Sulphur 419 Jul-Aug 2025
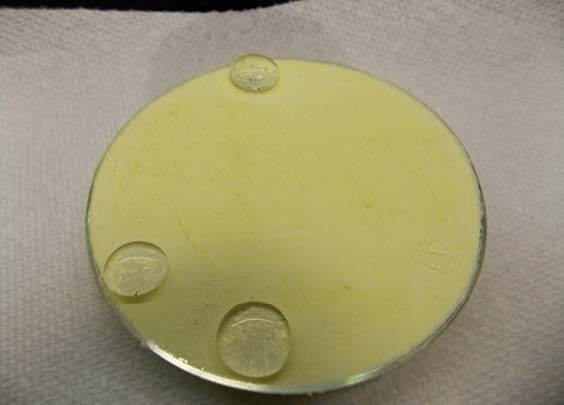
17 July 2025
Advances in sulphur dust suppression and acidity control
SULPHUR HANDLING
Advances in sulphur dust suppression and acidity control
Although elemental sulphur is relatively non-toxic, it presents significant risks when stored or transported. Jeff Cooke of DuBois Chemicals Canada highlights advancements in both dust suppression and acidity control, including the development of novel agents designed specifically for use with elemental sulphur.
Globally, there is a growing emphasis on minimising the environmental and occupational impacts of industrial activities. Regulatory bodies are tightening restrictions, and heightened public scrutiny – fuelled by rapid information dissemination via social media – has placed additional pressure on companies to adopt safer, more environmentally conscious practices. This is particularly true in the energy sector, where elemental sulphur – produced as a by-product of sulphur removal from oil and gas – is handled in large quantities during storage and transportation.
Although elemental sulphur is relatively non-toxic, it presents significant risks when stored or transported in prill, pastille, lump, or crushed forms. Fires and explosions can be triggered by static electricity, embers, or sparks. Moreover, the handling of solid sulphur frequently leads to the generation of fine dust particles. Without appropriate dust control methods, this dust becomes not only a product loss and air quality issue but also a severe fire and explosion hazard.
Sulphur dust accumulates during material transfer, particularly through harsh handling or areas with turbulent airflow. Fine particles become airborne or settle on infrastructure surfaces – especially indoors – where they can be disturbed and dispersed, potentially exceeding the lower explosive limit of 35 g/m³. Compounding this risk, sulphur oxidising bacteria can colonise sulphur surfaces in humid environments (such as coastal terminals), metabolising sulphur and excreting sulphuric acid. This acid can corrode metals and damage infrastructure if not properly controlled. Acidic sulphur is often deemed of lower quality and value.
To mitigate these risks, sulphur handlers typically apply dust control agents, implement acidity control measures, and follow disciplined maintenance protocols. Traditionally, these dust suppressants and acidity control agents are delivered via water-based sprays.
Advances in sulphur dust suppression
To be effective, dust suppressants must rapidly wet the entire surface immediately after application by spray. Application locations should be where all sides of the sulphur can be easily reached, such as during transfer at conveyor headboxes and/or chutes. The goal is to bind fine particles before they can become airborne. Agglomeration helps prevent dusting, while adhesive properties enable fines to adhere to larger particles. Rapid wetting also limits release of fine particles generated through mechanical attrition.
Since sulphur is inherently hydrophobic, traditional water-only sprays are often ineffective. An optimised dust suppressant should possess low surface tension, be capable of rewetting, and offer a degree of lubricity – just enough to reduce attrition without compromising material flow or pile stability.
Designing a dust control system requires understanding the dust generation mechanism, the variables influencing it, and the limitations of the dust control method itself. Effective systems address both prevention (eliminating dust formation) and collection/elimination (removing already airborne dust).
Collection/elimination measures
Dust collection or elimination strategies function by reacting to dust that has already become airborne. These include water curtains, fogging systems, and mechanical air filtration units such as baghouses and cartridge filters. While effective under tightly controlled conditions (such hoppers), these systems come with notable limitations that reduce their practicality in many sulphur handling operations.
Wind and environmental sensitivity
Water curtains and fogging systems are highly susceptible to wind and air currents. In open or semi-open environments such as domes, transfer towers, or loading facilities, crosswinds can easily displace fine mist or fog, rendering the system ineffective at targeting dust-laden air streams. As a result, dust often bypasses the intended capture zone entirely.
Lack of persistence
Unlike chemical dust suppressants that bind to the sulphur and provide ongoing dust control throughout the material’s handling lifecycle, physical collection methods only operate at the moment and location of application. They offer no residual protection. Once airborne dust is missed by a fog or curtain, or once the treated air moves beyond a filtration zone, control is lost. This makes these systems reactive rather than preventative.
Complex air management requirements
Air filtration systems require careful control of airflow patterns to capture dust effectively. Ducting must be installed to direct ambient air to centralised collection units, and high-powered blowers must overcome system resistance. These setups are often impractical in outdoor facilities or where operations are spread out or frequently reconfigured.
High operating and capital costs
Filtration systems demand significant energy inputs, especially for large-scale air handling. Fan motors, filter changes, and maintenance all contribute to operating costs. Additionally, the capital investment required to design and install ducting, access platforms, and collection housings can be substantial, particularly if retrofitting is involved.
Seasonal and climate constraints
In colder climates, water-based fog and mist systems are limited by freezing conditions. Even when antifreeze additives are used, nozzles and pipes are prone to clogging, and ice formation on the treated surfaces can pose operational hazards.
Intermittent efficiency and overspray risk
The efficacy of knockdown systems depends on achieving and maintaining a fine balance between droplet size, density, and distribution. Oversized droplets can saturate sulphur or equipment, causing product handling problems, while undersized droplets may evaporate before capturing dust. Overspray can also result in excessive moisture on surrounding walkways and structures, creating slip hazards or unintended corrosion.
For all these reasons, while collection/ elimination measures may play a supporting role in a broader control strategy, they are best suited to enclosed, engineered environments with stable airflow and controlled climate. As standalone solutions, they lack the reliability and persistence of direct chemical applications, which remain the most robust means of preventing sulphur dust emissions and their associated hazards.
Preventative measures
Liquid-applied suppressants remain the most efficient method for sulphur operations. Applied directly to the material via engineered spray systems, they promote:
- agglomeration of existing fines or adhesion to larger particles;
- reduction in generation of new fines;
- prevention of escape of dust during processing.
To address the performance needs of dust prevention applications, DuBois Chemicals has developed Dustbind 1888C, a sulphur-specific concentrated formulation which builds on the success of our benchmark product, Dustbind S5.
Dustbind 1888C can be effective in doses as low as 1-3 ppm (grams per tonne sulphur) and is applied in diluted form in ratios up to 1:1000 Dustbind:water depending on the requirements of the operation.
Entirely flexible, this product can be applied as a traditional hydraulic spray, a coarse, penetrating foam (through air induction), or a creamy foam (with an external compressor). The recommended application method of application is using a hydraulic, foamless spray or a coarse penetrating foam.
The fundamental basis of the performance of Dustbind 1888C, and all other DuBois Dustbind products, is their inherent ability to immediately wet and penetrate the substrate bulk, coating the surface and preventing the small particles from escaping. Water is often used as a dust control agent on sulphur and other hydrophobic materials with little success. In Fig. 1, water can be seen sitting on the surface of powdered sulphur, without the slightest wetting or penetration, similar to water on wax. Clearly water alone is not sufficient to control dust on sulphur.
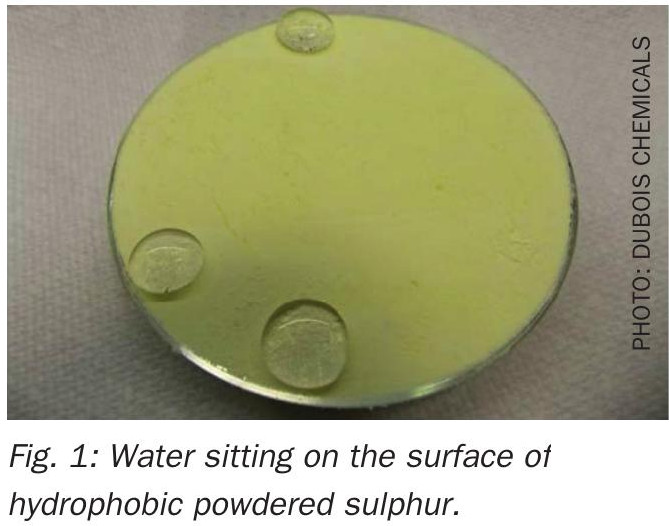
An example of the efficiency of Dust-bind dust control agents can be seen in the before/after pair of photos in Fig. 2. The first photo is sulphur treated with water being stacked in an indoor storage area. There is clearly significant dust generation occurring. Once the sulphur was treated with the Dustbind agent, there was essentially zero dust generated from even the aggressive stacking operation shown.
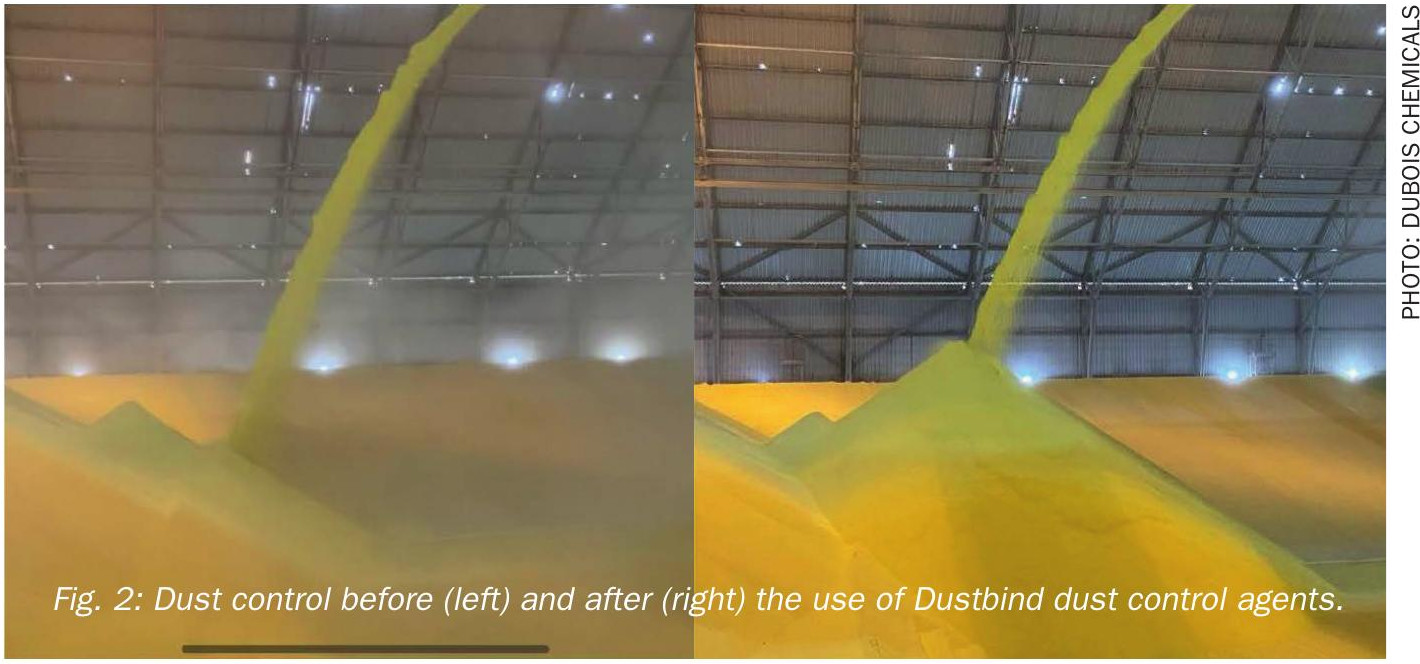
Acidity control in elemental sulphur
In addition to dust, elemental sulphur piles are vulnerable to acid generation caused by sulphur-oxidising bacteria (SOB), especially in warm, moist storage environments. These bacteria metabolise sulphur into sulphuric acid, which can damage concrete pads, steel reinforcements, storage buildings, and conveyance equipment.
Acidity control agents have been developed and formulated to inhibit bacterial colonisation and thus prevent acid generation. Not normally pH neutralisation agents, these products prevent the acid problem before it starts. Typically applied through the same spray infrastructure used for dust suppression, these treatments provide a persistent action, resisting leaching and offering ongoing protection.
The ideal acidity control agent must:
- be chemically compatible with sulphur and dust suppressant formulations;
- resist leaching during rain events; provide a residual barrier to bacterial colonisation;
- maintain efficacy in both tropical and temperate environments.
The integration of acidity control agents into existing dust suppression programs offers a streamlined and cost-effective approach to managing both physical and chemical degradation in elemental sulphur storage and transport.
Traditional SLS-based products and their limitations
Historically, sodium lauryl sulphate (SLS) has been widely used in elemental sulphur treatment. While SLS-based products offer good acidity control functionality, they suffer from several key limitations: limited durability in wet conditions;
- high foaming tendency, complicating equipment operation and material handling;
- potential to nourish sulphur-oxidising bacteria rather than suppress them;
- corrosive byproducts in moist, warm environments leading to infrastructure damage;
- environmental concerns regarding aquatic toxicity and regulatory compliance;
- relatively high cost.
These drawbacks have led to the development of next-generation agents offering improved longevity, environmental compatibility, and microbial resistance.
Neutrasul – A new generation acidity control agent
DuBois Chemicals has recently introduced a next-generation acidity control agent, branded as Neutrasul, representing a significant advancement in the treatment of elemental sulphur. Designed to overcome the limitations of traditional SLS-based products, Neutrasul provides a robust, adaptable platform for managing acid formation in sulphur storage and transport environments.
Neutrasul is notable for its ability to be tailored to meet specific operational needs, providing flexibility and performance across a wide variety of use cases. The product is available in a portfolio of formulations, each optimised to balance key properties:
Temperature range: Can be handled, stored, and applied at temperatures as low as –20°C or lower, making it suitable for cold climate applications where the sulphur will eventually warm.
Health and safety: Can be formulated to be entirely non-hazardous, enhancing worker and environmental safety.
Cost efficiency: Neutrasul can be applied at a significantly lower cost than traditional formulated SLS products.
Handling and storage: Unlike many SLS-based agents, Neutrasul exhibits excellent stability in storage with no phase separation, simplifying logistics and inventory control.
These combined advantages make Neutrasul a compelling choice for sulphur handlers seeking an advanced, cost-effective, and safe solution to long-standing acidity control challenges. When incorporated into an integrated dust and acidity management program, Neutrasul can enhance equipment life, reduce maintenance, and ensure regulatory compliance even in demanding environments.
Neutrasul has been tested extensively by DuBois, with testing verified by Alberta Sulphur Research Laboratories. The chart in Fig. 3 shows virtually identical performance between DuBois Neutrasul and IPAC EAC on elemental sulphur over a period of six weeks.
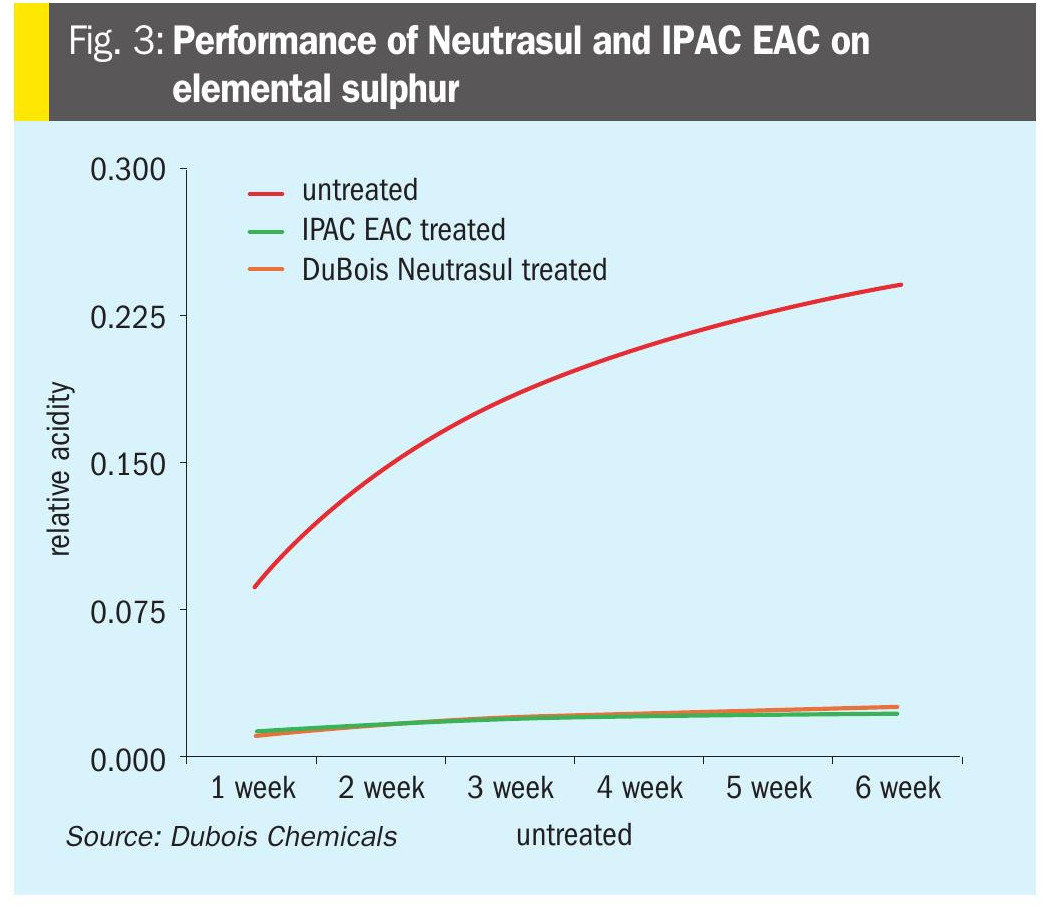
In summary, through the judicious use of properly applied chemical agents, both sulphur dust and acidity issues can be easily remedied. Proper design, installation and service will ensure trouble-free operation of your sulphur handling systems.