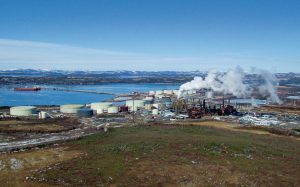
Sustainable refineries
Liquid fuels will be with us for decades to come, but refiners will be pushed to decarbonise their activities, via greater use of biofuels, and green/blue hydrogen use.
Liquid fuels will be with us for decades to come, but refiners will be pushed to decarbonise their activities, via greater use of biofuels, and green/blue hydrogen use.
New methods for low-carbon ammonia production are emerging, while project activity is also rising rapidly.
The world’s most common syngas production method remains steam methane reforming, a process which has a substantial CO2 footprint as the necessary reaction heat is supplied by combustion of hydrocarbons. Topsoe’s eREACT™ technology allows for the first-of-its-kind electrification of the traditional SMR process. The reaction heat for eREACT™ is instead generated directly by (renewable) electricity, thereby eliminating the flue gas altogether. Having gone through scale-up from bench scale to industrially relevant pilot scale the technology is now ready for industrial application.
Casale has developed a range of methanol-ammonia coproduction processes to match different requirements according to product capacity.
New low-cost metal oxide solid scavengers for hydrogen sulphide (H2 S) removal from wet and dry natural gas have been developed and deployed at commercial scale. The desulphurisation process uses a proprietary sorbent chemistry to achieve a high sulphur capacity and removal efficiency. G. Alptekin, F. Kugler and M. Schaefer of SulfaTrap LLC describe the new technology and its performance.
Major fertilizer industry players such as Stamicarbon, Nutrien and CF Industries are ramping up investment in ‘green’ and ‘blue’ fertilizer production. Consequently, low-carbon production technologies are being scaled-up and deployed commercially.
M. Østberg and M. Rautenbach of Haldor Topsoe describe ReShift ™ technology, a new high temperature CO 2 reforming process, where preheated CO 2 is added directly downstream of a main reformer and then equilibrated in an adiabatic reactor. This new technology makes use of the high temperature of the reformer effluent to circumvent carbon formation, while at the same time maintaining an overall minimum steam to hydrocarbon carbon ratio, depending on process specific conditions. An increase in the amount of CO 2 added to the process will result in an increased fraction of CO in the produced synthesis gas. Synthesis gas with H 2 /CO ratios in the range 0.5-3 can be produced. These CO-rich gases are typically utilised in the production of functional chemicals and synthetic fuels.
Reducing the carbon footprint in the synthesis of chemicals is a new global challenge as the world works towards providing sustainable products designed to minimise their environmental impacts throughout their whole lifecycle. This article looks at the role of blue technologies as part of a roadmap towards the decarbonisation of fuels and chemicals.
thyssenkrupp Industrial Solutions discusses a revamping concept to reduce CO2 emissions by replacing some of the hydrogen in the front end of the ammonia plant with green hydrogen, KBR and Casale report on revamp options to increase the capacity of vintage ammonia plants in the former Soviet Union, Johnson Matthey presents a novel integrated ammonia flowsheet for the production of ammonia, methanol, urea and UFC and Arvos | Schmidtsche Schack discusses the benefits of a new process gas boiler.
By harnessing the power of real-time data and exploiting the opportunities provided by digital solutions plant owners can achieve greater plant efficiency and reliability. In this article Stamicarbon shows the benefits of the Stami Digital Plant Optimiser for urea plants, OnPoint Digital Solutions provides a case study on optimising primary reformer heater operations using Smart Combustion™ , TOYO provides an update on its digital transformation service DX-PLANT® and thyssenkrupp Industrial Solutions provides examples of how digital solutions can be used to improve plant operation.