Nitrogen+Syngas 396 Jul-Aug 2025
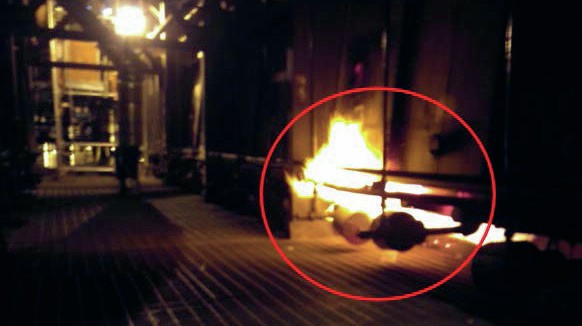
9 July 2025
Reforming furnace tube failure results in fire
TROUBLESHOOTING
Reforming furnace tube failure results in fire
This article describes an unusual tube failure incident which resulted in fire escaping the furnace box during normal operation of a hydrogen plant. Ken Wohlgeschaffen of Chevron Products Company shares the sequence of events leading up to the incident, the extent of damage caused by the incident, and most importantly the causes and lessons learned from this incident to prevent recurrence.
Most instances of reforming furnace tube failures occur during transient conditions such as start-up or shutdown when the risk of overheating tubes is the highest. This incident occurred during normal operation of a world-scale side-fired steam methane reforming furnace of a 1960s vintage hydrogen plant.
The incident
The first indication there was a problem was a high fuel gas pressure alarm. Several tube effluent temperatures had failed and the control system responded by firing up the furnace. Flames were observed coming out of the furnace near the location of a burner manifold (Fig. 1). Fuel gas to the burners was reduced, and natural gas feed was pulled. The plant was set to steam-only mode.
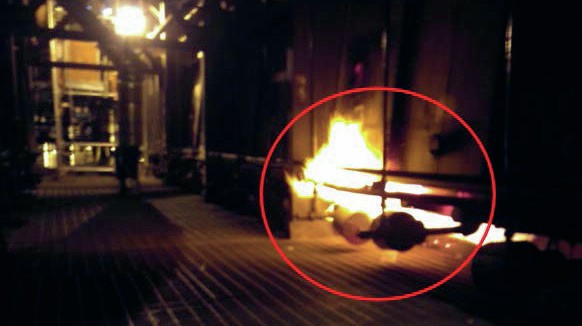
Visual inspection of the interior of the fire box revealed that refractory on the wall had been knocked off. The fire box wall was glowing red on the inside and outside (Fig. 2a) due to the damaged refractory. A leaking tube could be seen with the jet flame clearly impinging on the furnace wall (Fig. 2b). The flame impingement had caused refractory to fall off the furnace wall onto a burner below, deflecting the flames through the burner air inlet above the walkway.
2a
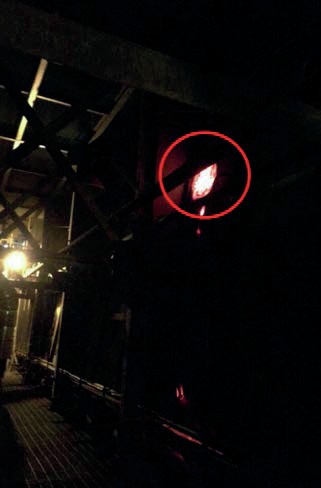
2b
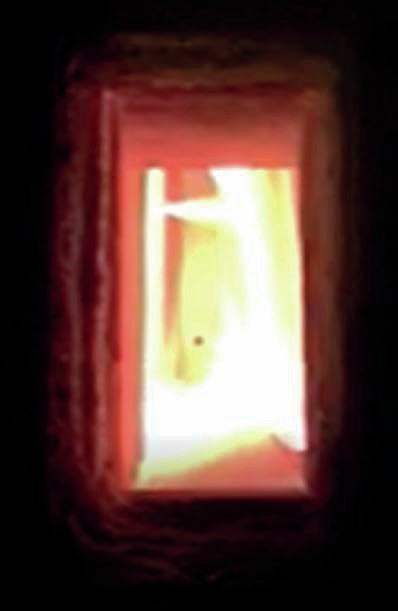
The steam flow eventually dropped off below the minimum flow limit causing a full plant trip (Fig. 3)
Upon inspection it was found that a radiant section tube had a crack approximately 5 inches (127 mm) in length and ¼ inch (6 mm) wide (Fig. 4). The tube was bulging about 6 feet (1.8 m) above the closest burner located on the lower level, or approximately one third the length of the tube from the bottom of the tube.
Incident investigation findings
The tubes were newly installed during a major turnaround several years prior. After that start-up a tube in this same section of the furnace had failed near the bottom of the tube outside the extreme heat zone. Destructive testing revealed manufacturing defects or voids in the material resulting in premature failure of this new tube. During the subsequent major turnaround a tube crawler inspection was performed to identify early signs of creep damage or thinning. No abnormalities were found.
The possibility that this most recent tube failure occurred because of a manufacturing defect like the one which occurred many years prior could not be ruled out since destructive testing of the failed tube could not be done. However, the probability of this to be a manufacturing defect is low because manufacturing defects tend to be found in the far ends of the tubes or the tube welds rather than near the middle of the tube. Furthermore, this failure would likely have occurred much sooner after start-up, as was the case with the previous tube failure.
Temperature data was reviewed. A few years earlier the catalyst supplier measured tube wall temperatures and found one tube to be running close to the creep limit. This tube which had been identified was closely monitored to ensure it was well below the creep limit. Later on the routine tube wall temperature surveys were discontinued.
A survey was conducted by the catalyst supplier much later on which identified tubes with wall temperatures above the creep limit. Adjustments were made immediately to reduce the tube wall temperature. It is unclear how long these tubes were running at elevated temperatures.
As a result of the investigation it can be concluded that to prevent safety incidents of this nature, hydrogen and ammonia plant operators should: train their personnel on the importance of routine tube temperature monitoring; conduct routine tube temperature surveys; use appropriate equipment for tube temperature monitoring; and have in place a robust process for communicating and managing the identification of hot tubes.
Lessons learned
- Recognise that, with a loss of several layers of protection (the “Swiss cheese effect”), it is possible for a reforming furnace radiant section tube leak to result in fire escaping the furnace fire box.
- Recognise the risks associated with furnace tube failures, understand what safeguards are needed to minimise them, and ensure that they are in place and working.
- Follow up on incident investigation action items in a timely manner.
- Take tube wall temperature measurements routinely.
- Do not normalise deviation, in this case hot tubes.
- Use the right tools for the job, in this case a good combination pyrometer and data logger.