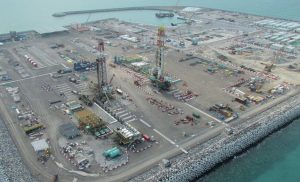
Abu Dhabi’s sour gas expansions
Already the world’s largest exporter of sulphur, Abu Dhabi continues to expand its sour gas production and sulphur output.
Already the world’s largest exporter of sulphur, Abu Dhabi continues to expand its sour gas production and sulphur output.
A complete listing of all articles and news items that appeared in Sulphur magazine during 2023.
Pyrite roasting as a source of sulphuric acid continues to be a significant, albeit minor sector of the overall acid market.
Cobalt-molybdenum (CoMo) catalysts are integral components of tail gas units (TGUs), playing a vital role in reducing harmful sulphur dioxide (SO2 ) emissions arising from Claus sulphur recovery units. Effective activation of these catalysts is essential for their optimal performance. The consequence of sulphiding at low temperatures and atmospheric pressure in low temperature TGUs is to compromise effectiveness of catalyst activation. In the first part of this two-part article, Michael Huffmaster , Consultant, explores CoMo catalyst activation at low pressure, focusing on sulphiding reaction pathways and the impact of temperature and the composition of the sulphiding media on reaction kinetics, specifically the concentration of H2 , H2 S, and H2 O.
The nickel market has been through a period of unprecedented change over the past few years due to demand for batteries for electric vehicles, with Indonesia becoming a centre for production via high pressure acid leaching.
Small quantities of sulphur in a refinery or gas feed can present challenges for conventional large scale sulphur recovery techniques.
With increased demands to reduce SO2 emissions and lower energy consumption, Eduardo Almeida and Nelson Clark of Clark Solutions highlight the advantages of single absorption sulphuric acid plants compared to double absorption plants.
MECS, Inc. (MECS) has developed a new impaction-based mist eliminator called Brink® Prime Impact™ , which offers equivalent or improved efficiency at higher throughput and the same pressure drop as traditional impaction beds, resulting in the ability to debottleneck existing inter-pass absorption towers and final absorption towers in sulphuric acid plants or design new or replacement towers with smaller diameters, thus reducing investment cost.
This case study reports on the successful collaboration of two experienced partner companies to replace the problematic upper part of a co-current flow quench tower in a spent acid plant and shows the benefits of using resistant, pre-lined workshop fabricated equipment.
Axens has developed a new titania-based catalyst named CRS 41, which has a much larger porosity than its renowned predecessor, CRS 31 catalyst. Thanks to an improved catalyst manufacturing process and a new recipe, the porosity of CRS 41 has been increased while preserving the mechanical resistance for loading, allowing customers to optimise their capex by either reducing the Claus reactor size or loading volume of TiO2 catalyst.