Nitrogen+Syngas 395 May-Jun 2025
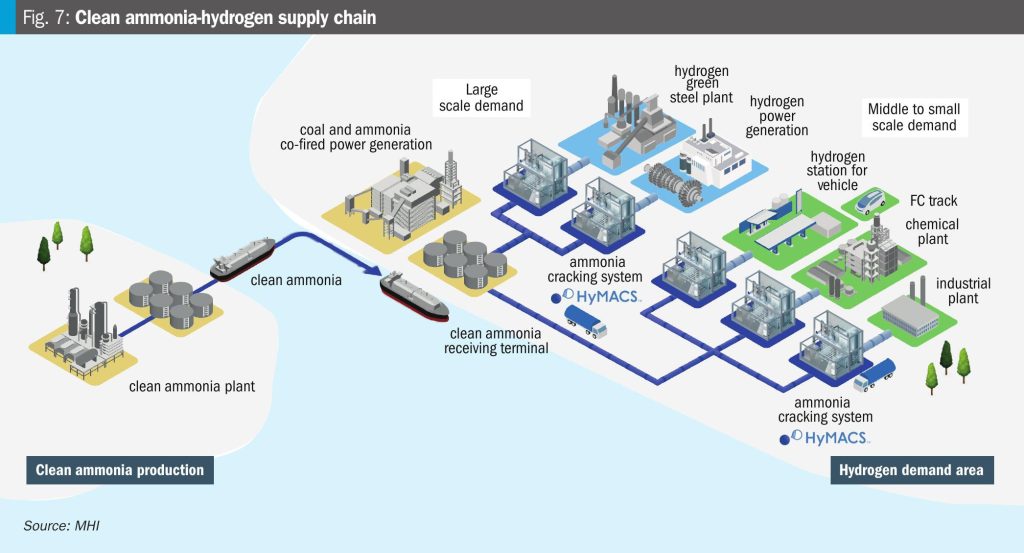
2 May 2025
Low temperature ammonia cracking technology
AMMONIA CRACKING
Low temperature ammonia cracking technology
Mitsubishi Heavy Industries is developing a low temperature ammonia cracking technology (HyMACS™) that leverages exhaust heat from existing sources, such as boilers, steam turbines, engines, and heating furnaces. This innovative approach, which also includes the development of more efficient membrane separation technology using molecular sieves for hydrogen purification, is designed to offer a more sustainable, reliable and cost-effective pathway towards hydrogen production.
Hydrogen, a promising clean energy source, presents challenges in storage and transportation due to its low energy density and high diffusivity. Considering this, ammonia (NH3) offers a compelling solution, boasting high hydrogen content, established infrastructure, and safe handling. Its high hydrogen density (17.6% by weight) enables efficient transportation and storage
Ammonia’s readily liquefiable nature facilitates safe and efficient handling and transport. In fact, the International Energy Agency (IEA) reported shipping ammonia from Australia to Japan in 2030 is projected to be significantly more economical than directly shipping gaseous hydrogen. In Table 1 various hydrogen carriers are listed and compared as per the report by the Ministry of Economy, Trade and Industry of Japan.
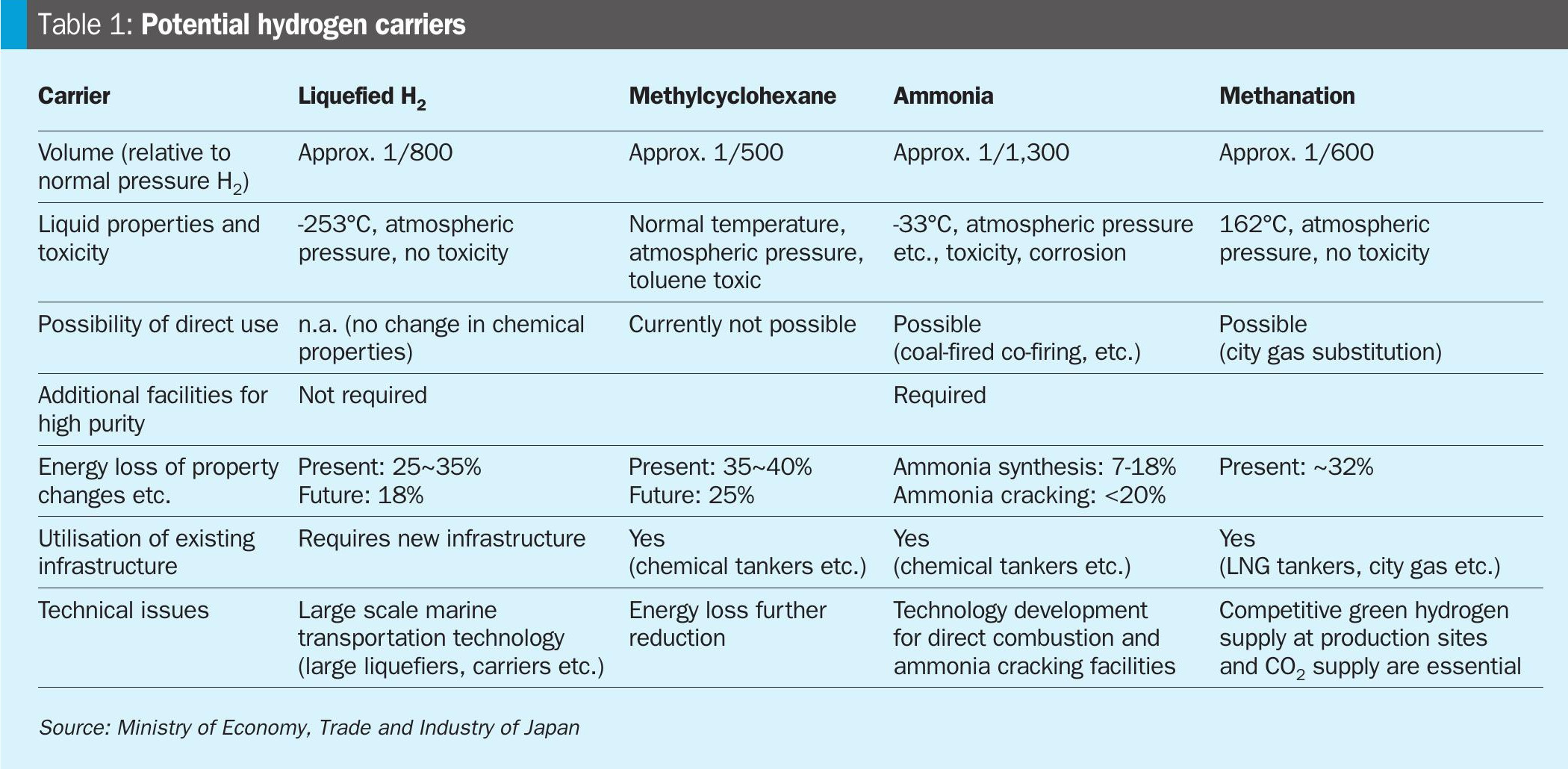
Leveraging current ammonia production, transportation, and storage infrastructure significantly reduces the need for new investments in the establishment of an ammonia-hydrogen supply chain. To fully utilise ammonia as a hydrogen carrier, the development of efficient and cost-effective ammonia cracking technologies is crucial. These technologies aim to decompose ammonia into hydrogen (H2) and nitrogen (N2).
MHI’s ammonia cracking development
Mitsubishi Heavy Industries (MHI) is actively developing its own innovative ammonia cracking technology, working on its extensive experience in ammonia plant engineering, procurement, and construction (Fig. 1). This approach enables MHI to capitalise on existing expertise, prioritise safety, and offer comprehensive solutions.
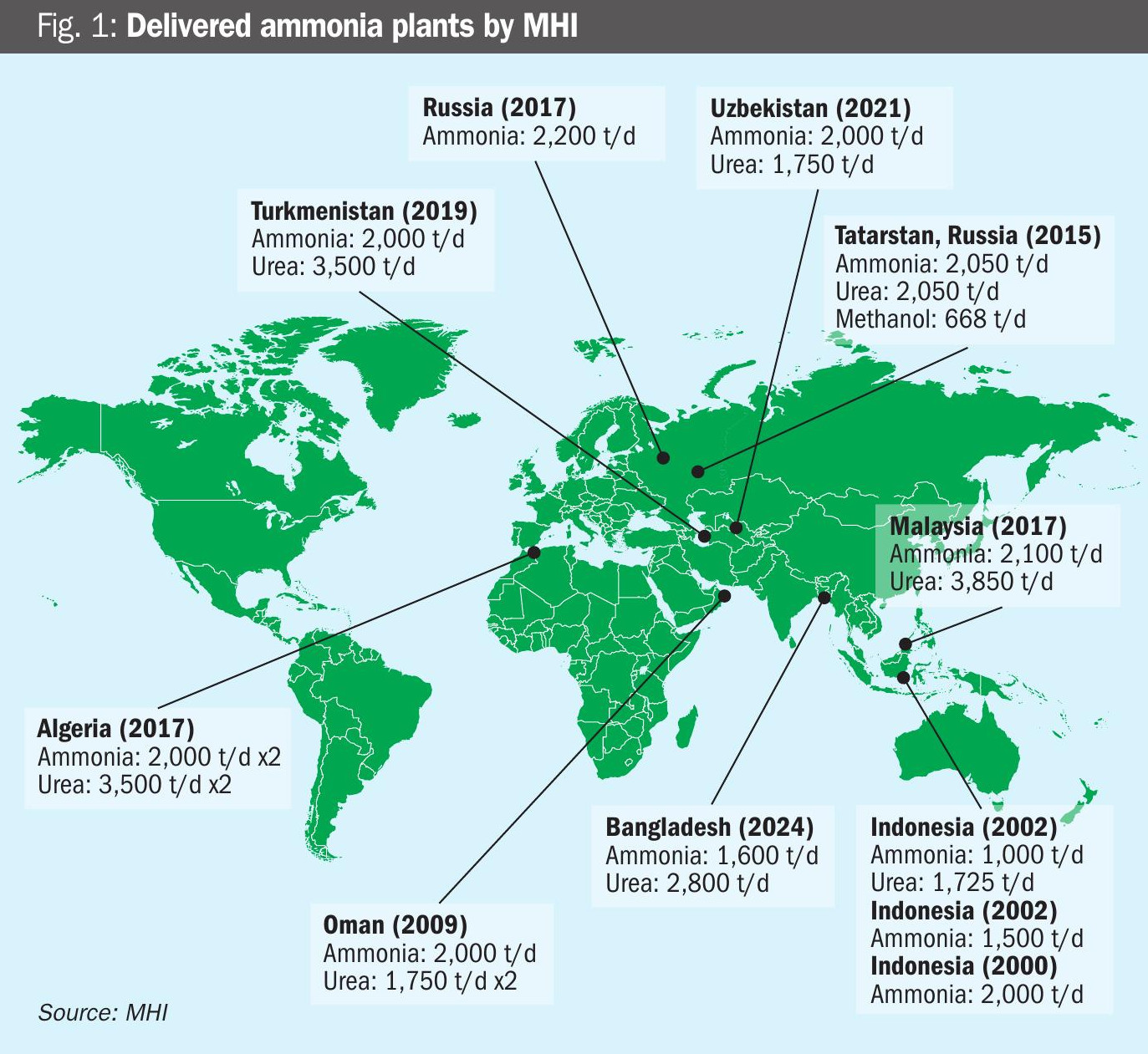
MHI can utilise design knowledge garnered from decades of experience in building ammonia synthesis plants, including expertise in handling high-temperature, high-pressure environments, managing corrosion, and working with hydrogen-rich gas streams.
Additionally, MHI draws upon its extensive experience in ammonia plant construction and operation to ensure the utmost safety in ammonia handling practices throughout the entire value chain.
MHI can provide integrated solutions for the entire clean ammonia value chain, encompassing production, ammonia transportation, receiving terminals for ammonia, and ammonia cracking infrastructure.
Low temperature ammonia cracking
Typical ammonia cracking process
The cracking of ammonia includes several key steps. First, liquid ammonia is transferred and pressurised for the cracking process. Then, it is vaporised and subsequently cracked by a catalyst. A small amount of unreacted ammonia is absorbed by water and the absorbed ammonia is separated and recovered by distillation. Finally, nitrogen is separated by the membrane separation method and hydrogen is purified. The purified hydrogen can be utilised for various applications, such as fuel cells, industrial processes, or injected into the existing gas grid.
A simplified flow diagram of the ammonia cracking process is shown in Fig. 2.
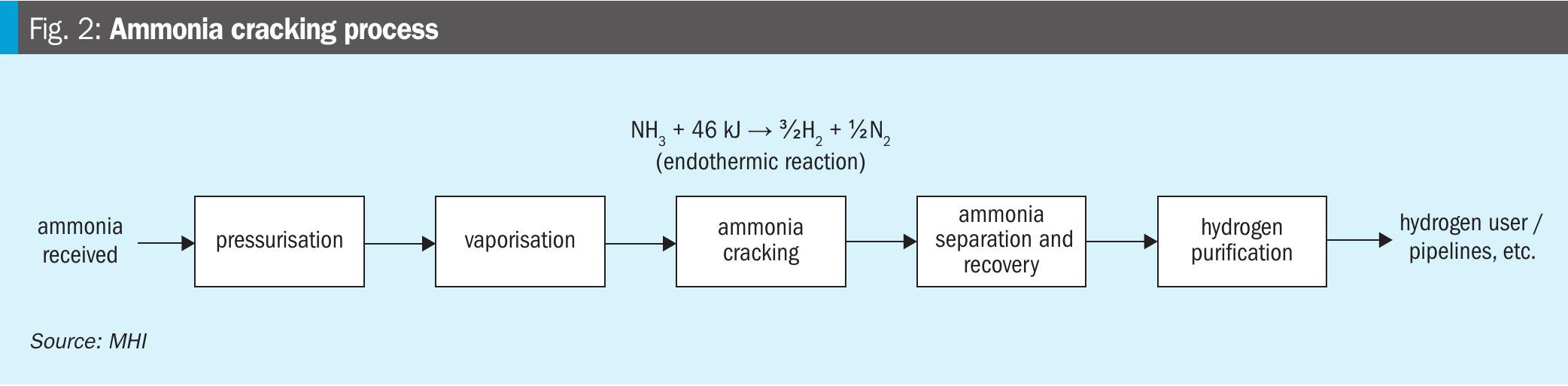
Currently, most ammonia cracking systems operate at high temperature (around 700°C). Conventional approaches often rely on high temperature fired heating cracking, akin to steam methane reformers (SMRs). High-temperature cracking faces several critical challenges. High reaction temperature induces significant thermal stresses, potentially leading to equipment fatigue and premature failure. In addition, the high-temperature environment accelerates nitriding, a process where nitrogen from the ammonia reacts with the metal components of the cracking system, causing embrittlement and reducing equipment lifetime. Furthermore, many high-temperature systems utilise the ammonia cracking gas itself as fuel for the cracking furnace, resulting in increased hydrogen consumption and consequently higher operational costs.
MHI’s low-temperature ammonia cracking system
MHI’s innovative ammonia cracking system, named HyMACS™, can operate at a significantly lower temperature range (400-500°C), utilising exhaust heat from various combustion sources, such as steam or flue gas from boilers, turbines, and engines.
Fig. 3 compares features of low-temperature and high-temperature cracking.
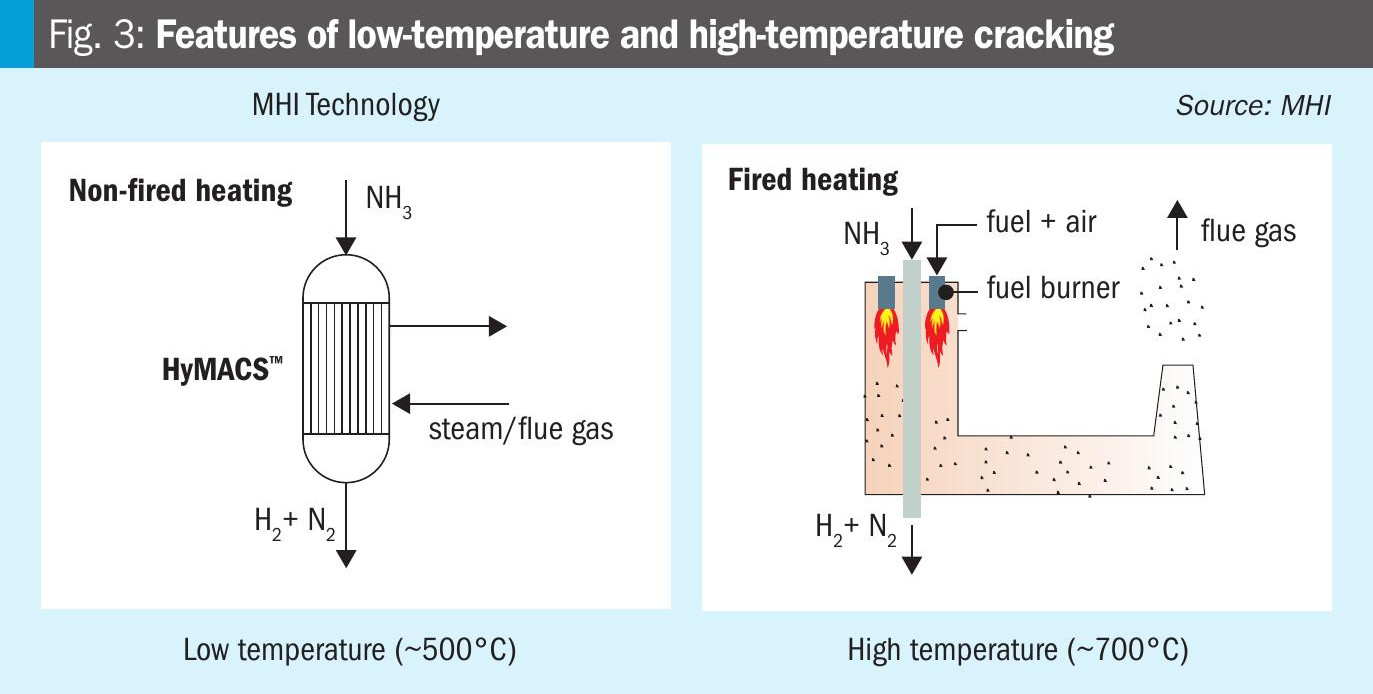
MHI’s approach offers several key advantages. Firstly, developing a non-precious metal-based catalyst will lead the low-temperature ammonia cracking. Accordingly, the lower operating temperature of HyMACS™ minimises the influence of nitriding, a prevalent issue in high-temperature cracking processes that leads to material embrittlement. Mitigating the risk of nitriding ensures the long-term durability and reliability of the cracking equipment.
The system minimises heat loss by effectively utilising exhaust heat, thus reducing the overall energy consumption and operational expenditure (opex). Additionally, no fired heater is required in MHI’s HyMACS™ which leads to a compact system.
Finally, MHI is developing a cutting-edge membrane separation method for hydrogen purification. This technology offers several advantages over traditional pressure swing adsorption (PSA) methods, including higher hydrogen yield and lower operating costs.
These key features demonstrate MHI’s commitment to developing a robust and efficient ammonia cracking technology that addresses the challenges of existing systems and offers a competitive advantage in the growing hydrogen economy.
High-activity catalyst in low temperature
Catalysts for low-temperature cracking typically consist of precious metals such as ruthenium. MHI is actively working on catalysts based on non-precious metals, which are more easily accessible compared to catalysts based on precious metals. These catalysts are designed to be much more active and stable at lower operating temperatures, resulting in high ammonia conversion.
Fig. 4 shows several catalyst types at varying catalyst bed operating temperatures, as well as their respective catalyst activity in terms of ammonia conversion rate. Among the catalysts shown in the figure below, the non-precious metal-based catalyst (highlighted) demonstrated high activity at lower catalyst bed temperatures.
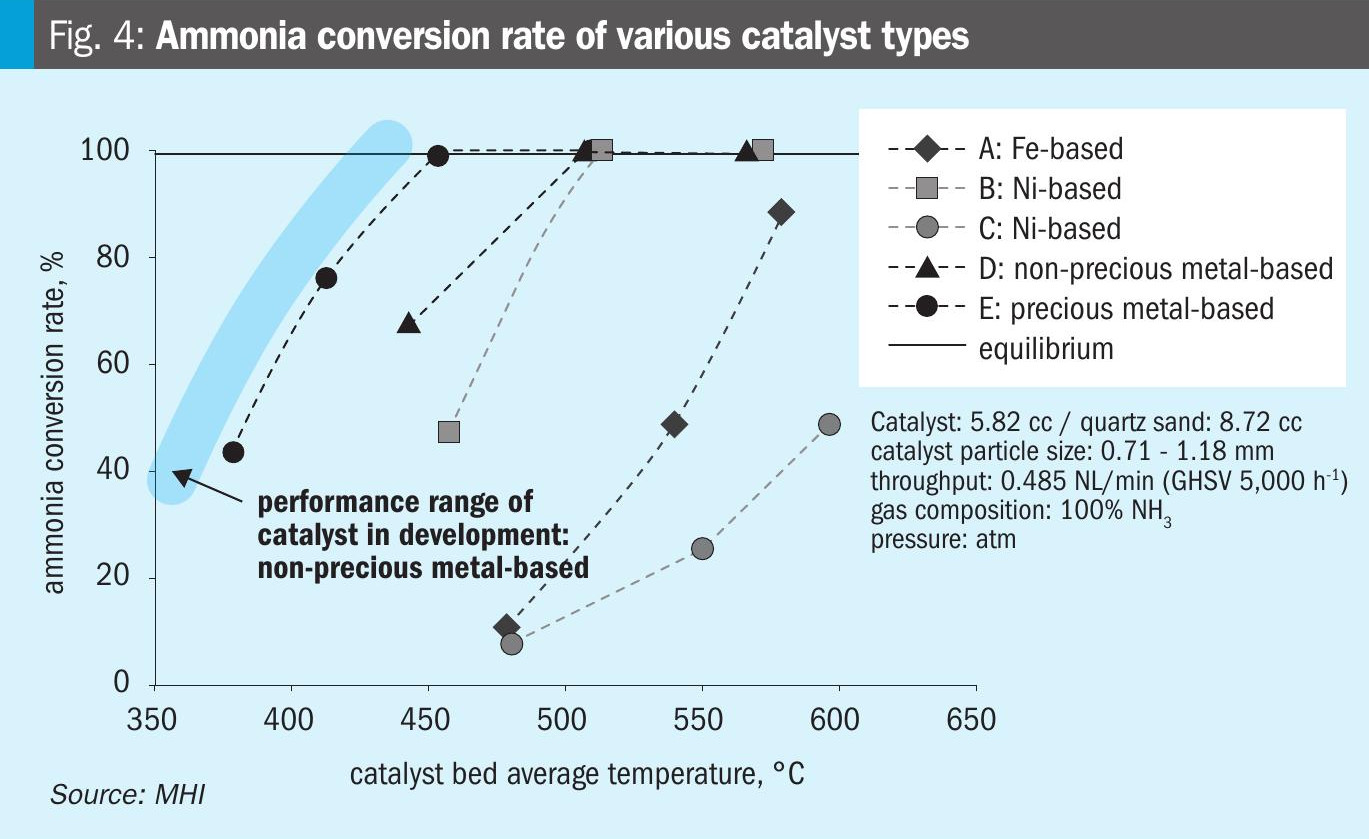
Low nitriding risk
Nitriding, a process where nitrogen reacts with the metal components of the cracking system, is a significant concern in high-temperature ammonia cracking (see Fig.5).
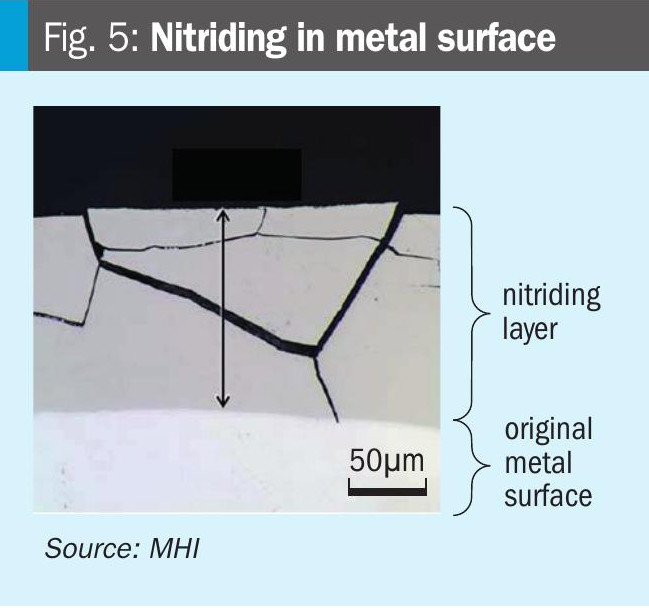
To mitigate this issue, MHI has optimised the cracking process parameters, such as temperature and ammonia concentration, to minimise the occurrence of nitriding while maintaining high hydrogen yield. MHI’s patented technology (JP7389065B2) utilises cracked gas recycling which has lower nitriding potential.

where, pNH3 is the partial pressure of ammonia and pH2 is the partial pressure of hydrogen.
Compact module
MHI recognises the diverse hydrogen needs of many sectors and applications. To meet this broad demand, MHI’s ammonia cracking technology provides a versatile capacity range, from small-scale units producing 10 kg/h of hydrogen to large-scale units capable of producing up to 1,000 kg/h. This scalability enables MHI to deliver tailored solutions for a wide range of applications, including small industrial use, large-scale power generating, and steelmaking.
This adaptable methodology means that MHI’s ammonia cracking technology may be smoothly integrated into a variety of current and new hydrogen ecosystems.
Furthermore, MHI’s steam heating system outperforms fired-heating systems in terms of opex and capex using the high-activity catalyst with low-temperature cracking technology. The compact container-sized skid module cracks ammonia and produces hydrogen using steam or exhaust gas as a heat source.
Table 2 compares HyMACS™ and fired ammonia cracking.
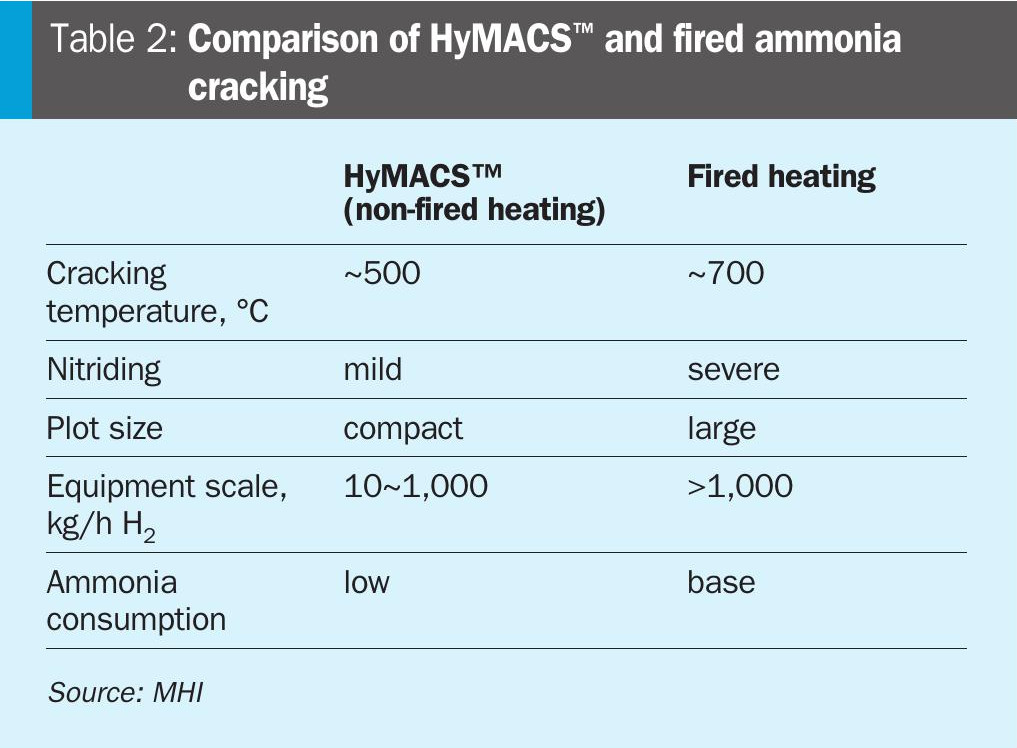
Hydrogen purification with ceramic membranes
MHI’s ammonia cracking technology utilises an innovative hydrogen purification process based on a membrane separation method. This process uses a ceramic membrane as the membrane element, offering significant advantages over conventional purification techniques such as PSA.
In a ceramic membrane purification process, feed gas containing hydrogen and nitrogen enters the membrane material which allows permeate gas, which is hydrogen, to pass through as the main product (Fig. 6). Consequently, outlet gas containing mainly nitrogen with a small amount of hydrogen exits at the outlet of the membrane.
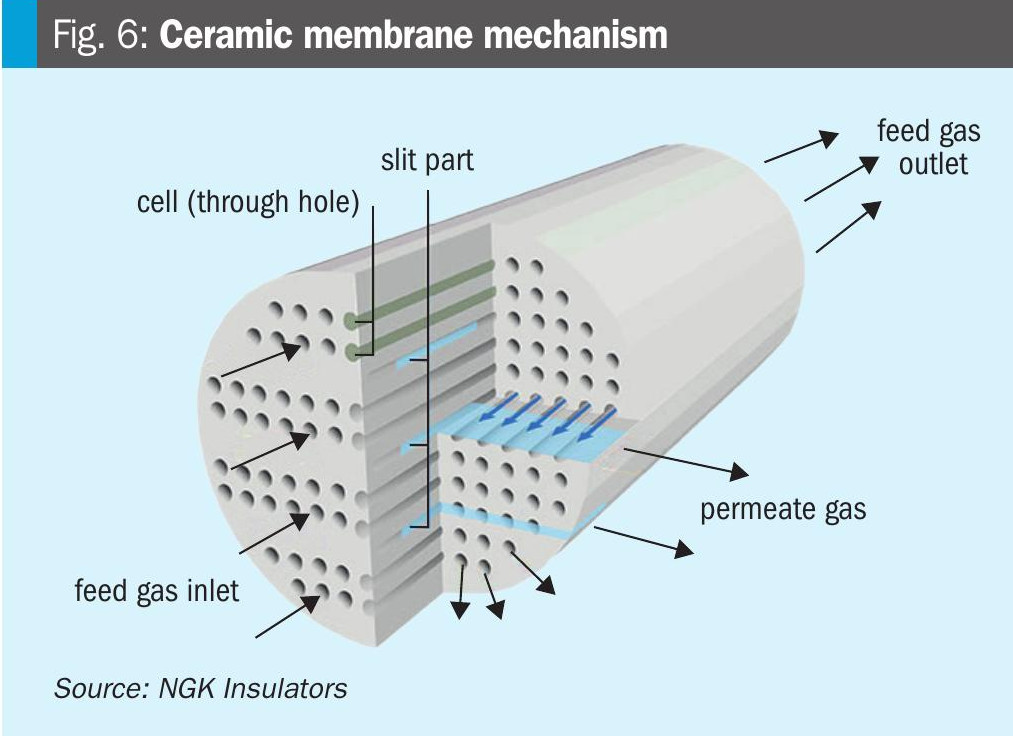
Key advantages of hydrogen purification with ceramic membranes are:
- Reduced opex: Compared to the pressure swing adsorption (PSA) method commonly used in the industry, MHI’s membrane separation approach offers a substantial reduction in operational expenditure (opex). This is achieved through lower energy consumption and reduced maintenance requirements.
- High hydrogen recovery rate: The ceramic membrane will achieve about 10% higher hydrogen recovery rate than PSA (95% vs 85%). This minimises the loss of valuable hydrogen and reduces the consumption of raw material ammonia, as a result contributing to lower operating costs. Hydrogen purity for HyMACS™ membrane separation is >99.0% compared to 99.97% for PSA.
- Versatility: Membrane separation technology is compatible with various cracking methods, including steam heating, fired heating, and autothermal systems. This flexibility allows for seamless integration into different ammonia cracking configurations.
MHI’s development of this advanced hydrogen purification process underscores its commitment to innovation and efficiency in ammonia cracking technology. By leveraging the advantages of ceramic membrane separation, MHI offers a cost-effective and environmentally friendly solution for hydrogen production.
Applications of HyMACS™
MHI’s HyMACS™ ammonia cracking system is a versatile solution with broad applicability across various sectors, including:
- Industrial plants: Integration into existing industrial processes, such as chemical production, steelmaking, and refining, to provide a reliable and costeffective source of on-site hydrogen.
- Hydrogen stations: Supplying high-purity hydrogen for fuelling fuel cell vehicles, contributing to the development of a sustainable hydrogen infrastructure.
- Power generation: Integration with gas turbines offering a clean and efficient alternative to fossil fuels.
Fig. 7 shows the clean ammonia-hydrogen supply chain. With its experience, MHI Group can offer clean ammonia production, ammonia shipping transportation, ammonia cracking, hydrogen power plants, hydrogen green steel plants, as well chemical plants.
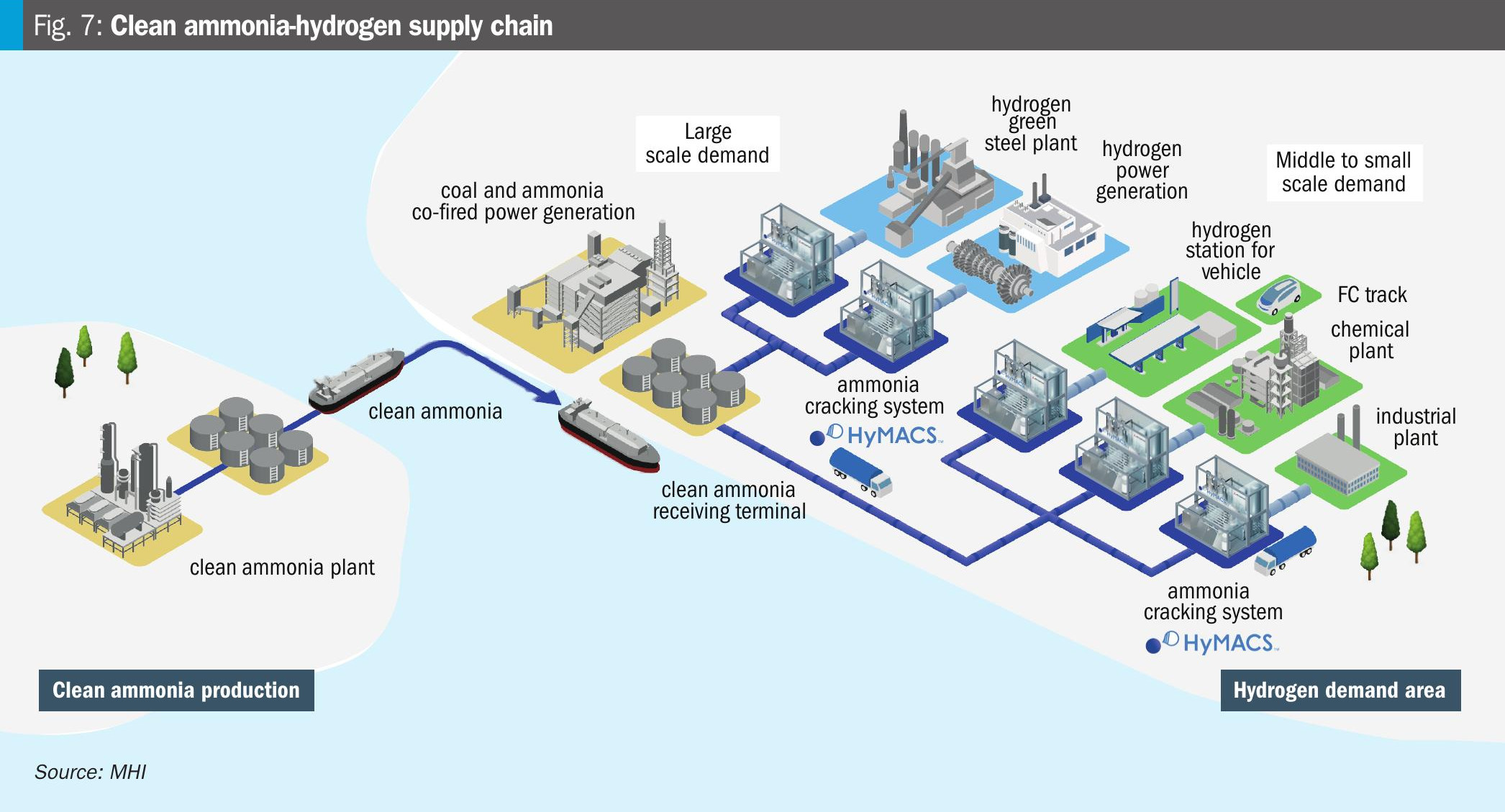
In this clean ammonia-hydrogen chain, ammonia is received from the blue or green ammonia plant and delivered to the primary consumer, especially in Japan, the coal and ammonia co-fired power generation facility. From there, ammonia will be delivered to sub-users, such as ammonia cracking devices capable of producing product hydrogen for end customers. The hydrogen supply chain aims to initially meet medium to small-scale hydrogen demands from consumers ranging from chemical plants, small hydrogen boilers or furnaces and hydrogen stations for vehicles before catering to large-scale hydrogen power generation demands.
HyMACS™ utilises exhaust heat from current combustion devices, including steam or flue gas, for the cracking procedure. This greatly lowers energy usage and operational expenses in comparison to systems that depend on combustion heat.
As shown in Fig. 8, steam or flue gas for the cracking process can be sourced from external facilities like coal and ammonia co-fired boilers, ammonia direct combustion gas turbine, among others. Accordingly, product hydrogen can be supplied or exported to meet the demand of external hydrogen users. Meanwhile, product hydrogen can also be utilised within the system or plant and the steam or flue gas generated can be reused as a heat source for ammonia cracking.
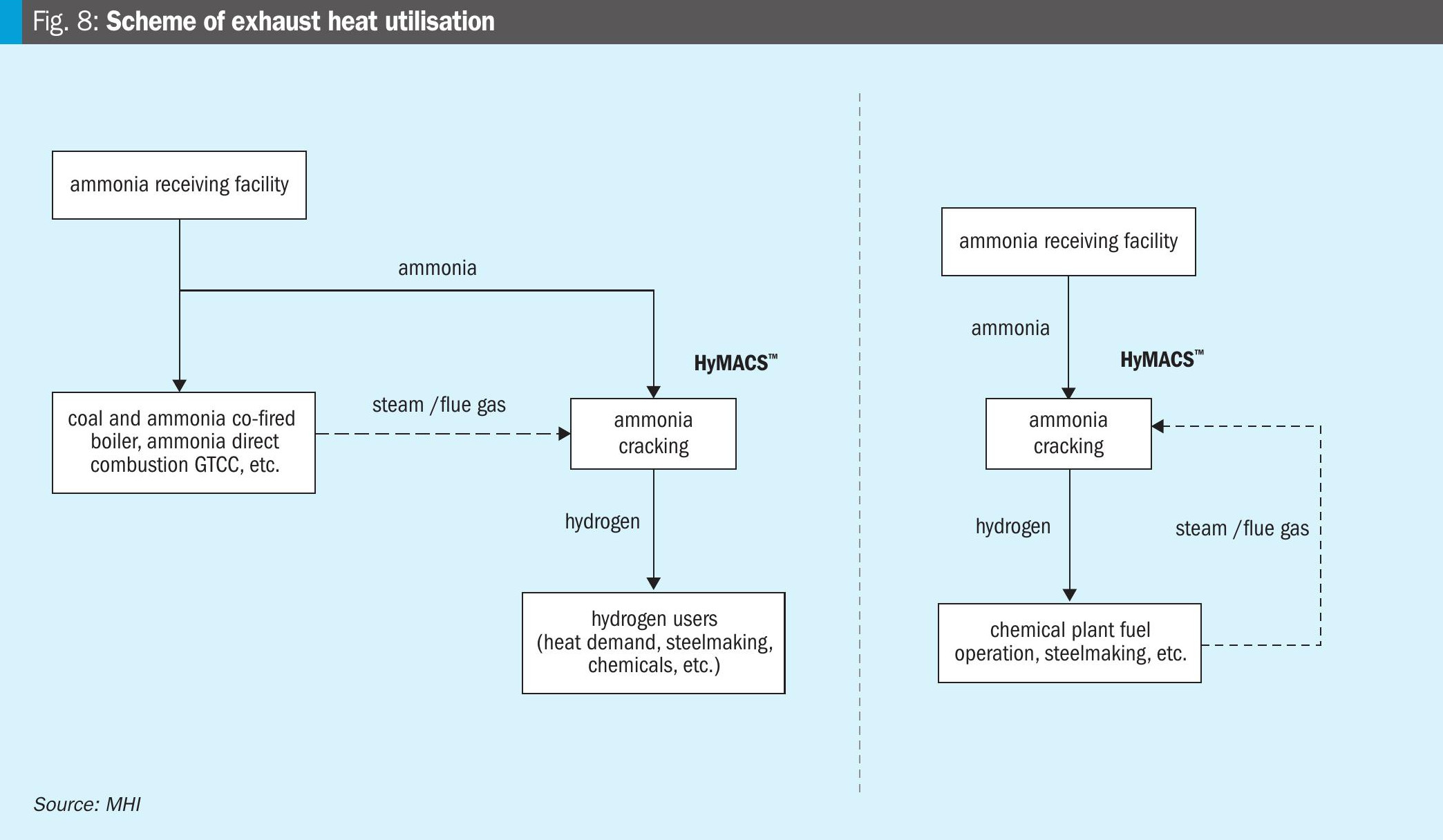
Current status of development
Development roadmap for HyMACS™
MHI initiated the development of its ammonia cracking technology in 2017. Laboratory tests for verifying equipment components were successfully completed in 2023. A pilot test is scheduled for completion by the end of FY 2025 at MHI’s research laboratory to establish fundamental technologies. After the pilot test, a demonstration test will be conducted to validate the performance and durability on an actual scale, with the first commercial unit expected to be delivered in FY 2028. The development roadmap encompasses scaling up the unit size and comprehensively verifying the performance and durability of the entire system.
Summary
MHI is drawing upon its extensive experience in the design and construction of numerous ammonia plants to develop a low-temperature ammonia cracking system utilising non-precious metal catalysts. The low reaction temperature enables the efficient utilisation of exhaust heat (steam or flue gas) and significantly mitigates the risk of nitriding. Non-fired reactors are particularly well-suited for small to medium hydrogen demand applications and hydrogen purification using ceramic membranes can contribute to substantial savings in ammonia consumption.
MHI is currently preparing to conduct a pilot test, followed by a demonstration test, to validate the technology’s performance and readiness for commercial deployment.
References