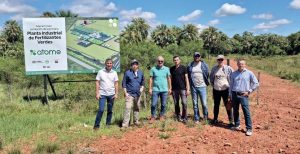
Casale – leading the green fertilizer revolution
Casale’s technologies are transforming hydropower into green fertilizers for ATOME’s Villeta project in Paraguay.
Casale’s technologies are transforming hydropower into green fertilizers for ATOME’s Villeta project in Paraguay.
MOPCO has selected thyssenkrupp Uhde to supply advanced technology for its Damietta ammonia-urea complex in Egypt.
Days 2 and 3 of the CRU’s 38th Nitrogen+Syngas 2025 Expoconference turned to the technical sessions, organised in three parallel streams covering: green ammonia technology, nitric acid and ammonium nitrate, plant operations and reliability, urea technology, digitalisation, carbon capture, emissions reduction and sustainable fertilizer production, and fertilizer finishing.
10th February, 2025 – sessions as reported by Richard Hands from Barcelona CRU’s 38th Nitrogen+Syngas 2025 Expoconference has begun in Barcelona with three strands covering business development, technical innovations and practical operator training, the latter comprising case studies for analysing hazards associated with green ammonia production. Heading up the business development session, Marti Leppälä, Secretary […]
6th February, 2025 Johnson Matthey (JM) – a global leader in sustainable technologies – and Bosch a leading supplier to the automotive industry – have today agreed terms to accelerate future projects together. The agreement confirms both parties’ intentions to develop and produce catalyst coated membranes (CCM) for use in fuel cell stacks. Transforming and […]
Blue hydrogen has emerged as a crucial technology for decarbonisation as nations around the world work towards net-zero carbon targets. By decarbonising hydrogen production and exploring clean hydrogen sources we can fully harness the potential of hydrogen in the global energy transition. Johnson Matthey, Topsoe and Casale report on their strategies and advanced technical solutions for large scale blue hydrogen production.
While there is still a considerable push for use of biomass waste as a lower carbon feedstock for chemical production via gasification to syngas, biological processes such as fermentation are increasingly gaining traction as an alternative.
New concepts focused on the transfer and combination of existing sulphur and sulphuric acid technologies to support decarbonisation of the sulphuric acid industry are being investigated. In this article three research projects are discussed: sulphur dioxide depolarised electrolysis for green regeneration of spent acid, use of renewable heat and catalyst to the splitting process from sulphuric acid to SO2 for reduction of fossil fuel consumption, and sulphur as an energy vector.
The 2030 greenhouse gas emission reduction goals in the European Union are driving oil and gas producers to reduce CO2 emissions wherever possible. This extends to even the incinerator attached to a sulphur recovery unit (SRU). In this article Sulphur Experts review the role of the incinerator, how the three most common European TGUs each affect the demand on the incinerator itself, and the potential reduction in CO2 emissions for a generic facility of each type.
Van Iperen International is pursuing an ambitious sustainability strategy to cut its carbon footprint by 50%.