Nitrogen+Syngas 395 May-Jun 2025
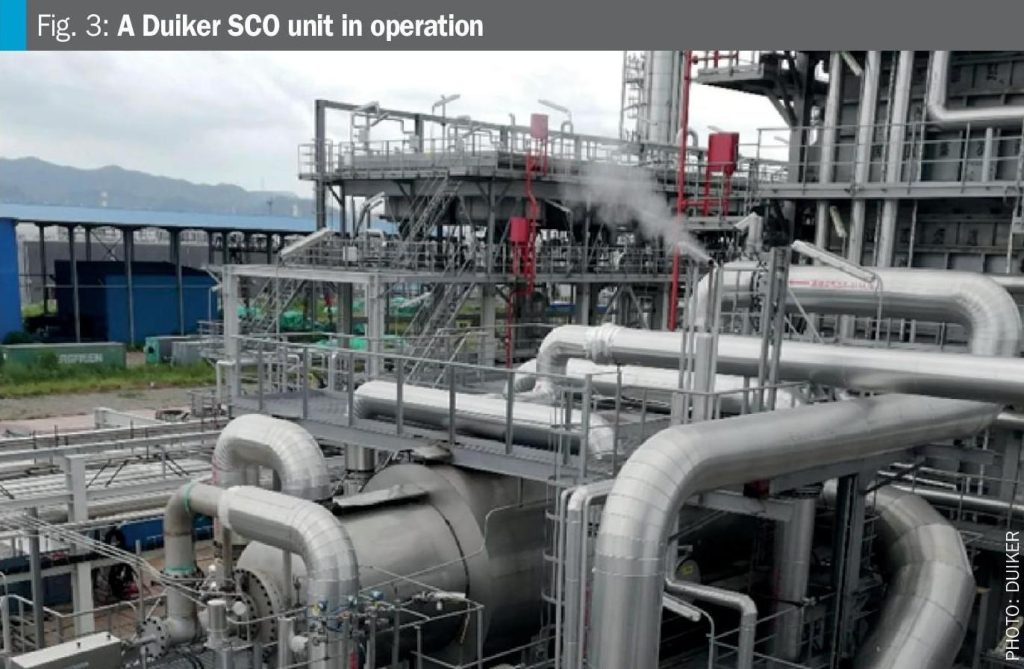
2 May 2025
Cracking confidence: Perceived risks for industrial investors
AMMONIA CRACKING
Cracking confidence: Perceived risks for industrial investors
Common risks of ammonia cracking as a new technology and how these risks can be recognised and mitigated by applying an innovative approach of the technology maturation process is described as seen through the eyes of an end user/investor. Addressing those risks is pivotal to enable end users to choose the best technology for their needs. Albert Lanser of Duiker Clean Technologies discusses some of these risks and how they have been addressed in its novel technology for producing the lowest levelised cost of hydrogen via its unique ammonia cracking process.
Pressing need in decarbonisation is pushing existing industries to search for innovative technologies. As much as innovations are exciting and inspiring, they always come at a cost and bring risks. Addressing those risks as early as possible and implementing the remedies for de-risking is essential for the successful implementation of new technology. Duiker designed its unique ammonia cracking technology following a structured approach to technology maturation. This process was based not only on Duiker’s expertise and engineering experience but also on the perspective of a future client and their view on the risks associated with implementing such innovative technology in their projects.
Ammonia cracking
In certain regions like Northwestern Europe, Japan and South Korea the demand for sustainable energy is expected to rise to large volumes in the near future; however, local wind and solar energy generation is considered insufficient. This creates the need to import sustainable energy. Ammonia plays a key role in this energy transition, especially since ammonia can be used as a carrier for hydrogen and as a fuel. Economically2,3 it is cheaper to store and transport hydrogen in the form of ammonia compared to pure hydrogen in gaseous or liquid form. To convert this ammonia back to hydrogen at or near the end-user’s location an ammonia cracking process is required.
Bearing in mind the well-known statement of Leonardo da Vinci: “Simplicity is the ultimate sophistication”, Duiker developed its design philosophy as shown in Fig. 1.
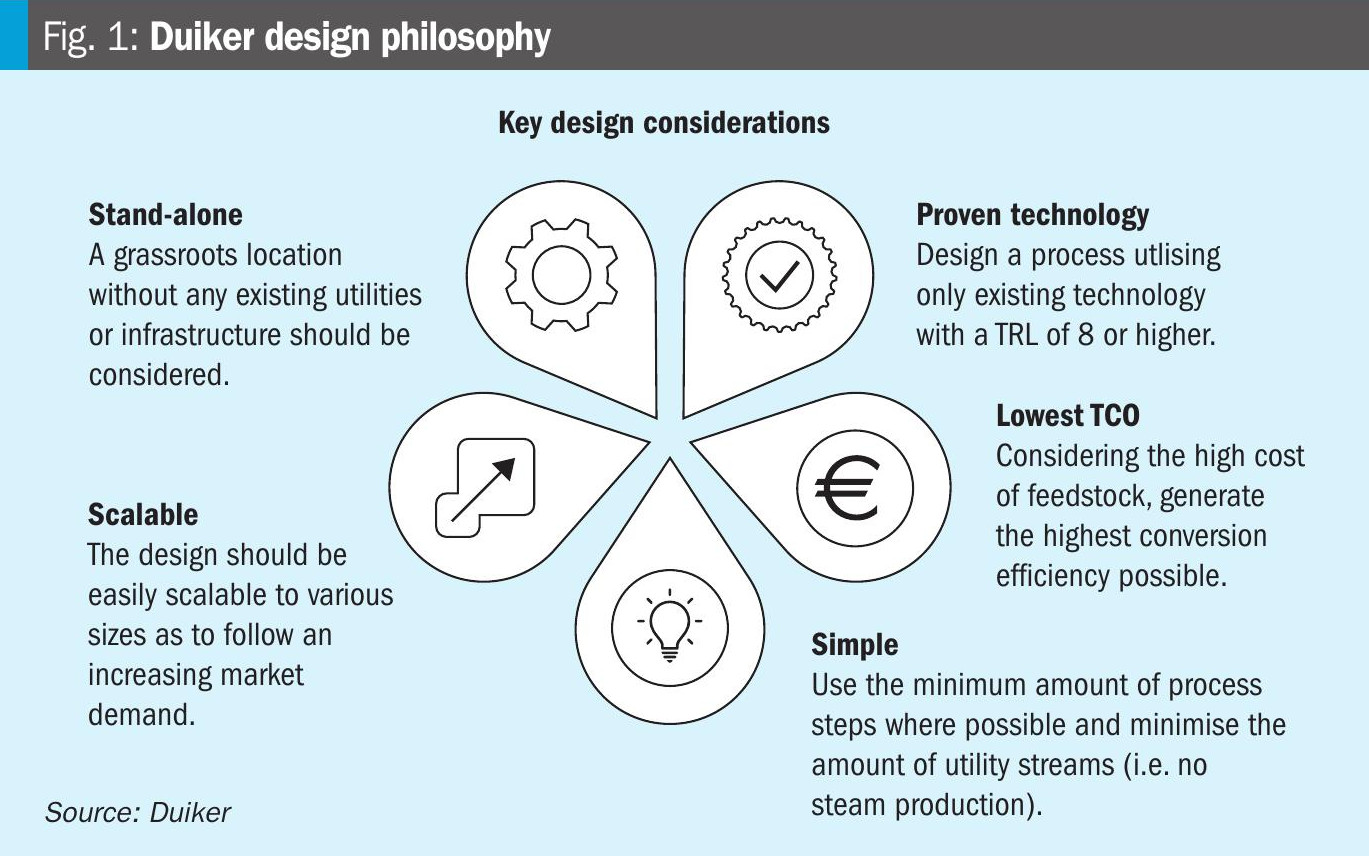
Applying these considerations, Duiker’s ammonia cracking process achieves simplicity by comprising only three main operational units (excluding heat exchangers, pumps and air blowers, see Fig. 2):
• heat generation with ammonia as zero-carbon fuel;
• ammonia cracking;
• purification of cracked gas.
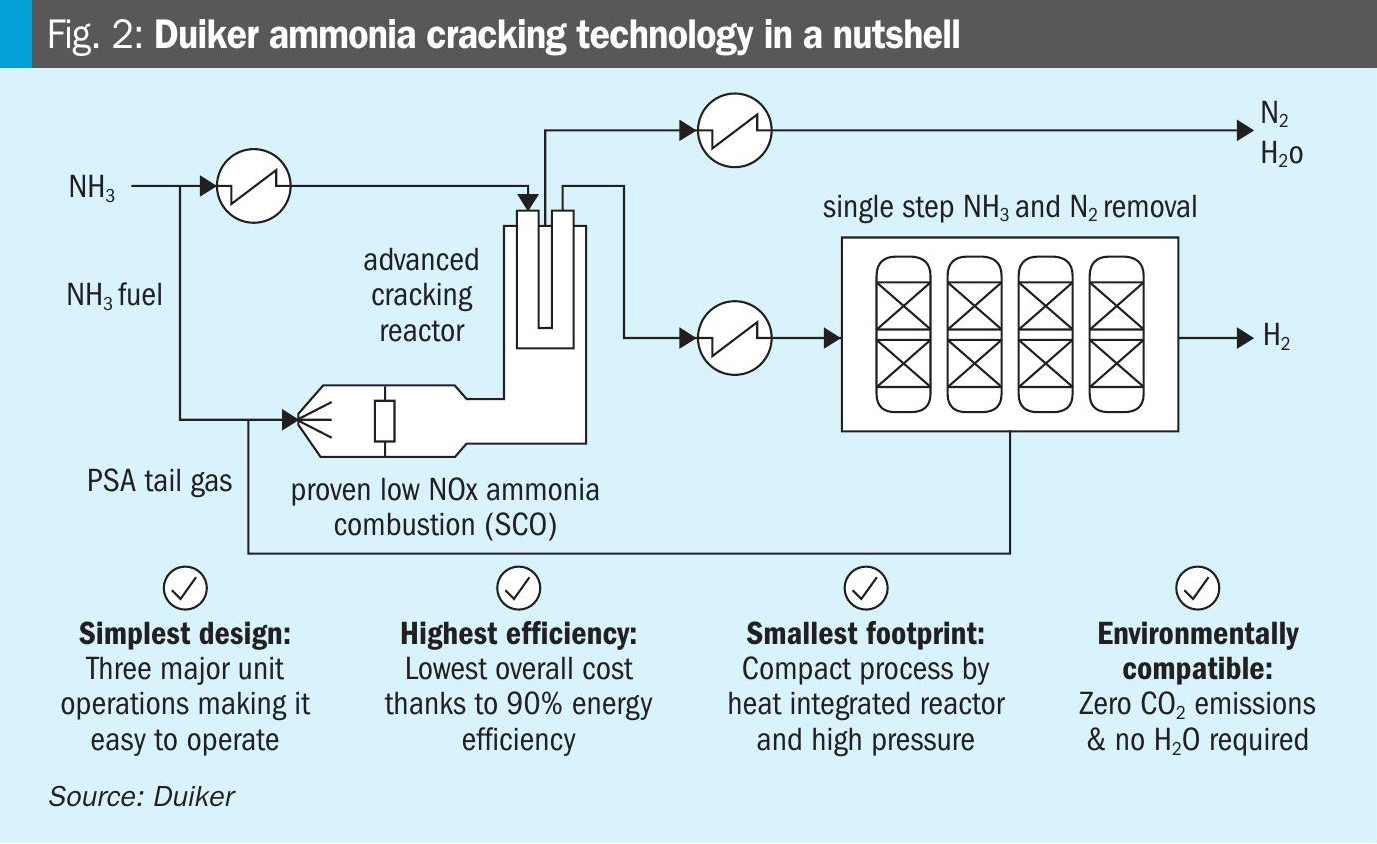
As a result, the cracking process achieves high availability and reliability, and does not emit CO2 or NH3, nor does it produce liquid ammonia waste streams. In addition, water or cooling is not required, whilst the hydrogen is delivered at an elevated pressure of 50 bar(g).
Innovation technology maturation process
For an innovation to be successful and commercially viable it needs to bring unique value to the market and client. Therefore, an essential step in the technology maturation process is identifying potential risks, developing solutions to mitigate them, and transforming these solutions into “unique selling points”. Sound and structured methods such as Technology Maturation Process1 help not only to identify and map the potential risks, but also define features and benefits of the innovative technology, frame the opportunity and describe the first potential client early in the development process.
Perspective of industrial investors
There is a common phrase that says: ”Every organisation wants to have state of the art technology”. However, when it comes to investing a large amount of money for this technology an additional caveat emerges: “… and it should have been proven for more than a decade”. This is exactly where the conflict of interest lies; ideally, we want to have the newest technology for a product or process, but the newest will always come along with an uncomfortable feeling about critically evaluating this new technology without existing references. Performing a comprehensive risk analysis is a good approach to focus efforts on the right aspects of the new technology.
Duiker has followed the “TECOPS” principle1 (technical, economical, commercial, organisational, political and societal risks) and listed the major risks and their remedies with respect to ammonia cracking technology in an overview in Table 1.
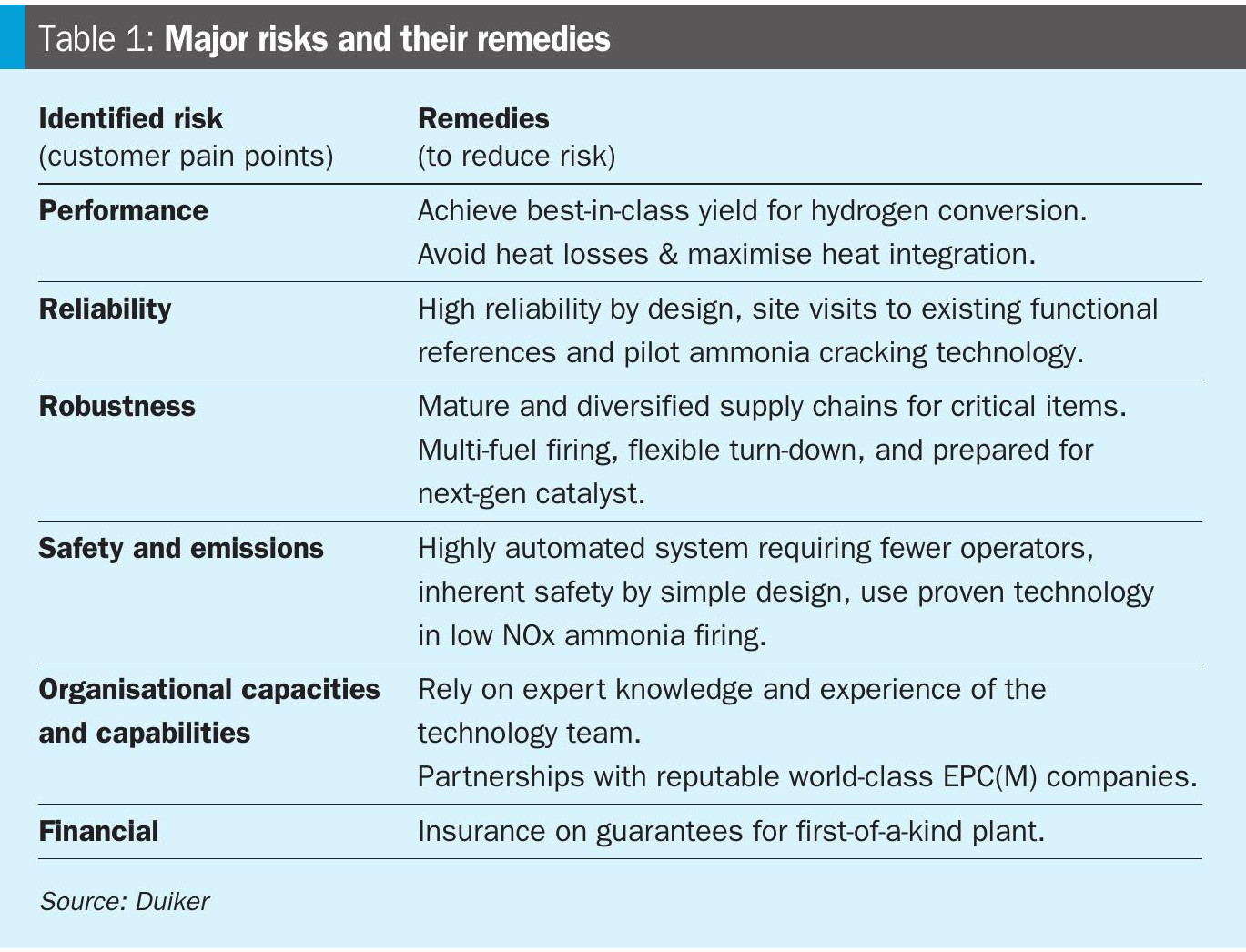
It is important to note that Table 1 includes only those risks that are under control of the technology developer/innovator. The risks and remedies suggested by Duiker are a result of continuous critical evaluations and are further elaborated below.
Performance
The importance of well-performing new technology is self-evident and should be optimised to ensure its commercial viability. But what level of performance is Lorem ipsum required if the technology has not been applied before?
Duiker decided to strive for the highest energy efficiency values by minimising heat loss through implementing a highly heat-integrated system in its ammonia cracking technology. For example, the geometry of the equipment is designed to reduce heat losses compared to alternative designs. Besides that, the select geometry also performs mechanically better and is more predictable when exposed to elevated pressures, which paves the way for operating under higher pressure and results in smaller sized equipment and reduced plot size.
Furthermore, the output pressure of delivered hydrogen makes a post cracking compressor redundant in most projects. Another significant electricity consumer has been eliminated with this approach. Reducing unnecessary energy consumption further enhances the efficiency of the cracking plant. Utilising a liquid ammonia pump to increase system pressure, rather than a compressor for gaseous (vaporised) ammonia, proves highly beneficial. The savings in electrical power consumption from this design choice are undeniable. Heat losses are avoided where possible and together these features lead to a very high energy efficiency. The purity of the hydrogen, considered as another important key performance indicator, complies with ISO 14687:2019 and can simply be achieved by selecting a well-known, proven and scalable purification method: pressure swing adsorption (PSA). The PSA plant will be designed and supplied by reputed companies in this area of expertise.
Reliability
The reliability of a new technology can be considered as one of the key concerns for an investor for obvious reasons; once the business case calculations have been made, an investor wants to have a “certain level of comfort” that the technology will perform and last for the duration of its investment horizon. Reliability has been improved through design features such as extending the lifespan of the tubes in the cracking reactor by eliminating direct combustion.
This approach prevents hot spots on the tubes, which could otherwise cause unexpected tube failures, while also enhancing temperature control within the reactor and reducing plant complexity by limiting the number of equipment items.
Next to design-related solutions, reference visits to commercial scale plants of the new technology can be very insightful as well as piloting the new technology at a relevant scale. In this respect Duiker organised reference visits to commercial scale plants (see Fig. 3) where visitors can directly see and speak with the operators of low NOx ammonia combustion units (SCO). Another milestone in Duiker’s endeavour in reducing risks, is to build and operate a pilot for an ammonia cracking plant with commercial scale reactor tubes, that aims to start operation in Q4-2026.
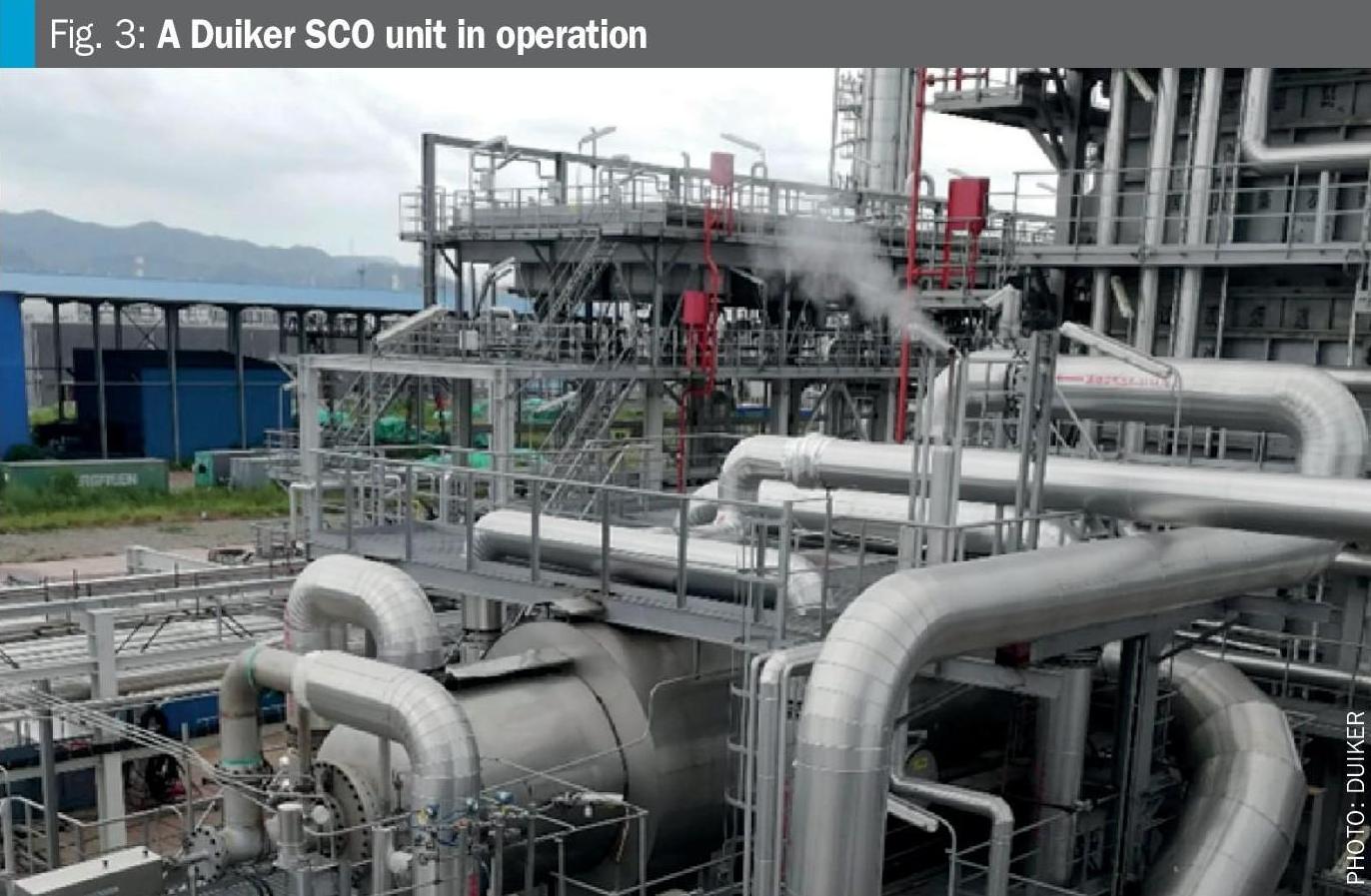
Robustness
Robustness of new technologies in different aspects is always a welcome addition when it comes to reducing investor risks. With respect to robustness in the supply chain, Duiker works with different suppliers for critical components, eliminating the chances of being “locked-in”.
Flexibility in fuel selection also offers robustness to the technology. Handling different types of fuels or fluctuating feeds does not have an impact on the performance of the ammonia combustion technology, due to its flexible turndown. Smart choices in design features create flexible scalability for the SCO unit while a “numbering-up” approach for the cracking reactor, allows significant reactor scalability. Together these aspects make most future expansion plans (capacity) or future developments (low temperature catalyst) quite simple and feasible. It can also be integrated with existing capacities, making the technology adaptable for both small and large installations.
Safety and emissions
“If you think safety is expensive, try an accident” is a statement that perfectly shows why safety is perceived as a big risk of new technologies, especially when they are applied in industry handling hazardous substances, like ammonia. A perfect solution to protect humans is to lower the number of operators required to operate the new technology and reduce the risk of human errors by selecting highly automated process control technologies. Designing the process with fewer steps and fewer equipment means a more inherently safe design because it also simplifies the operation. Supported by decades of experience in ammonia handling within process combustion units, including sulphur recovery (SRU) and stoichiometry controlled oxidation (SCO) for low NOx ammonia firing, Duiker has developed a strong expertise in safely managing ammonia within its ammonia cracking plant.
The emissions hurdles have been addressed by opting for ammonia as a zero-carbon fuel, and applying a proven low NOx ammonia combustion system as the heat generator to keep the NOx and NH3 emissions inherently low. NOx levels can even be further reduced to achieve the most stringent regulatory levels by adding a modest SCR unit. In addition, selecting an advanced PSA removes the nitrogen and ammonia in a single step, eliminating an ammonia waste stream.
Organisational capacities and capabilities
Often neglected or valued as a “low or medium risk”, both the capacities of a team and the capabilities of an organisation are crucial for the success of an innovation. Especially after product launch, in case of unexpected setbacks, the resilience of a team and the organisation, as well as the ability to learn and apply new insights to technology, proves invaluable and helps mitigate risks. Ideally, an organisation builds up its own core knowledge and expertise teams and seeks subject matter experts that can fill temporary knowledge gaps and manage specialised tasks. Duiker also collaborates in long term partnerships with reputable organisations that offer additional capabilities for risk reduction, during engineering, building and operating ammonia cracking plants. To expand capabilities in EPC(M), Duiker is partnering with world-class companies with proven track records.
Finance
“Last but not least, it is all about the money” that drives innovation and its commercial success. Clearly, a new technology that provides the lowest levelised cost of hydrogen (LCOH) plays a key role in supporting the feasibility of business cases. Financial risks are reduced hereby, because the new technology is deemed sufficiently bankable to take off and become profitable.
By focusing on the strategies to reduce the cost for cracking, such as:
• avoiding heat loss as it can cause up to 0.5%-point efficiency loss;
• reducing post-cracking compression of hydrogen as it may lower efficiency by 1.5%;
- avoiding the use of H2 or electricity as ‘fuel’;
• catalyst costs are minor component of the overall costs.
Engineering these strategies into smart solutions, the LCOH of cracked hydrogen from Duiker’s technology is among the lowest currently available on the market. For a visual quantification of those costs refer to Fig. 4. The graph is a relevant picture of present day but can fluctuate in time.
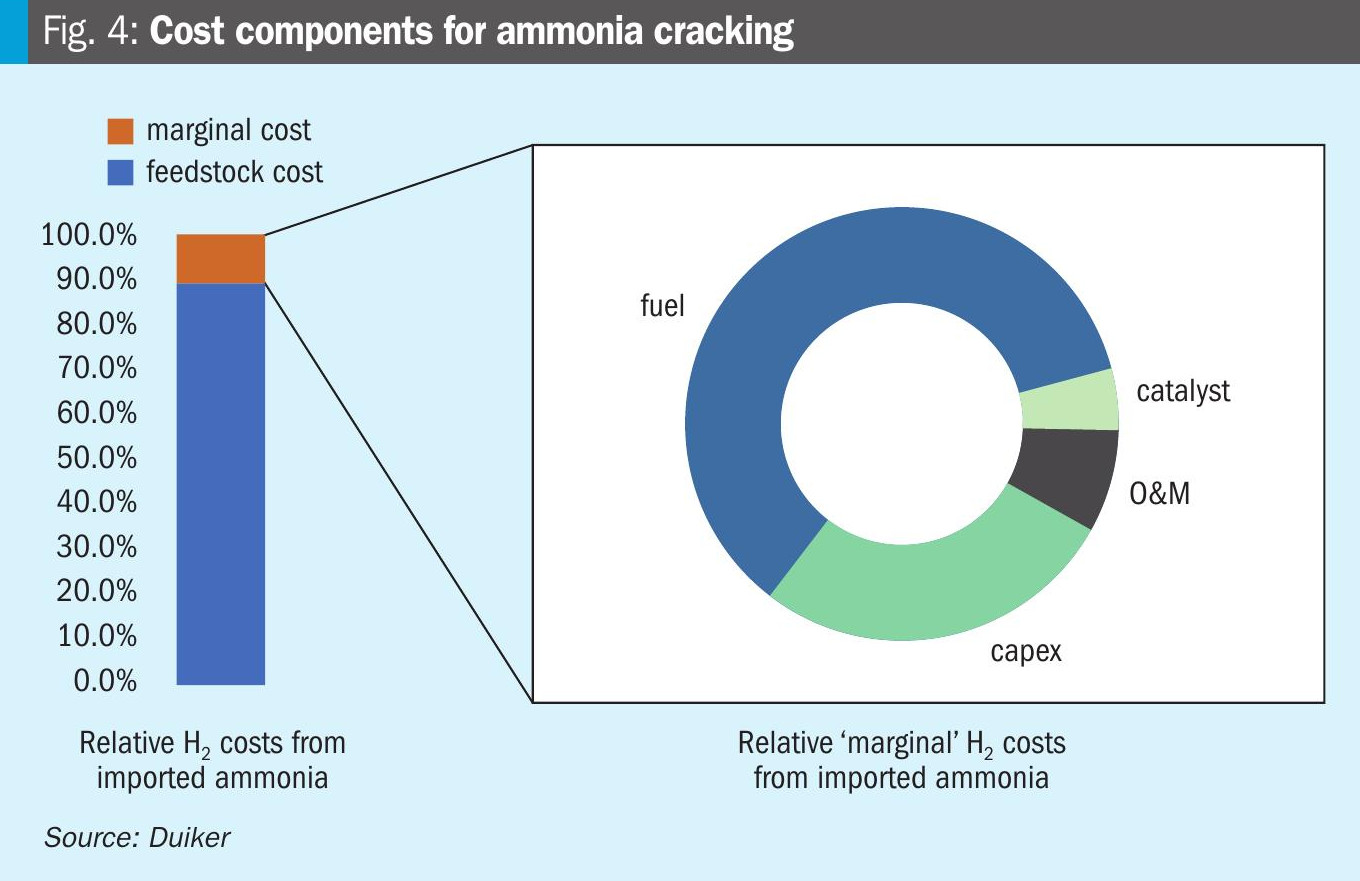
Furthermore, Duiker reduces financial risks by offering insurance on guarantees for “first-of-a-kind plant” – a specialised insurance to cover perceived risks exceeding those of a routine technology project.
Conclusion
New technologies, like ammonia cracking, come with risks and it is up to the innovation teams to identify and address these risks by engineering innovative solutions to mitigate and turn them into USPs. It pays to take a structured method for this innovation step. Duiker has greatly succeeded in its innovation process and invites potential customers with interest in ammonia cracking to get in touch about its innovative and reliable ammonia cracking technology that carries one of the lowest cost of ownership in its field.
References