Sulphur 419 Jul-Aug 2025
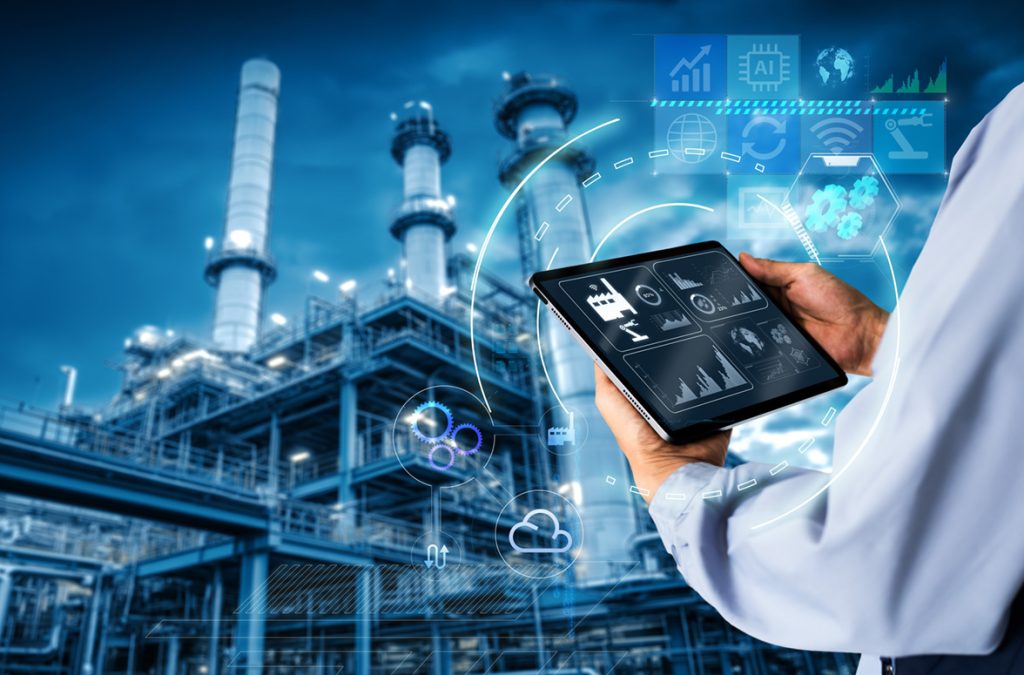
17 July 2025
Improving operations and monitoring in the acid industry
DIGITAL SOLUTIONS
Improving operations and monitoring in the acid industry
Metso is using a digital process twin as the core component of its digital solutions for sulphuric acid plants, which are currently under contract execution. In this article, Metso describes how digital solutions can profit from the deep integration of a digital process twin in the sulphuric acid technology, helping to improve operation, monitoring and reporting in the acid industry.
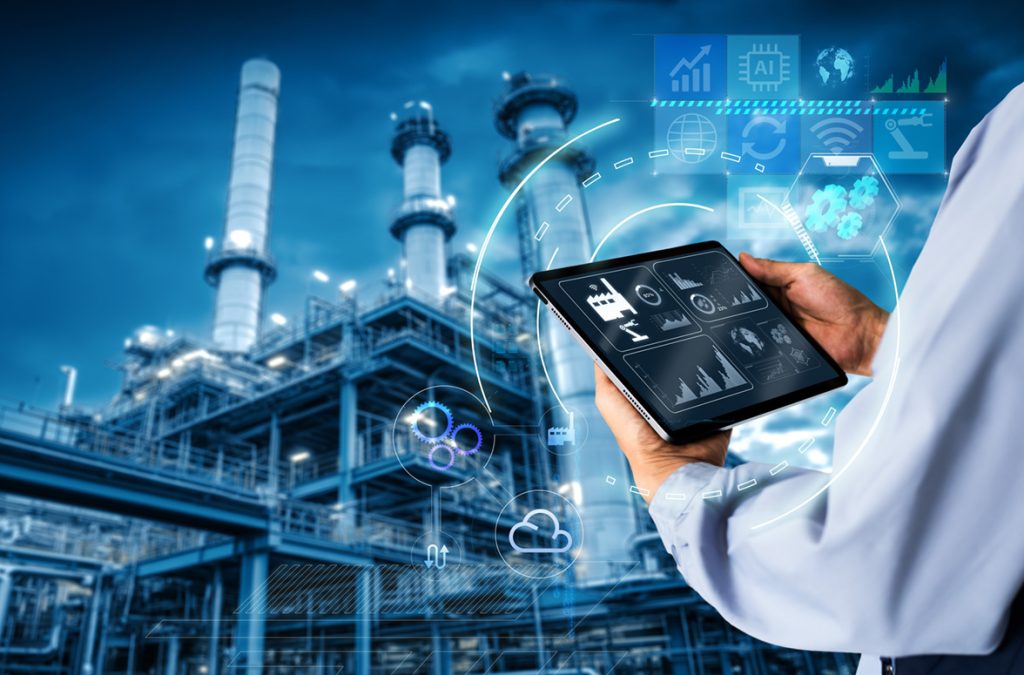
Steffen Haus, Collin Bartlett, Sagar Bhatta, Santhosh Sobhanakumari, Jochen Grünig, (Metso).
Many process design steps in modern manufacturing rely on the extensive use of process simulation models. Over the past decade, Metso has developed a suite of solutions for digitalisation in the value chain of sulphuric acid production1,2. Examples of significance include the Wet ESP Optimizer and the High Efficiency Scrubber Optimizer to support monitoring and control of metallurgical gas cleaning plants; and Sulphuric Acid Digital Solutions3. These digital solutions utilise a wide variety of methodologies, such as logic based algorithms, process modelling, KPI monitoring, etc.
However, a key component in the digital solutions for sulphuric acid plants is a high-fidelity process simulation, the so-called digital process twin. To understand the importance of a digital process twin, one must understand that the utilisation of process simulation models has evolved significantly in recent years.
Earlier, the focus was to use simulations predominantly to calculate the heat and mass balance of a process. Nowadays, simulation models or digital process twins are used for additional purposes that embrace process design, engineering related topics as well as pre-design of equipment, dimensioning, etc.
Closing the feedback loop between the digital process twin within the digital solution and operational data allows for progress and advancement on simulation accuracy and reliability or trustworthiness. This is an opportunity for an entire industry and can result in a win-win situation between plant designers and operating companies.
Thus, a traditional simulation model is converging towards a digital process twin. These process twins are now finding their way into digital solution offerings, which affect the daily process plant operation. The technology will provide an opportunity to improve operations, to monitor equipment or entire process sections, and to provide neutral and fact-based reporting to plant operations and management.
Metso is currently using such a digital process twin as the core component of the digital solutions for sulphuric acid plants, which are currently under contract execution. In this article, three key topics of the digital process twin will be discussed in more detail, namely:
- Digital process twin concept – how Metso’s simulations are integrated into its digital solutions, a commercial offering for on-site use by the plant operating company.
- Data historian/data lake integration – enriched data is retrieved by using the digital process twin. This enriched data can be utilised to provide additional information content into an on-site data historian.
- Reporting – enriched data can be utilised for enhanced reporting, e.g., including longer-term trending and monitoring of information, which is not normally available, but which can be retrieved by a digital process twin.
Digital process twin concept
Metso has developed proprietary process unit models for all relevant key process equipment of the sulphuric acid plant. These unit models are used within full plant simulations. Fig. 1 details the integration of proprietary process unit models into a full plant simulation.
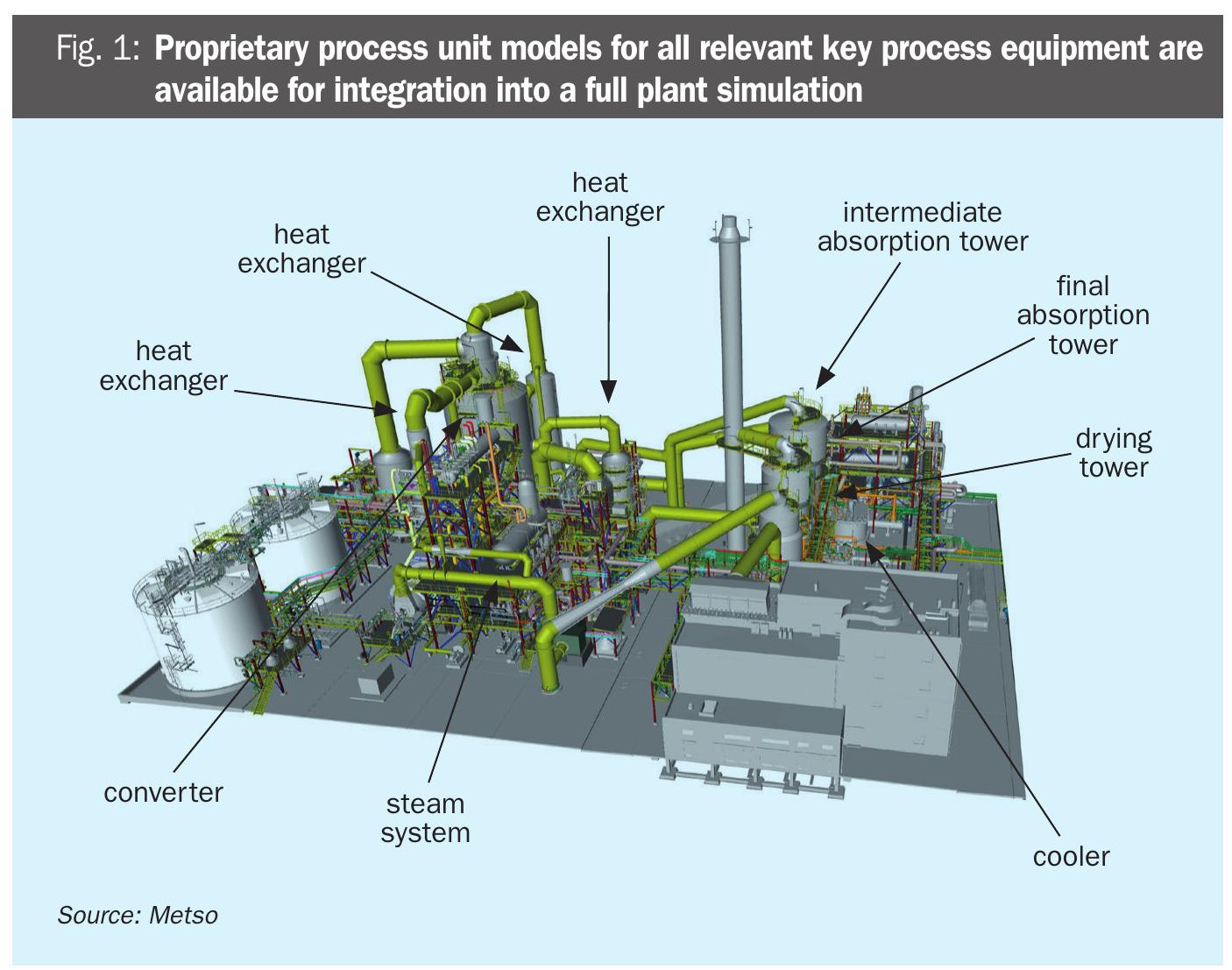
These process unit models have been validated against real-world operating plants and provide the required accuracy for reliable process design. Furthermore, the unitary models already have inbuilt relevant equipment design features. For example, early dimensioning of the equipment can be realised and allow full flowsheet simulation based on equipment design decisions. High-fidelity and validated unitary models can therefore be combined very efficiently into a full process simulation. Changes of dimensioning or other design decisions to a certain process unit will immediately become visible within the full process flowsheet calculation.
It is worth noting that the full digital process twin capabilities of the unit model integration into one platform has the advantage that process upgrades and modifications can be investigated or designed very efficiently. An example is the development of the LUREC-S process, shown in Fig. 24. Process engineers can rely on validated process unit models of key process equipment and can simulate the effect of a process adaptation or modification very quickly and effectively.
Compared to the “good old days”, when a simulation merely had the target to calculate the heat and mass balance for a certain condition, e.g., design plant load, the consequent and decisive utilisation of the digital process twin comes with a few beneficial changes in the plant design flow. One should not consider a process simulation as the main goal of process modelling, rather the thinking should adopt to a sequence of “concept to design to production”.
Furthermore, a feedback loop of operational data and information into the digital process twin can also be envisaged in the very near future or is already in implementation. It is well understood that in the process industry, a fully operational feedback loop is still very challenging, however a more digitalised industrial environment will truly open opportunities for optimised feedback loops. With such digital developments, achievement of a win-win scenario between plant designers and operating companies is a significant step closer.
The digital process twin concept within a platform will thus allow for adjusted thinking in the plant design process. The step sequence concept of design to production, plus feedback loop, will increase the design efficiency and will mitigate the risk for design errors.
Digital process twin integration into Metso digital solutions
The digital process twin is also beneficial for Metso’s digital solutions. Within this use case, the process twin is running calculations with live plant data, measured via traditionally installed field instrumentation. This can be done either for the full plant model, for a single piece of equipment, or for specific sections of the process plant, and is dependent on the use-case. One simple example is the monitoring of a heat exchanger, where an ideal instrumentation configuration consists of all instruments required to calculate the enthalpy at inlet and outlet and at both the cold and hot side. Typically, such an instrument configuration is not available. Thus, the digital process twin can be used to estimate missing information.
In such cases, the digital process twin is integrated into and utilised as an integral part of the Metso digital solution. Dependent on the plant instrumentation, Metso process engineers identify the required configuration of the simulation models, meaning that the simulation is set up in such a way that available instrumentation is utilised, so that the combination of plant instrumentation and plant process model provides a reliable and comprehensive overall understanding of the live plant operation. Non-measured data becomes available via the digital process twin and can be used for process optimisation or assessment of health-status of the equipment.
A good example of this relates to heat exchanger monitoring, involving the integration of a parameter for fouling in the unit model equations. The monitoring of the unit therefore becomes independent of the plant load or process conditions since operational conditions are inherently integrated by using the digital process twin, and not only monitoring and evaluating certain individual plant instrumentation data. This is a huge advantage of having the digital process twin as an integral part of the digital solution. This saves the application designer from normalising operational data to make it comparable, since this step is handled by the digital process twin. High fidelity and validated process unit models, digital process twin, and live operational plant data are combined and utilised together to retrieve relevant and valuable process insights.
The full information flow is shown in Fig. 3. The plant data is made available to the digital solution via its interface with the plant distributed control system (DCS). The algorithms in the digital solution can then query the digital process twin calculations with real-time measured plant data. The digital process twin calculation results are thus available for the algorithms and logic within the digital solution. The results are shared to the users via a specific user interface (UI). It is also possible to integrate parts of the UI directly into the DCS.
The information retrieved from the digital process twin via the digital solution algorithms can be numerous, and several examples are detailed below:
- non-measurable, but calculated process information, such as the earlier example of fouling effects in heat exchangers;
- longer term trends of certain process/ performance KPIs or equipment parameters, such as heat-transfer coefficients calculated by the digital process twin;
- the health status of equipment becomes available by combining digital process twin results with interpretation of these results within the monitoring algorithms.
As a result, enriched information is available, which is hidden in the data without a digital solution and the associated digital process twin, and this information is made available to operations personnel via specific digital solution screens. It is also possible to integrate such information into the plant DCS system and both options allow ad-hoc decision making in the control room considering this real-time information.
An on-site digital solution is a real opportunity to develop a functional feedback loop of operational data into the digital process twin. The on-site simulation results need to be checked for consistency, and together with the experience of running the digital process twin can loop back into the simulation and design modules, which form the core of the digital twin. This will result in more accurate and highly dependable unit model libraries for the relevant key process equipment of the sulphuric acid plant over time.
In addition to providing the data for ad-hoc local operational decision-making support, calculated and simulated information can be very valuable for longer-term analysis and optimisation purposes.
Data integration and longer term plant evaluation
While the previous chapter highlighted the use of ad-hoc information within the daily operation, another major impact of digitalisation in general, and a digital process twin in particular, is the benefit for longer term operational data evaluation. It is highly recommended that such enriched information from the digital process twin is integrated into a higher level data storage system – these systems are commonly referred to as a data historian, or more recently as a data lake. Typically, operating companies use data historian systems for storing production data and making the data available to various user groups. Integration of equipment-specific model calculation results have been discussed in significantly more detail elsewhere3 . Therefore, this article shall review only the major aspects of data and information integration and what the longer term evaluation offers to the operating company.
The essence of the earlier publication is that a digital transformation within the process industry requires a collaborative effort amongst various stakeholders. A plant designer as a single player cannot provide all the necessary solutions on enterprise level. Vice versa, a provider of data-based solutions on the highest level, enterprise- or site-level, lacks the details on the equipment or the process plant level. At the equipment level, digital process twins or process simulations offer insights into the details of the process operation, which would remain hidden without digitalisation effort on a very detailed technical basis.
Data collected from equipment or a plant-level digital solution is integrated into a plant or enterprise-wide solution and the key factor is the sharing of data with higher level systems. These solutions collect and synchronise data of various kinds (for example, operational and maintenance data) and together with enriched data calculated by the digital process twin of the plant, a plant section, or an individual piece of equipment. These various layers of digital solutions make data accessible to various stakeholders of the operating plant. Such information can then be utilised, for example, for longer-term analysis of the plant or equipment performance over time, as well as its potential optimisation. The vertical integration of data from different detail levels is visualised in Fig. 4.
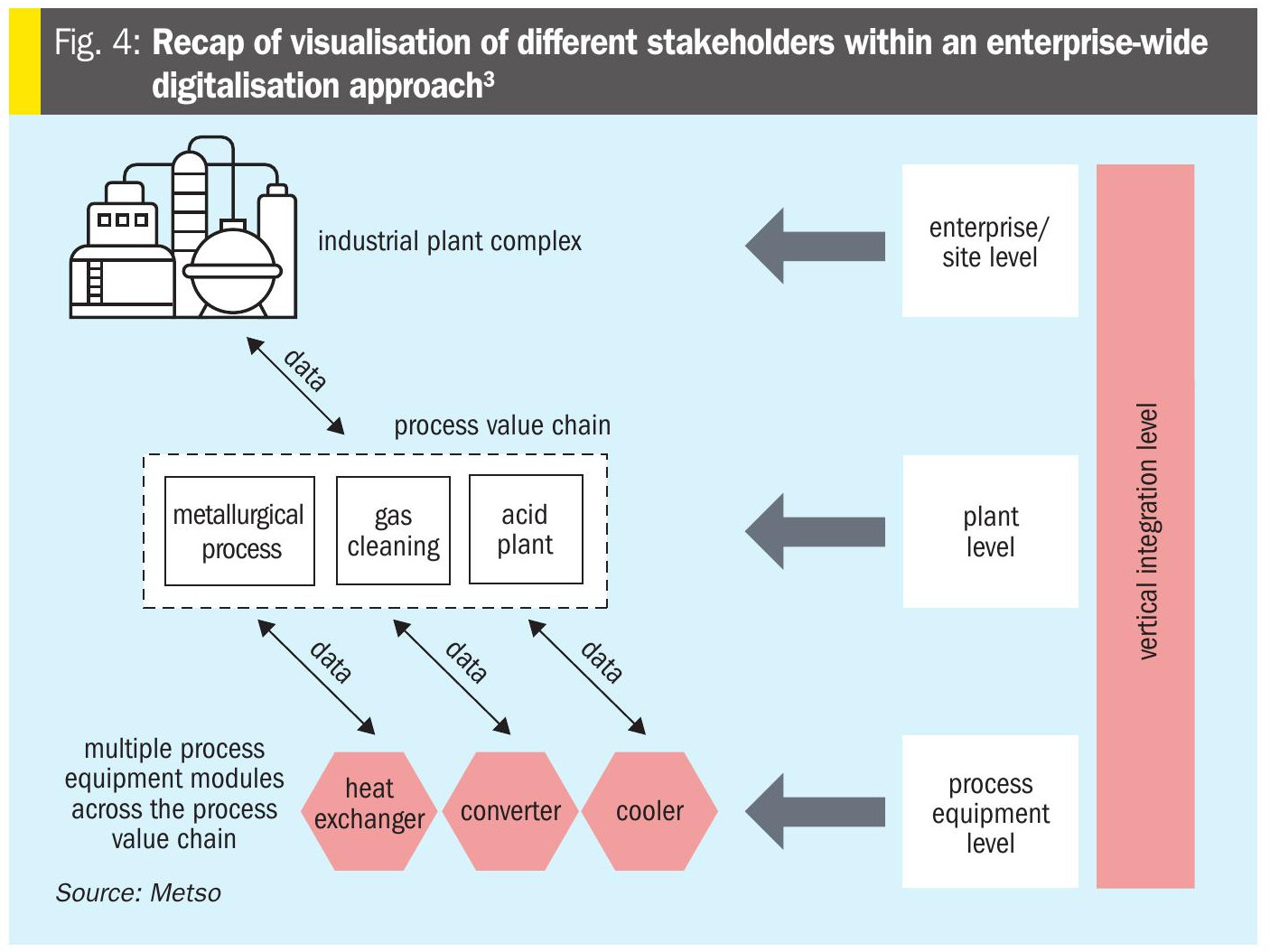
Returning to the heat-exchanger example from earlier, such equipment shows efficiency degradation over a longer period in a sulphuric acid plant. Such degradation does not generally occur within days or weeks, rather within months or, more commonly, years. This means, the operating personnel typically have no visibility on the health status of the heat exchanger, if the equipment is operating within the limits of the plant control system warning/ alarm system. Very slow process effects, such as fouling of the heat exchanger, are more than likely remaining ‘unrecorded’. That said, such health status information would be very valuable for on-site maintenance teams for better shutdown planning activities based on actual status, rather than empirical knowledge.
The physical and thermodynamic model of the equipment, in this case the heat exchanger, provides such information on a continuous basis via the digital process twin. It should be noted that a fouling coefficient will not be used on an ad-hoc analysis, rather the information will be trended and evaluated over a longer period to be able to visualise the degradation of the heat exchanger. Information is thus available to the operational or maintenance team via an interpretation of the longer-term behaviour, or via a threshold on a parameter calculated within the digital process twin.
An example trend for a fouling development in a heat exchanger is visualised in Fig. 5, showing artificial but representative data. The fouling factor itself is calculated via the digital process twin. Nevertheless, a certain noise level within the calculated signal is expected in a real-world example, originating from the noise of the algorithm input data, such as temperatures, pressures, etc. It is worth mentioning, that any mismeasurement in the process can lead to noisy data when applying a simulation based digital process twin. Thus, a linear trendline is added to simplify the analysis. This trend can now be used for an easy interpretation of the digital process twin calculations for the respective operational and maintenance teams.
The heat exchanger is only a generic example within the gas cleaning and/or sulphuric acid plant configuration, but further digital solution use cases, which are based on the digital process twin calculations, are available and currently under implementation. In addition, mathematical optimisation algorithms are based on the results of the digital process twin simulation. In terms of information integration into the longer-term databases or data lake, basically all calculated information can be made available and stored for longer-term analysis. It should also be noted that the near-future machine learning algorithms are expected to benefit from such information that emanates from the digital process twin.
Closing of the feedback loop via on-site digital solution operation to the simulation basis within the digital process twin is very important. The longer term availability of information offers an opportunity for in-depth and very accurate model review and in so doing, the digital process twin will be inevitably improved over time. This will allow for a continuous improvement of the simulation accuracy and increase the predictability of process operational changes, or of the reliability of the monitoring algorithms. The operating company will ultimately profit from a more accurate digital process twin, if integrated into the on-site process operation.
Digital process twin solution in reporting
All data, directly measured or digital process twin enriched, can be utilised in reporting and many different reporting tools are available on the market. Most operating companies have their own reporting tools in operation, handling key operational KPIs, such as production rate or emission levels. These KPIs and the associated reporting are relatively easy to configure and will not require a digital process twin.
The addition of the digital process twin within the digital solution can be seen as a toolkit for further, in-depth process reporting. Insights, otherwise hidden, can therefore be added to existing reporting systems. To give a few examples, a process engineer could be interested in calculated information over a specific period, such as the conversion rates in the respective converter bed, or the aforementioned fouling factor in heat exchangers. The combination of the digital process twin with longer-term trending or reporting systems makes the data instantaneously available and there is no need for an on-site process engineer to perform time consuming manual modelling exercises.
The result of such a simulation model calculation is continuously available via the digital process twin and is stored in the respective database and therefore historically results from process calculations are available instantaneously. It is expected that such an approach can significantly reduce the time required to perform a detailed analysis of a certain event or a certain process plant behaviour. The digital process twin therefore ensures that the information basis for such an analysis is comprehensive for any required investigation.
With respect to reporting, many operating companies utilise periodical reporting to various stakeholders in the organisation and the configuration of such reports is today easily compiled and tailored to specific user group needs. For example, a high-level management report is more focussed on overall KPIs, such as production rate, plant availability, or emission KPIs, whereas operational teams are more interested in the process details, such as information that is calculated via the simulation model.
Conclusions
Metso has identified the digital process twin as a key component in the success of digital solutions for sulphuric acid plants and acknowledges that the role of legacy simulation models has evolved into the first-generation digital process twin of today. Although the digital process twin should not be considered as a stand-alone tool, it is a support tool for further benefits.
In other words, apart from using high-fidelity simulation modules for the key process equipment during the plant design process, the digital process twin is the central element within a multitude of digital solutions.
Monitoring algorithms and optimisation solutions are based on the integrated digital process twin. As an example, heat exchanger monitoring can benefit from the digital twin since not all required instrument measurements are available. Missing information is therefore provided by the digital process twin, offering an opportunity to gain further process insights into the plant and equipment, which would otherwise remain unknown or inconclusive.
The calculated information is not only used directly within digital solution applications but also provided to higher level data historian or data-lake architectures. That means, the detail simulation on equipment level provides information, which can be ultimately valuable on the plant- or enterprise-wide reporting systems.
Finally, the opportunity to integrate deep process understanding, based on digital process twin calculations, into neutral reporting systems is expected to positively impact the plant operations in the longer term. Data analytics can be enhanced by having results from such calculations available. Combining process calculations, measured instrument data, and key operational KPIs into a user-specific reporting solution will maximise the understanding of operations and allow well-informed operating plant decision making to take place.
References