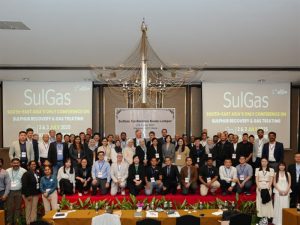
SulGas® Kuala Lumpur 2025 – First Edition of South-East Asia’s Only Sulphur Recovery & Gas Treating Conference
SulGas® KL 2025 - 17 speakers, dedicated exhibition area, panel discussions...
SulGas® KL 2025 - 17 speakers, dedicated exhibition area, panel discussions...
MEScon 2025 took place in Abu Dhabi from 19-22 May 2025, providing delegates with renewed energy, new connections, and fresh ideas to apply across the sulphur value chain.
AMETEK Process Instruments has collaborated with Worley Comprimo, part of Worley’s Technology Solutions, to provide sulphur recovery unit (SRU) stakeholders with critical analytical measurements combined with advanced burner control technology to deliver enhanced automated air control management. The companies say that their 2ACT™ Solution is a fully automated system that minimises SRU upsets, enhances reliability, and delivers strong returns on investment. At the heart of this partnership, the innovative 2ACT™ Solution offers an all-in-one approach to advanced air control – significantly boosting SRU performance and efficiency while reducing operational costs. 2ACT uses AMETEK’s IPS-4 ultraviolet and infrared analyser to measure H2 S, CO2 , NH3 , H2 O and total hydrocarbons (THCs) by continuously sampling the acid gas upstream of the SRU. The change in air demand requirement is then calculated, with main and trim air adjustments implemented automatically by the feed forward control scheme designed by Worley Comprimo. The companies say that the benefits of the 2ACT Solution include maintaining an optimal H2S to SO2 ratio at the outlet of the Claus Plant to maximise recovery efficiency, mitigating damage to tail gas treatment unit (TGTU) components, lowering SO2 emissions and carbon footprint with improved uptime and plant throughput.
S&P has raised its 10-year production outlook for the Canadian oil sands. The latest forecast expects oil sands production to reach a record annual average production of 3.5 million bbl/d in 2025 (5% higher than 2024) and exceed 3.9 million bbl/d by 2030; half a million barrels per day higher than 2024. The 2030 projection is 100,000 bbl/d (or nearly 3%) higher than the previous outlook. Despite a lower oil price environment, the analysis attributes the increased projection to favourable economics, as producers continue to focus on maximising existing assets through investments in optimisation and efficiency. While large up-front, out-of-pocket expenditures over multiple years are required to bring online new oil sands projects, once completed, projects enjoy relatively low breakeven prices.
Samsung E&A has announced the termination of its $1.6 billion contract with the Mexican state-owned oil company PEMEX for a sulphur recovery facility project. Samsung says that the contract, originally signed nearly a decade ago, has faced significant delays and suspensions due to budget cuts imposed by the client. It concerns a hydrodesulphurisation (HDS) facility aimed at removing sulphur components from diesel fuel at the Salamanca refinery in Guanajuato state, central Mexico. In a statement, Samsung E&A confirmed that they have reached an amicable agreement regarding the contract termination, stating, “We have been fully compensated for the expenses incurred during the project suspension, and since this project was not included in our sales or operating profit forecasts for this year, there will be no financial loss due to the contract termination.”
The Middle East remains the world’s largest regional exporter of sulphur, with additional capacity continuing to come from both refineries and particularly sour gas processing.
Kazakh state gas company QazaqGaz says that work is progressing well and on schedule on the 1 billion m3 expansion project at the Kashagan Gas Processing Plant. A recent site report says that seven absorption columns have been installed at the sulphur treatment unit (each weighing between 50-170 tonnes); three sections of the smokestack have been installed at the sulphur recovery block, along with storage tanks and pumps for the heat carrier, instrumentation air, and nitrogen supply units; and a total of 2,177 t of process equipment has been installed. Welding works for tank assembly are ongoing, and over 12,000 meters of underground piping have been laid, and more than 38,000 cubic meters of concrete have been poured.
Astron Energy, a subsidiary of Glencore, says that it will spend $328 million to upgrade its South African crude oil refinery in order to comply with the country’s upcoming cleaner fuel regulations. The investment aims to bring the facility in line with South Africa’s Clean Fuels II standards, which mandate lower sulphur content in both petrol and diesel. The 100,000 bbl/d refinery near Cape Town is one of only two remaining operational refineries in the country. Astron says that construction work is already under way for a gasoline hydrotreating plant that will reduce sulphur levels to Euro 5 (<10ppm sulphur) specifications. The regulations have been delayed to July 2027 due to concerns over the cost of upgrading existing refining infrastructure. n
Together with Slovnaft, Worley Comprimo has developed a near real-time monitoring dashboard using data sharing via the Cloud. Using a two-year data set containing minute average data, trends and insights were used to optimise performance. This paper describes the main learnings and improvements with respect to energy optimisation, which supports sustainability targets for Slovnaft.
The Middle East’s premier event for the sulphur global industry, MEScon 2025, returns to the Conrad Abu Dhabi, Etihad Towers from 19 to 22 May 2025.