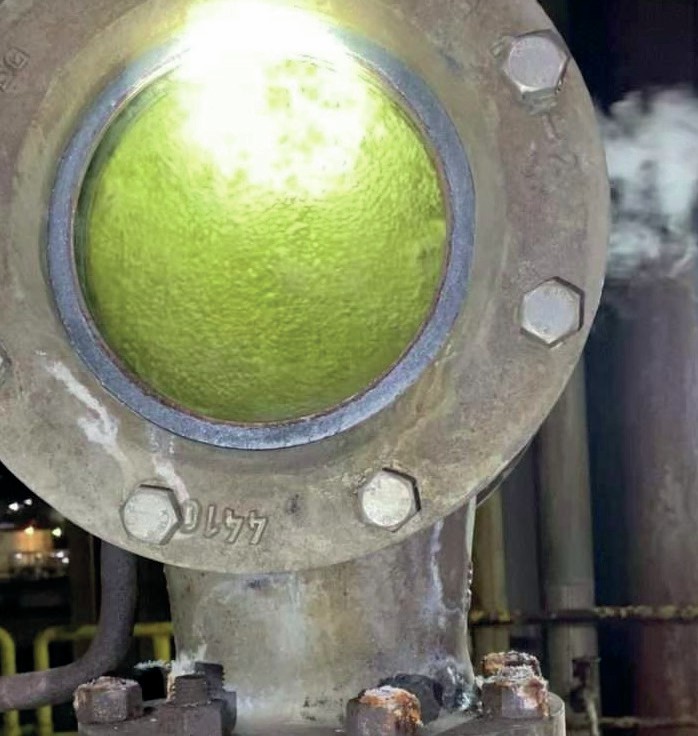
Mark suggests a possible cause: I think the green colour is a result of the larger amounts of chromium oxides, which seem to have a green-blue colour according to the following: “The prevalence of chromium oxides resulted in greenish or bluish shades, whereas iron oxides’ dominance produced brownish and reddish hues.” Source: https://www.sciencedirect.com/science/article/abs/pii/S0030399223013622?via%3Dihub
Kumar makes further enquiries to find a cause: A one month shutdown was a good interval for conducting a detailed inspection of the equipment and pipelines for the entire urea plant. Was any thickness reduction observed in the main HP loop synthesis equipment e.g. the urea reactor, stripper, etc. or the pipelines? What was the oxygen percentage in CO2 maintained before shutdown? Was the online oxygen analyser or air flow meter calibrated? Did you observe anything while cleaning urea solution tank bottom?
Ali replies: Our facility has completed 50 years. Work began to change the synthesis lines approximately two years ago. New lines will come this year.
What we are curious about is that the green solution is first activated or blocked and then returns to normal after two hours. If there is active corrosion, why doesn’t it continue?
• Iron oxide residues were found in the sediment at the bottom of the urea solution tank.
• Oxygen values in CO2 are 0.8 to 0.9 vol-% before the stripper.
- We do not have an instantaneous tracking analyser for hydrogen and oxygen. We follow the hydrogen converter inlet-outlet temperature difference and additional air.
Kumar provides a possible suggestion for the temporary green colour: A possible explanation for corrosion not continuing could be due to dynamic passivation. The formation of a passive layer on the metal surface is dynamic. If there is a deficiency of oxygen or a lack of oxygen for a certain period, it can lead to temporary corrosion and potentially result in material loss. Once oxygen is restored, the passive layer can reform, inhibiting further corrosion. However, this is just one possible explanation and cannot be confirmed without further investigation and analysis of relevant parameters.
Ali replies: Actually, this green solution incident occurred after pipe replacement with 316L pipe (with Stamicarbon approval) in February 2024 because the HP scrubber GCB line thickness value was too low and the pipe could not be supplied for replacement. After that, the first solution coming from the synthesis was seen to be green in the subsequent commissioning and exits. In the technical control made after the last stop, no excessive corrosion was detected in the 316L pipe. Do you think this is possible due to the 316L material?
Mark replies: Yes, I think applying 316L instead of 316L UG will lead to higher corrosion rates under synthesis conditions. But whether one line can make this difference, I doubt.
You also had a blocking in situation didn’t you? That leads to accumulation of chromium oxides in the blocked in liquid.
Dynamic passivation is an interesting topic. The formation of a passive chromium-oxide layer is an equilibrium with the dissolving rate of chromium oxides in the acid ammonium carbamate solution. But once active corrosion starts it cannot be stopped by adding more oxygen. One has to stop the plant, drain and re-passivate the surface.
Kumar comes back with some follow up questions: How long was the solution held in the urea reactor before start-up? Was this holding time longer than the licensor’s recommendation?
Can you confirm that chromium levels are stable while nickel levels are elevated?
Blocking urea solution in the urea reactor for an extended period can indeed lead to the accumulation of chromium oxides in the blocked-in liquid.
Referring to the potential impact of using 316L instead of 316L UG, I fully agree with the earlier assessment. As correctly pointed out, a smooth metallic surface generally indicates that the passive layer is intact and active corrosion has not yet significantly progressed. Once the metallic surface becomes rough, for example inside the urea reactor, it signifies that active corrosion has already taken place, and the passive layer has been compromised.
Ali provides more details of the incident: On 03-12-2024 at 08:30 due to a problem in the ammonia unit, we stopped the system. We waited for about 12 hours with the synthesis block. After 12 hours, while restarting the system, we went out of service due to a different malfunction and drained and emptied the synthesis.
On 10-12-2024, we started to restart the system, while the synthesis was heating.
While rotating the evaporation in circulation with the solution in the urea solution tank (the solution we drained the synthesis), we noticed that the solution in the observation glass was green. When we took samples from the solution in the urea solution tank and analysed them, we saw the analysis results reported earlier.
We stopped commissioning the system. We completely emptied and cleaned the urea solution tank. Corrosion inspection of the synthesis lines was performed. It was reported that there was no situation preventing operation (Stamicarbon).
We re-commissioned the synthesis on 20-01-2025 (ammonia was fed after 4 hours of passivation and the level in the reactor was reached after 2 hours. No waiting was done).
The rest is as already mentioned.
Mark replies: The pictures below show passive and active corrosion. Passive corrosion is typically a blueish, reddish or grey colour, while active corrosion gives a silver shiny surface.
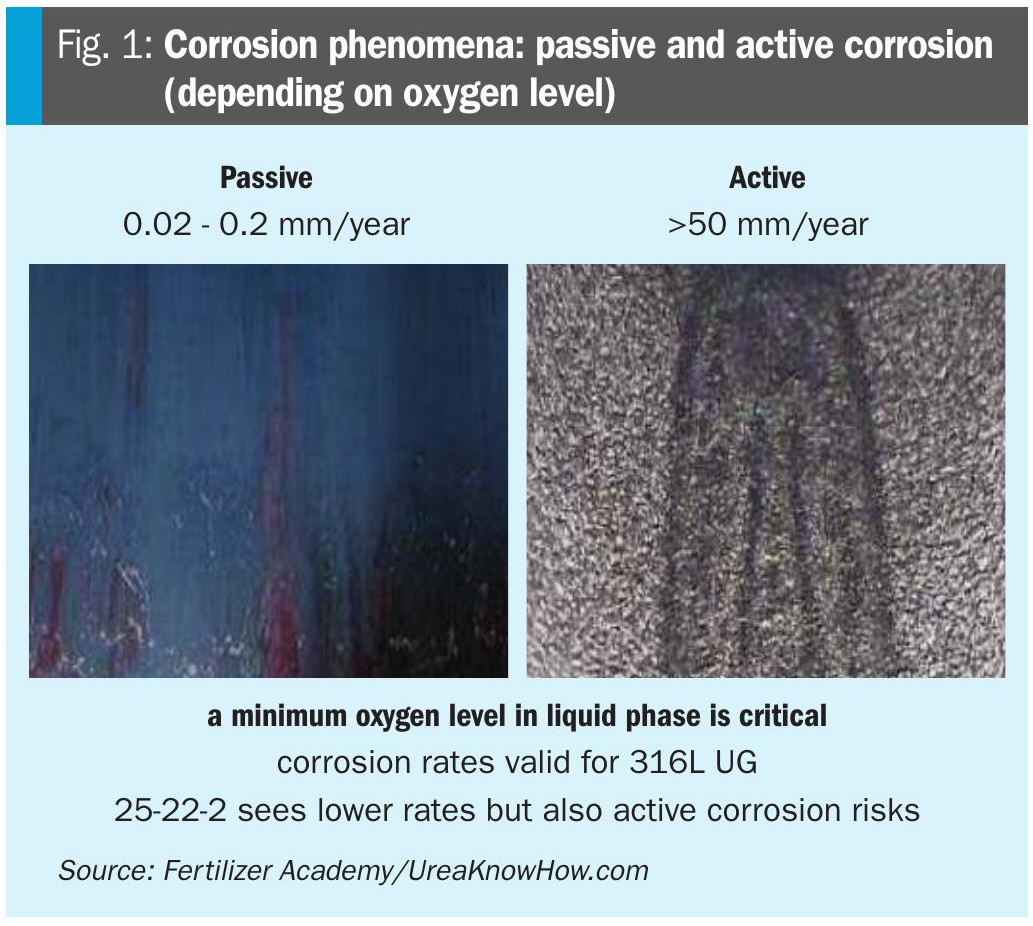
Kumar replies: The images along with the corrosion rates are truly informative and a valuable learning experience.
Please find my observations as mentioned below:
• A 12-hour block of urea solution may not be the sole cause of this issue unless proper MOC is in place.
- The replacement of the HP scrubber GCB line with 316L in February 2024 suggests that corrosion concerns were already identified in this specific area. This incident highlights the potential for localised corrosion in other critical components within the system.
- The age of the plant (50 years) raises concerns about the suitability of existing materials for the current operating conditions. A comprehensive equipment/pipe lines materials suitability review, considering factors such as operating temperature, pressure, and the presence of corrosive species, is crucial. What is the capacity of your plant? You may calculate how much chromium is lost during the incident and considering parameters at that time.
- Can you confirm that the oxygen meter before the stripper was calibrated before and after the December 2024 shutdown? Accurate oxygen measurements are critical for understanding and controlling corrosion processes.
- A thorough investigation is recommended, including a detailed review of operating logs, material analysis of corroded components, and potentially a review of the original design specifications to identify potential areas for improvement.
Ali comes back: We do not have a continuous oxygen meter in our system. We take samples from CO2 before the stripper and analyse it. The oxygen value is around 0.8 – 0.9 – 1 vol-%.
The last corrosion inspection we had on the synthesis lines reported no problem preventing the start-up. The new lines were ordered and the delivery process is ongoing.
Mark replies: It is recommended to install a continuous O2 analyser to ensure sufficient oxygen is supplied to prevent active corrosion. Once active corrosion occurs it cannot be stopped by adding extra oxygen.
It is good practice to take daily samples of the final product, analyse nickel and watch for rising trends indicating active corrosion (see figure below).
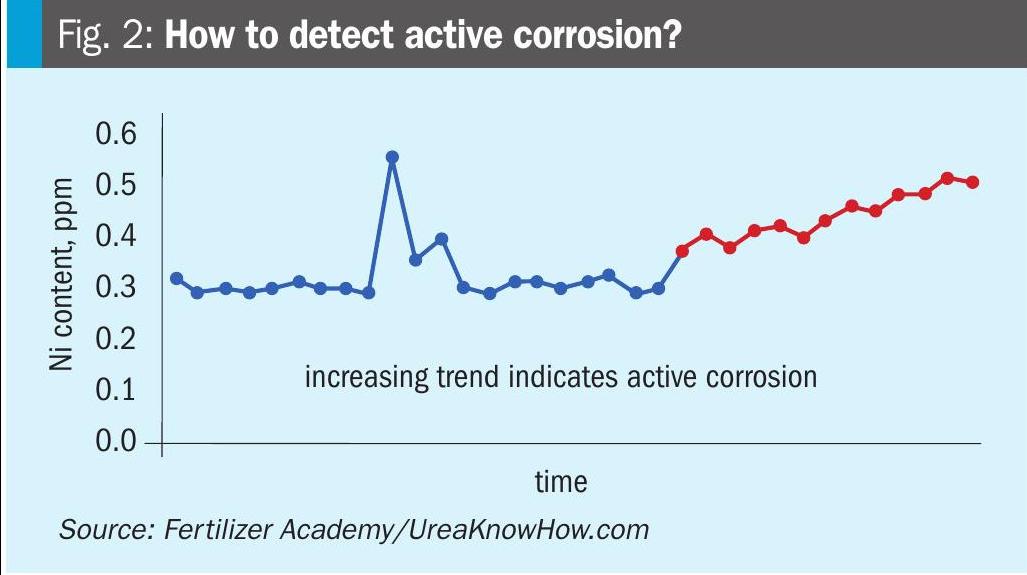
Another benefit of a continuous O2 analyser is that one can control the oxygen content more closely to the minimum required 0.6 vol-% (in case the stripper has 25-22-2 tubes).