Nitrogen+Syngas 371 May-Jun 2021
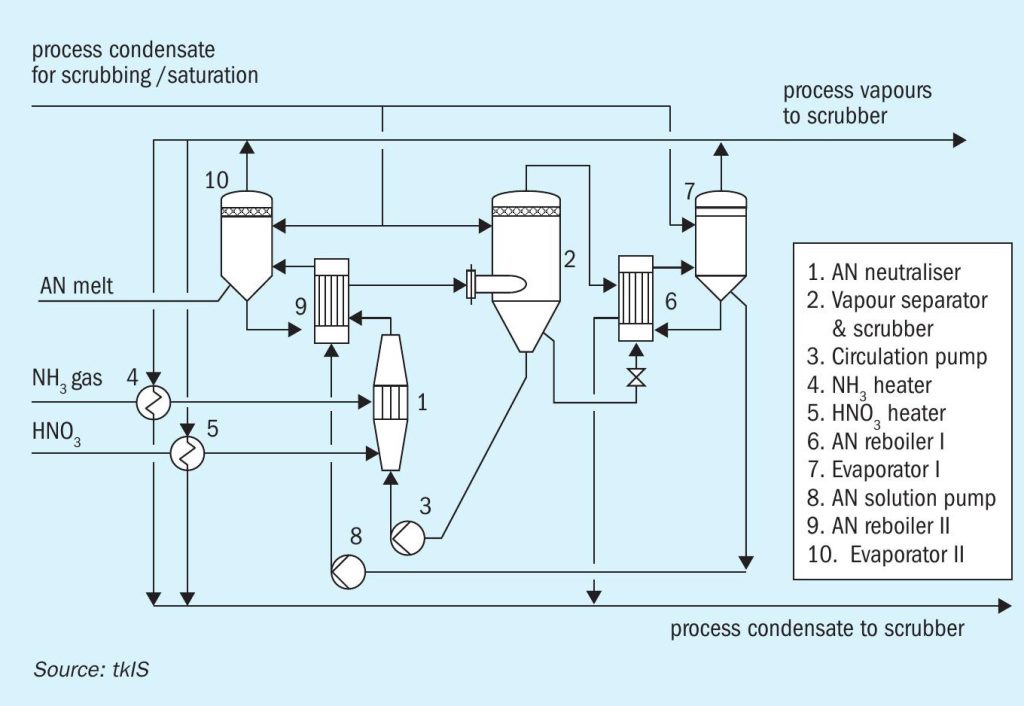
31 May 2021
The green and safe way to produce ammonium nitrate
AMMONIUM NITRATE
The green and safe way to produce ammonium nitrate
In August 2020 the tragic explosion of ammonium nitrate fertilizer in the port of Beirut caused many fatalities and injuries. This was a wake-up call for the entire industry to review the design of plants and storage facilities, as well as the procedures for plant operation and the handling of products. The key factor for safe new installations is the process design: the right choice of unit operations, operating temperatures and pressures, the control of process variables and the design of key items of equipment. A modern ammonium nitrate (AN) plant design not only mitigates the environmental impact, but also reduces investment costs and contributes to the key factors mentioned. M. Pieper and P. Kamermann of thyssenkrupp Industrial Solutions discuss how, by using the right design, safety in ammonium nitrate plants can be easily achieved, while maintaining outstanding product quality.
Many of us will recall the pictures and video records showing the effects of the tragic Beirut explosion on August 4, 2020. Investigations proved that the disaster was caused by 2,750 tonnes of ammonium nitrate (HDAN) – stored together with fireworks – brought to rapid decomposition (explosion) by an external fire. However, as with most incidents, a series of failures finally led to the catastrophe. In the Beirut case, this can be attributed to a lack of knowledge about the specific properties and risks caused by the misuse of AN.
AN is considered to be safe, but can decompose or even explode when not treated correctly. Care has to be taken to avoid extensive heat input and contamination, the main triggers for decomposition1 . Therefore, any source of heat and burnable substances must be kept away from AN storage facilities. In addition, the maximum storage capacity should be limited – several stacks of bagged AN rather than one large heap. None of this is new to those active in the AN business and it can be found in various sources of literature, e.g. from Fertilizers Europe2 and IFA. In Beirut, the guidelines were clearly not observed by the parties involved. Presumably, they were inexperienced in the handling of AN.
As a general rule of thumb, AN is safe when a) not exposed to heat and b) not contaminated by foreign (organic) materials.
Producers cannot entirely avoid incidents from happening, but they must do their utmost to ensure safe production and on-site storage of AN. In West, Texas, in 2013 another accident reminded the community of AN producers that failures occur even with those working with AN on an everyday basis.
AN as a fertilizer
But why is AN used as a fertilizer in the first place when there is a risk of incidents with fatalities, and what advantages does it have over other fertilizers?
First of all, worldwide ammonium nitrate is the second most important nitrogen fertilizer after urea. In addition, AN has the advantage of containing two different forms of nitrogen: nitrate (NO3) that can be taken up by plants directly and rapidly and ammonium (NH4 + ) that has to be converted by bacteria in the soil first. As a result, nitrogen is available to the plants directly and over an extended period of time, not just once or over the long term. Another important issue is the higher yield in both nitrogen availability and crops when applying AN (compared to UAN or urea): The loss of nitrogen (by ammonia volatilisation) contributes to pollution, affects the air quality and simply wastes resources. Fig. 1 shows that ammonia volatilisation is several times lower for AN-based fertilizers like AN or CAN compared to urea or UAN. Quantity (crop yield) and quality (protein yield) are also higher with AN compared to urea (Fig. 2).
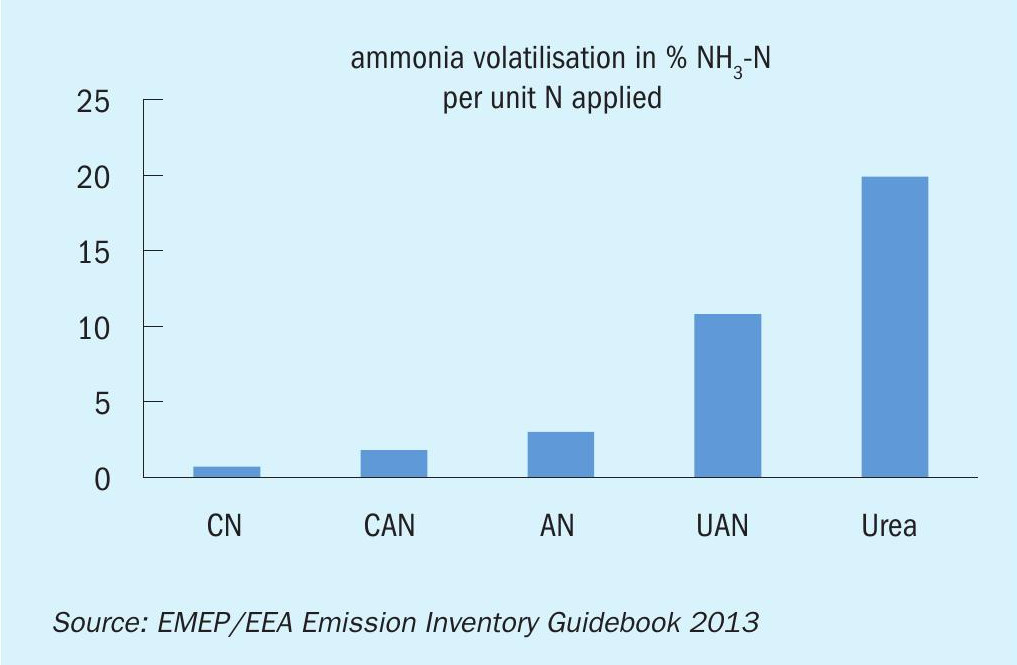
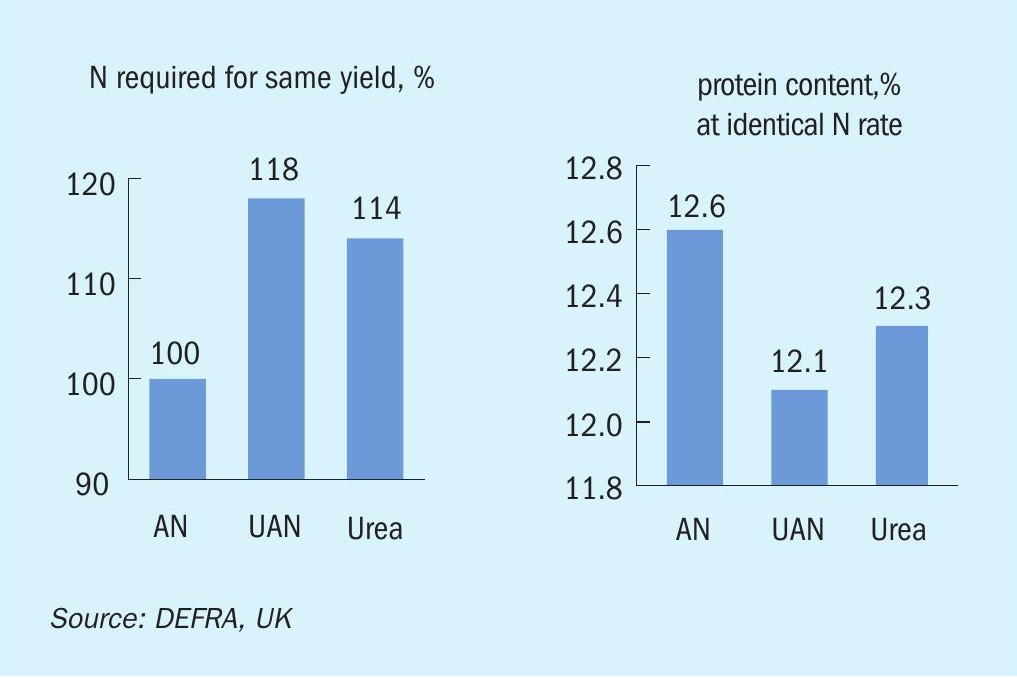
Green technologies
By utilising renewable energy sources to produce green hydrogen/syngas/ammonia/nitric acid and finally green AN, a complete and integrated environmentally-friendly fertilizer production line can be designed by thyssenkrupp Industrial Solutions (thyssenkrupp Uhde as of June 1, 2021), based on its own technologies:
- hydrogen generation by water-electrolysis;
- conversion to ammonia3 ;
- nitric acid production with highest (beyond BAT) N2 O-reduction technology EnviNOx®3 ;
- ammonium nitrate production with the option to feed granulation-, prilling- or UAN-plants.
Plant safety by design
It is still reasonable for AN to be used widely as a fertilizer – but what can manufacturers do within their own scope of responsibility to strictly minimise the likelihood of an accident? What is mandatory for the safe production of AN?
Basic rules
There are some basic rules to be considered for the design and operation of AN plants:
Temperature and pressure: Depending on the temperature, AN starts to decompose by following several chemical reactions, which lead to various chemicals and compositions. Reactions that start at elevated temperatures (>180°C) are problematic as they generate huge amounts of heat and are therefore self-sustaining. The released gaseous reaction products can cause enclosures to burst or even explode when confined. If the first gases are not vented but accumulate in the system, the increasing pressure accelerates the decomposition processes even further.
This chemical response to physical influences requires the following design rules:
- low operating pressure;
- release of gases/vapours must be possible at any time;
- low temperatures must be maintained;
- any possibility of heat input into the system must be observed and limited.
Composition: Even though AN is formed by neutralising nitric acid with ammonia in equal molar ratio, its composition is very important when it comes to safety. There are several ions with a negative effect on the onset-temperature of AN’s decomposition reactions: With increasing concentration of impurities like chlorides, (organic) carbon, metal ions (Cu, Zn, Cr,…) and the like, the onset-temperature decreases – reactions are more likely to happen and will develop more quickly. Carbon, in particular, when reacting with AN, will liberate large amounts of heat. But, not only foreign ions, even nitric acid itself can promote the described effects if applied in excess or having become available due to decomposition reactions. Such a reaction already takes place at ambient temperature: AN slowly decomposes into nitric acid (causing the pH value of the aqueous solution to drop) and gaseous ammonia, leaving the system via the vent. AN producers will all be familiar with the faint smell of ammonia in close proximity to AN storage vessels that are not properly vented.
As a result, the plant design has to meet the following challenges: precise feedstock control, process monitoring and provisions to compensate for the natural acidifying of AN solutions accompanied by strict quality management of the feedstock.
Basic process
How can these limiting safety considerations be combined in an AN neutralisation plant?
In general, the focus of the plant design is on safety. Nonetheless, other important aspects of plant operation are also looked at, e.g. flexibility in plant load, export of very pure process condensate and general ease of operation (i.e. no wear and tear parts in static equipment).
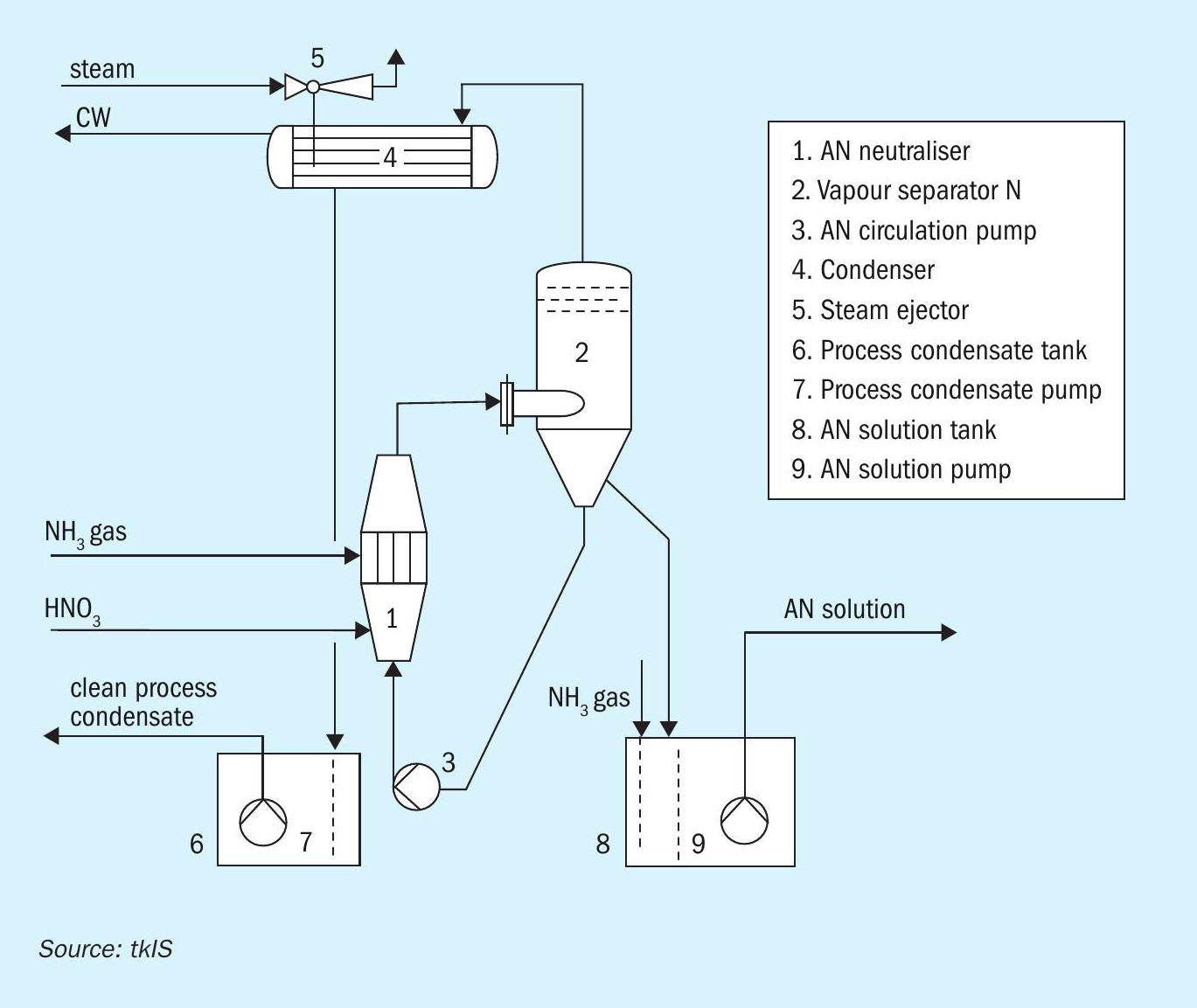
Choosing to operate an uhde® AN vacuum neutralisation and concentration unit, allows plant operators to perform the exothermic reaction between nitric acid and ammonia at a low temperature of only 145°C, thereby staying away from critical on-set limits (see Fig. 3). Additionally, the precise control of both pressure and temperature enables AN producers to generate AN solution at a constant concentration of e.g. 92 wt-% in the neutralisation step (item 1, Fig. 3). This high grade AN is achieved without external steam supply just by flash evaporation – the resulting vapours are thoroughly clean as well as condensed, leaving no chance for any nitrogen to pass into the atmosphere (item 4, Fig. 3). Besides the high nitrogen yield, no increase in system pressure is possible. An ESD system continuously monitors the temperature, pressure and critical flows, while a sophisticated control system takes care of the best operating conditions: An uhde® AN vacuum neutralisation system not only runs at low temperatures, but also at slightly acidic conditions. This is the key factor for the safe control of process parameters and lowest nitrogen slippage through process vapours. The proper pH value for (intermediate) storage is in the alkaline range and is adjusted downstream of the vapour separation under atmospheric conditions (item 8, Fig. 3).
Special features
An important contributor to safety and homogenous product quality (see uhde® pH measuring system, Fig. 4) is the measurement of pH values throughout systems containing AN solution by a proven sampling system. The lifetime of the pH probe is prolonged by diluting the AN solution with water and thereby reducing the risk of crystallisation. The feed of saturated steam through the red coloured valve (see Fig. 4) is normally closed, but can be used for flushing purposes.
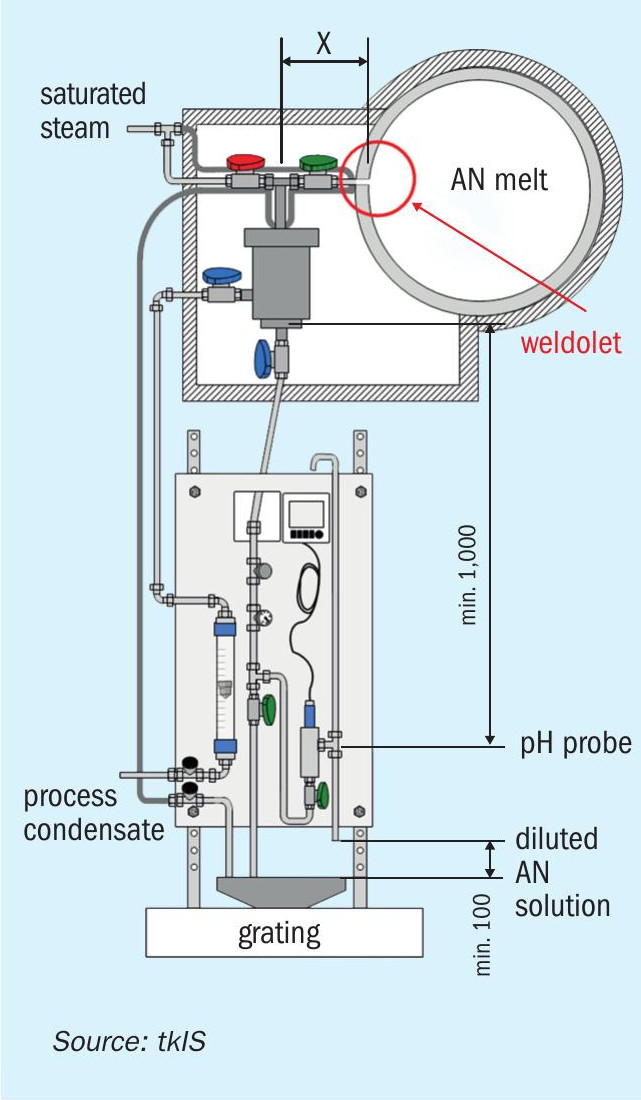
Furthermore, in cases of a prolonged period of time running on lower pH levels than optimal for process control, the plant is stopped automatically by its control system. Even during a shutdown, the plant does not need to be drained. After stopping the feedstocks, the circulation pump will still be in operation allowing for a very quick restart.
Inside the reactor, the key to reducing ammonia losses (environment) and minimising spots of high nitric acid concentration (safety) is to have the ideal mix of the reactants ammonia and nitric acid. The result of a FLUENT® simulation in Fig. 5 demonstrates the almost perfect flow pattern in the uhde® reactor.
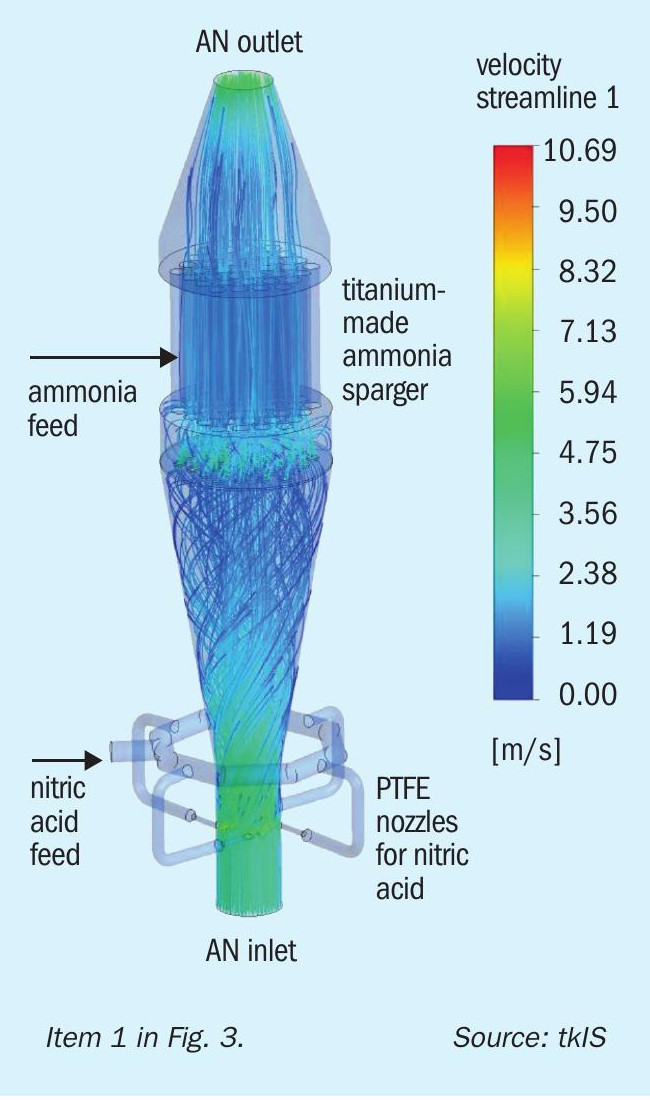
Not only the neutralisation reaction, but even the concentration to the final AN melt can be performed under sub-atmospheric pressure, relieving the plant management from having to think about operating temperatures beyond the on-set temperature and resulting formation of AN aerosols in the separated vapour stream and their abatement. The comparably low temperatures and the absence of air-swept concentrators avoids the formation of AN aerosols right from the very beginning. uhde® AN vacuum neutralisation and concentration plants are free of aerosols and have clean vents – only leakage air from the vacuum systems containing inert gas is released to atmosphere.
Latest Developments
The latest development in tkIS AN technology is the combination of the two vacuum units (neutralisation and concentration) to form one common vapour and condensate system as shown in Fig. 6, items 4 to 7 (patent pending). With AN melt being the final product, the concentration and temperature of this fluid defines the system pressure in the entire vacuum network. The vapours from concentration and neutralisation are cleaned separately, under their respective ideal conditions, but merged afterwards and finally condensed together. In doing so, there is no longer a need for a dedicated condenser for the concentration unit and both systems have one common process condensate tank.
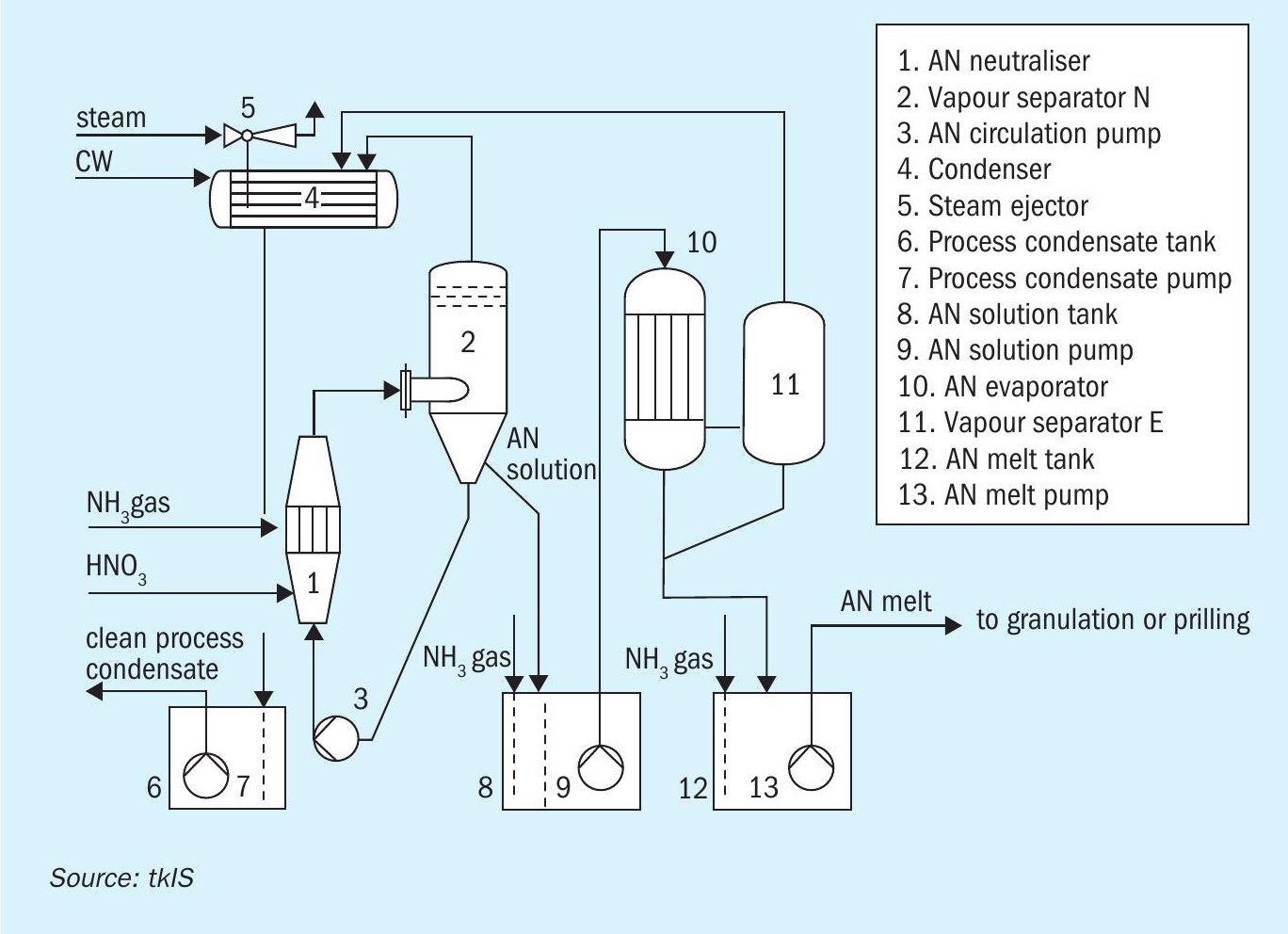
Other variants of neutralisation plants include systems operating at atmospheric pressure (in the vapour separator) or even at elevated pressure, depending on project-specific requirements like availability and cost of utilities. When designing those plants, special attention must be paid to the operating temperatures in the AN system, to absolutely avoid reaching the onset conditions of decomposition reactions. A wise selection of construction materials for pressure neutralisation plants is mandatory as the corrosion rate increases with elevated temperatures. Fig. 7 shows an example where process waste heat is used in reboiler 6 and 9.
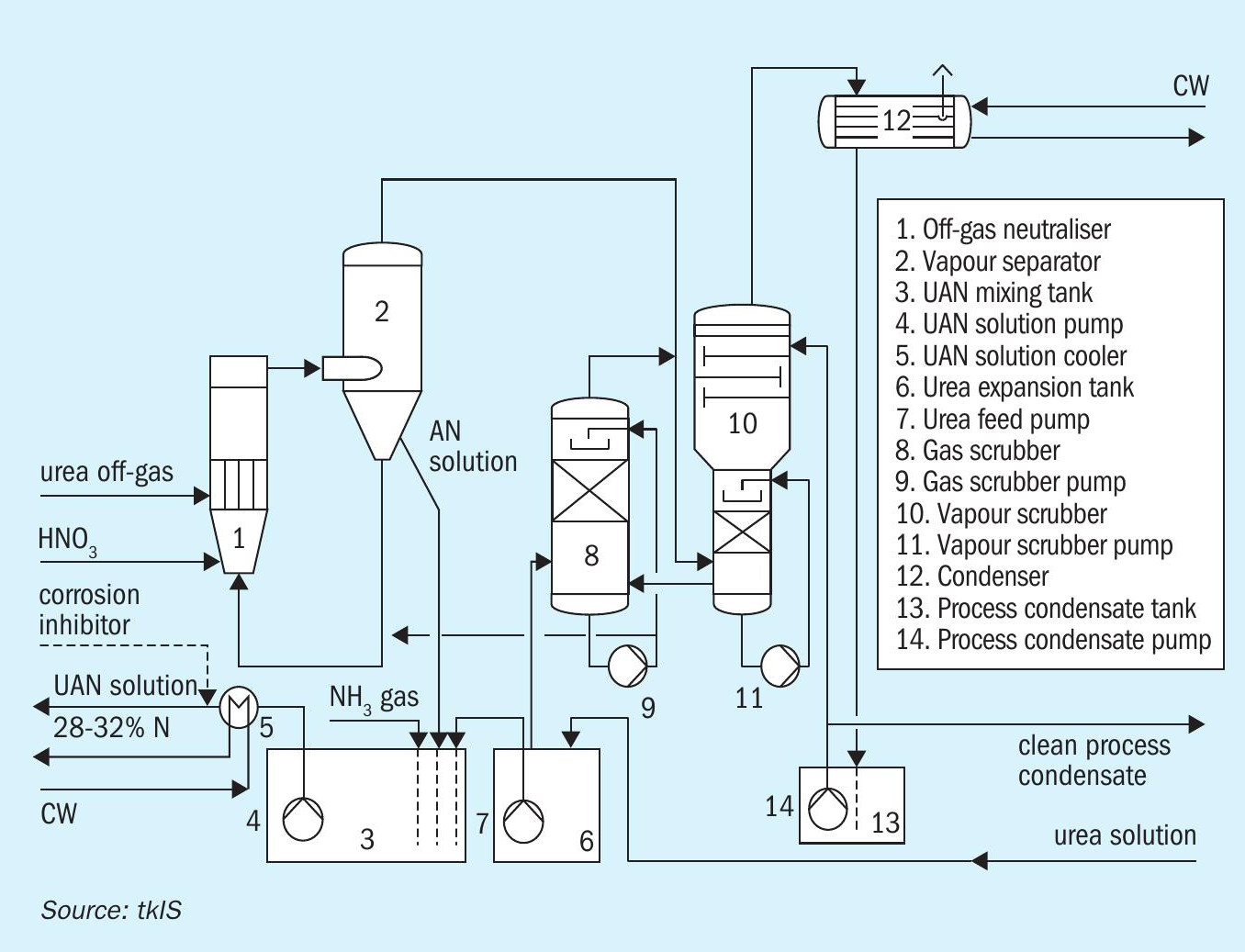
Due to the chosen operating pressures and temperatures and the utilisation of process heat for concentrating the AN solution, pressure neutralisation is the right choice. In particular, if the focus is on safety and, additionally, on utility consumption (steam and cooling water) rather than investment cost.
With UAN production it might be commercially beneficial to feed the low-pressure, ammonia-rich off-gas of a urea plant directly to the AN neutraliser. Consequently, the system pressure in the AN neutralisation must be lowered to cope with the pressure of the urea off-gas. This can be achieved by natural draft circulation instead of the forced circulation that is typical for most plants (see Fig. 8). Thereby low pressure off-gases from a urea synthesis unit can be utilised to produce AN that meets environmental limits by using dedicated additional scrubbers (items 8 and 10 in Fig. 8).
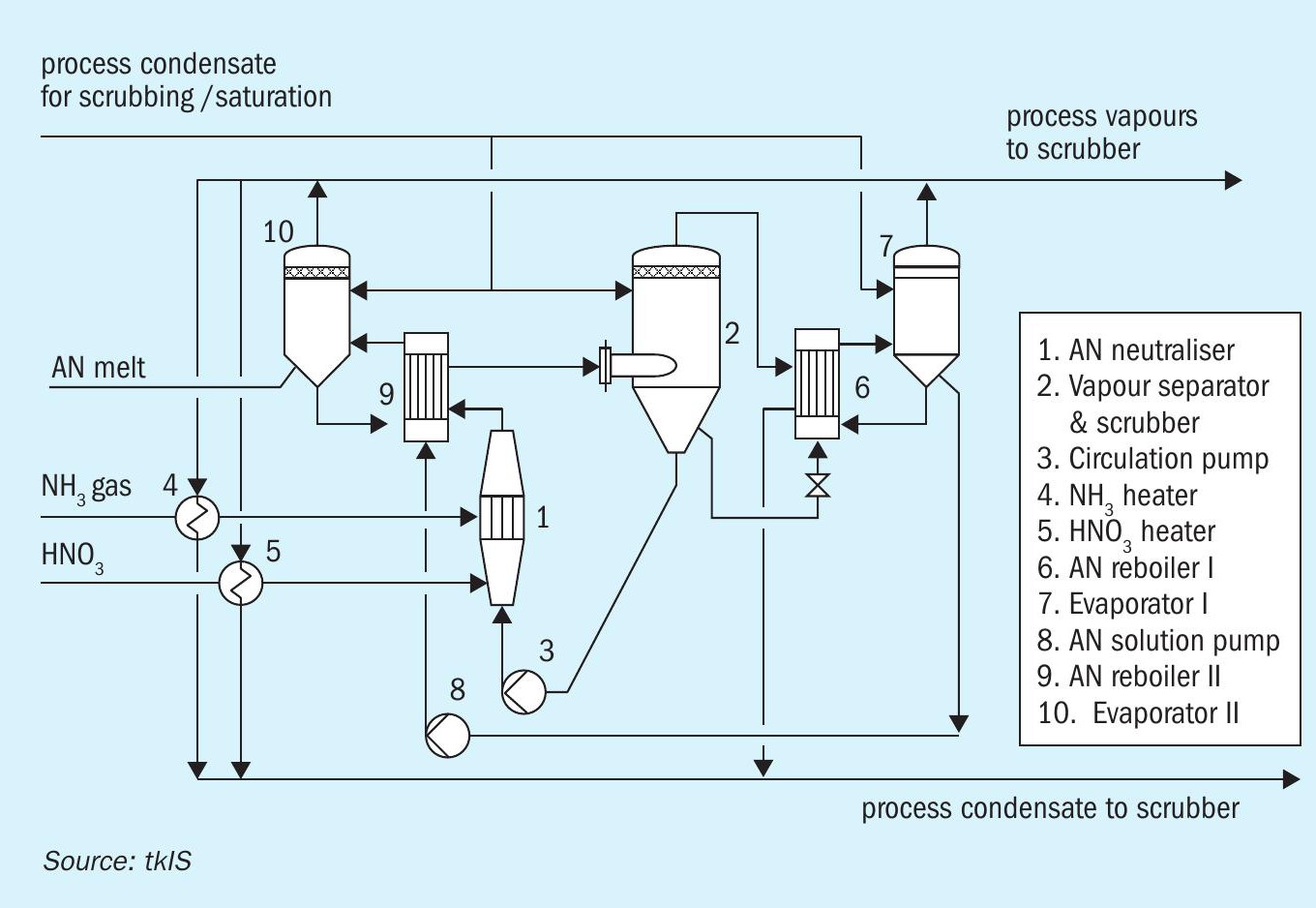
Reliability
What is the key to building safe AN solution plants with almost all-year round operation?
The application of nitric acid nozzles made of PTFE (see Fig. 8) ensures yearlong operation of the AN neutralising reactor without any maintenance being necessary. Gaseous ammonia is brought into contact with the circulating, acidified AN solution by means of a titanium-made sparger (see Fig. 8), which lasts the whole lifetime of the plant. Even after an unplanned shutdown, e.g. due to power failure, the plant can usually be restarted within 30 minutes. All AN inventory is stored in either the neutralisation loop or the intermediate buffer tanks, allowing for close condition monitoring and precise control of the temperature, concentration and pH value. Gaseous ammonia and water can be added at any time to all AN-containing systems, due to the fact that AN is safe if treated properly! Further aspects like the monitoring of pumps (possible sources of heat into the AN solution), utilisation of saturated steam, avoidance of “dead legs” in the piping system, and sophisticated and reliable interlocking systems are part of a state-of-the-art AN neutralisation plant. If the internal values are not of main interest, then the measurable external results are: The typical nitrogen content in the process condensate leaving this type of neutralisation plant is below 10 ppm. From a technical point of view this is a unique contribution to the environment as no further dedicated water treatment section needs to be involved.
Customer orientation
How can safety requirements, internal and external standards and client requirements in the design phase be handled by assuring quality while not following the ‘copy and paste’ approach?
The design of safe, reliable and individual plants must consider lessons learned, strict internal and external standards based on experience and best practice, while at the same time focussing on the client’s needs. This can be achieved by using the Pre-Configured Plant Concept, PCPC, approach. This engineering method divides up a complete plant into functional modules, covering all main engineering documents for the design of a standardised plant and summarising all safety and operability related information to represent a holistic and quality assured basis for proposals. The PCPC method includes key information from all engineering disciplines like process, layout, piping, static equipment and machinery. The system is stringent in so far as it ensures quality and safety, but it is also flexible in that it allows tailor-made proposals according to client’s requirements.
Conclusion
Even though AN is a potentially hazardous substance that requires advanced attention, it is a state-of-the-art fertilizer and can as such contribute to the global effort to reduce greenhouse gas emissions. When AN is produced under well selected conditions at a plant that was designed with experience and care, significant steps towards a safe product have been taken.
References