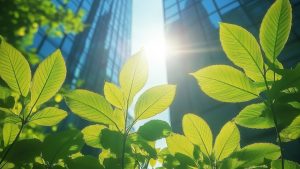
Uhde gasification selected for biomass-to-SAF project in France
Thyssenkrupp Uhde’s BioTfueL® technology has been selected for the BioTJet project by Elyse Energy and its partners (Axens, Avril, IFPEN). This project will produce sustainable aviation fuel (SAF) from end-of-life wood waste and local forestry residues. together with the addition of green hydrogen. By 2029, BioTJet will supply sustainable aviation fuel to reduce carbon intensity in air