Sulphur 419 Jul-Aug 2025
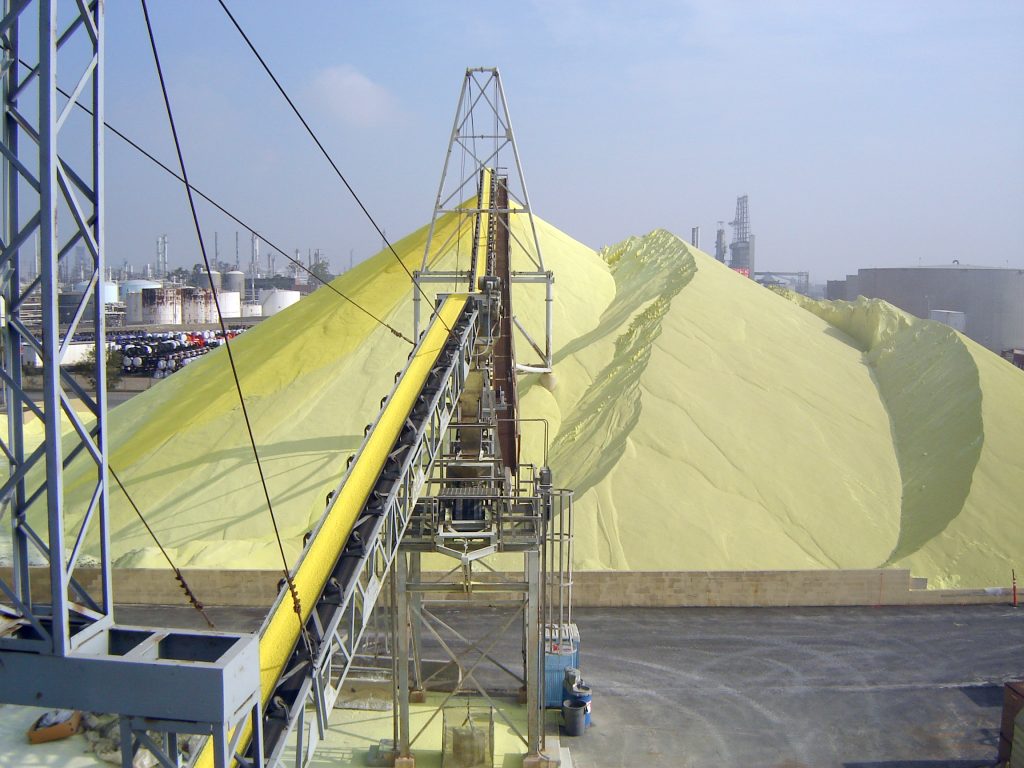
21 July 2025
Safety in design of sulphur forming and handling
SULPHUR SAFETY
Safety in design of sulphur forming and handling
David Savage of Matrix PDM Engineering discusses the importance of management and control of sulphur dust during the forming and handling of sulphur throughout the entire solid sulphur lifecycle while maintaining commercially acceptable product that contains less than 2.0% overall moisture.
Sulphur forming with outdoor storage and handling, Calsulco, Long Beach, California
Dust control of formed sulphur during forming and handling continues to be a major safety issue that must be addressed during the technology selection and design process. Sulphur dust when airborne can be harmful to personnel as a skin, eye, and lung irritant and is considered by most local environmental authorities as a violation if the dust is allowed reach the local waterways and ports. Another major issue that is often overlooked is the need for proper forming and handling of sulphur throughout the solid handling process to minimise the risk of a dust explosion resulting in an extremely long downtime and large financial losses. Proper moisture and/or dust suppression significantly reduces sulphur dust becoming airborne while still maintaining the proper amount of moisture (< 2%) on the solid sulphur product to meet “premium grade” product requirements as defined by the National Standard of the People’s Republic of China (GB/T 2449-2006).
Safety in Design (SiD) refers to the integration of hazard identification and risk assessment early in the design process to eliminate or minimise risks throughout the lifecycle of a project. It emphasises the significance of incorporating safety measures from the initial stages of design to prevent accidents, reduce costs, and ensure compliance with legal standards. In addition, it considers the safety of substances, materials, products and processes for human health and the environment as much as possible in the design phase.
Safety is often considered as a condition where employees and operators are working and undertaking tasks that do not result in an injury. Safety of employees is most important and should always be considered first; however, safety of the equipment to minimise the potential for equipment failure, accidents, and environmental impacts that result in a loss of operational availability and facility production are also critical. This article provides insight into Matrix PDM Engineering’s approach to ensure safe operation of the facilities and the importance of operations personnel and equipment design.
Matrix corporate core values include “Safety” and support its full commitment for safety from the initial design of the facility and supporting equipment and extends to the construction and ends with the client personnel and operations. The safety hierarchy is a simplistic and obvious concept that says that the manufacturer should first try to eliminate the hazard through design. Then, if it cannot, it can implement the necessary safeguards to minimise the risk of such hazards or, as a last resort, provide warnings to the end-user.
How do we take “Safety in Design” to the next level? We work within an industry that is inherently risky and has many areas that impose risks to personnel and equipment safety. It is impossible to eliminate all risks; however, that does not mean we should accept the risks without evaluating and reducing the potentials (Fig 1).
During hazardous operations assessments, it is the responsibility of the HAZOP team to identify the areas and issues that need to be addressed. Once the probability and severity have been evaluated, it is up to the project to reduce anything that is considered “very high” or “high” however, the equipment suppliers and project teams should always consider areas that have been indicated as “medium” to continue to drive the design to as “low” risk as possible.
Safety during the initial design and frontend feasibility is the lowest cost and can have the greatest impact on the facility. The best way to provide the greatest impact to the overall design is for engineering and designers to “think outside the box”. The questions that should constantly be asked during the initial engineering phase are:
- Can we design prefabricated components to simplify site assembly and future disassembly?
- How can we reduce the need for onsite construction work to be performed at height?
- By using trenchless technologies, can we reduce the need for excavation?
- Have we considered using varied materials that will make it safer and easier for the construction team without compromising mechanical integrity?
- Can we hold an internal and external workshop with other disciplines, suppliers, and client to share ideas and best practices. Early discussion during P&ID generation and 30% model review can provide the most benefit to the overall project design. Most changes recognised during the 90% model review are ignored due to the complexity to change the entire facility to accommodate.
- Will the new equipment be assembled within an active and operating facility? How will this affect the need for added safety requirements on existing operations staff? Completing daily work permits, hot work permits, critical lifts, lock-out/tag-out, etc.
• Will the facility produce product that fully meets design requirements and provide the best solution at the lowest overall capital and operating costs while exceeding all environmental requirements.
Several tools and procedures that assist are used to help with the design process (Table 1). Hazard Identification can be simply completing Hazard Checklists or completion of a full hazard study review (HAZOP or HAZID). Once the hazards are identified and risks are assessed, the project team should explore all ways to eliminate or reduce those risks. All risks cannot be eliminated or reduced; therefore, procedures need to be created or modified to reduce the potentials of the risks resulting in a safety incident. With the advancements in 3D modelling over the past couple of decades, model reviews with strict guidelines and defined expectations need to be adhered to.
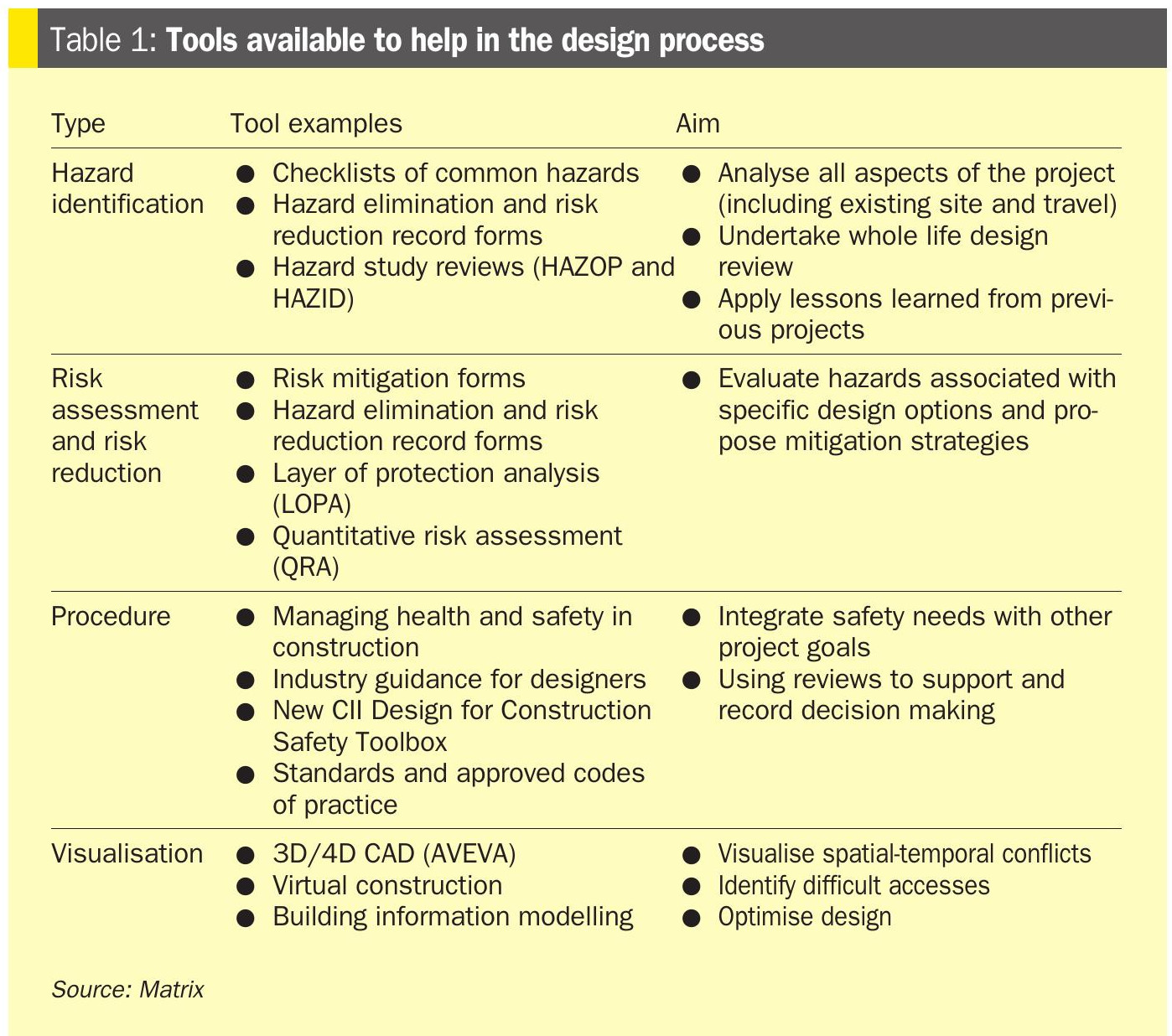
The main purpose for a safety in design checklist is to identify the potential hazards, verify the design has reduced or eliminated the hazards, design controls to further reduce the risk or severity of hazards, and document all continued risks with procedures.
Within the sulphur industry there are several hazards that are considered “very-high, high, and medium” that must be addressed during the design phase. The following list for hazard identification and risk assessment within sulphur forming, handling and blocking facilities is not intended to be a comprehensive list but does provide examples of issues that must be considered.
Hazard identification and risk assessment in sulphur forming, handling and blocking facilities
Using a risk assessment matrix, examples can be evaluated, and mitigations are implemented for proper safe working practices and conditions.
Personnel hazards
• Hot surfaces
-
- Hazards: burns
- Assessment: probability frequent / severity moderate = high risk
- Mitigation: all hot surfaces must be properly insulated. If hot surfaces cannot be properly insulated, barriers and guards should be used to protect personnel from potential burns when touching hot surfaces.
• Noxious gases exposure
-
- Hazards: sickness, critical illness, hospitalisation, death
- Assessment: probability frequent / severity critical to catastrophic = very high risk
- Mitigation: majority of facilities utilise molten sulphur degassing. The resultant sulphur contains less than 10 ppmw of H2S entrained in the molten sulphur. H2S will partially evolve from the molten sulphur and can reach toxic levels if not properly vented. Additionally, personnel and area H2S detection should be required within all sulphur recovery, forming, and melting facilities.
• Sulphur and sulphur dust exposure
-
- Hazards: skin, eyes, inhalation
- Assessment: probability frequent / severity moderate = high risk
- Mitigation: reduce airborne dust with proper moisture and dust suppression. Proper amount of moisture on product and/or use of dust suppressant at all material handling points must be in service and properly applying correct amount of moisture.
Equipment hazards
• Materials of construction and compatibility with sulphur
-
- Hazards: corrosion, erosion, equipment failure, loss of production, facility shutdown
- Assessment: probability likely / severity moderate with possibility to be critical = medium/high risk
- Mitigation: all equipment must be evaluated individually to determine best design to reduce overall impacts. Proper steel coatings should also be considered and properly maintained throughout the life of the facility.
• Potential failures of individual components and major equipment
-
- Hazards: equipment failure, loss of production, facility shutdown, time to repair or replace equipment
- Assessment: probability occasional to likely / severity critical = high risk
- Mitigation: depending on the equipment, time to repair or replace the equipment may have significant impacts to the entire operation. With increasing issues with global supply of key materials and equipment, additional purchase on onsite storage of critical spares must be evaluated.
• Required system shutdown to repair, replace, and clean various key equipment.
-
- Personnel hazards: confined space entry, hot surfaces, sulphur dust, heat exhaustion
- Equipment hazards: failure, loss of production, facility shutdown, time to repair or replace equipment
- Assessment: depending on technology: probability likely to frequent / severity critical = very high risk
- Mitigation: depending on the technology and equipment, the time to repair or replace may have significant impacts to the entire operation. Some forming technologies require daily equipment cleaning, while other technologies use minimal rotating equipment with simplistic forming process.
• Sulphur and sulphur dust airborne during solid sulphur handling process resulting in high level of sulphur dust in atmosphere.
-
- Hazards: sulphur dust fires, sulphur dust explosions
- Assessment: probability occasional / severity catastrophic = high risk
- Mitigation: proper moisture control of solid sulphur product is paramount to reduce the potential and risk. Various sulphur forming technologies produce sulphur with less-than-optimal moisture content that requires additional water and dust suppressant to be applied after forming. Matrix PDM technology produces solid product with optimal moisture content that does not require additional water or dust suppression post production.
Environmental hazards
• Sulphur and sulphur dust contamination with surface water and potential high acidity water to effluent.
-
- Hazards: high acidity water that must be pH controlled, Possible violation of environmental regulations
- Assessment: probability occasional to likely / severity critical = high risk
- Mitigation: proper housekeeping in the sulphur forming and material handling areas. Proper design of rainwater collection with testing and maintenance of equipment.
• Sulphur and sulphur dust airborne during solid sulphur handling process resulting in high level of sulphur dust in atmosphere and potential contamination of area land a water.
-
- Hazards: sulphur dust explosions, sulphur dust going into waterways at point of origin and destination
- Assessment: probability likely to frequent / severity critical to catastrophic = very high risk
- Mitigation: proper moisture control of solid sulphur product is paramount to reduce the potential and risk. Various sulphur forming technologies produce sulphur with less-than-optimal moisture content that requires additional water and dust suppressant to be applied after forming. Matrix PDM technology produces solid product with optimal moisture content that does not require additional water or dust suppression post production.
Mitigation of the highest safety risk when dealing with solid sulphur
Most mechanical equipment issues can be resolved with proper selection of equipment, meeting latest project specifications, and minimising impacts to the overall process that results in facility shutdowns. Matrix PDM Engineering continues to evaluate its process and provides industry standard equipment that can be easily repaired or replaced within a single shift. Minimal moving parts and proper selection of materials provides the highest reliability while considering overall value of the facility.
Considering the three focus areas and overall facility safety, “sulphur and sulphur dust” issues appears in each group. Using the assessment formula, sulphur dust appears as very high and high within each group. Mitigation of sulphur dust is required using technology and engineering tools. Sulphur dust can be mitigated through the proper application of water or a mixture of water and dust suppressant.
Proper moisture control of solid sulphur product continues to be misguided within the industry. Several companies continue to reference an outdated and obsolete material specification that was disbanded in 1982. Currently there is only one internationally recognised solid sulphur specification. This specification was developed by the Chinese in 2006 (see Table 2).
The proper moisture content of all solid sulphur should be less than 2.0% for all three defined sulphur purities. China continues to lead the world in imported sulphur and uses the sulphur specification to define all imported sulphur and not as produced. Proper moisture content at the point of production, storage, and when the product is loaded onto the outbound vessel should be approximately 2.0% to ensure the dust is properly controlled. Final product leaving the point of origin should be approximately 2% to meet the import requirements of the only active solid sulphur specification.
Various independent studies and papers have been authored over the past four decades addressing proper moisture content of solid sulphur product. All authors agree that solid sulphur should be maintained with a moisture content of minimum 1.5% and various ports of origin within North America have imposed standards that require sulphur to be between 2% to 3%. This level of moisture significantly reduces the risk of sulphur dust fires, explosions, and airborne particulate.