Sulphur 409 Nov-Dec 2023
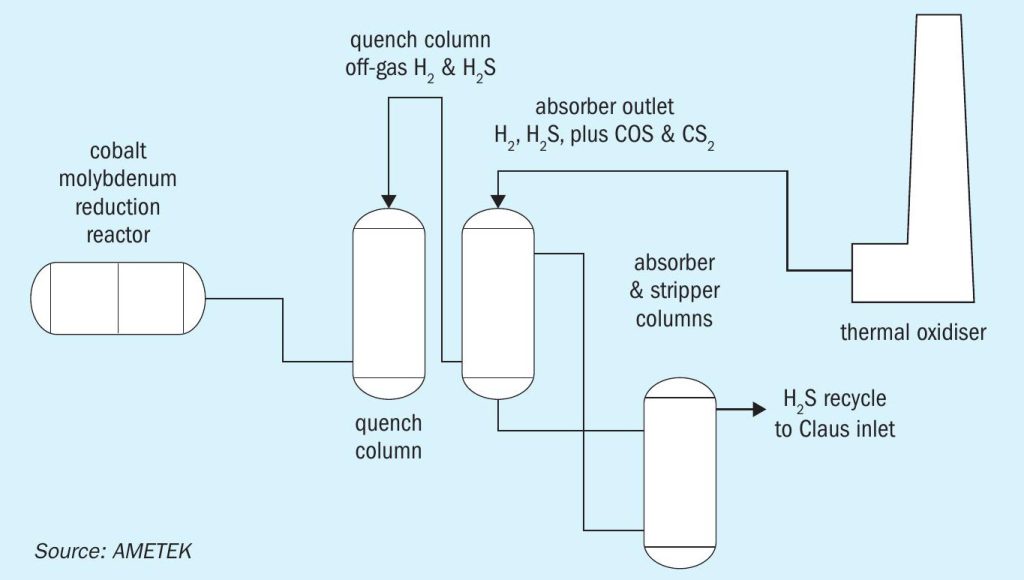
30 November 2023
Next generation sulphur plant analysers
INSTRUMENTATION AND CONTROL
Next generation sulphur plant analysers
As plants move towards full unit control, Jochen Geiger of Ametek Process Instruments provides an overview of how the latest sulphur plant analysers are providing greater insight into sulphur plant operations.
When looking at process optimisation, besides process control itself, it is important to consider new developments. To improve process yield we may look for new equipment and consider different process control mechanisms, but what about mitigating upset conditions? The results from installed process instrumentation is often questioned whenever there are any unexpected process conditions. Previous publications have discussed this in detail, but what can we learn from those discussions?
First, it is important to analyse the root cause for the lack of trust (if it exists) in the results shown by the process analytical equipment, which can be misinterpreted. As with all electronic equipment, the development of new features is happening at a rapid rate. For example, with regard to process analysers, improvements in data transmission have been introduced in recent years.
In the past, with the exception of process gas chromatographs, process analysers were mostly designed to analyse one component. Today, however, a wide range of multi component instruments are available, but despite being known to the instrumentation department, the process control team often sticks to its usual program.
For example, one very common application in the sulphur recovery industry is the measurement of excess hydrogen at the quench tower outlet in an amine-based tail gas treatment unit (TGTU). A basic flowsheet of a TGTU is shown in Fig. 1.
In the first SCOT units (Shell Claus Off Gas Treatment units) there was a single component measurement for hydrogen.
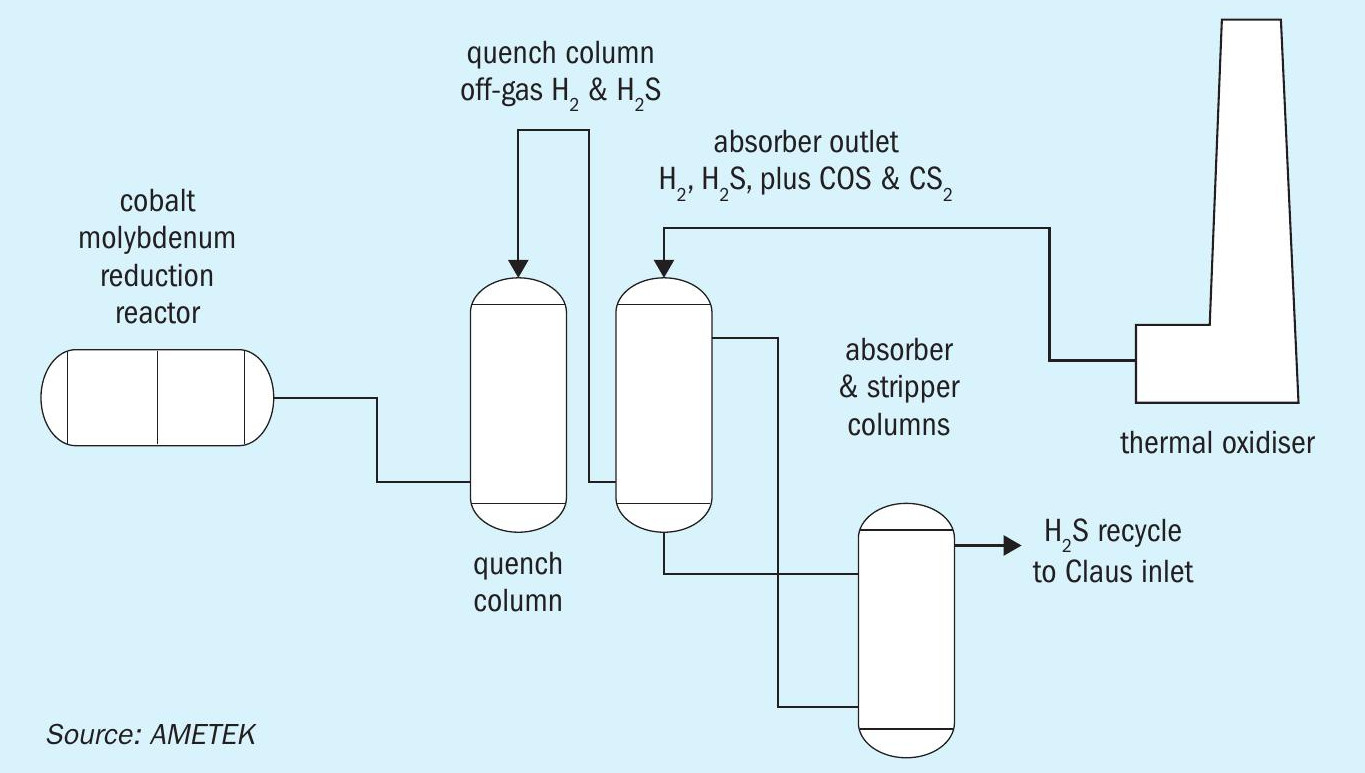
Today, however, in several installations Ametek has found two measurement locations in a TGTU process. Besides the quench tower outlet, there is a sample point at the amine absorber outlet, where hydrogen sulphide (H2 S) can be measured to ensure that the concentration does not exceed the limits. Looking into the process chemistry shows that at both sample points other components can be of interest as well. For example, at the quench outlet, besides the hydrogen measurement, H2 S is also a component of interest. Downstream of the absorber outlet additional components to consider are hydrogen for redundancy, plus carbonyl sulphide (COS) and carbon disulphide (CS2 ). Both sulphur components will provide information about the reaction of the cobalt-molybdenum catalyst in the reactor.
Nowadays, modern process analysers are able to make these measurements simultaneously with one instrument. This is essential to achieve further process optimisation. Gaining more information about the process, if used correctly, will help to better understand “upset conditions” which in turn will help to mitigate them in the future.
The instruments need to be easy to operate, simple to connect with the process and provide readings to the process control team in a timely and reliable manner.
Process gas chromatographs (PGC) are still widely used today for applications which require multicomponent analysis. However, PGCs require a lot of maintenance and are considered as “complex” plus, depending on the application, require several utilities.
Alternatives are available and now this measurement tool has been brought to a modern process analyser platform. Most sulphur reaction gases are strongly absorbed in the ultraviolet area of the light spectra (Fig. 2).
What makes analysis in the UV range of the absorbance spectra so unique is that no water and no hydrocarbons are absorbed there, making sample preparation simpler and safer. There is no need for a chiller or any other method of sample preparation. Water is a strong absorber all over the infrared spectra and the same applies for the hydrocarbons. For the TGTU, one remaining concern is the measurement of hydrogen, which does not absorb in the usable infrared or ultraviolet spectra. For this reason, a multi sensor technology is used. The new process analyser platform can incorporate different measurement technologies: ultraviolet for sulphur species, infrared for hydrocarbons plus CO/CO2 and a thermal conductivity detector for the hydrogen.
Fig. 3 shows an instrument that incorporates all of these measurements. The modular design makes customised solutions possible. The electronics are located on the left with the sample measurement enclosure on the right and the sample handling part below. All components are easily accessible.
With decades of experience measuring sulphur components in gas, gas processing and refinery process streams, Ametek focused on developing the 993X with features requested from Model 93X end users and maintenance teams. Standard features include a 7-inch, colour touch screen display, Modbus TCP and Modbus RTU support, at least four isolated and self-powered analogue outputs, and a longer lamp life.
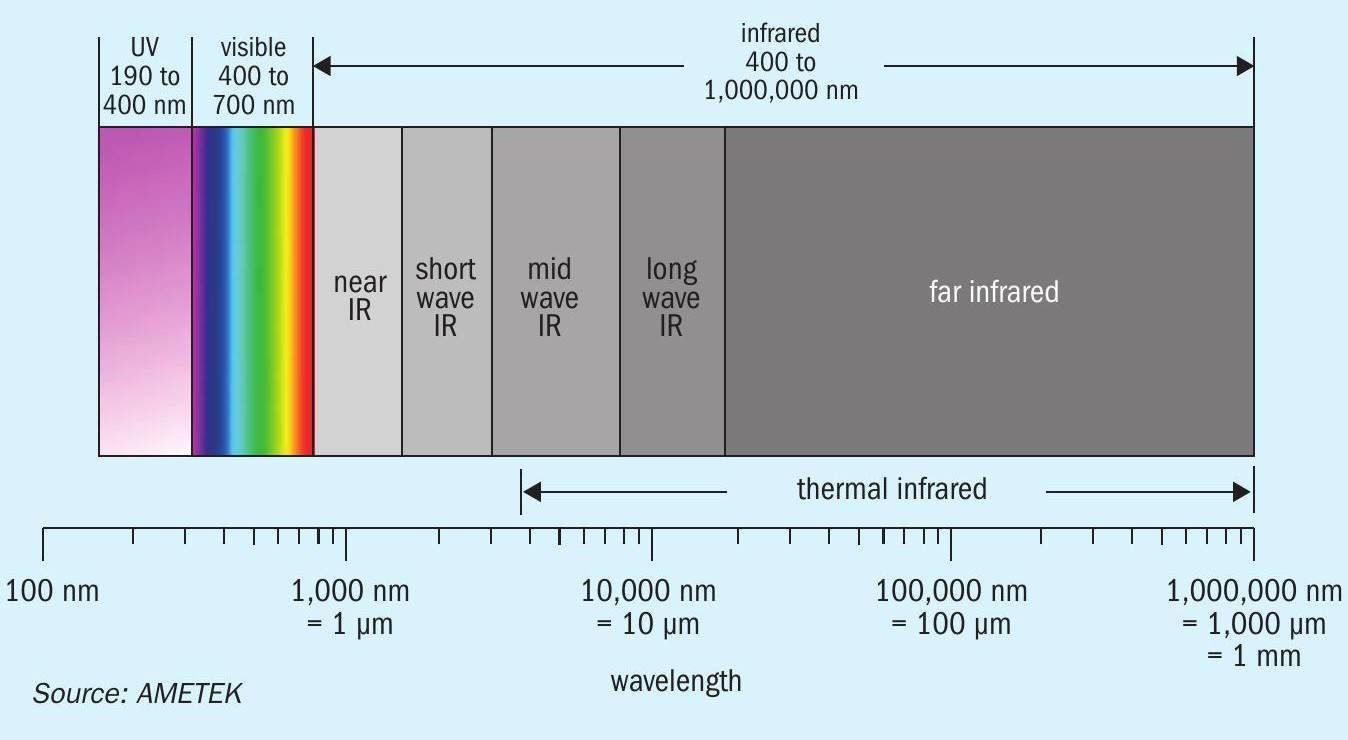
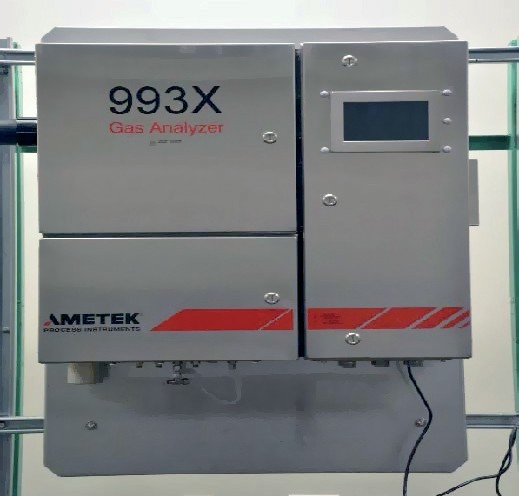
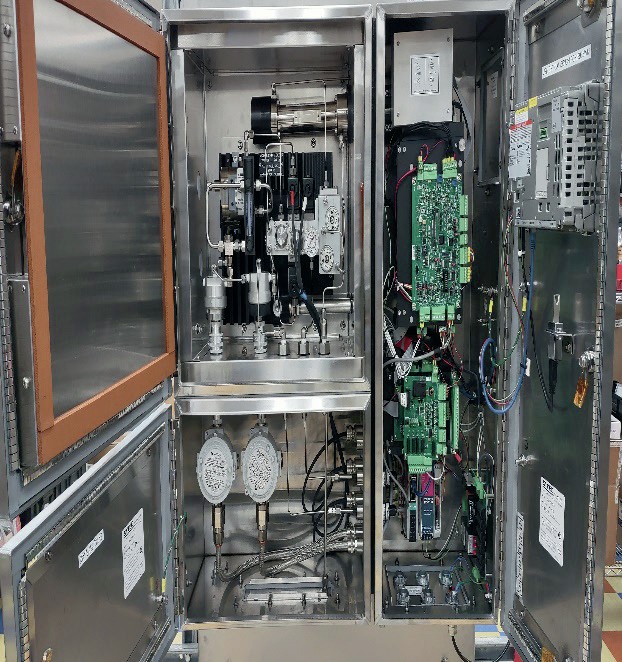
With its rugged design the instrument can be use in a wide range of ambient air temperatures from -20°C to 50°C (-4°F to 122°F), which leads to a lower installation cost.
An Ethernet port is a new standard on modern process instruments, allowing remote service diagnostics, which helps to reduce onsite service activities.
This latest model now completes the series of sulphur plant control analysers.
When selecting or installing a process analyser it is important to consider how to get a representative sample from the process to the instrument as well as sample disposal arrangements. Other important considerations with regard to any process gas analysis in sulphur recovery plants is whether the instrument is safe to work with and whether the overall design includes enough flexibility to allow the instrument to work over a wide range of operating conditions. A fully functioning instrument is required during upset conditions.
The automated process control has isolated and self-power analogue outputs which enables monitoring of relevant components within the required control range.
For monitoring “upset conditions” there are digital outputs such as MODBUS. All process analysers have the capability to monitor “over range” readings by a factor of two to three outside the calibrated range. This is important to keep an eye on the process during upset conditions.
For instrument reliability an Ethernet connection is important to allow the instrument to be checked remotely.
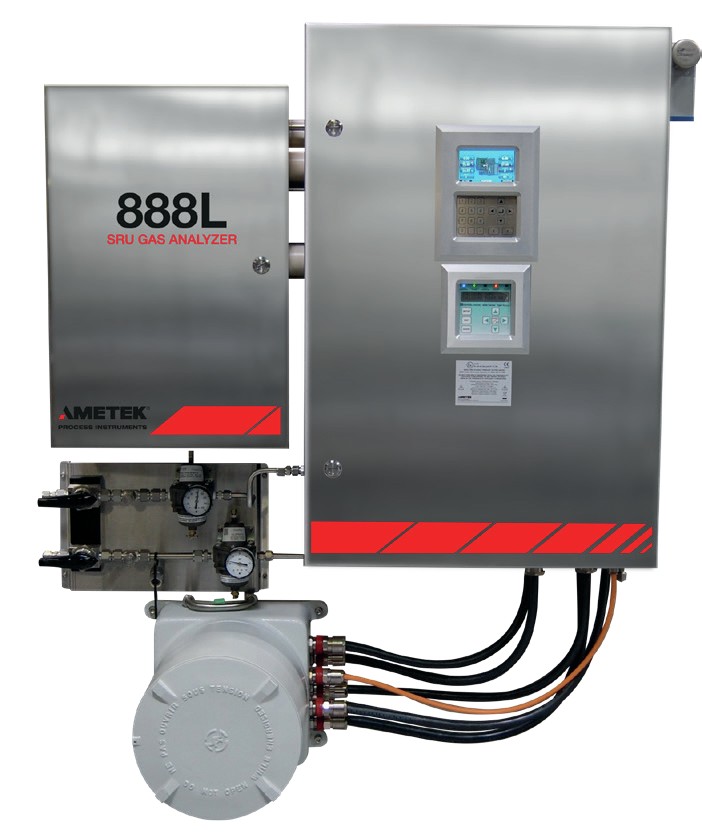
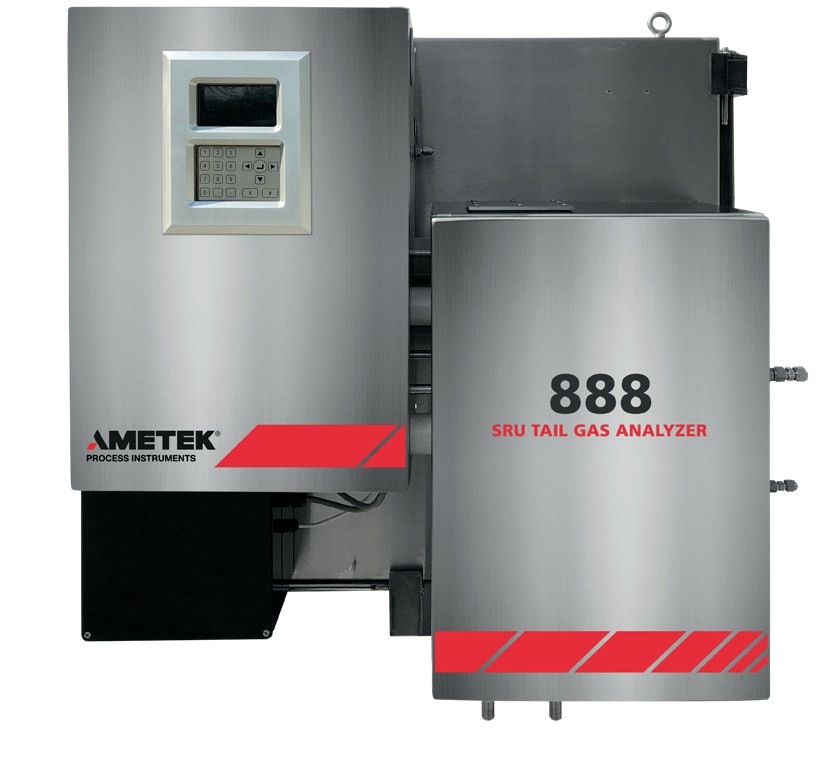
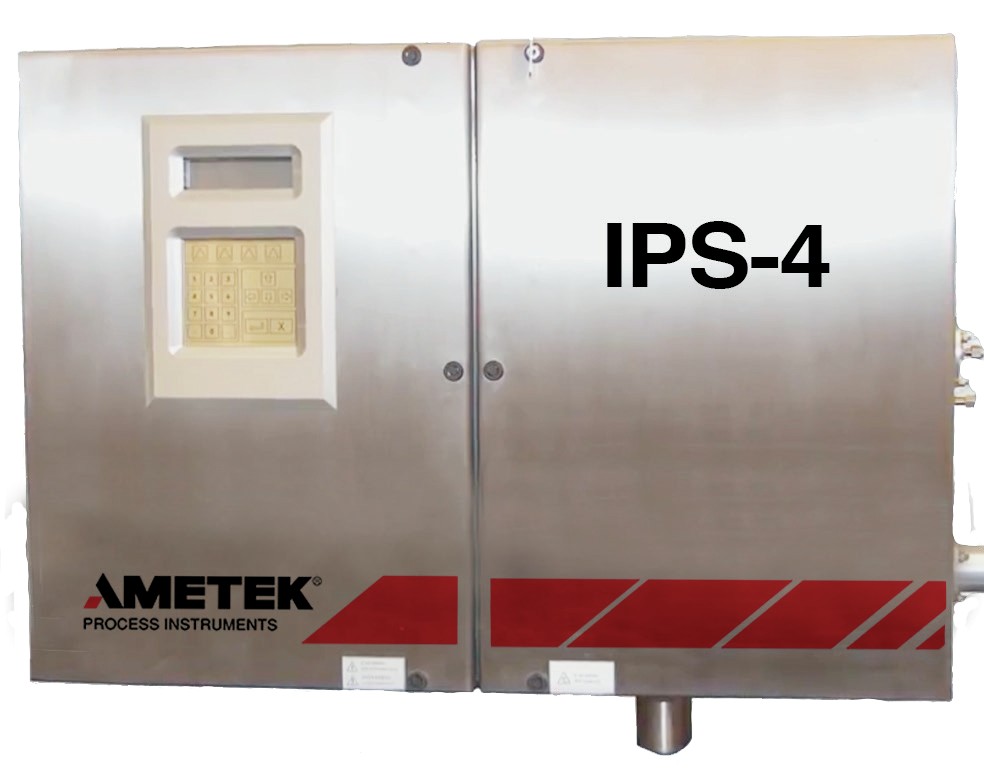
Instrument implementation
Today, modern SRUs can range in capacity from tens to thousands of tonnes per day of sulphur production. Over the decades, significant improvements have been made to the overall recovery efficiency. While it was sufficient to operate at 80 to 85% in the 1970s and between 95 and 99% in the 1990s, today it has become standard to operate at recovery efficiency rates of 99.9 +%.
Considering that we, more or less, rely on the same chemistry that has been used for over 90 years, with the exception of tail gas clean up units, such efficiency improvements were only possible by using reliable process instrumentation.
It is important to understand the potential impact on the process control scheme for each of the measurements provided by the instrument installed. What are the alternative measurement scenarios, what would be “nice to have” and what is actually required to achieve the emissions targets from the sulphur recovery unit? Keeping in mind that too much information potentially leads to confusion.
The challenges are:
- understanding the environmental impact for each instrument;
- finding the best instrument combination to gain the best improvement;
- keeping the instruments in operating condition;
- mitigating upset conditions by understanding “unexpected” instrument behaviour.
Instruments are required to react fast to process changes, work reliably over the time required and maintain the highest possible safety standards.
Another topic of discussion these days is process optimisation to keep emissions at a low level plus reducing energy consumption. A common sulphur plant process configuration consists of a modified Claus process with a downstream amine-based tail gas treatment process to provide an overall sulphur recovery efficiency of 99.98+% and assuring low sulphur dioxide (SO2 ) emissions. Instrumentation can be installed to make further improvements. For example, in the modified Claus process the existing air demand analyser can be used with a feed gas control system based on a feed gas analyser system. Depending on the SRU train setup this type of control scheme will help to optimise the overall sulphur recovery performance. In plants with an amine-based tail gas treating unit it will help to reduce upset conditions. In an extreme situation the information provided by the feed gas system can help to protect the amine absorber from SO2 breakthrough, keeping in mind that the TGTU will not be significantly impacted when the hydrocarbons are appearing. In fact, an increase of hydrocarbons in the feed gas will lead to an air deficiency situation and the H2 S concentration in the tail gas will increase. So, less conversion of other sulphur compounds to H2 S means less work for the TGTU. Unfortunately, hydrocarbons can disappear as fast as they appear. No-one is able to forecast when a process upset starts or when it ends. As an upset is identified, the control system will manage the air flow to the reaction furnace, getting everything to the required set points for optimal operation. However, when the upset ends, the hydrocarbons disappear, leaving a situation where too much air is supplied to the reactor furnace and the SO2 concentration in the tail gas will be too high. How high, nobody can predict! So now the system and operators are asking themselves: “Do I have enough hydrogen available to hydrolyse the SO2 into H2 S? “
This leads to the question of how to ensure that the plant control is based on correct information? In many other cases it is standard for important components to be designed in a redundant manner. Unfortunately, this has not been the case for operating TGTUs. There are units with a single excess hydrogen measurement at the quench tower outlet. Now with the appearance of multi sensor process instruments it is becoming easier to “convince” operators to consider redundancy for the hydrogen measurement.
The new standard for TGTU instrumentation is to measure hydrogen plus H2 S at the quench tower outlet as well as hydrogen plus COS and CS2 at the amine absorber outlet.
Conclusion
Modern process instrumentation has the potential to help reduce the emissions from a sulphur recovery unit. The initial investment is not negligible, but it is a highly challenging application with regard to measurement reliability and safety – the SRU has the most toxic gas mixtures of the entire refinery. The average lifetime of an instrument in a sulphur plant is 15 to 20 years.
Knowledge, understanding and awareness training are essential to maintain the instruments, and without the instruments the emission targets are not achievable. It is important that different technical disciplines work together, starting at the design phase of the processing unit. Misunderstandings about pipping can result in unsafe installations. Choosing the “wrong” instrument may result in not achieving the best possible process performance.