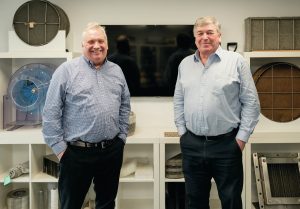
Begg Cousland – more than 70 years in the making
Fertilizer International interviews Graeme Cousland, Managing Director, and Martyn Dean, Sales Director, Begg Cousland Envirotec Limited.
Fertilizer International interviews Graeme Cousland, Managing Director, and Martyn Dean, Sales Director, Begg Cousland Envirotec Limited.
Metso launches Cu POX leaching process for copper extraction industry - solution maximises copper recovery while reducing environmental impact
Days 2 and 3 of the CRU’s 38th Nitrogen+Syngas 2025 Expoconference turned to the technical sessions, organised in three parallel streams covering: green ammonia technology, nitric acid and ammonium nitrate, plant operations and reliability, urea technology, digitalisation, carbon capture, emissions reduction and sustainable fertilizer production, and fertilizer finishing.
New concepts focused on the transfer and combination of existing sulphur and sulphuric acid technologies to support decarbonisation of the sulphuric acid industry are being investigated. In this article three research projects are discussed: sulphur dioxide depolarised electrolysis for green regeneration of spent acid, use of renewable heat and catalyst to the splitting process from sulphuric acid to SO2 for reduction of fossil fuel consumption, and sulphur as an energy vector.
The 2030 greenhouse gas emission reduction goals in the European Union are driving oil and gas producers to reduce CO2 emissions wherever possible. This extends to even the incinerator attached to a sulphur recovery unit (SRU). In this article Sulphur Experts review the role of the incinerator, how the three most common European TGUs each affect the demand on the incinerator itself, and the potential reduction in CO2 emissions for a generic facility of each type.
This study introduces a new platinum-promoted honeycomb catalyst for sulphur dioxide oxidation, designed to enhance energy efficiency and reduce emissions in sulphuric acid production. Compared to conventional vanadium oxide based catalysts, the platinum-based catalyst demonstrates higher catalytic activity, lower ignition temperature, and significantly reduced toxicity.
Due to ever stricter legislation towards lower SO2 emissions, superior catalyst shape and composition has become ever more important. Jochen Willersinn of BASF SE explains how BASF’s high-performance catalyst O4-116 Quattro combines the benefits of an increased surface area with a superior caesium-promoted active phase composition enabling significantly lower ignition and operating temperatures and thus reducing SO2 emissions.
Revamping aging urea plants with the latest urea technology brings many benefits. Not only can greenhouse gas emissions be reduced, but the overall performance and sustainability of these facilities can also be optimised. Hiroo Kunii of Toyo Engineering Corporation discusses TOYO’s approach to urea plant revamping.
One challenge of a green revamp by stepwise injection of green hydrogen into existing ammonia/urea complexes is to cover the nitrogen demand for the ammonia synthesis while stepwise reducing the front-end load, usually by applying a cost-intensive air separation unit (ASU). thyssenkrupp Uhde GmbH has developed an advantageous concept whereby, instead of an ASU, the nitrogen gap is closed by the introduction of pretreated reformer flue gas back into the ammonia process, with the side effect to also enhance CO2 production.
Urea revamp activities are performed to achieve improvements of the urea plant. Besides the typical capacity increase there are many options to reduce operation costs, increase plant availability or reduce environmental impact. In this article Marc Wieschalla of thyssenkrupp Uhde GmbH provides an overview of some of the options from an EPC contractor point of view.