Nitrogen+Syngas 396 Jul-Aug 2025
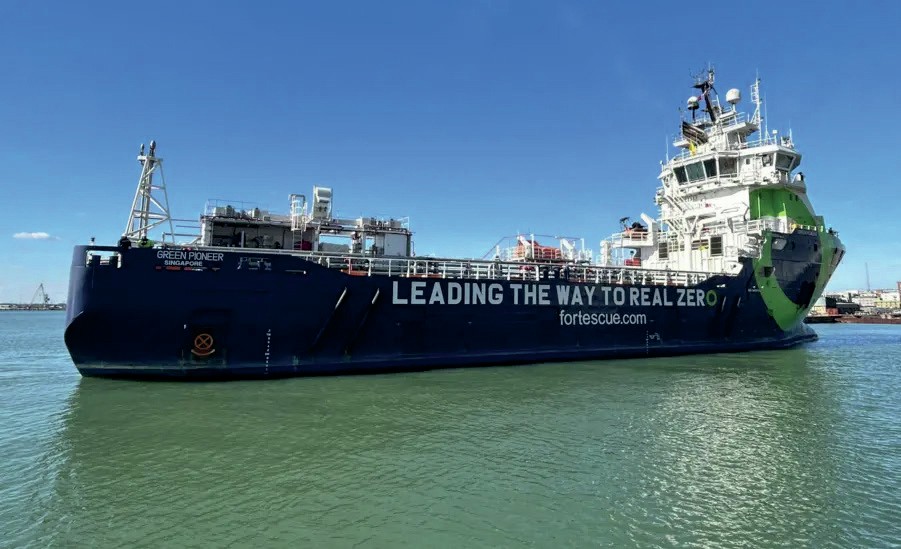
15 July 2025
Ammonia safety update
SAFETY
Ammonia safety update
As well as a recent US Chemical Safety Board report on an ammonia release incident, the past year has seen considerable focus on safety of ammonia at sea, in preparation for its possible use as a clean burning maritime fuel.
Ammonia is the second largest chemical produced worldwide by tonnage after sulphuric acid – approximately 200 million tonnes in 2024. While its toxic properties are well known and characterised, the sheer volume of ammonia being produced and used worldwide means that safety incidents regrettably continue to occur, and safe handling of ammonia remains an important topic for the industry. This article looks at some of the developments in ammonia safety in the past year.
CSB report on ammonia release
In November 2024 the US Chemical Safety and Hazard Investigation Board (CSB) issued its interim report on an ammonia release which occurred at Cuisine Solutions in Sterling, Virginia on July 31st 2024. At the time of the incident, 286 personnel, which included employees and contractors, were on site. The company, producing packaged foods, had an ammonia refrigeration system to control chilled water temperature in its processes and to operate freezers and food storage areas. Emergency pressure relief valves, set at 300 psi, protected the heat exchangers and associated equipment from excess pressure conditions, and discharged ammonia to the atmosphere.
At about 8:20pm personnel located in a cafeteria and break area inside the building and adjacent to the release point identified and reported an ammonia odour. An emergency pressure relief valve had discharged ammonia from a release valve horizontally near the roof of the building and formed a white cloud of ammonia vapour which was partially visible outside the emergency exit door for this area, on the west side of the building. Accordingly, the site manager directed all personnel to evacuate the building via the opposite (east) side of the building. However, some personnel unwittingly exited the building near or into the ammonia cloud and were exposed to ammonia vapour. Four workers were admitted to local hospitals, including one to intensive care. Fortunately there were no fatalities. Cuisine Solutions reported that approximately 170 pounds (77kg) of anhydrous ammonia were released. The three-way valve to isolate the emergency pressure relief valve was turned to stop the release by approximately 9:30 pm with the assistance of emergency services.
The CSB says that it is continuing to gather facts and analyse several key areas for its final report, including: potential causes of the ammonia emergency pressure relief valve opening; the total quantity of ammonia released; Cuisine Solutions’ emergency action plan for an ammonia release, and its process safety management and risk management programs and policies; and general codes and standards for ammonia refrigeration systems.
Maritime ammonia safety
Recent updates in ammonia safety have focused on enhancing guidelines for using ammonia as a marine fuel, particularly for ships. The International Maritime Organisation (IMO) has recently (March 2025) released interim guidelines and says that it is working towards finalising comprehensive safety standards, including those for ships using low-flashpoint fuels like ammonia. The IMO’s Maritime Safety Committee (MSC) approved the guidelines in December 2024, following their development and finalisation by the Sub-Committee on Carriage of Cargoes and Containers (CCC) in September 2024.
The interim guidelines provide a goal- and function-based safety framework covering ship design, equipment, operations, bunkering, toxicity mitigation, and crew protection. While the guidelines are nonmandatory, they align closely with the IGF Code and SOLAS (Safety Of Life At Sea) principles. The guidelines aim to ensure that ammonia-fuelled systems offer at least the same level of safety and reliability as conventional oil-fuelled machinery, recognising ammonia’s specific hazards, including high toxicity, potential for explosive atmospheres, and material compatibility challenges. They encourage early uptake while noting that further refinements will be necessary as operational experience is gained, particularly in relation to toxicity controls and emergency systems.
EMSA
The European Maritime Safety Agency (EMSA) published its own comprehensive study on ammonia as a shipping fuel in July 2024. The two-part study first detailed an extensive analysis of ammonia properties and characteristics and how these are applicable as marine fuel. The second focused on potential areas of a vessel where hazards might arise.
The main hazard of ammonia in comparison to other conventional and alternatives fuels is of course its toxicity, but a secondary concern is its corrosive nature and the potential for stress corrosion cracking of metalwork. Toxicity of ammonia adds complexity to ship designs based on ship-specific gas dispersion analyses supported by relevant risk assessment covering several scenarios (e.g. loss of containment from storage tank or piping, during bunkering etc.).
An analysis for PPE requirements and standards was conducted. It should be ensured that suitable protective equipment is provided for persons on board, for both routine operations and emergency conditions. Experience from land-based industry shows that the choice of PPE in different areas is subject to the expected concentration and exposure time to ammonia therefore different chemical suits and accessories may be required. Toxic areas determination as described above is a critical step to decide what PPE will be used for each space onboard.
As regards ship-specific hazards, the report considered internal combustion engines (ICEs) and the ammonia engine fuel system, and then how that related to the engine fuel oil system, common engine components, engine auxiliary systems, hydraulic and sealing oil systems, the fuel supply and recirculation system, bunkering and reliquefaction plants. A workshop with engine vendors’ experts was conducted to validate components selected for the fault tree analysis (FTA) in a hierarchical structure. These potential points of failure are detailed in the report. Out of the eight subsystems mentioned above, the fuel supply system was determined to have the shortest mean time to failure (MTTF) at 9,406 hours, as it is a more complex system which has more failure modes, contributing to a higher failure rate, and the report recommends that effort should be taken to plan for control measures and improving design failures, such as valves leaking due to incorrect gasket material selection.
Ammonia spills at sea
The American Chemical Society (ACS) also published a paper in September last year covering risk assessments of ammonia fuelled ships and the consequences for human health of ammonia releases from damaged fuel storage tanks. This research focused on the effects of accidental ammonia releases during ship-to-ship collisions, affecting ammonia tank integrity, considering factors like tank types and locations, breach sizes and positions, weather conditions, and dispersion patterns, using PHAST software for modelling. The results indicated that semi-pressurised tanks pose greater health risks on human health than fully refrigerated ones. Underwater releases are less hazardous, as a significant amount of ammonia dissolves before surfacing. Mitigation efforts, such as water curtains and containment basins, were evaluated for their effectiveness in minimising the impact of ammonia releases. These measures significantly reduce risks to nearby populations but are less effective for crew safety onboard. This underscores the challenge of ensuring onboard safety in ammonia-fuelled vessels, highlighting the need for innovative and effective safety design.
The report formed part of the basis of a report by the International Tanker Owners Pollution Federation (ITOPF) highlighting the distinct nature of claims arising from ammonia spills compared to traditional oil spills, and on the unique impacts associated with ammonia’s toxicity and reactivity. As noted above, when spilled into the marine environment above the waterline, part of the liquid ammonia rapidly boils, releasing ammonia vapours. The ammonia that comes into contact with water will dissolve, with part of it also evaporating. For large surface spills, approximately 60% of the spilled volume would dissolve, with the remaining ammonia evaporating. This evaporation/dissolution ratio remains consistent when spilled underwater at shallow depths. However, if the spill occurs at depths less than 2 meters, the quantity of vapours produced and lost to the atmosphere may decrease to between 5% and 15% of the spill volume. When spilled in large quantities, ammonia vapours will absorb moisture from the air, forming a dense white cloud of ammonium hydroxide (NH4OH) that can travel laterally for several hundred meters, particularly in high wind conditions. As ammonia vapour temperatures increase to ambient conditions, they become less dense than air and will dissipate into the atmosphere.
Ammonia that dissolves in seawater will form a corrosive, caustic solution of NH4OH, which is less dense than seawater and will form a layer on the water’s surface. The violent reaction between ammonia and water is exothermic, leading to a localised temperature increase on the water surface. The concentrations and elevated temperatures will decrease with distance from the incident location. The rate at which the ammonium hydroxide plume disperses depends on the intensity of mixing in the aquatic environment, which is influenced by tidal currents and wind-induced wave action. A release in high-energy open water will disperse more rapidly than one in a sheltered port or inland waterway.
ITOPF’s analysis highlights how storage conditions influence the nature of ammonia release, either as a boiling pool on water, producing a mix of vapor and liquid, or a flash release creating a toxic cloud.
Focus on shipping
The focus on ammonia safety at sea is increasing. Classification society DNV published guidelines in May 2025 in collaboration with industry partners such as Yara Clean Ammonia, to promulgate new recommended practices that offer a clear framework for the safe use of ammonia as fuel. Laurent Ruhlmann, HESQ Vice President, Yara Clean Ammonia, puts it like this: “While ammonia presents certain challenges, shipowners and operators can confidently integrate it into their operations by implementing structured safety protocols, clear regulatory guidance and comprehensive crew training. Seafarers must receive ammonia-specific instruction, covering safe handling, emergency response and maintenance procedures. Regular simulated emergency drills and credible scenario-based training should also become standard practice to ensure operational safety and preparedness.”