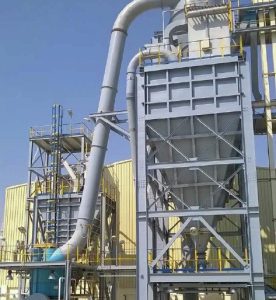
Reducing wear during size reduction
Ian Hancock, Vice President Sales and Operations, Bradley Pulverizer Company, offers expert advice on how to reduce wear during phosphate size reduction.
Ian Hancock, Vice President Sales and Operations, Bradley Pulverizer Company, offers expert advice on how to reduce wear during phosphate size reduction.
CRU’s 2025 Phosphates Conference – now in its 16th year – will be held in Orlando, Florida, 31 March - 2 April next year. The 2024 event convened in Warsaw was one of the most successful to date (Fertilizer International 519, p4).
CRU Events will convene the 2024 Phosphates International Conference & Exhibition in Warsaw at the Hilton Warsaw City Hotel, 26-28 February.
The cadmium and heavy metal content of sedimentary phosphates are of great concern. This has seen industry raw material consumption shift towards igneous phosphates or the blending of phosphate rocks from different sources. While rock blending can successfully reduce the heavy metal content of superphosphates, it needs to be accompanied by careful process adjustments, as Ian Hancock , Bradley Pulverizer’s vice president sales & operations, explains.
The Broadfield process has remained a mainstay of the global phosphate industry since its introduction in the 1930s. Ian Hancock, vice president sales & operations, Bradley Pulverizer, explains it continuing success in superphosphate production worldwide
A holistic understanding of the phosphate milling process is necessary, says Ian Hancock of Bradley Pulverizer. This ensures maximum plant uptime, the highest process efficiencies, and ultimately guarantees profitability.
The crushing and grinding of mined phosphate rock and potash ore is a vital preparatory step for subsequent beneficiation and chemical processing. Although often overlooked, the efficiency of downstream P & K fertilizer production is heavily reliant on successful particle size reduction upstream.