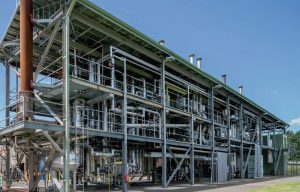
Modular plant design
A move towards smaller scale feedstocks such as renewable energy and waste and biomass gasification is leading to increased focus on improving the efficiency of small-scale, modular plants.
A move towards smaller scale feedstocks such as renewable energy and waste and biomass gasification is leading to increased focus on improving the efficiency of small-scale, modular plants.
Reducing carbon footprint in the synthesis of chemicals is a new challenge, a necessary requirement in the pursuit of sustainable products designed to minimise environmental impacts during their whole lifecycle. So-called “green” technologies for ammonia, methanol and hydrogen are being developed to meet these challenges. Casale, Linde, thyssenkrupp Industrial Solutions, Toyo Engineering Corporation, Haldor Topsoe and Stamicarbon report on some of their latest developments.
A detailed rain and wastewater concept is an important part of a urea plant to meet current stringent environmental standards. Wastewater can originate from the process reaction or from outside the process equipment. In order to optimise the wastewater system of a urea plant, both the amount and type of contamination need to be known. With this knowledge, non-contaminated rainwater as well as process drains can be kept separate as much as possible to minimise the amount of wastewater to be treated, saving costs and energy. Wastewater treatment concepts from thyssenkrupp Industrial Solutions and Toyo Engineering Corporation are described.
Scanfeld™ is the world’s first remote sensing solution for fully automated early-warning gas leak detection for chemical plants. Using FTIR spectroscopy, Scanfeld™ identifies hundreds of different gases in real time from kilometres away. With just a few Scanfeld™ sensor units, large production sites, tank farms, or gas loading areas can be monitored reliably. Gas leaks are quickly detected, and the formation of dangerous gas clouds is monitored, measured, and visualised. René Braun of Grandperspective discusses how the system works and how it is being applied in industry.
In China, requirements for methanol to produce olefins, mainly propylene and ethylene, from coal, has driven much of the growth in global methanol demand over the past decade. However, a new wave of ethylene cracker investment may put a stop to new MTO plant building.
Nitrogen-rich wastewaters remain a major issue for fertilizer and other industries. Saipem’s new electrochemical technology, SPELL, is an important step towards the overall objective of zero industrial pollution. A complete engineering review of the technology, its alignment with all international applicable standards, and optimisation has now been concluded and the technology is ready for deployment for the removal of ammonium nitrogen from industrial waters and wastewaters. Saipem discusses the key features of SPELL and reports on the first two industrial references.
The ammonium nitrate explosion in Beirut in August 2020 has once again focused minds upon the potential risks associated with the chemical.
Venkat Pattabathula, a member of the AIChE Ammonia Safety Committee, reports on the American Institute of Chemical Engineers’ Safety in Ammonia Plants and Related Facilities Symposium, held virtually on 30 August to 2 September 2021.
Arun Murugan and Mike Antony of FITIRI and Venkat Pattabathula of SVP Chemical Plant Services discuss the COORS Analytics system for more accurate prediction of the performance of a CO 2 removal system.
Johnson Matthey’s latest methanol synthesis catalyst, KATALCO™ 51-102, was introduced in 2018 to offer improved catalyst stability and therefore higher end-of-life activity and extended lifetimes than conventional methanol synthesis catalysts. Since launch, KATALCO 51-102 has been successfully installed in two methanol plants and a third is planned for later in the year. In this article Johnson Matthey provides an update on the proven performance of KATALCO 51-102 during lab and pilot scale testing as well as in customer plants. The application of catalysts made using the KATALCO 51-102 technology for methanol synthesis via new ‘green’ routes, such as using captured and purified CO2 in conjunction with ‘green’ hydrogen, is also discussed.