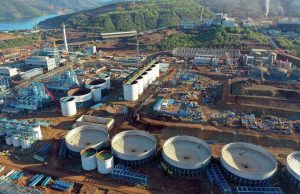
Sulphuric acid projects 2021
Sulphur’s annual survey of recent and planned construction projects in the sulphuric acid industry includes several large-scale acid plants both for phosphate processing and to capture sulphur dioxide from smelters.
Sulphur’s annual survey of recent and planned construction projects in the sulphuric acid industry includes several large-scale acid plants both for phosphate processing and to capture sulphur dioxide from smelters.
With demand for conventional fuels projected to peak and fall over the next decade, some refiners are looking to petrochemical production as a way of diversifying their product slate.
A. Goudarzi of CECO Industrial Solutions discusses the science behind NOx content and how it impacts sulphuric acid producers. In a recent project in Korea, TWIN-PAK® candle filter technology was successfully used to reduce NOx emissions in metallurgical oleum tower production. After installation of the candle filter mist eliminators the plant was compliant with environmental regulations enabling the producer to operate the plant without penalties or shutdowns.
The continuing spread of alkylation technology and the preference for the sulphuric acid route are leading to increased demand for acid in refineries.
Temperature monitoring and measurement of the Claus thermal reactor in sulphur recovery units is one of the most challenging applications in the oil and gas industry. Recently, market interest in unpurged thermocouples has increased with the introduction of new unpurged thermocouple designs utilising alternative thermowell materials such as monocrystalline sapphire.
Sulphur ’s annual listing of new or recently completed sulphur forming projects worldwide covers both new sour gas and refinery sulphur forming projects as well as upgrades at existing units.
Significant capacity additions in the Middle East are still awaited. The more positive outlook for fuel demand is providing support to seeing these projects ramp up in the coming months. New supply is expected from Saudi Arabia following the commissioning of a gas project in 2020, sulphur availability is likely to improve from the country through the second half of 2021 and into 2022 as a result.
Are the three “T”s (temperature, turbulence, time) of Claus unit ammonia destruction still meaningful with improved understanding of the thermal reactor? CFD models appear to be adequate at higher temperatures, e.g. 1,200°C, but not at lower temperatures, e.g. 800°C and 1,000°C. A. Keller, on behalf of the Amine Best Practices Group, reviews how meaningful the rules of thumb for Claus unit ammonia destruction really are.
New state-of-the-art equipment has been installed in the thermal stage of one of Europe’s largest Claus SRU units. Substoichiometric firing and a furnace designed with CFD calculations and a modern compact boiler system design based on detailed heat engineering and FEM calculations were key to the success of the retrofit. P. Foith of CS Combustion Solutions reports on the retrofit and how the novel combination of a CS low pressure swirl burner, additional mixing using a VectorWall™ and a new waste heat boiler design achieved the desired results.
Sulphur processing and handling equipment manufacturer IPCO has completed the commissioning of a groundbreaking new drum granulator in Italy that will serve as a global showcase for this patented system. C. Metheral of IPCO, describes the innovative approach and key features of the SG20 sulphur granulation system.