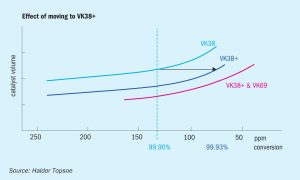
New catalysts target key industry challenges
Selecting the right catalysts for the SO2 converter in a sulphuric acid plant has always been about balancing expenses, gains, and compliance. With increasing demands for sustainability and in challenging economic times, operators need to adjust their plants to get even more from less. This has led to market demand for new catalytic solutions that offer better productivity and a lower climate footprint, all at the lowest cost possible. Catalyst design and formulations continue to evolve with Haldor Topsoe, DuPont Clean Technologies and BASF all adding new types of sulphuric acid catalysts to their portfolios.