Sulphur 418 May-Jun 2025
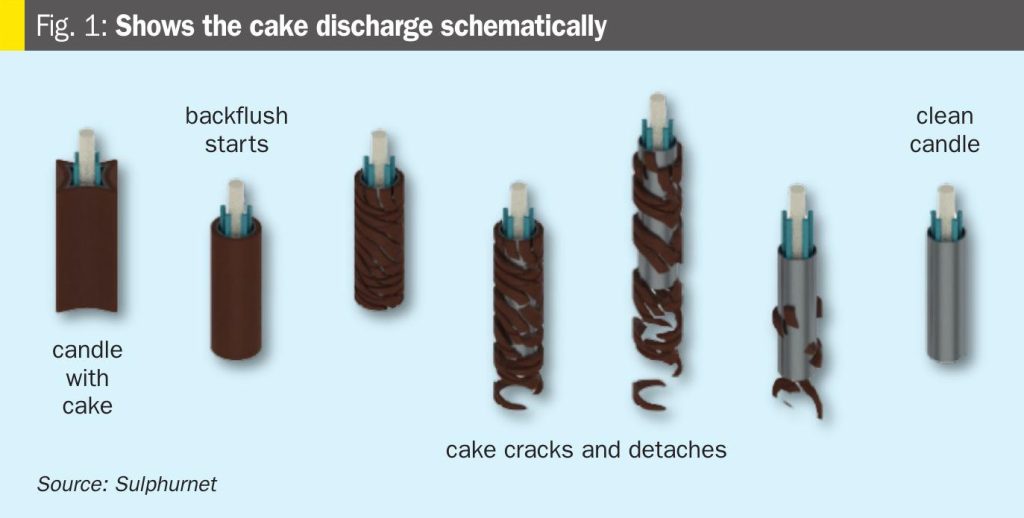
1 May 2025
Next generation filtration for liquid sulphur
LIQUID SULPHUR FILTRATION
Next generation filtration for liquid sulphur
The Self-Cleaning Liquid Sulphur Candle Filter (LSCF) is setting a new benchmark in liquid sulphur filtration. With its innovative candle arrangement and advanced back-flushing technology, it enhances filtration rates significantly and minimises downtime for cake discharge. Jan Hermans of Sulphurnet explores the LSCF design, process parameters, and operational advantages.
In recent years, Sulphurnet has introduced the Self-Cleaning Liquid Sulphur Candle Filter (LSCF), a modern alternative to overcome the limitations of traditional pressure leaf filters. This new technology employs candle elements with an automatic system for filling and cleaning which minimises manual intervention, which improves efficiency, operational reliability, costs, and safety standards.
A historical overview of sulphur filtration
In 1942 E.I. Dupont patented the first self-cleaning candle filter. This filter included vertical candles, and the application of precoat material to facilitate the filter cake discharge.
A decade later, researchers J.R. Donavan and B.J. Barnett from Monsanto Chemical Co., presented a publication on the flowrates and filtration efficiencies of the pressure leaf filter versus the carbon tube filter.
Although the filtration efficiency of the later prevailed, the market leaned towards pressure leaf filter technology, mainly because of its capacity, and it has been the standard for decades ever since.
Nevertheless, pressure leaf filters come with their own share of disadvantages: They need to be cleaned in open position by operators that come in contact with hot vapours and high temperature filter cake; they also present a high risk of fires due to the presence of FeS in the filter cake; and the operation process overall is not an easy or straightforward task.
Fast forward to today, with more stringent industrial standards for Health, Safety, and Environmental regulations, the low availability of labour and process downtime are becoming increasingly important factors in decision-making when choosing an industrial filter, influencing business operations across all industries.
Nowadays, due to its high labour involvement and safety matters, the pressure leaf filter is no longer an ideal solution for in sulphur filtration. The low level of automation, operational costs and efficiency issues have opened the path for alternatives like the ones developed by Sulphurnet.
The Self-Cleaning Liquid Sulphur Filter (LSCF) is a direct response to the modern-day challenges. It has been designed to enhance operational efficiency, reduce downtime, and meet stringent health, safety, and environmental standards, specifically for sulphur filtration applications.
Understanding the filtration mechanisms
The LSCF is a pressure filter which employs vertical hanging candles in a vertical positioned tank with a cone bottom, for dry cake discharge. The filter candles are made of stainless steel, covered with filter media suitable for the extreme process conditions.
The general process steps of the LSCF can be summarised as follows:
Filling: The pressure vessel of the filter with the candles inside is filled with clean liquid sulphur after which the precoating process is started.
Precoating: To obtain a good efficiency in sulphur filtration, the application of filter aids is essential. The type and grade of the precoat material is responsible for the filtration performance as well as the flow rates (pressure drop).
Fine grade filter aids, (low Darcy number) give a high efficiency in filtration, but also a high pressure drop and lower flowrates. Course filter aids, (high Darcy Number) give a lower efficiency with high flow rates and low pressure drops. It is always of importance to make the right selection to obtain good contaminant removal efficiency.
Adding the precoat layer provides two filtration principles, which are similar for both the candle type or pressure leaf filter.
Particle removal occurs either by means of surface filtration (used for cake filtration) or depth filtration (the precoating layer). The filter medium retains particles in two principal ways: When the particles are predominantly larger than the size of the filter medium pores, solids are deposited on the up-stream side of the thin filter medium during what is referred to as surface filtration.
Sulphurnet’s recommendation is the application of cellulose filter aids. They have a lower consumption in comparison with mineral filter aids. And at the same time, due to the fibrous structure, rough surface, and large porosity, higher flow rates and longer cycle times can often be obtained. In the case of the pressure leaf filter, easier cake discharge helps reduce manual cleaning which leads to longer lifetime of the filter leaves and the filter in general. And last but not least, the lack of harmful crystalline components also reduces health hazards.
Filtration: The liquid sulphur passes the filter cloth from the outside to the inside of the support candle. Liquid sulphur flows downwards to the bottom of the candle into the centre tube. The filtrate flows up into the horizontal register and out of the pressure vessel through the filter outlets. The centre tube is essential for effective candle drainage and optional drying of the cake.
Cake extraction-drying: During the pumping out of the heel volume from the filter vessel and the drying phase, steam is forced through the filter cake in the direction of the filtration towards the inside of the filter element. At the same time, the central tube guarantees that the cake on the filter element is extracted and that the remaining sulphur in the filter element is displaced by the steam leaving the minimum of sulphur. The extraction can be improved by executing these steps per individual manifold.
Cake discharge: After emptying the filter vessel, and possible cake extraction, each filter manifold is subjected to a reverse gas flow pressure shock. As the filter medium expands, vertical cracks are generated in the cake. When the medium reaches its maximum deflection, its movement stops, and the cake is thrown off. This backflushing is done per manifold/register, so the filter cake is completely dislodged from the candle. The cake drops downwards into the conical section of the pressure vessel and can be discharged (see Fig. 1).
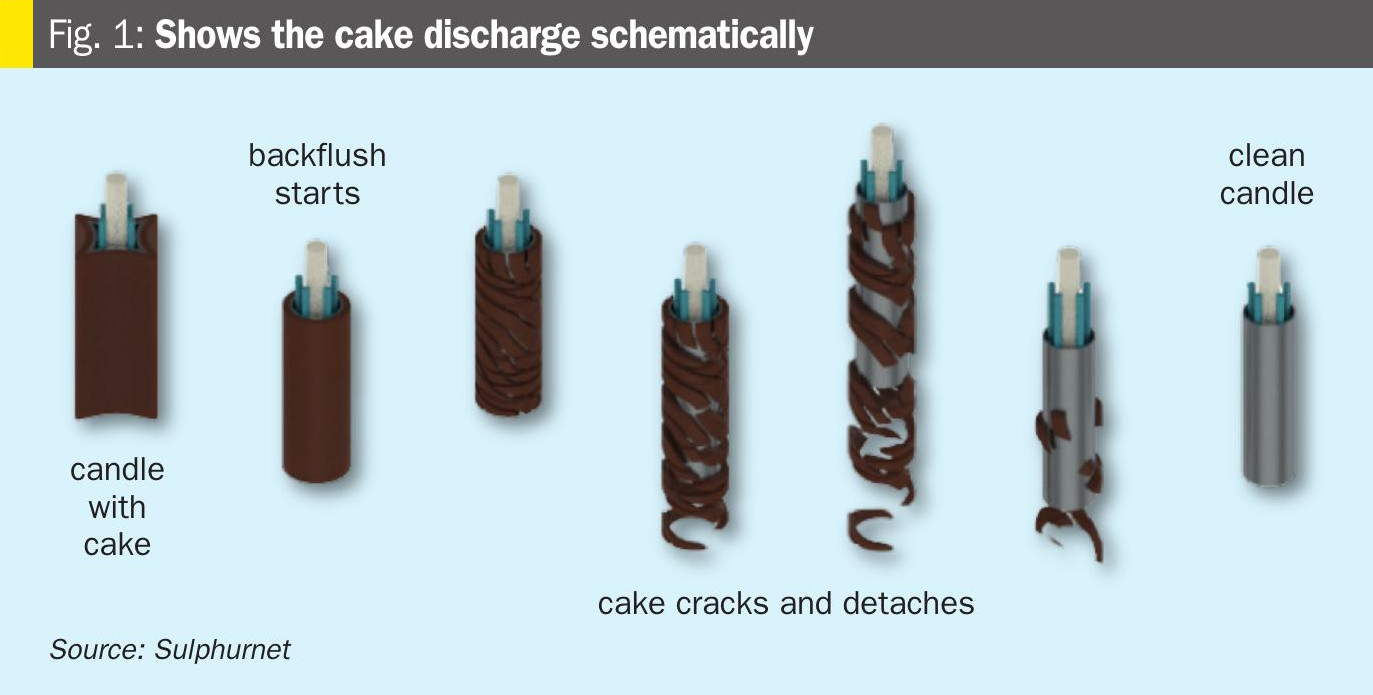
Superior filter media design
The filter medium used in this application is suitable for the elevated temperature as well as the high-pressure backflush. The combination of multifilament and monofilament fibres provides a balance between strength and efficient cake discharge, which is crucial for maintaining operational efficiency. The cylindrical weave is the multifilament that adds durability and structural integrity, while the monofilament in vertical orientation improves the removal of filter cake.
The lifespan of the filter medium is more than ten months in operation without needing replacement. It is a reliable and long-lasting solution for sulphur filtration under tough conditions.
Automation and process control
The biggest advantage is the possible automation of such a system. By adding functional process instrumentation and automated valves, the complete procedure from filling to cleaning can be fully automated, providing the following benefits:
• reliable, controllable, and reproducible process;
• semi- or fully automatic operation; real time monitoring (MMI);
• data logging of level and pressure changes;
• reduced operator workload.
Advantages over standard pressure leaf filters
Compared to standard pressure leaf type filters, the LSCF offers the performance and operational advantages:
Superior cake discharge: With its back-flush system that cleans the filter cloth and dislodges the cake in a single step, the LSCF improves cake removal efficiency and drastically reduces the manual cleaning stage. No high-maintenance nozzles are needed for discharge, reducing failure and maintenance downtime.
Enhanced filter cloth performance: The cylindrical seamless cloth design ensures longer cloth life and delivers more consistent filtration performance overtime.
Higher filtration efficiency: The LSCF achieves higher filtration rates and shorter cycle times thanks to its compact vertical layout and efficient cleaning mechanism.
Simplified filter maintenance and automation:
• no moving parts except for the filter cloth;
• no nozzles or mechanical scrappers needed;
• fully enclosed system improving operator safety;
• real time process monitoring;
• reliable cake removal.
This flexibility enables integration into a wide range of plant setups with minimal re-engineering.
Conclusion
In a modern industry landscape where process efficiency, safety and automation are more critical than ever, the Self-Cleaning Liquid Sulphur Candle Filter marks a significant advancement. With features that deliver a higher filtration efficiency, minimal maintenance and fully automated operation, this filter redefines the best practices for liquid sulphur purification.
For producers in the sulphuric acid industry looking to upgrade and automate their systems, the technology presents a compelling modern solution.