Nitrogen+Syngas 367 Sept-Oct 2020
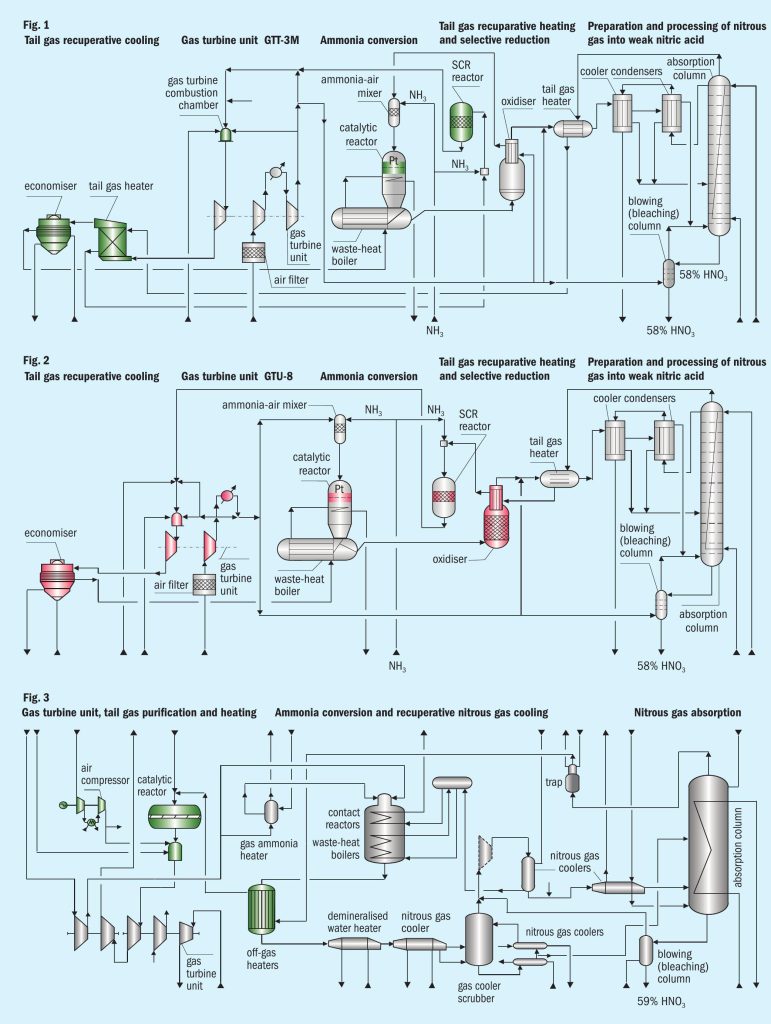
30 September 2020
Improving nitric acid plant performance
NITRIC ACID PLANT MODERNISATION
Improving nitric acid plant performance
N. Temnaya and S. Suvorkin of NIIK report on the modernisation of monopressure (UKL-7) and dual pressure (AK-72) nitric acid plants in Russia and the CIS.
The main nitric acid manufacturing facilities in Russia and the CIS are based on large scale UKL-7 and AK-72 process units that are in need of upgrading.
Besides producing nitric acid, existing UKL-7 and AK-72 units generate thermal energy in the form of superheated steam which is fed into the plant’s network and mechanical energy which is generated in high-temperature gas turbines and is used for process air compression.
The main modernisation targets for existing UKL-7 and AK-72 units are to:
- switch to a selective catalytic tail gas reduction system;
- enhance unit capacity by reducing air consumption;
- reduceeliminate natural gas consumption;
- switch existing gas turbines to lower operating temperatures to increase their performance.
Research and Design Institute of Urea and Organic Synthesis Products (NIIK) is a leading design and technology company for chemical plants in Russia and the CIS. In co-operation with engineering and technical centre Khimazot-SPb LLC, NIIK is actively engaged in various projects for the modernisation projects of existing mono and dual pressure nitric acid units.
Currently NIIK is implementing two UKL-7 units modernisation designs which differ in the following ways:
- gas turbine equipment available in the market;
- process equipment design;
- steam generation system used.
The first design is a new modernised UKL7-76M unit equipped with a GTT-3M gas turbine offering improved technical and economic performance (Fig. 1). The nominal capacity of the unit is 16.5 t/h nitric acid (HNO3 monohydrate).
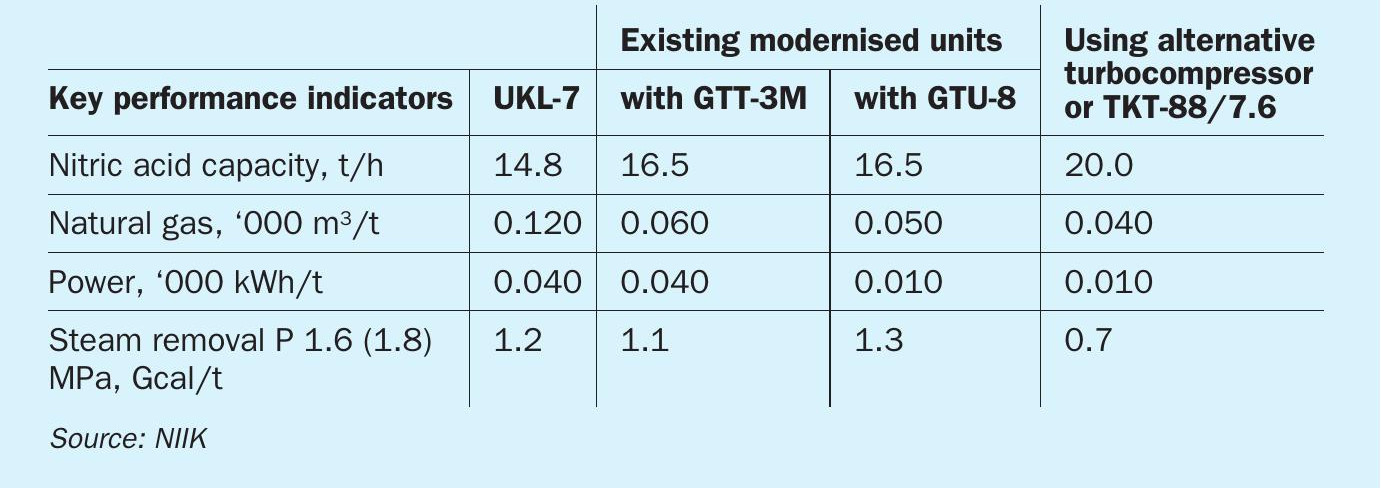
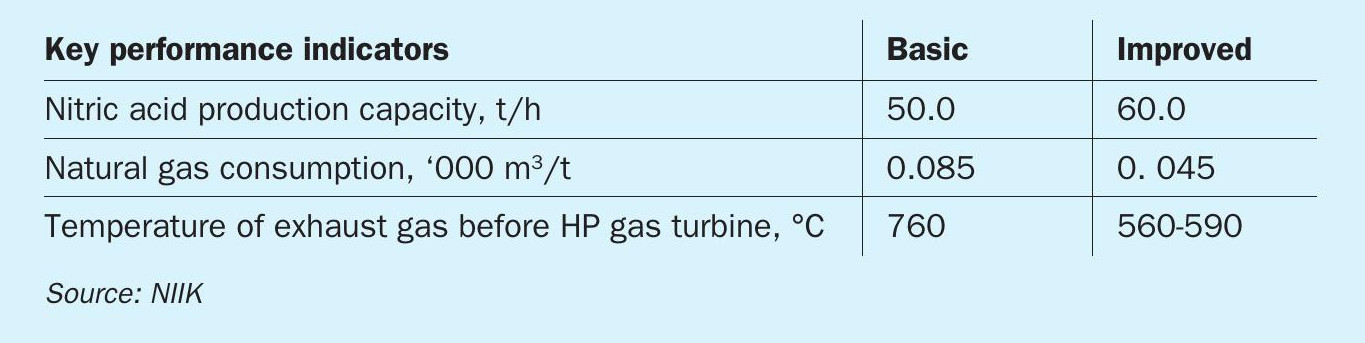
The second UKL-7 process design, currently in operation, uses a GTU-8 gas turbine unit, which is characterised by its smaller size and requires no intermediate air coolers or compensatory capacity of the drive. This scheme offers a quick return on capital investment and a compact and simpler plant arrangement (see Fig. 2).
The improvement of the existing mono-pressure UKL-7 unit benefits from:
- 20% nitric acid capacity increase;
- 30% reduction in natural gas consumption,
- 15% increase of steam removal.
Going forward, a new single stage turbo-compressor unit TKT-88/7.6 will be introduced to the market as the latest NIIK REP Holding (Saint-Petersburg) development.
The TKT-88/7.6 turbo-compressor unit for new nitric acid plants is supplied as a single unit with a starting device, combustion chamber and aggregate equipment located in a noise-insulating casing on the support frame.
A distinctive feature of the TKT-88/7.6 gas turbine unit is the increased air capacity which has an output of 20 t/h min nitric acid (HNO3 monohydrate).
The new TKT-88/7.6 unit increases nitric acid output to 20 t/h min and reduces natural gas consumption (Table 1).
NIIK in cooperation with KhimAzot-SPb are also currently implementing the modernisation of a large scale AK-72 dual pressure unit. Fig. 3 shows the improved AK-72 nitric acid unit with selective catalytic tail gas reduction. In the proposed design, the gas turbine unit will be switched to low temperature conditions (550-590°C).
At the same time the capacity of the modernised AK-72 plant will be increased to 60 t/h nitric acid (HNO3 monohydrate) and the natural gas consumption will be reduced by 50%.
The main parameters of the improved AK-72 unit are specified in Table 2.
