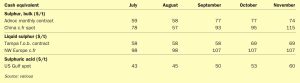
Price Trends
Meena Chauhan, Head of Sulphur and Sulphuric Acid Research, Argus Media, assesses price trends and the market outlook for sulphur.
Meena Chauhan, Head of Sulphur and Sulphuric Acid Research, Argus Media, assesses price trends and the market outlook for sulphur.
Ron Olson of The Sulphur Institute considers sulphur’s important role in plant health.
Norilsk Nickel has finally closed down its nickel smelting operation at Nikel in Russia’s Murmansk region; the company’s oldest still operating production facility. The shutdown is part of the company’s environmental programme, which aims to significantly reduce its environmental impact at all production sites. The Nikel closure will eliminate SO2 emissions in the cross-border area with Norway, which had become a major bone of contention with the Norwegian government. Norilsk aims to reduce SO2 emissions at Kola by 50% by the end of 2020 and 85% by the end of 2021, and is modernising its production in Monchegorsk, including the construction of new state-of-the-art facilities.
Process and simulation models can be valuable tools when troubleshooting to solve operational issues in sulphur recovery units. Two examples are provided. In the first case study it is shown how a tuned model was useful in troubleshooting an SRU that was experiencing lower than expected recovery efficiency and apparent channelling in the first catalytic converter. In the second case study an SRU simulation tool is used to investigate sulphidic corrosion in a waste heat boiler.
Continuing rationalisation in China’s phosphate industry has been reducing demand for sulphur and sulphuric acid at the same time that the country is producing more of both.
Corrosion Resistant Alloys, LP, a manufacturer of high-grade corrosion resistant alloy tubes, has appointed Tom W. Slaughter in a business development and advisory role. Based in Houston, Slaughter will be responsible for building relationships with strategic partners, including customers and suppliers. Slaughter’s background is as an industry leader in high-pressure, high-temperature (HPHT) and deep gas applications with more than 40 years of global industry experience. Most recently, Slaughter served as president of Energy Alloys, Advanced Tubulars beginning in 2007. Prior to this role, he served as president of CRA from 2001 to 2007 where he had full responsibility for global sales and supply chain and worked directly with domestic and international end users of specialty CRA OCTG products.
Fires are known to occur in sulphur storage pits and tanks somewhat frequently due to the presence of both flammable material and air, so methods for preventing and extinguishing these fires are critical. D. J. Sachde, K. E. McIntush, C. M. Beitler, and D. L. Mamrosh of Trimeric Corporation review fire suppression methods used in the industry including snuffing/sealing steam, rapid sealing, water mist, and inert gas blanketing. Protective tank design features to reduce the likelihood of a sulphur fire are also reviewed. Benefits and limitations, design considerations, and recommended guidance for suppression and preventative measures are discussed.
Selecting the right catalysts for the SO2 converter in a sulphuric acid plant has always been about balancing expenses, gains, and compliance. With increasing demands for sustainability and in challenging economic times, operators need to adjust their plants to get even more from less. This has led to market demand for new catalytic solutions that offer better productivity and a lower climate footprint, all at the lowest cost possible. Catalyst design and formulations continue to evolve with Haldor Topsoe, DuPont Clean Technologies and BASF all adding new types of sulphuric acid catalysts to their portfolios.
The turning of a new calendar year is a predictable waypoint in our lives. That is why it has always traditionally been a time for reflection on the past and looking to the future. Therefore, given how 2020 had turned out, perhaps there was an inevitable hope that the turning of the New Year and the start of 2021 might see an improvement in things in general, and of course the trajectory of the pandemic in particular, especially now that several vaccines have been approved for use in record time, and a massive programme of vaccination has begun across the world.
Failure investigations, equipment design and process upgrade projects for SRUs often overlook the impact of water quality. In this article E. Nasat o of Nasato Consulting and L. Huchler of MarTech Systems explore impacts of higher heat transfer rates, control of boiler and condenser water chemistry, conventional equipment design/configurations and monitoring program designs. SRU operators can improve the effectiveness of their failure investigations by implementing a broader, more holistic approach that assesses equipment design, process conditions, operating protocols and water quality issues.