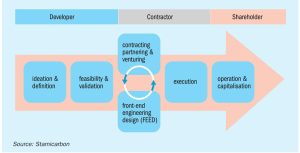
Sustainable production of nitrates from renewable energy
Paving the way for commercially attractive, sustainable, decarbonised fertilizer production, J. Dobrée of Stamicarbon BV discusses the latest developments for nitrate fertilizer production based on renewable feedstocks sourced from solar and wind energy. Stamicarbon has upgraded plant designs used in the past to create a new type of small-scale fertilizer plant capable of producing a product mix that can be adjusted to meet specific local requirements with maximised output value, thereby maintaining a competitive position towards imported products and large-scale producers.