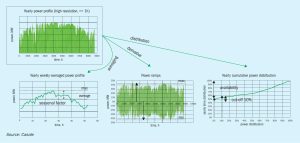
Ammonia plant hybridisation
The ammonia industry is expected to change drastically in the coming years to meet sustainability goals and to face the problem of climate change. New low carbon ammonia plants as well as fully green facilities are expected to be commissioned to meet the target of climate neutral production. The integration of an existing ammonia facility with green hydrogen to supplement or replace the grey ammonia production with green ammonia represents a low-risk solution to meet the requirement for running clean ammonia plants and offers the most competitive green ammonia production cost in the short term. In this article Sergio Panza and Marco M. Carlucci of Casale paper present different scenarios based on energy availability at battery limits.