Fertilizer International 503 Jul-Aug 2021
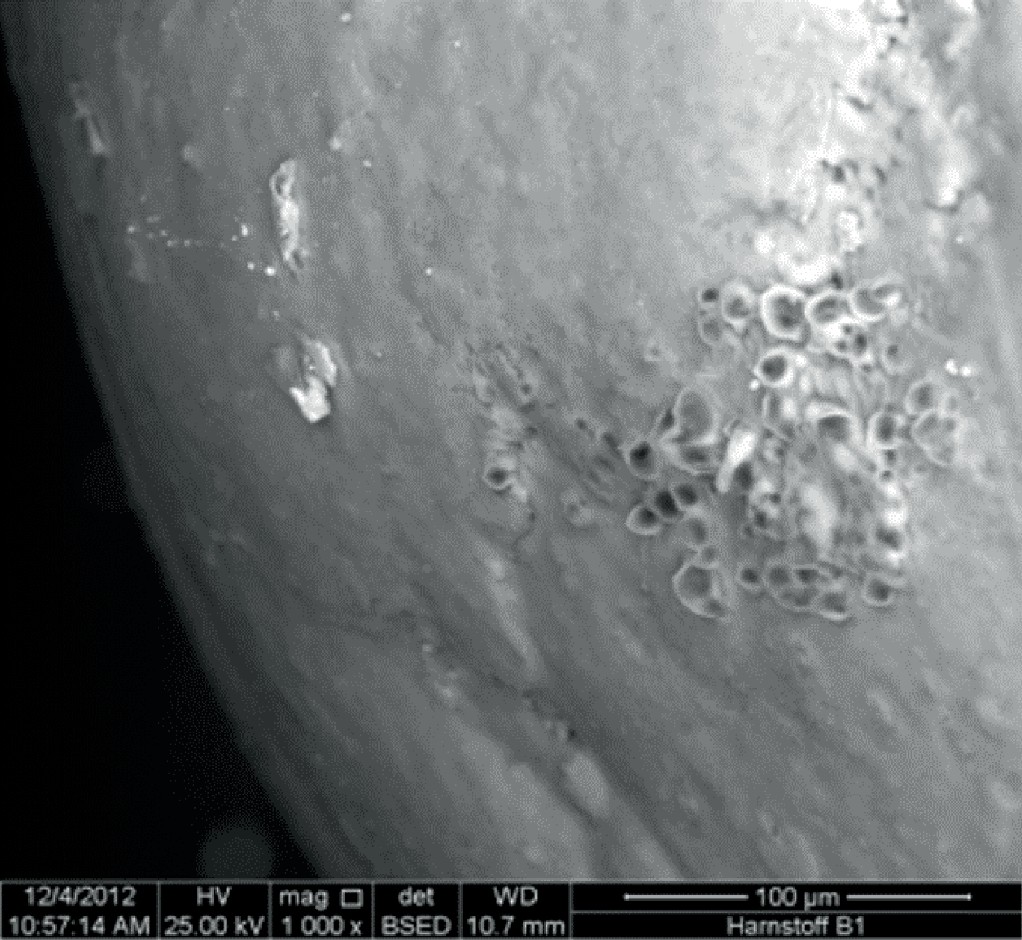
31 July 2021
Technologies for boosting nitrogen use efficiency
PRODUCT TECHNOLOGY
Technologies for boosting nitrogen use efficiency
The European Union is seeking to create a climate-neutral and circular economy through its flagship Green Deal policy. The fertilizer industry can support these objectives by adopting inhibitor treatment technology (ITT) and controlled-release fertilizers (CRFs) based on biodegradable polymers. These two innovations have a vital role to play in improving nitrogen use efficiency and the shift towards more sustainable resource use, says Dr Matthias Potthoff of thyssenkrupp Fertilizer Technology.
Fertilizers exert a dual pressure on the environment. On one hand, the world’s population is constantly growing, diets are shifting towards higher meat consumption, as at the same time the area of arable land becomes less and less. The result is higher fertilizer demand and usage.
On the other hand, the agricultural sector contributes 10-12 percent towards worldwide greenhouse gas emissions, out of which about two percent is attributable to fertilizer production (CO2 , NOx, N2 O). Understandably, the pressure to reduce such emissions is growing constantly.
Moreover, the nitrogen losses from the application of urea – the mostly widely applied nitrogen fertilizer with a 75 percent market share – are known to be considerable. A fact that makes the focus on improving the nitrogen use efficiency (NUE) of urea particularly important.
The European Union is one region that has taken action on this issue – by implementing a ban on the application of untreated urea fertilizers from 2022. At the same time, fertilizer producers, faced with a highly competitive market environment, are seeking to expand their portfolios and diversify into higher margin products.
Against this backdrop, the fertilizer industry needs to manage its product offerings and innovate in preparation for future market needs. In this context, two successful technologies for improving the NUE of granular urea are proposed:
- Inhibitor treatment technology (ITT), jointly developed by BASF and thyssenkrupp Fertilizer Technology
- Controlled release fertilizers (CRFs) which coat urea granules with biodegradable polymers such as polylactic acid (PLA).
We summarise each of these innovative technologies below.
Inhibitor treatment technology (ITT)
Regulators around the world have recognised the problem of ammonia volatilisation from surface-applied urea. The result has been by an increasing number of stringent regulations and restrictions governing the application of urea.
Urease inhibitors are one answer. These reduce ammonia emissions, improve NUE and increase yield performance. They also provide farmers with a higher degree of freedom in terms of their fertilizer application strategy. Urease inhibitors need to be present when urea is applied to soils. The easiest way to achieve this is by incorporating the urease inhibitor within urea granules during their production.
With this in mind, new inhibitor treatment technology (ITT) provides a highly efficient way to treat granular urea with a urease inhibitor at large scale in the quantities required globally. ITT is flexible too – being available as a plant add-on for both existing and new UFT® fluid bed granulation plants. This saves cost and space, since no additional coating equipment is necessary. Furthermore, ITT is less labour intensive, and also provides scope for additional surface treatments further down the value chain (e.g. for micronutrients).
There is a need to ensure that the urease inhibitor formulation and the application technology are completely compatible and correctly and specifically match one another. To achieve this, BASF and thyssenkrupp Fertilizer Technology (tkFT) have cooperated closely together on a new ITT project.
Under a formal agreement, the two project partners have now successfully developed an application-specific version of BASF’s proprietary Limus® urease inhibitor formulation for use in the UFT® fluid bed urea granulation process. No additional investment is required beyond a simple dosing system.
ITT has been thoroughly tested and validated at pilot plant scale. It was also recently verified for the first time at a full-scale industrial UFT® fluid bed urea granulation plant. The results and the stability of the inhibited urea product produced at industrial scale are currently being evaluated. ITT is then expected to become fully commercialised in late 2021.
Controlled-release fertilizers (CRFs)
Under unfavourable conditions, conventional fertilization can result in big nutrient losses to the environment – up to 70 percent or more in the case of nitrogen. These losses are directly responsible for nitrate pollution of groundwater and soils in countries where agricultural fertilization is extensively practiced, including EU countries.
Consequently, legislators have reacted by imposing restrictions. The amounts of fertilizers applied need to be decreased, as does the number of applications over the crop growing season. Additionally, standard commodity fertilizers such as urea need to be replaced with so-called enhanced efficiency fertilizers (EEFs) – also known as stabilised fertilizers (SFs) – to decrease these losses.
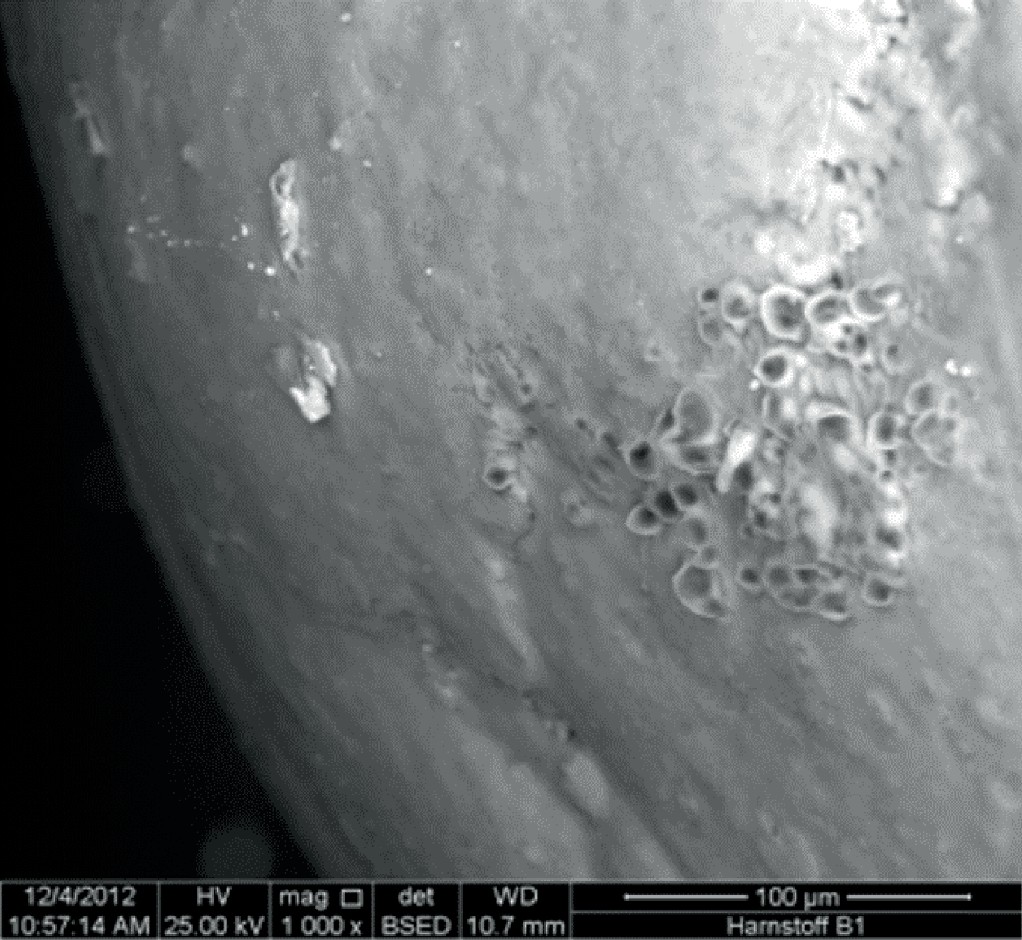
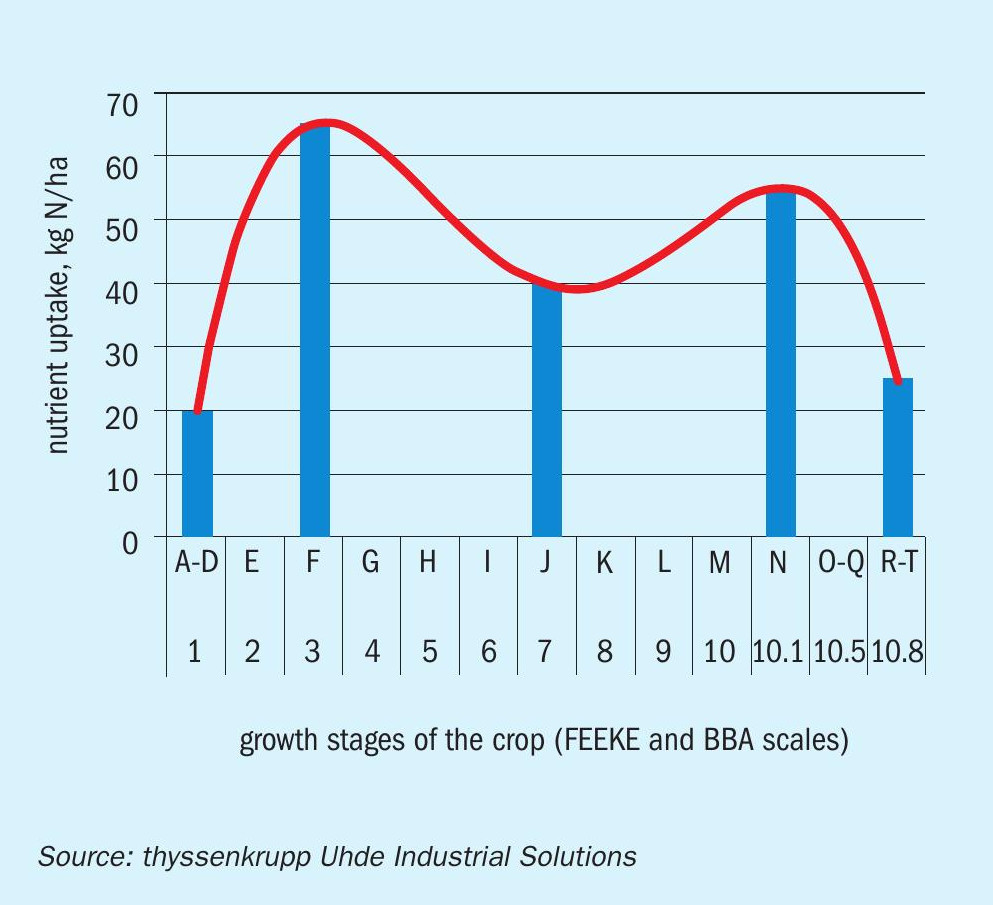
Having recognised this trend, thyssenkrupp Uhde has been working to develop SFs and controlled-release fertilizers (CRFs) together with their associated production processes. One successful outcome has been the development of an innovative polymer-coated urea (PCU), a special type of CRF. This focused especially on the application of biodegradable polymers such as polylactic acid (PLA) as a coating material (Figure 1).
These polymers can be produced from renewable materials and decompose naturally in soils without producing environmentally-harmful substances. This guarantees that the whole production and application process can be sustainable.
These type of CRFs ensure the availability of nutrients over the entire growing season (Figure 2). They are also more efficient as they supply nutrients in the exact quantities required by the crops. This provides the option to either increase crop yields by up to 10 percent or apply less fertilizer, with scope to also combine these two positive effects.
CRF production can be integrated within an existing ammonia/urea complex, or set up as a standalone plant, and is offered in a wide range of production capacities. The application of a polymer coating helps minimise the nitrogen losses associated with urea and improve its NUE. This technology can also be successfully applied to K-, P- or S-fertilizers to provide similar benefits and positive effects.
Conclusion
The innovative fertilizer technologies described here increase nitrogen use efficiency (NUE). They also make a valuable contribution to new environmental requirements encouraging the sustainable use of resources. Both these technologies, which are readily available for commercial implementation, provide new product options that will help ensure fertilizer producers are well-positioned to satisfy changing market demand.