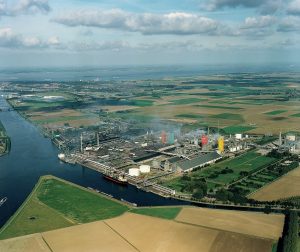
The future of Europe’s nitrogen industry
High feedstock prices and regulatory burdens continue to put pressure on European nitrogen producers to innovate.
High feedstock prices and regulatory burdens continue to put pressure on European nitrogen producers to innovate.
New innovations, services and latest technologies to improve the operation and reliability of steam methane reformers from AMETEK Land, Kontrolltechnik, BD Energy Systems, Koch Engineered Solutions, and Quest integrity.
The COP-26 summit in Glasgow last year signed into force new rules on carbon emissions trading which may gradually start to see carbon pricing spread worldwide, with knock-on effects on emissions intensive industries like ammonia and methanol.
A complete listing of all articles and news items that appeared in Nitrogen+Syngas magazine during 2021.
The production of syngas from hydrocarbon feedstock uses a number of catalytic steps to increase efficiency and maximise conversion while minimising energy consumption. In this article we report on the latest developments in water gas shift catalysis from Johnson Matthey, Clariant and Topsoe, and shift converter design from Casale.
Gordon Feller looks at Gasunie’s plans to build a new nitrogen plant at Zuidbroek to allow for the progressive shutdown of the Groningen gas field, one of the largest in Europe.
Recent spikes in natural gas prices, particularly in Europe, have highlighted the tightness of natural gas markets around the world going into the northern hemisphere winter. Are ammonia and methanol producers on for a run of high gas prices in 2022?
Last year the International Energy Agency (IEA), in conjunction with IFA, published the Ammonia Technology Roadmap, which looks at ways of achieving decarbonisation of the nitrogen fertilizer industry by 2050. In this article we look at the scenarios and technology options that will define the industry over the next three decades.
Stamicarbon offers advanced scrubbing technologies for fertilizer granulation plants and prilling towers. This article describes the technology and experience with the second operational MMV scrubber, which is installed at the Dakota Gasification Company’s (DGC) urea granulation plant, and highlights the successful pilot test with its JV scrubbing technology.
With globalisation seemingly in retreat, the protectionist impulse is seeing a rise in barriers to trade, from quotas and tariffs to anti-dumping actions and domestic subsidies.