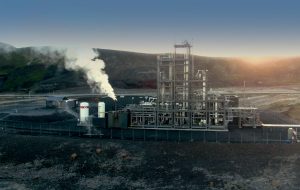
Carbon dioxide as a feedstock
Falling costs for production of hydrogen by electrolysis are encouraging more serious consideration of using recovered carbon dioxide as a feedstock for chemicals and even fuels production.
Falling costs for production of hydrogen by electrolysis are encouraging more serious consideration of using recovered carbon dioxide as a feedstock for chemicals and even fuels production.
Although the Covid-19 pandemic has been the big story in every market this year, the disruption and dislocations that this has caused have masked some of the bigger trends in the urea market, such as the revival of Chinese exports and India’s push for self-sufficiency.
New technology makes it possible for methanol producers to diversify their product portfolio and participate in the high growth mono ethylene glycol market. A. Shah of Johnson Matthey reports on the development of the new technology and its commercialisation.
The following case study reports on a serious incident in a urea plant where a leak in the weld overlay in the urea reactor bottom resulted in a costly plant shutdown and near miss of rupture of the high pressure vessel. It is known that carbon steel can corrode with rates of 1000 mm/year not taking into account erosion due to flashing. The impact of the NH3/CO2 ratio on the corrosion rate is questionable.
Johnson Matthey (JM) has been selected by China’s Ningxia Baofeng Energy Group as licensor for a third methanol synthesis plant at their coal to olefins complex near Yinchuan in Ningxia province. With a planned capacity of 7,200 t/d (2.4 million t/a), the unit will be the largest single train methanol plant in the world once completed.
In spite of continuing safety concerns due to the Beirut explosion, and the rise of the use of urea as a nitrogen fertilizer, ammonium nitrate demand continues to increase in several key markets.
Alistair Wallace, Head of Fertilizer Research, Argus Media, assesses price trends and the market outlook for nitrogen.
Troubleshooting and root cause analysis help to identify and solve problems in the operation of nitric acid plants and to prevent future reoccurrences. Johnson Matthey, Casale and Sabin Metal Corporation discuss their approach to solving problems in nitric acid plants to improve plant reliability and efficiency and to avoid unplanned shutdowns, costly replacement of equipment and loss of production.
N. Temnaya and S. Suvorkin of NIIK report on the modernisation of monopressure (UKL-7) and dual pressure (AK-72) nitric acid plants in Russia and the CIS.
It’ s not a very worthy thought, I’m afraid, but I must admit it was my first reaction on seeing the terrible pictures from Beirut on August 4th. The explosion that ripped through the centre of the historic and much troubled Mediterranean city was captured from many different smartphone cameras, and watching the expanding vapour cloud from the supersonic shockwave, and witnessing the sheer size of the explosion, it seemed immediately evident to me that it had to be a high explosive responsible, not the fireworks that could be glimpsed sparkling beforehand in the smoke from the burning warehouse. The rising cloud of orange-brown nitrogen dioxide that followed the blast was the clincher – it looked like it was ammonium nitrate yet again.