Fertilizer International 525 Mar-Apr 2025
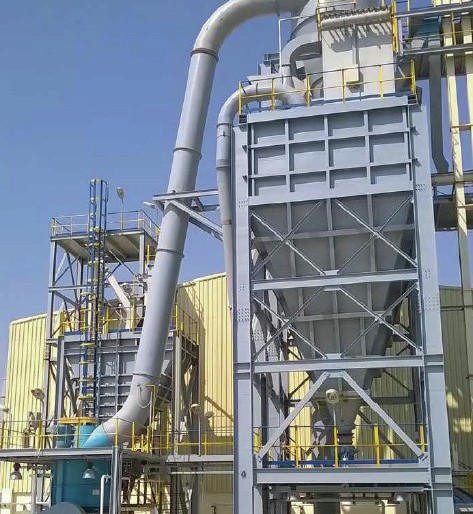
18 March 2025
Reducing wear during size reduction
Factors such as hardness, abrasiveness, brittleness, moisture content, and friability determine the extent of wear on phosphate milling equipment. Ian Hancock, Vice President Sales and Operations, Bradley Pulverizer Company, offers expert advice on how to reduce wear during phosphate size reduction. This is becoming a critical issue as the industry moves toward processing lower-grade, high-silica phosphate rock.
Introduction
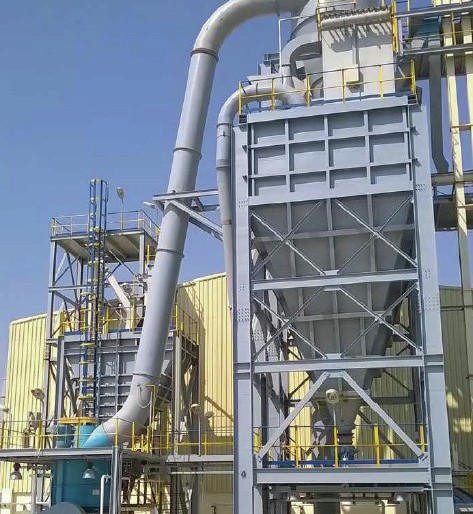
Phosphate processing is a critical component of global fertilizer production, requiring efficient size reduction techniques to ensure optimal particle size and product quality. However, wear during milling operations remains a significant challenge, particularly when processing low-grade phosphate rock with high silica content. This article explores key considerations for reducing wear during phosphate size reduction. Advances in wear-resistant materials and mill design are also highlighted – together with operational strategies that improve equipment longevity and efficiency.
Milling technologies and wear considerations
The physical properties of phosphate rock are known to influence milling efficiency. Factors such as hardness, abrasiveness, brittleness, moisture content, and friability determine both the energy required for size reduction and the extent of wear on milling equipment.
Different milling technologies are employed in phosphate processing, each with varying wear characteristics. Commonly used mills include:
• Vertical roller mills & pendulum mills: Ideal for medium-hard phosphates with limited levels of impurities. These mills provide efficient grinding but are susceptible to wear from abrasive materials – although this can be mitigated for with the correct approach.
• Impact mills (hammer, pin, chain mills): While highly effective for particle size reduction of brittle materials, impact mills can suffer from rapid wear due to high-speed particle collisions.
• Ball & rod mills: Effective for finer grinding but require high containment due to dust generation.
Common wear issues
Wear is particularly prevalent in cyclones, ducts and grinding rolls. In phosphate milling, low-grade rock with high silica content accelerates this wear, especially because of the fine grind that is required for low-reactivity materials.
Common wear mechanisms include:
• Impact wear: Caused by particle collisions with mill surfaces, this requires softer wear materials like polyurethane or butyl rubber.
• Attrition & shear wear: In this type of grinding, surfaces require harder materials such as Hardox or chrome carbide.
• Compression wear: Increased surface degradation during high-pressure crushing necessitates advanced roll designs.
Advances in wear reduction – lining materials & component design
To mitigate wear resulting from impact, attrition and compression forces, the industry has adopted several innovative high-performance wear linings and coatings. Matching wear-resistant materials to specific wear causes can help reduce frequency of maintenance, mill downtime, operational costs and extend equipment life. General recommendations are as follows:
• Rubber (or soft) linings, including butyl and polyurethane (see photo), have proven effective in protecting mill bodies, grinding rolls, and support parts. These materials reduce abrasion in direct impact areas while maintaining process efficiency.
• Hardox or chrome carbide linings, in contrast, are better suited for low-angle impact zones. These hard linings can be used in cyclones, ducts, and classifier components for long-term abrasion resistance.
• Ceramic coatings, meanwhile, offer superior hardness and extended wear resistance when applied in high-stress areas.
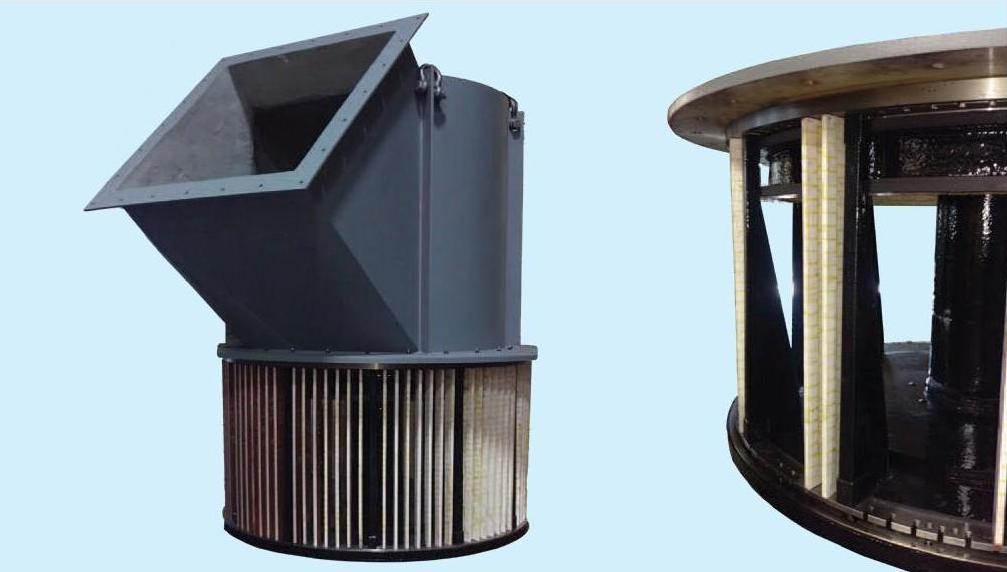
To increase the useful life of wear parts, several improvements have been incorporated into the design and composition of common mill components. Adopting advanced geometry in roll designs & grinding media, for example, reduces material slippage and improves grinding pressure distribution. The use of new alloy compositions, by extending roll life, also reduces replacement frequency and maintenance costs.
Operational adjustments for lower wear
A proper assessment of operational parameters helps reduce wear in phosphate milling. Operators, by fine tuning independent parameters such as mill speed, feed material flow, and other process variables, can maximise production while minimising excessive wear and extending equipment service life. The following adjustments are generally advised:• Optimising air velocity within the system is essential as it has a direct effect on wear.
• Pre-crushing phosphate rock before milling optimises the feed size to reduce stress on primary grinding units. Smaller particles generate less wear because they have lower kinetic energy and lower transport velocity.
• Adjusting moisture content will minimise clogging and cohesion-related wear.
Other successful operational strategies for wear reduction include predictive maintenance and real-time monitoring:
• IoT-enabled sensors, for example, track wear patterns and can help predict failures before they occur.
• Additionally, data-driven maintenance schedules can help ensure components are replaced before performance declines, so reducing unexpected downtime.
Conclusions
Reducing wear during phosphate size reduction is essential for maintaining processing efficiency, lowering maintenance costs, and enhancing equipment longevity. Phosphate producers can significantly enhance operational efficiency by adopting advanced wear-resistant materials, improved roll designs, and strategic milling practices. Innovations in milling technology and wear protection will play an increasingly critical role in sustaining productivity and cost-effectiveness as the industry moves toward processing lower-grade, high-silica phosphate rock.
CRU Phosphates+Potash Expoconference 2025
Ian Hancock of Bradley Pulveriser will be presenting on this topic at the conference in Orlando on Tuesday 1 April at 12:15-12:45.