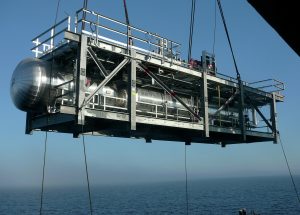
100 years of Comprimo
As Comprimo celebrates its 100th anniversary, we explore the group’s history from its earliest days in the Netherlands in the 1920s to its current status as a global leader in gas treatment and sulphur recovery technology.
As Comprimo celebrates its 100th anniversary, we explore the group’s history from its earliest days in the Netherlands in the 1920s to its current status as a global leader in gas treatment and sulphur recovery technology.
Aparna Saiju and Nishevitha U G of SLB-MPS explore the concept of energy optimisation using power recovery turbine (PRT) technology in amine sweetening units, focusing on its potential benefits, implementation strategies, and environmental implications.
Ganank Srivastava of Bryan Research & Engineering examines ways to reduce carbon footprint in sour gas facilities.
A look at the safety challenges that face developers of ammonia-powered shipping vessels before it can become used more widely as a low carbon fuel.
Casale, Saipem, Stamicarbon & Toyo Engineering Corporation showcase a selection of innovative technologies that have recently been brought to the market.
A review of the current slate of plans for green and blue ammonia production.
The production and use of nitrogen fertilizers are responsible for around five percent of global greenhouse gas (GHG) emissions. The fertilizer industry will need to drastically cut these emissions by 2050 as part of its contribution to the 1.5 °C global warming target. Yet around 48 percent of the global population rely on crops grown with nitrogen fertilizers. Guaranteeing food security, by continuing to supply affordable crop nutrients at scale, while transitioning to a low-carbon future, is therefore the collective challenge for the global fertilizer industry and world agriculture.
The need for immediate climate action and cuts in carbon emissions has never been more urgent, especially in a world where ecosystems are increasingly under threat. The production of green fertilizers offers a clear route to achieving these goals by decreasing the chemical industry’s reliance on fossil fuels. Stamicarbon’s Carmen Perez, Rolf Postma and Nikolay Ketov outline the company’s innovative and integrated approach to green fertilizer technology.
RNZ Group is positioning itself as the most innovative and sustainable fertilizer producer in the UAE. In partnership with Shell, the company has been manufacturing sulphur-enhanced fertilizers using Thiogro technology since the end of 2022. Raza Soomar , RNZ’s managing director, provides an overview of the company and highlights recent business successes.
Fertilizers will always be fundamental to food production, but they will also have to be low emissions, environmentally friendly and support healthy soils. In this article, Dr Alexander Schmitt, Chief Marketing Officer, Anglo American Crop Nutrients, explains how polyhalite meets all three of these criteria – while also helping to increase the quantity and quality of food a farmer can produce.