Sulphur 418 May-Jun 2025

2 May 2025
SRU energy and cost optimisation
PLANT MONITORING
SRU energy and cost optimisation
Together with Slovnaft, Worley Comprimo has developed a near real-time monitoring dashboard using data sharing via the Cloud. Using a two-year data set containing minute average data, trends and insights were used to optimise performance. This paper describes the main learnings and improvements with respect to energy optimisation, which supports sustainability targets for Slovnaft.
Energy saving is an important topic in achieving the net-zero strategy to limit global warming. But next to global warming, using less energy in conversion and separation processes in refineries and gas plants also means direct cost savings in utility consumption and costs for emitting CO2 as regulated for example in the European Unit – Emission Trading Scheme (EU-ETS).
The main energy consumer in an SRU is the incinerator. Minimising the fuel gas consumption in the incinerator as needed to just comply to the environmental permit could have the largest energy saving. But also, other no-cost measures to reduce energy consumption must be explored, e.g. feasibility of reducing the reactor inlet temperatures or the necessity of co-firing in case the temperature readings in the main combustion chamber are below e.g. 1,250°C for ammonia destruction or below 1,050°C for BTEX destruction. Although the total energy consumed by an SRU is only minor compared to the whole site, every easy win, even if it’s small, must be pursued.
But apart from direct energy saving opportunities, this article also discusses opportunities to save costs by extending the lifetime of the catalyst using the latest monitoring capabilities by data sharing technologies and technical services offerings by subject matter experts (SME).
To enable the in-depth analysis of the energy consumption savings and extending the catalyst lifetime, Slovnaft and Worley Comprimo have worked together on a data sharing platform. By sharing the data near real-time, the Worley Comprimo SME gets familiar with how the SRUs are operated in normal plant load, but also during turndown and special operating scenarios. This is needed to find the opportunities to improve the performance and for Slovnaft being best in class.
This article starts with the journey to develop a data sharing infrastructure that is then used as the basis for identifying opportunities to monitor and improve SRU performance based on the shared data. A couple of examples are provided related to energy savings.
Historical background
Slovnaft is a refining company in Bratislava, Slovakia, and part of the MOL group. Worley Comprimo is a licensor of sulphur technologies and part of the Worley group. Slovnaft and Worley Comprimo have had an excellent working relationship that has lasted for several decades. In 2017 a technical service agreement was signed meaning that Worley Comprimo would do a yearly review of the performance of the units in the sulphur complex, consisting of two identical sulphur recovery units (SRU), two amine regenerator units (ARU) and two sour water stripper units (SWS). As part of the assessment, the historical data of most of the instruments in the different units was collected in hourly average values and downloaded in a large Excel sheet. The Excel sheet was shared by email, and it took the assigned technology specialist weeks to prepare all the trends, set-up the calculations of the key performance indicators (KPI) and make the analysis for each unit.
The second year, the exercise went a little faster, but still manipulating the large sets of data was quite cumbersome in Excel. Also, the unit engineer in Slovnaft was not in favour of the yearly trouble to download and configure the data from the historian. Therefore, other means than Excel and email for sharing data were explored. The cloud technology was rapidly developing and after several attempts, in 2021, the right set of people and the best available cloud environment came together successfully. And as of May 2022, the data sharing was running stable, plant data from the instruments was shared by Slovnaft to Worley Comprimo and the KPI and virtual analyser data was shared by Worley Comprimo to Slovnaft. A virtual analyser means that the value of an analyser or instrument is calculated based on other measurements. For example, the temperature rise in the Selective Oxidation (SelOx) reactor is related to the H2S concentration at the SelOx reactor inlet. The calculated temperature rise, reactor inlet temperature minus bottom bed temperature, is a measure of the H2S concentration and the calculated H2S concentration can be compared with the actual measured H2S concentration from the tail gas analyser.
Using streaming data via the cloud, much more data can be exchanged, and the optimum time interval was set at minute average data to follow fast changing trends of flow rates and H2S concentrations that can result in trips in the unit. The delay of data transfer was optimised to about 5 to 10 minutes, so near-real time, which provides adequate assistance of a Worley Comprimo SME in case immediate trouble shooting assistance would be required.
Architectural overview
It took quite some time to develop the right IT infrastructure with people who have the appropriate skill-set, mindset and system knowledge of the different disciplines. The historian vendor, in the case of Slovnaft, OSI-PI, which is part of the AVEVA group, and the Microsoft Azure consultant worked together closely with the MOL IT and Worley IT departments. The schematic overview of the IT architecture as it is in use today is provided in Fig. 1. It shows at a high level the components used to share data in a cyber secured way, that was adopted by both IT organisations.
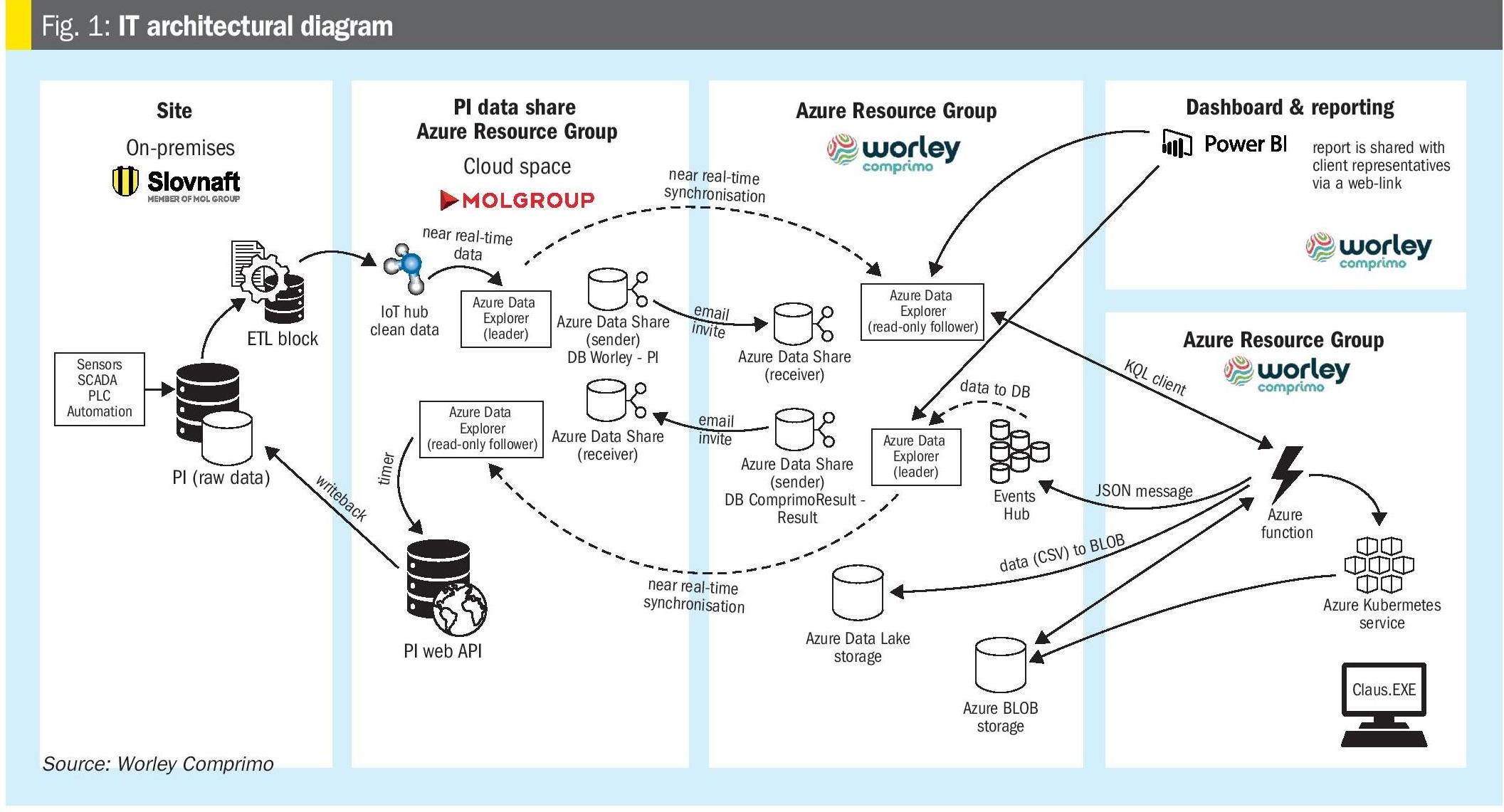
On the left side of Fig. 1, the data from the sensors is collected in the historian database. The data from this data historian is then uploaded to the cloud database, Azure Data Explorer (ADX), which is well suited to process streaming data. The ADX environment of Worley has many different databases, for different clients and per client there is a historian database and a result database which are both used for visualisation of the dashboard in PowerBI. The result database is shared with Slovnaft, for accessing the KPI and virtual analyser data points.
The time delay is about five minutes. Only a defined subset of the data as needed for the sulphur complex is then shared for view only with the Worley ADX via a secured email invite within the same cloud region. Using an Azure Function which is triggered every five minutes, a set of subroutines in Python code is carried out, which include the following sequence of actions:
- Read data from read-only ADX database, which contains the data from the data historian.
- Add/delete records in new time stamp queue. New time stamps are added to a table that lists all time stamps that need to be processed. In case a time stamp is available in the Worley ADX, it was already processed, and the time stamp in the table will be deleted. Send to ADX, historian database.
• Data processing by selecting the time stamps from the table that need to be processed. Read data from read-only ADX database.
- Add/delete records in data processing time stamp queue. This table keeps the overview of the time stamps that are new brought in for processing and keeps track of the time stamps that are in progress. Once the processing is finished, the time stamp in the table will be deleted. Calculate the KPIs.
• Simulate using a sub-set of the sensor data.
• Send to ADX, Result database.
• Save CSV to datalake (BLOB storage container)
Monitoring and performance improvement
Data sharing and processing has been in production since May 2022. Since then, quarterly reports have been prepared and discussed in regular calls with the unit engineer of Slovnaft and the SME of Worley Comprimo. And based on the observations, a good understanding of the operating philosophy was obtained and advice was provided on e.g. improving the sulphur recovery efficiency (SRE) for aged catalyst. After more than a year of monitoring and optimisation, it was time to prove the added value of Comprimo Insight as a data sharing and dashboard service to save cost. Slovnaft indicated their interest in saving energy and therefore, it was decided to study natural gas savings in the SRUs. The points where natural gas is consumed are indicated in the SRU schematic overview of Fig. 2.
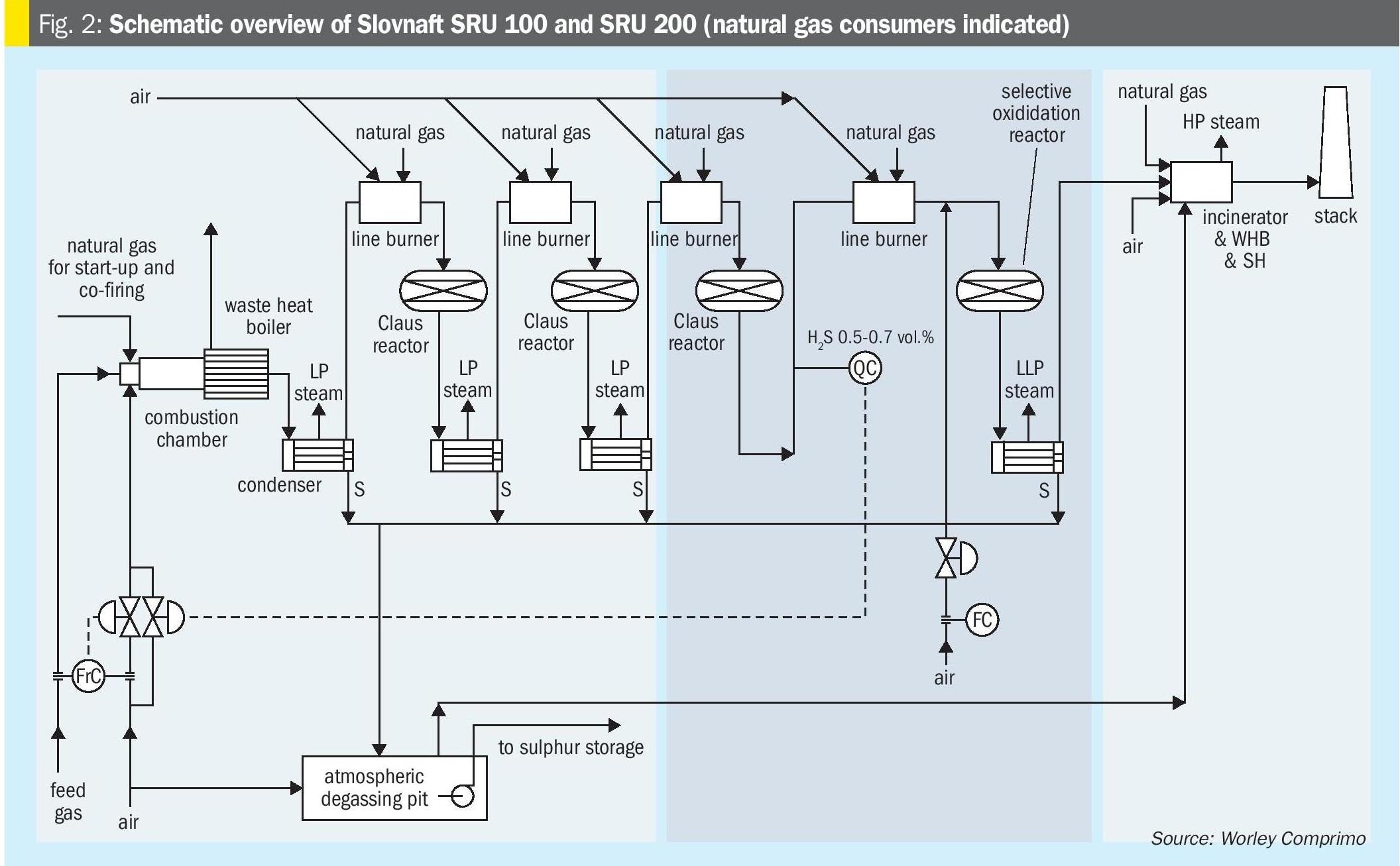
The main natural gas consumer in normal operations is the incinerator, so the main savings can be expected there. However, lowering the reactor inlet temperatures can also provide an interesting contribution without spending money or reviewing the operating procedures for the necessity of co-firing.
Natural gas saving potential in the incinerator
The incinerator is the largest natural gas consumer in an SRU. Operating at the right conditions to balance destruction requirements at minimum fuel is covered in Ref. 1. For Slovnaft the only requirement is that the H2 S concentration is less than 10 ppmv in the stack as measured by the CEMS. Although the oxygen concentration in the flue gas is occasionally higher than 3 vol-%, by having the dashboard and regular unit review, operations is aware to target the oxygen concentration between 2 to 3 vol-%.
The heat recovery, consisting of a waste heat boiler followed by a superheater, downstream of the incinerator needs adequate attention. Generally, a site steam boiler is much more efficient and provides better heat recovery than an incinerator heat recovery system. Slovnaft experiences limitations in the superheater, because the waste heat boiler takes up too much duty. A superheater directly after the incinerator followed by a waste heat boiler is more expensive due to a higher design pressure and more exotic material, resistant to high temperatures, but assures sufficient superheat.
The temperature in the incinerator chamber is strictly controlled at 750°C, so there are no other datapoints at other temperatures than 750°C. To quantify the potential savings of natural gas for the incinerator and to compare actual savings in the future, a baseline consumption was established from the large amount of data available. But to keep the dataset manageable, the data was averaged per day for the variables that were assumed to correlate with the natural gas consumption. Especially the plant load was the main parameter. During normal operation, the SRUs run at a plant load between 78% and 86% most of the time. Below 60% plant load, natural gas co-firing is started in the thermal reactor. Therefore, all days with a plant load below 60% were left out of the working dataset. The correlation between the daily average natural gas flow versus the plant load is shown in Fig. 3. Notably, the natural gas consumption in SRU 100 is higher than for SRU 200 at the same plant loads.
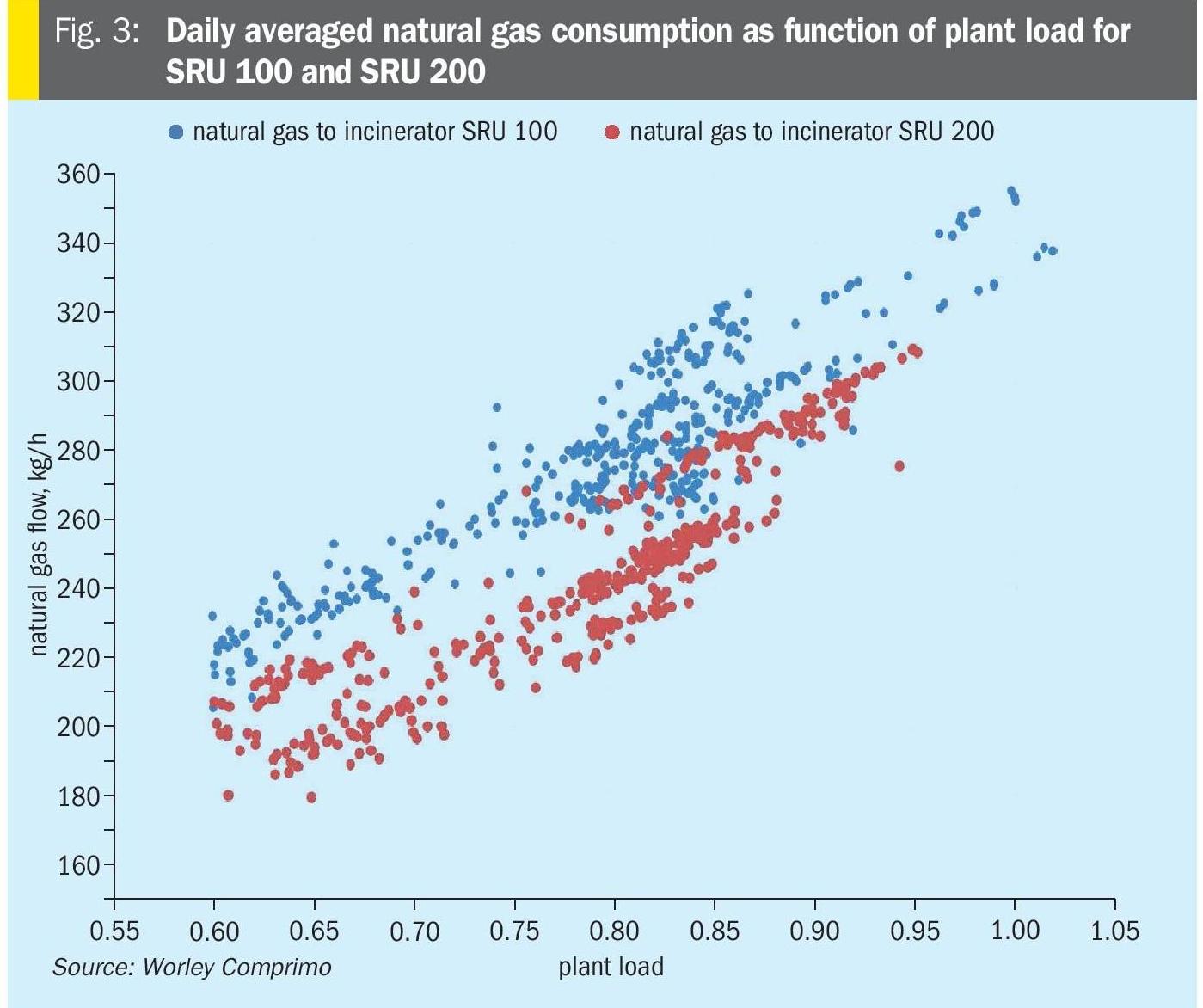
For SRU 100, Temperature 2 is very close to the control temperature of 750°C, while for SRU 200, the Temperature 2 is slightly lower. This difference in temperature is supported by the temperatures measured at the outlet in the incinerator WHB.
The base lines for the Incinerators of SRU 100 and SRU 200 for different plant loads are shown in Fig. 4. SRU 100 consumes about 25 kg/h more natural gas than SRU 200. It should be evaluated if the temperature in the incinerator of SRU 100 can be reduced to the same performance as for SRU 200.
The incinerator temperature could be reduced as low as 650°C for an adequate conversion of sulphur species into SO2 . In case of low frequency vibration noise produced by the incinerators, reducing the temperature in the incinerators could also result in a reduction of the low frequency noise. Reducing the temperature also reduces the combustion air flow rate considerably, which in case of noise issues is the main factor in the vibration of the incinerator burners.
However, a low incinerator temperature will have a direct impact on the steam superheat temperature at the battery limit. The minimum required high pressure steam temperature at the refinery grid is 300°C to prevent the risk of condensate droplets in the steam turbines. Therefore, a reduction in incinerator temperature may not be feasible in the current line-up and operation.
Several options can be considered to reduce the natural gas consumption in the incinerators, which also need to be balanced against requirements in the high-pressure steam super-heat temperature and high-pressure steam capacity for the whole refinery:
• The super-heat requirement can be dropped if the saturated steam will be routed directly to steam heaters in a nearby unit.
• Install electrical heater to superheat the high-pressure steam further.
- Replace existing incinerator WHB with a shorter one or even leave out the WHB and replace the superheater. This will result in less heat transfer in the WHB and sufficient duty for the superheater to reach the required grid temperature. In case of the option without a WHB, a de-superheater may be necessary.
- Increase the flue gas temperature downstream of the incinerator WHB and reduce the steam flow to the superheater by plugging tubes in the waste heat boilers. This option was studied, but plugging tubes results in an increased process gas flow and hence improved heat transfer. Therefore, the steam production is reduced only marginally, and the high-pressure steam superheat improvement was negligible. Increasing the gas flow was limited to a maximum velocity of 120 m/s, to prevent equipment damage due to vibration issues in the WHB.
A remarkable difference was found between simulation and plant data for the incinerator. Where SRU 100 uses only 279 kg/h natural gas and about 7700 kg/h combustion air at 80% plant load to achieve 750°C temperature, the simulation shows 379 kg/h natural gas and 9,637 kg/h combustion air. This could mean that the simulation assumes more heat losses than actual or the plant data for flow rates or temperatures are not correct.
Based on the relative difference of natural gas consumption for the incinerator from the simulation, a saving of 60 kg/h per unit of natural gas is expected in case the incinerator temperature could be dropped to 650°C.
With an assumed price of €0.40 per Nm3 natural gas and €74 per tonne CO2 emission, the total saving could be as high as €800,000 per year. A test is recommended where all turbine positions will be switched to electrical, and the incinerator is gradually reduced in temperature until 650°C without adverse effects.
Can we lower the reactor inlet temperatures to save energy?
As part of a licensor package, a heat and material balance and an operating manual is provided specifying the reactor inlet temperatures. For most clients these inlet temperature setpoints are fixed and not to be changed. Also, for Slovnaft, the setpoint range for the DCS operator is limited to 5°C below the value in the operating manual. But to find the minimum energy consumption, some more margin in the ranges can be beneficial. On the other hand, experimenting with the SRU also requires sufficient basic understanding for the process, because there are potential negative effects on the overall unit performance.
Inlet temperature 1st Claus reactor
The bottom bed temperature from the first reactor needs to be sufficiently high for COS and CS2 conversion. Typically, the bottom bed temperature must be maintained between 290°C to 310°C. The bottom bed temperatures during normal operation for Slovnaft are between 305°C to 310°C. Therefore, it was proposed to decrease the inlet temperature setpoint of the first Claus reactor from 240°C to 235°C. When reducing the temperature, the emissions must be monitored. A lower bottom bed temperature may result in slightly more COS and CS2 slip, which can be detected indirectly via the continuous emissions monitoring systems (CEMS) in the stack gas.
Reducing the inlet temperature to the first reactor will still provide ample margin to the sulphur dewpoint. A 10°C margin to the sulphur dewpoint is considered as sufficient. If the hydrocarbon content in the acid gas is very low and with that minimum CS2 formation, the first Claus reactor inlet temperature can be reduced further, which is favourable for the Claus equilibrium.
Inlet temperature 2nd Claus reactor
It is also recommended to test the second Claus reactor for an inlet temperature reduction of 5°C, from 210°C to 205°C. For the second reactor, only the consideration of the sulphur dewpoint is to be taken into account, but during normal operation sufficient margin is assured.
Inlet temperature 3rd Claus reactor
The third Claus reactor inlet temperature is currently set at 190°C. In case the inlet temperature is reduced to 180°C, the margin to the sulphur dewpoint would still be 6°C. Although a margin of 10°C is recommended and on the safe side of operation, 6°C margin can also be accepted.
Apart from saving natural gas, according to the theory, the recovery efficiency of the SRU is also expected to improve. The Claus equilibrium shifts towards sulphur and water at lower reaction temperature. When keeping the H2S setpoint at the SelOx inlet constant, the SO2 is further reduced. Especially for aged catalyst, this setpoint change could have a notable impact on the SO2 measured in the stack. Note however, that in case the third Claus reactor is kinetically limited, there is also the possibility that a temperature decrease will not result in a better recovery.
Inlet temperature SelOx reactor
The SelOx inlet temperature is controlled at 215°C. Lowering the temperature may have a direct negative impact on the yield. In a 3+1 SUPERCLAUS® configuration as in Slovnaft, the normal operating setpoint for the H2 S setpoint in the tail gas is 0.5 mol- %. However, increasing the setpoint to 0.6 mol-% generates more heat and depending on the catalyst activity, the temperature setpoint could be reduced by 5°C to achieve a comparable reactor yield.
Testing the reduction of the reactor inlet temperatures
A test was done to verify the potential natural gas saving by just reducing the reactor inlet setpoints for the three Claus reactors with 5°C. The third Claus reactor inlet temperature was reduced first, then the first Claus reactor and the second reactor last. In Fig. 5 the inlet temperature trends of the test are provided. It was not possible to extend the test to the SelOx reactor, also because the H2S setpoint was at its maximum range, being 0.60 mol-%, according to the operating instructions.
Each setpoint change was followed by a couple of hours to stabilise the SRU and verify the effect on the SO2 in the flue gas from the stack, which is trended in Fig. 6. The SRU was running stable, except for a short peak in the sour water acid gas flow rate at 11:30. The H2S concentration dropped in the tail gas dropped as the feedback controller in the Advanced Burner Control (ABC) system needs time to compensate with the combustion air flow rate for this sudden change. As a result via the Claus equilibrium, the SO2 in the tail gas rises when the H2S drops. The SO2 is not converted in the SelOx reactor and is measured by the stack gas analyser.
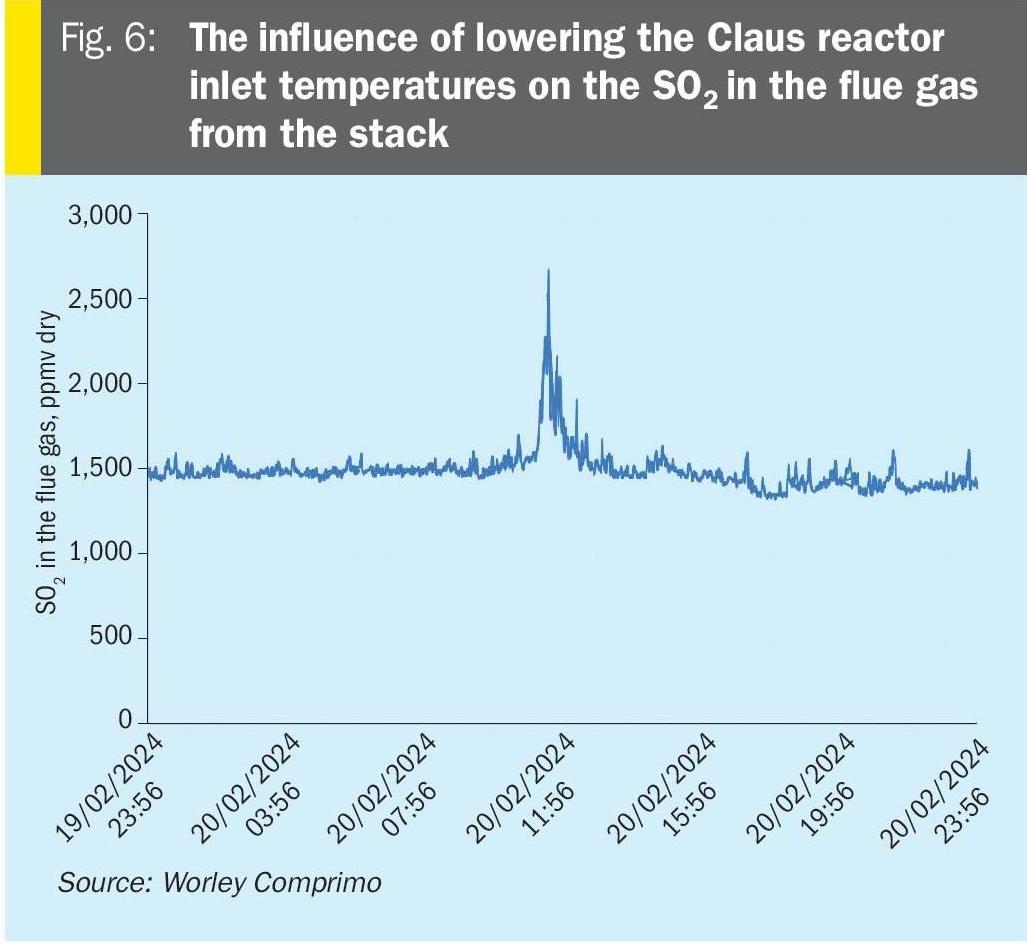
As was clear from the test, lowering the reactor inlet temperatures has no negative impact on the SRU performance, and even a positive result by a very small reduction in SO2. The next item to investigate was the natural gas savings because of a 5°C reduction. In Fig. 7 the natural gas consumed in the line burners to the three Claus reactors is trended on the primary y-axis and the plant load on the secondary y-axis.
To estimate the reduction in natural gas flow rate to the line-burners, the flow rates before, from 0:00 to 9:00, and after, from 17:00 until 0:00, the test are averaged. The result is summarised in Table 1.
It’s clear from the test that in this operating mode, reduction in inlet temperatures of the Claus reactors can be done without any investment cost, only clear operating instruction, providing a potential saving of almost 24,000 kg/ year in natural gas. This is equal to the consumption of 19 average Dutch households or about €18,000 per year natural gas and CO2 emission costs.
With the result of the test to lower the Claus reactor inlet temperatures, the next step is to update the operating instruction to the shifts. The lower setpoint range for the reactor inlet temperatures has been advised to be reduced by 5°C and awareness needs to be created to operate at lower inlet temperatures to reduce energy consumption. The DCS operator needs to understand that subdewpoint can occur at too low reactor inlet temperatures and needs to know which system parameters to monitor, such as the bottom bed temperatures, SO2 and H2S concentrations in the tail gas and the SO2 concentration in the stack flue gas.
Modelling of the natural gas consumption of the line burners
Fig. 7 shows a clear correlation of the natural gas flow rate to the line burners with the plant load and the temperature increase over the line burner. The correlation with the ambient outside temperature was tested but not found to be statistically relevant. To predict the potential savings of natural gas to the line burners, a baseline consumption was prepared from the large amount of data collected over time. But to keep the dataset manageable, the data was averaged per day for the variables that were assumed to correlate with the natural gas consumption.
Based on the linear regression trends for the individual line burners and considering the temperature increase over each line burner, a second regression was done to find the correlation between the natural gas consumption, temperature increase over each of the line burners and the plant load. This results in a straight line through three points, one for each line burner. The slope of each of those lines is also a linear correlation with the plant load. The deviation of natural gas consumption obtained from the model and as measured in the unit deviated more than 25% and therefore this model is not considered being accurate. Maybe a machine learning model could be trained and tested as the natural gas flow rates from simulation are also not all in acceptable correspondence with the measured natural gas flows.
What about co-firing?
Many operators in a refinery where sour water stripper acid gas is also processed are tempted to start co-firing if one of the temperature measurements in the main combustion chamber (MCC) is below 1,250°C. But the temperature readings of these measurements, pyrometer and thermocouple, are far from accurate. Many times, the difference in reading between those two instruments is easily over 100°C! Typical causes for this large deviation are that the instruments are very sensitive to how they are positioned and the setting of the purge flow rate. An additional reason to relax on co-firing below 1,250°C is that the industry wide accepted rule for adequate ammonia destruction to prevent plugging might not be so firm as was concluded in Ref. 2.
MCC Reliability temperature reading
A good example on the lack of accuracy of the temperature readings in the MCC is provided in Fig. 8, which shows screenshots of one of the trends in the Comprimo Insight dashboard. Both SRU trains are identical, except that SRU 200 has a combustion air preheater. Both plants are operated at equal load, around 70% of the maximum plant load, based on the maximum combustion air flow rate. Surprisingly, the temperature in the MCC of SRU 100 according to the thermocouple is higher than for SRU 200. The pyrometer in SRU 200 is about 20°C higher than in SRU 100, so the trend is credible, but still below 1,250°C, suggesting co-firing should be considered.
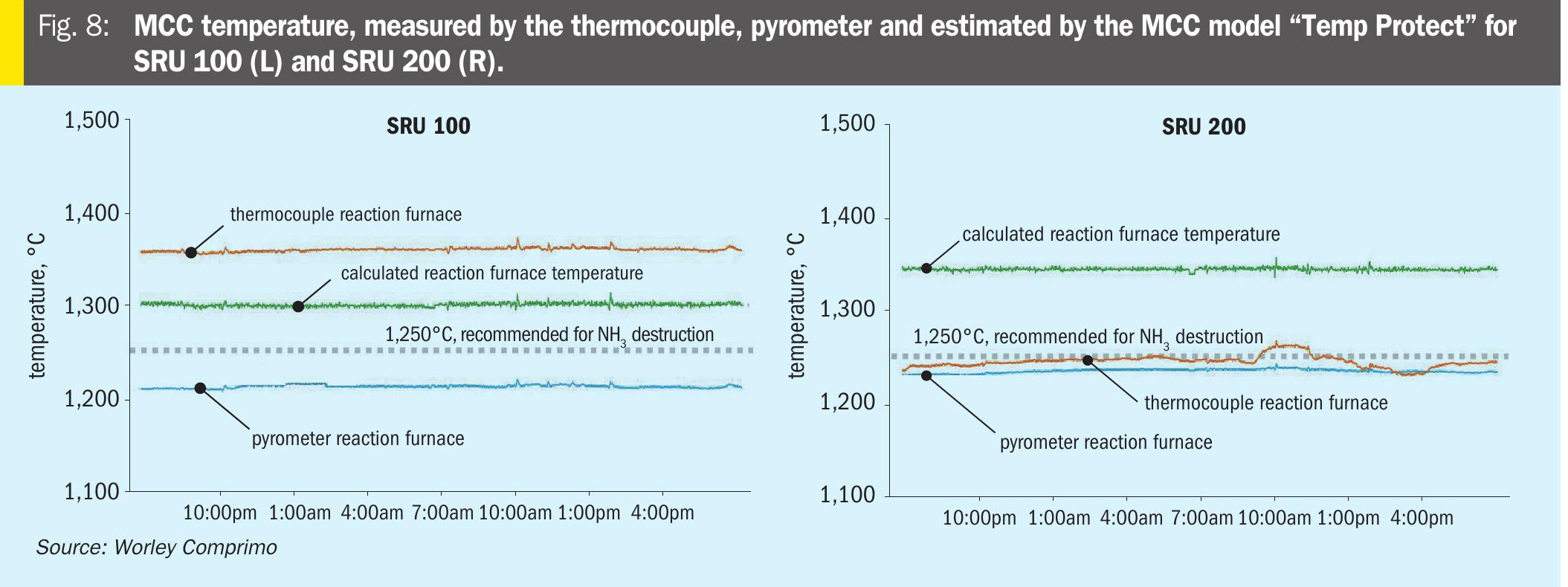
The Comprimo Insight includes a Worley Comprimo model called “Temp. Protect” to estimate the MCC temperature based on the flow rates to the main burner and an assumed feed gas composition. This model gives more credible numbers for the MCC temperature. Since the calculated and simulated data is shared back with Slovnaft, the estimated MCC temperature is configured as a DCS tag in the historian database and is therefore called a virtual analyser. And from the historian database, the calculated MCC temperature is available to operations as a third independent temperature value. A second parameter to monitor the assumed feed gas composition is the actual and expected air-to-gas ratio. If those two parameters are showing a close correspondence, the assumed feed gas composition is in accordance with the actual feed gas composition.
Review and test plant turndown to minimise co-firing
At Slovnaft, co-firing is started if the thermocouple reading is below a value of 1,250°C or in case the combustion air flow drops below a certain value, which causes instabilities in the blower controls. In case line burner flame stability issues are experienced below a turndown of 50% for example, then co-firing is a logical step. If co-firing is started because of outdated knowledge, inaccurate temperature measurement in the combustion chamber or some control issue, it could be interesting to assess if the amount and occasions of co-firing natural gas can be reduced. This can save potentially quite some natural gas and unnecessary cost.
The load on the SRUs fluctuates now adays more than in the past due to different crudes since the troubles in the neighbouring countries. Depending on the crude being processed in the refinery, co-firing takes typically 50 kg/h of natural gas during a week, so 8,400 kg of natural gas in a week. If co-firing operation is typically occurring 8 weeks per year for each unit due to low sulphur load and this operation can be prevented, then this would save €100,000 per year.
Conclusions and summary
Applying monitoring tools to share data near real-time between the operating company and the licensor, enables a knowledge exchange between the unit engineer/ operations and the Technology Specialists. Together they explore and implement optimisation opportunities.
Although the SRU is only a minor energy consumer in the whole refinery, still an interesting saving was identified for reducing the natural gas consumption in the incinerator of up to €800,000/year. However, this reduction might require some investment for this particular plant and will be first tested in practice to see if the predicted saving is achievable.
Minor reductions in natural gas consumption can be achieved in the line burner operation by reducing the reactor inlet temperatures of the three Claus reactors with 5°C. It was shown in a test that there were no negative effects on the SRU. Although this saving is relatively small, about €18,000/year, it can be implemented without spending capex and only updating operating procedures.
The last potential saving in natural gas is the co-firing. From experience, the temperature measurements in the MCC are not very accurate and having a temperature estimate from a model provides extra information if the temperature would be really too low for adequate ammonia destruction. And also, the operating instructions for co-firing below 60% plant load, which could be based on outdated insights, should be reviewed. A year of unnecessary co-firing easily adds up to €100,000 wasted money.
References
Acknowledgements
Worley Comprimo would like to acknowledge Slovnaft and especially Martin Genšor as co-author and David Kállay for arranging the approval to use Slovnaft data providing valuable learnings about SRUs to the industry.